Tube bending is a versatile and essential technique used in various industries, from piping, automotive manufacturing to plumbing and construction. It allows for the creation of complex shapes and structures without the need for welding or soldering. The tool that makes this tube-bending activity easier is known as a Tube Bender. Understanding the fundamentals of tube bending and tube benders is crucial for smoothly working in the pipe and tube construction industry. In this comprehensive guide, we’ll delve into the world of tube benders, exploring their types, applications, and essential tips for achieving perfect bends.
What is a Tube Bender?
Tube benders are specialized tools used to bend piping and tubing at different angles without crimping or collapsing the internal profile. They prove to be useful in various applications across numerous industries including plumbing, automotive, construction, and more. Tube Benders are available in various types and sizes and are crucial for bending ductile metal tubing at precise angles.
Types of Tube Benders
There are several types of tube benders, each with their unique features suited for different tasks. The most common types are:
Manual Tube Benders:
These are the simplest form of tube benders and are ideal for home use or small projects. They are easy to use but might require physical force depending on the material of the pipe or tube. They come in various shapes and sizes to accommodate different tube diameters and bend angles. Fig. 1 below shows a typical manual tube bender.
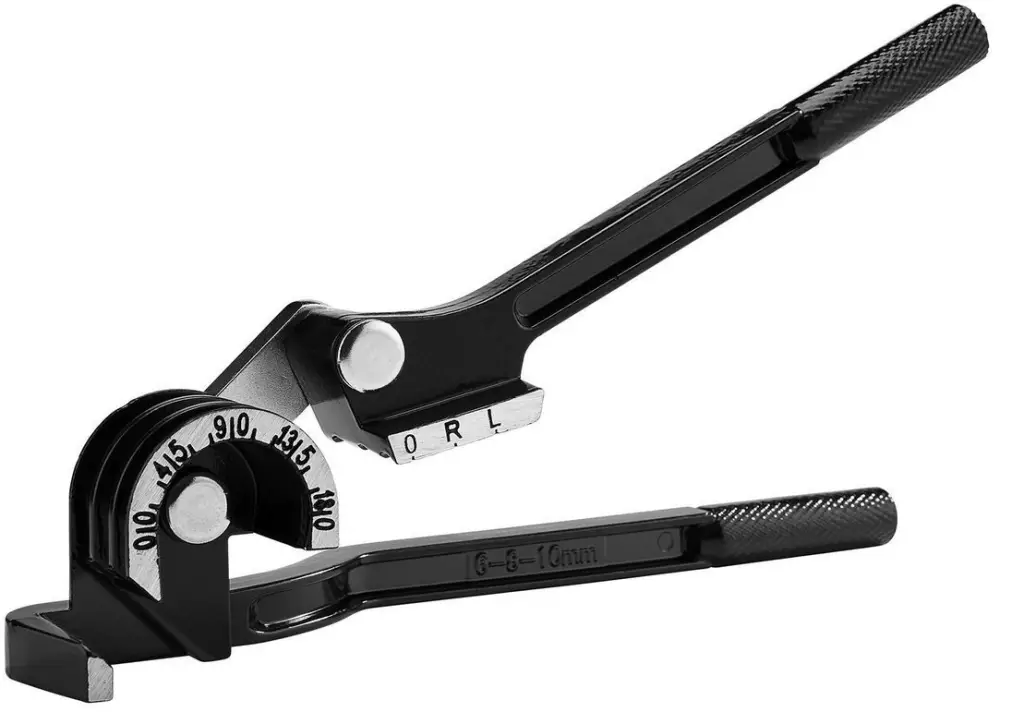
Hydraulic Tube Benders:
These machines use hydraulic pressure to bend tubes. They are capable of handling larger tube diameters and are often used in industrial settings where high precision and consistency are required. Hydraulic tube benders are more powerful and efficient, making them ideal for heavy-duty applications. Fig. 2 shows a typical hydraulic tube bender.
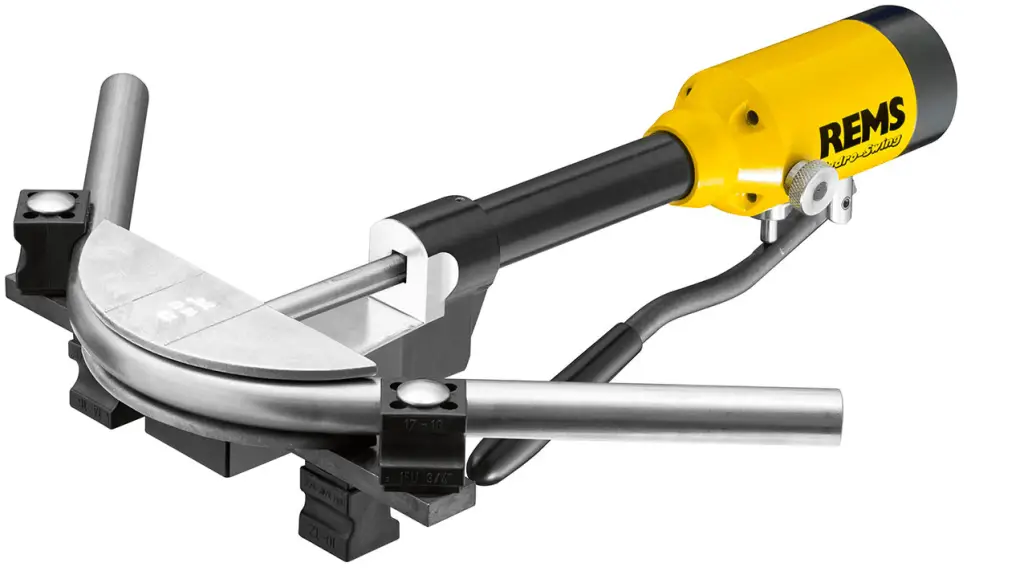
Electric Tube Benders:
Electric tube benders are powered by electricity and provide precise control over the bending process. They are suitable for medium-sized projects and offer a balance between manual and hydraulic benders in terms of power and convenience.
Rotary Draw Benders:
These benders are great for producing accurate and consistent bends. They use sets of dies to bend tubes, which makes them perfect for precise, repeated bends. Refer to Fig 3
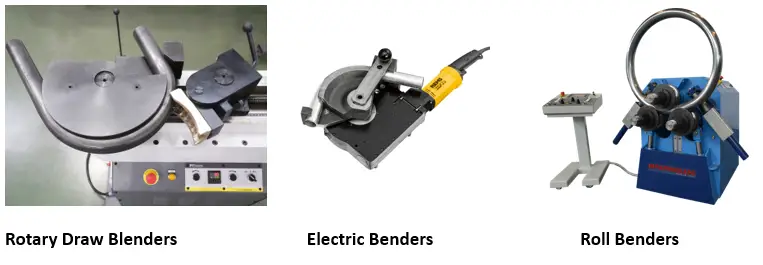
Roll Benders:
Also known as a three-roll push-bender, they work by incrementally bending the tube with three points. They are used primarily for bending large tubes and pipes.
Components of Tube Benders
- The Frame: The frame functions as a support structure for the machine, ensuring stability during the bending process.
- The Dies: Dies are shaped like a tube to be bent. They are usually made from hardened steel and are crucial in maintaining the shape of the tube during the bending process.
- The Bend Radius: This is the measurement of how much a tube can be bent before it begins to collapse or become deformed. Each tube bender will have its specific bend radius.
How Tube Benders Work
Tube benders work on a simple principle: they exert force externally onto a tube to make it follow the shape of a die set. This force is applied gradually, reducing the risk of wrinkling or flattening the tube. In a hydraulic bender, this force is delivered through hydraulic pressure, while manual benders rely on human strength.
Applications of Tube Benders
Tube benders find wide-ranging applications in industries such as automotive, where they’re used to build roll cages and exhausts, or plumbing for creating water supply lines. They are also used extensively in construction and manufacturing.
Plumbing:
Tube bending is commonly used in plumbing to create bends and curves in pipes for water supply and drainage systems. It allows plumbers to navigate obstacles and create custom pipe configurations to fit tight spaces.
Automotive Industry:
Tube bending is extensively employed in the automotive sector for exhaust systems, roll cages, and chassis construction. It helps improve the vehicle’s performance, safety, and aesthetics.
Furniture Manufacturing:
The sleek and modern designs of furniture often require curved metal or tubing. Tube bending is used to create the frames and supports for chairs, tables, and other furniture pieces.
Aerospace:
In the aerospace industry, precision is paramount. Tube bending is utilized to create the intricate tubing systems needed for aircraft, such as hydraulic lines and fuel pipes.
Construction:
From handrails and guardrails to structural components, tube bending plays a vital role in construction projects. It allows for the creation of aesthetically pleasing and structurally sound elements.
The primary benefits of using a tube bender are reduced waste and increased efficiency. By allowing for precise, accurate bending, tube benders minimize the amount of material needed and time taken to create bends, thus saving resources and labor costs. They also decrease reliance on welding and other methods that may compromise the strength and integrity of the tube.
Hands-on Application of Tube Benders
A tube bender is a tool used to bend various types of pipes and tubes, making them more appropriate for specific purposes such as plumbing, construction, and engineering. They can work on metals like copper, brass, aluminum, and steel.
Before Getting Started Issues
Before beginning the bending process, select the appropriate tube bender for the size and type of material of your tube. Capacities and capabilities differ, and improper pairing might damage the tube or the tool. A correctly selected tube bender will accommodate the tube’s radius without causing distortion, wrinkling, or breaking.
Safety Precautions: Protect Yourself
Safety is paramount when operating a tube bender. Always wear suitable protective gear like safety glasses, gloves, and sturdy footwear. Ensure your working environment is neat, clear of debris, and well-lit. Secure your workpiece to prevent it from slipping and causing injuries. Check your bender for any signs of wear or damage before use. Do not use a bender with damaged parts.
Initial Steps: Part Preparation
Before bending the tube, make sure to properly measure and mark the exact locations where you need the bends to be. This step will ensure all the bends will follow the correct angle and direction and align with your project design. Mark your tubes using a suitable marker that’s visible on the tube material.
Bending the Tubing
- Insert the tube into the die set of the tube bender, lining up the mark on the tubing with the indicated mark on the bender.
- Use the pressure die component to hold the tube in position. Make sure the tube is well secured.
- Begin bending by pumping or cranking the handle. Watch the bend actively as you proceed; avoid overshooting your targeted degree of bend.
- Once you reach the desired angle, release the pressure in the bender then carefully remove your tube.
Post Bend Actions: Checking Your Work
After you’ve accomplished your bend, confirm if it is according to your desired specifications – it’s checking the angle and position. Use an angle gauge to ensure accuracy. Re-bend or correct as necessary.
Lastly, always clean and perform maintenance on your tube bender after use. This action will prolong its useful life and prevent the potential premature failure of components.
Troubleshooting and Maintenance of Tube Benders
Tube benders are essential tools used in bending tubes of various thicknesses and diameters without causing ridges or kinks. Despite their robustness, tube benders can develop issues over time, affecting their functionality. Here is a guide on how to troubleshoot common problems and maintain these handy tools.
One primary problem that users may encounter is the tool not achieving the desired bend. This is commonly due to worn-out bending dies. If this occurs, it’s crucial to inspect the dies and replace them if necessary. Remember, each tube size demands a specific die set, so always refer to the manufacturer’s chart for correct specifications.
Another common issue is the bender creating inaccurate or uneven bends. This could stem from a calibration issue, insufficient clamp die pressure, or the wrong radius bend die. Check the calibration of the bender and adjust it if needed. Also, increase the clamping pressure to prevent the tube from slipping during the bending process.
Lastly, if the bender isn’t bending at all, it could be due to a mechanical fault or loss of hydraulic pressure (in hydraulic tube benders). Investigate the moving parts for any visible damages, or any signs of leaks that might indicate a loss of hydraulic pressure.
Implementing Regular Maintenance Practices
Routine maintenance can greatly extend the life of your tube bender and improve its performance.
Firstly, clean your tool after every use to remove any dust, grim, or residue. This protects the device from undue wear and tear caused by such particles.
Next, lubricate the bending dies and other moving parts frequently to ensure they function smoothly. However, avoid applying excessive oil or grease that might attract dust.
Further, check the hydraulic system (if applicable) regularly for any leaks or pressure changes. Replace the hydraulic fluid as advised in the user manual.
Inspect the bending dies for any signs of wear and tear. If they look excessively worn out, it’s time to replace them to maintain the tool’s efficiency.
Recognizing When Professional Help is Needed
Sometimes, despite your best troubleshooting and maintenance efforts, problems with your tube bender may persist. Noticeable issues like consistent improper bending, unusual noises, declining performance, or the bender’s inability to function all signify that immediate professional assistance is needed. Remember, trying to repair significant issues yourself could worsen the problem and jeopardize your safety.
So, if you’re unsure about what’s causing your tube bender’s problem or how to fix it, get in touch with a professional or the tool’s manufacturer. Avoid using the tool until it’s fixed; this way, you’re preventing the possibility of causing more damage.
Choosing the Right Tube Bender for Your Needs
Understanding Your Tube Bending Needs
Before you dive into the myriad of tube-bending products on the market, you first need to assess your specific needs. Ask what the tube bender will be primarily used for, what size and type of material will be bent, and how frequently you will use the tool. Also, consider your budget as costs can vary drastically depending on the type and brand of tube bender.
Choosing the Right Size
Size is a critical factor when choosing a tube bender. It would help if you thought about the outer diameter (OD) of the tube you’ll be using, the material thickness, and the bend radius you need. If your operations involve bending various sizes of tubes, look for a versatile tube bender that can accommodate different sizes and diameters.
Considering the Cost
The price of tube benders can vary significantly based on the brand, model, and additional features. Manual benders are more budget-friendly but require more physical effort, while hydraulic and electric benders are pricier but offer more power and convenience. It’s essential to assess the return on investment you will get from a tube bender based on your frequency of use.
Brand Matters
The brand of the tube bender matters because it usually indicates the level of quality and reliability you can expect. Established brands often offer better quality products and better customer service, which is beneficial if issues arise with the tool. The brand should also have good reviews from other users to ensure reliability.
Here are some of the top brands in the industry:
- Baileigh Industrial: Baileigh is a well-respected name in the metalworking and fabrication industry. They offer a wide range of tube and pipe benders suitable for various applications, from small shops to industrial-scale operations.
- RIDGID: RIDGID is a renowned brand known for its durable and dependable tools. They manufacture a variety of tube benders, including manual and hydraulic options, which are often favored by professionals in plumbing and construction.
- Greenlee: Greenlee is a trusted brand with a long history of producing high-quality tools for electrical and construction work. They offer a selection of conduit and pipe-bending tools for electricians and contractors.
- Swagelok: Swagelok specializes in precision tubing and fittings. They are highly regarded in industries like pharmaceuticals, petrochemicals, and aerospace for their tube bending and fabrication products.
- Pro-Tools: Pro-Tools is a company dedicated to tube and pipe bending equipment. They offer a range of manual and hydraulic benders, notchers, and other accessories, catering to both professional fabricators and DIY enthusiasts.
- Huth Ben Pearson International: Known for their tube and pipe bending machines, Huth Ben Pearson International serves industries such as automotive and exhaust fabrication. They are recognized for their durability and reliability.
- Ercolina: Ercolina specializes in tube and pipe-bending machinery. They offer a wide variety of benders, including mandrel and non-mandrel machines, which are commonly used in metalworking and fabrication shops.
- Edwards Manufacturing: Edwards is known for their high-quality ironworkers and other metalworking equipment. They also produce hydraulic tubes and pipe benders designed for precision and ease of use.
- Bailey: Bailey is another respected name in the tube bending industry. They produce a range of manual and hydraulic tube benders suitable for various applications, including automotive and fabrication.
- Chicago Electric: Chicago Electric is known for its affordable yet functional tube benders, making them a popular choice for hobbyists and DIY enthusiasts.
Evaluating Additional Features
Some tube benders come equipped with additional features like digital readouts, angle stops, spring back compensation, and more. While these features can make tube bending more convenient and efficient, they can also drive up the price. Determine which features are necessary for your operations and which ones are optional before making a purchase.
Material Type
The type of material you’ll be bending is another vital factor to consider. For example, softer materials like copper and aluminum require less force to bend, so a manual bender may be sufficient. However, for harder materials like stainless steel, you may need a hydraulic or electric bender for more power. Always ensure that the bender you choose is designed to handle the type of material you’ll be using.
Remember to take your time in selecting the right tube bender for your needs, considering all aspects from cost to capabilities. It’s an investment that, chosen wisely, can significantly improve your efficiency and quality of work.
Tips for Perfect Tube Bends
- Choose the Right Material: The material of the tube affects its bendability. Common materials include steel, aluminum, and copper. Make sure to select the appropriate material for your project.
- Measure Accurately: Precise measurements are crucial for achieving the desired bend angle and radius. Use a measuring tape, calipers, or a tube measuring tool to ensure accuracy.
- Lubrication: Applying lubricant to the tube’s interior reduces friction during the bending process, preventing wrinkles and kinks in the material.
- Bend Incrementally: When bending large-radius curves, it’s often best to make several small bends instead of a single sharp one. This minimizes the risk of deformation.
- Practice and Test: If you’re new to tube bending, practice on scrap material before working on your project. Testing your bends ensures that you achieve the desired results.
Square Tube Benders
Square tube benders, also known as square tubing benders or square pipe benders, are tools or machines specifically designed for bending square or rectangular metal tubing or pipes. These tools are essential for industries and applications that require the manipulation of square or rectangular tubing to create various structures, frames, supports, or custom components. Square tube benders are widely used in industries such as construction, manufacturing, fabrication, and metalworking.
Tube Benders vs Pipe Benders
Tube benders and pipe benders are specialized tools used for bending cylindrical metal objects, but they have some key differences. Here’s a comparison of tube benders and pipe benders in a tabular format:
Aspect | Tube Benders | Pipe Benders |
---|---|---|
Primary Purpose | Bending tubes (hollow, often with thin walls) | Bending pipes (usually solid, thicker walls) |
Material | Used for bending materials like copper, aluminum, and steel tubes | Designed for bending rigid materials like steel or stainless steel pipes |
Shape of Material | Typically used for round, square, or rectangular tubing | Primarily used for round pipes |
Wall Thickness | Usually used for tubing with thinner walls | Designed for pipes with thicker walls |
Bend Precision | Offers high precision and is suitable for intricate bends | May provide less precision but can handle larger diameter pipes |
Applications | Commonly used in industries like automotive, furniture, and construction | Often used in plumbing, HVAC, and heavy industrial applications |
Tool Types | Manual, hydraulic, and electric models are available | Manual, hydraulic, and electric models are available |
Bend Radius | Typically allows for smaller bend radii due to thinner walls | May accommodate larger bend radii due to thicker walls |
Bend Angle Range | Offers a wide range of bend angles, including tight bends | Provides a wide range of bend angles, including larger-radius bends |
Mandrels and Dies | Often used with mandrels or dies that match the tube’s shape | Utilizes dies or shoes that fit the pipe’s diameter |
Size Range | Suitable for a wide range of tube diameters | Primarily designed for specific pipe diameters |
Materials Worked With | Copper, aluminum, and mild steel are commonly used | Works with materials like steel, stainless steel, and carbon steel |
Safety Considerations | Safety precautions are necessary but generally involve less force | Requires careful handling due to the higher force required for bending pipes |
I like that you said that the unique features of tube bending could be achieved using different bending processes. My uncle mentioned the other night that he and his business partner were looking for a tube-bending company that could offer stainless steel and aluminum project beading processes for his business supplies. He asked if I had any idea what would be the best option to consider. Thanks to this informative tube bending guide article for the best planning approach.
Hello,
How do we ensure that the 76 mm ID of a 80 mm Tube stays perfect. I have heard the usage of wax that is filled prior to bending. Later the wax is removed by placing the tube in a tub of hot water.
could someone guide me here.
thanks