Tube bending is a mechanical fabrication process to bend tubes permanently from their straight form. In many applications, bent tubes are required to fulfill certain specific tasks. So, tube bending is a necessary forming method for industries. Various instrument items use bent tubes as one of their component parts. Bent tubes are also found in stair railings, automotive parts, furniture frames, handles, air conditioning equipment, and many other places. In piping, plumbing, and pipeline industries pipe and tube fittings in the form of bent pipes and tubes are widely used whenever a flow direction change is required. In this article, we will learn about tube bending, their working principle, terminologies used for tube bending, and types.
What is Tube Bending?
Tube bending is a manufacturing process used to shape metal tubes or pipes into specific angles or curves without altering their structural integrity. This process involves the application of force to the tube, typically through specialized equipment like hydraulic or mechanical benders, to achieve the desired bend radius and angle. Tube bending is commonly employed in industries such as pipelines, automotive, aerospace, and construction, where precise and durable tubing shapes are required for components like exhaust systems, roll cages, pipeline network, and structural frameworks. The technique ensures that the tube maintains its strength and functionality while conforming to the required design specifications.
A wide range of metal tubing, including aluminum, stainless steel, mild steel, brass, and titanium, can be bent into various shapes and configurations for specific purposes. Common bending shapes include L bends, U bends, S bends, and coil bends. These shapes are formed by applying force to straight metal tubing, which stresses and reshapes it to achieve the desired configuration.
How does Tube Bending work?
To start the bending process, the tube is fixed at two points. The bending action is then enforced using a rotating press, roller, or die. The tube material experiences a combination of tensile and compressive force when the tool advances. The tube bending process is dependent on various parameters like:
- the material of the tube
- used tooling
- bending geometry required
- applied pressure for bending
- lubrication, etc
Depending on the bending technique employed, the tube undergoes several physical changes per area. The outer side of the bend experiences tensile forces and creates elongation and wall thinning whereas the inner side of the bend experiences compressive forces and creates wrinkling and thickening of the wall.
The tube‘s cross-section undergoes a phenomenon known as ovality which is defined as the distortion of the tube‘s cross-section from the original round shape after bending.
After the tube bending process, the product may undergo various other fabrication processes like cutting and deburring, slotting, notching, and welding.
Terminologies used in Tube Bending
Let’s learn some of the terminologies frequently used in tube bending:
- Center-Line Radius: It is the distance from the center of the curvature to the tube centerline.
- Outside Diameter: The outside diameter is the distance between the two outermost points on the pipe or tube‘s cross-section having the same centreline.
- Inside Diameter: Inside diameter indicates the size of the tube’s hole and is calculated as Outside diameter-2 X wall thickness.
- Wall Thickness: It is the difference between the outside and inside radius of a tube. When choosing a die for a tube bending method, tube thickness, and outside diameter are the most important considerations.
- Degree of Bend: It is the angle formed by bending the tube and is measured in degrees. The degree of bend indicates the “sharpness” of the bend.
- Wall Factor: It denotes the relative wall thickness and is defined as the ratio of the outside diameter of the tube and its wall thickness. Wall factor determines if a tube is “thick-walled” or “thin-walled”. Tubes having lower wall factors are easier to bend and vice versa.
- D of the Bend: The “D of the bend” is the term used by tube fabricators that denotes the ratio of the CLR of the bend to the tube‘s outside diameter. The higher the bend’s D, the easier it is to form bends with tighter radii.
- Springback: Springback is the tube’s tendency to return to its original shape while bending. Springback is influenced by several factors like the material‘s stiffness, tensile strength, wall thickness, type of tooling, and bending technique used. Harder materials and smaller CLRs produce a greater springback.
Types of Tube Bending
The tube bending process can be classified depending on various parameters. In general, the following types of tube bending are popular:
Based on the forming methodology, there are two types of tube bending processes:
- Form-bound tube bending where the die geometry influences the forming process and
- Freeform tube bending where the forming is dependent on the tube’s movement through the tooling.
Based on the working temperature condition tube bending process is grouped as
- Cold bending and
- Hot bending.
Hot tube bending uses heat energy and is performed at higher temperatures whereas cold tube bending is done at room temperatures.
Depending on the tools used during the tube bending, there are various types of tube bending processes as mentioned below:
Press Bending
In the press bending process, the tube is fixed at two points and a ram/die is forced against the tube to take the shape of the bend. The bend characteristics are governed by the external dimensions of the cylindrical ram.
Press bending is widely used for symmetrical parts. The process is quick and does not require lubrication and cleaning. But, making a smaller degree of bend is difficult in this method. As this tube bending method is very difficult to control, it is only employed where a uniform cross-section is not required.
Rotary Draw Bending
Rotary draw bending is a highly precise tube bending method that gives minimal ovalization. This process is used in pipe fittings, instrument tubing, handrails, and automotive and aerospace parts. This method uses a set of interlocking dies. The tube is internally supported using a mandrel during the process.
A bend die that imparts the bend to the tube by rotating it around its outline determines the bend radius. Until the desired bend angle is obtained, the rotation is continued.
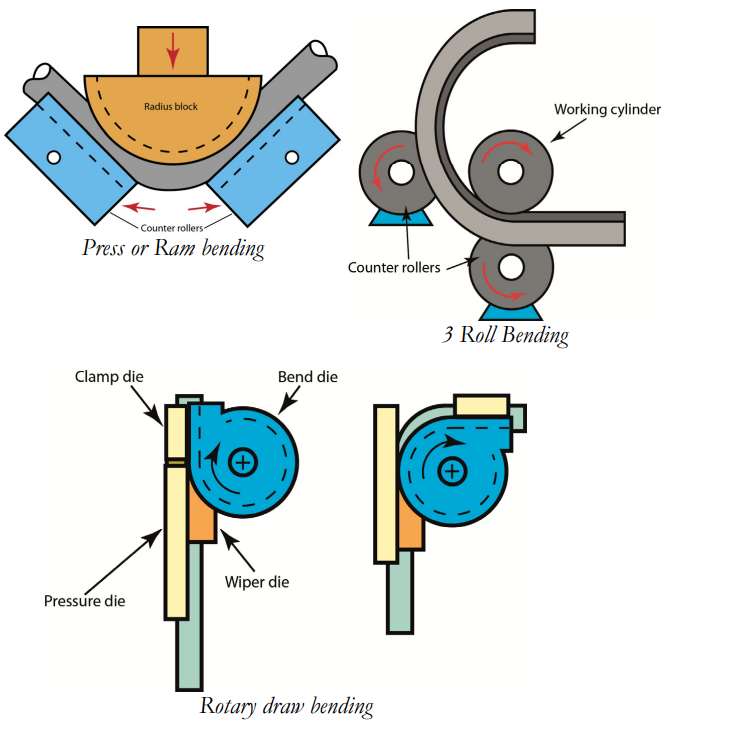
Compression Bending
Compression bending has a simpler setup but is limited to circular hollow sections only. A mandrel is not used for supporting which may cause the outside surface to flatten slightly.
Roll Bending
The roll bending method is suitable for creating bends with large CLR. Consisting of two stationary rotating rollers and a moving roller in a triangular pattern, the roll bending is used for large tube components and structural applications. The stationary rollers rotate in the opposite direction of the moving roller. As the tube moves back and forth on the rotating rollers, the bend radius is gradually formed.
Hydroforming
Hydroforming is a metal shaping process that uses two dies and pressurized liquid to form straight metal tubes into various shapes. Typically, round tubes are used due to their flexibility in creating different designs. The process involves placing the metal tube between the die halves and then applying pressurized fluid inside the tube. As the pressure increases, the liquid forces the tube to take the shape of the die. After achieving the desired form, the die is separated, and the new part is removed. Hydroforming produces high-quality, aesthetically pleasing parts with excellent shape retention and durability.
Bending Springs
Bending springs are used to bend softer workpieces having small diameters. A strong and flexible spring is inserted inside the tube walls from its end to the center of the bend radius. For positioning and easy removal, a wire is sometimes attached to the ends of the spring.
All the above-mentioned bending processes are performed at room temperature and hence fall into the cold tube bending category.
The heat energy used during hot tube-bending techniques enhances the tube‘s plastic deformation. Heat induction bending, Sand packing hot-slab bending, etc are examples of Hot tube bending which are normally used for bending polymeric tubes like PVC, CPVC, and ABS.
Heat Induction Bending
Heta induction bending is a hot tube bending process where the tube is supported on the front end and the bend clamp is placed in between the rotating arm and the rear end. After clamping the front end of the tube in the pivot arm, it is pushed gradually from the rear end. The tube passes through an induction coil where heat is supplied at a point tangent to the bend radius. The pivot arm is made approximately equal to the workpiece bend radius. Depending on the material of the tube, the working temperature can range from 430°C – 1,200°C. Once the bending is done, the tube piece is quenched in water spray or air.
Heat induction bending creates minimal wall thinning and ovality and can be applied for a wide range of pipe sizes and thicknesses. However, the operation is costly.
Sand Packing Hot-Slab Bending
This is one of the oldest hot tube bending methods that is still employed in many fabrication sites. In this technique, fine sand is filled inside the tube and then both tube ends are sealed. The sand-filled tube is then heated and at around 870° C, the pipe is placed in a slab with pins set on it. A mechanical force is applied to the tube to bend it around the pins. The sand inside the tube maintains its original cross-section.
Lubrication
To reduce friction, Lubricant must be used before the insertion of the dies. Proper lubrication prevents premature wear and increases the life of the tooling. Lubricants are available as a paste or gel. They have unique formulations for different tubing materials. Usually, lubrication is applied on the inside and outside of the tube, bending mandrels, contact points of wiper dies, and bending springs. For heavy-duty tube bending operation, a more concentrated lubricant application may be required for heavier-duty bending. At the end of the bending process, the remaining lubricant is cleaned from the tube and die surfaces.
Common Materials Used in Tube Bending
The choice of material for tube bending is crucial, as it affects the ease of bending, the quality of the finished product, and the application of the bent tube. Here are some common materials used:
Aluminum
Aluminum is a lightweight, corrosion-resistant metal with excellent workability. It is commonly used in aerospace, automotive, and construction applications due to its favorable properties. Aluminum tubes can be easily bent and formed, making them suitable for various designs.
Stainless Steel
Stainless steel is known for its strength, durability, and resistance to corrosion. It is widely used in industries such as food processing, pharmaceuticals, and marine applications. While stainless steel requires more force to bend compared to aluminum, its strength and resistance to environmental factors make it a preferred choice for many applications.
Mild Steel
Mild steel, or low-carbon steel, is a versatile material known for its ease of fabrication and affordability. It is commonly used in construction, automotive, and furniture industries. Mild steel tubes are relatively easy to bend, making them suitable for a wide range of applications.
Brass
Brass is an alloy of copper and zinc, known for its machinability and aesthetic appeal. It is often used in decorative applications, plumbing, and electrical fittings. Brass tubes can be bent with precision, and their appearance adds a touch of elegance to the finished product.
Titanium
Titanium is a high-strength, lightweight metal with excellent corrosion resistance. It is used in aerospace, medical, and high-performance engineering applications. While titanium is more challenging to bend due to its strength, its superior properties make it valuable for specific applications.
Applications of Tube Bending
Tube bending is employed in a wide range of industries and applications. Here are some notable examples:
Pipeline Industry
In the pipelines industry, the pipes are bent into specific angles using very large diameter bends for pigging purposes. Cold bending is performed and care is considered such that wrinkling does not occur.
Automotive Industry
In the automotive industry, tube bending is used to create components such as exhaust systems, roll cages, and suspension parts. Bending techniques allow for precise shaping of tubes to fit within the confines of vehicle designs while maintaining structural integrity and performance.
Aerospace Industry
The aerospace industry relies on tube bending for manufacturing parts such as hydraulic lines, fuel systems, and structural components. The high strength-to-weight ratio of materials like aluminum and titanium, combined with precise bending techniques, ensures that components meet rigorous safety and performance standards.
Construction Industry
In construction, tube bending is used for creating structural elements, handrails, and supports. Bending techniques allow for customization of tubes to fit architectural designs and structural requirements, enhancing both functionality and aesthetics.
Furniture Design
Tube bending is also utilized in furniture design to create stylish and functional pieces. Bended metal tubes are used in the frames of chairs, tables, and other furniture items, offering a modern and sleek look while providing strength and durability.
Medical Devices
In the medical field, tube bending is used to manufacture components for medical devices, such as catheters, stents, and surgical instruments. Precision bending ensures that these components meet strict performance and safety standards.
Overall, tube bending is a critical process in manufacturing and fabrication, allowing metal tubes to be shaped into various forms for use in a multitude of applications. This process is essential in industries ranging from automotive and aerospace to construction and furniture design. As a versatile technique, tube bending offers numerous possibilities for designing components with precise dimensions and complex geometries.