Pressure regulators play a critical role in ensuring the safe and efficient operation of equipment and processes in the oil and gas industry. From drilling to refining, maintaining optimal pressure levels is essential for the smooth functioning of systems that involve the handling of volatile substances.
What Are Pressure Regulators?
A pressure regulator is a device designed to maintain a desired output pressure by controlling the flow of gas or liquid from a high-pressure source to a lower-pressure environment. It automatically adjusts the pressure to the required level, ensuring consistent performance of the downstream equipment.
In the oil and gas industry, pressure regulators are used extensively to manage the pressure in pipelines, storage tanks, and processing equipment to ensure safety, reduce risks, and improve efficiency.
Pressure regulators are devices used for controlling fluid pressures within a range. The main function of a pressure regulator is to reduce a high input pressure to control lower output pressure. Pressure regulators can even find applications in situations where constant output pressure is required to be maintained.
The Role of Pressure Regulators in Oil and Gas Operations
Oil and gas extraction, processing, and transportation involve highly pressurized fluids and gases, making pressure regulation essential at various stages. Below are some key areas where pressure regulators are indispensable:
- Drilling Operations: During the drilling phase, pressure regulators are used to control the flow of drilling mud and prevent blowouts. This ensures that the well remains under control even in high-pressure reservoirs.
- Gas Distribution: In natural gas distribution systems, pressure regulators manage the flow of gas from high-pressure pipelines to lower-pressure delivery systems that supply consumers.
- Processing and Refining: Refineries use pressure regulators to maintain the optimal pressure within reactors, distillation columns, and other equipment. Proper pressure regulation ensures that chemical reactions occur efficiently and that safety is maintained in case of overpressure.
- Pipeline Transportation: Long-distance transportation of oil and gas requires precise pressure control to minimize energy loss and ensure the integrity of pipelines. Regulators help manage pressure drops across pipelines and maintain steady flow rates.
- Storage: Pressure regulators control the pressure inside storage tanks, especially when storing liquefied natural gas (LNG) or other compressed gases. This prevents hazardous conditions, such as over-pressurization, which could lead to explosions.
Other applications of pressure regulators are:
- gas grills,
- heating furnaces,
- dental equipment,
- pneumatic automation systems,
- automotive engines,
- aerospace applications,
- hydrogen fuel cells,
- reclaim driving helmets
- pressure cookers and pressure vessels,
- welding and cutting,
- gas-powered vehicles,
- mining and natural gas industries,
- hyperbaric chambers,
- inflating tires, etc
Functions of a Pressure Regulator
As already stated the main purpose of installing a pressure regulator is to reduce the pressure. However, they can effectively be used to perform the following functions:
- Regulating the back-pressure
- As pressure switching valves in pneumatic logic systems.
- As vacuum regulators, to maintain a constant vacuum.
Components of a Pressure Regulator
All pressure regulators are characterized by the reduction of the inlet pressure to lower output pressure. There are three main components that help a pressure regulator perform its intended function are:
- A pressure-reducing valve
- A loading element like an actuator or spring to apply the required force
- A sensing element like a piston or diaphragm.
Refer to Fig. 1 below which shows the schematic diagram of a typical pressure regulator.
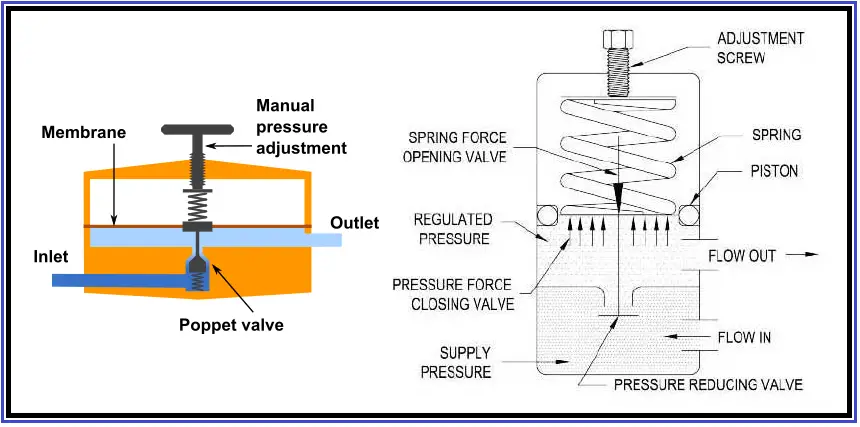
The pressure-reducing valve is also known as the restricting element. It provides a variable restriction to the flow. Examples include a globe valve, butterfly valve, poppet valve, etc.
The loading element is a part that can apply the needed force to the pressure-reducing valve. A weight, a spring, the diaphragm actuator in combination with a spring, or a piston actuator can act as the loading element.
The measuring element or sensing element determines when the inlet flow is equal to the outlet flow. Often, the diaphragm itself works as a measuring element; it can serve as a combined element.
Types of Pressure Regulators
Depending on the number of stages employed to get the final reduced pressure, there are three types of pressure regulators.
- Single-Stage Pressure Regulator: For relatively small pressure reduction in the range of 100 to 150 psi. Used for machine tools, test stands, linear actuators, automated machinery, leak test equipment, etc.
- Dual Stage Pressure Regulator (Suitable for large variations in the inlet pressure), and
- Three-Stage Pressure Regulator: They provide a stable outlet pressure and are able to handle larger pressure reduction. Typical examples are UAVs, medical devices, analytical instruments, hydrogen fuel cells, etc.
Again, based on the working methods they can be broadly categorized into the following two classes.
Self-operated Pressure Regulator: Simplest design. They have greater accuracy at lower pressures and lower accuracy at higher pressures. They do not require external sensing lines for effective operation.
Pilot Operated Pressure Regulators: They are complex in design but can handle larger pressure fluctuations. Pilot-operated pressure regulators provide precise control of pressure.
Based on the application of pressure regulators they are sometimes termed as:
- Water pressure regulator
- Gas pressure regulator
- Fuel pressure regulator
Working of Pressure Regulators
A pressure regulator matches the gas flow through the regulator to the gas demand placed upon it. At the same time, they maintain a sufficiently constant output pressure. When the load flow decreases, the regulator flow also decreases. Again, when the load flow increases, then the regulator flow also increases and thus keeps the controlled pressure from decreasing due to a shortage of gas in the pressure system. The pressure regulators are so designed that the controlled pressure does not vary greatly from the set point for a wide range of flow rates. At the same time, the flow through the regulator is stable and the regulated pressure is not subject to excessive oscillation.
Pressure Regulator Materials
The material of pressure regulators varies depending on the operating environment and compatibility of the fluid handled. Common materials that are used in typical pressure regulators are:
- Brass
- Aluminum
- Stainless Steel
- Plastic
Stainless Steel and sometimes carbon steel are used for spring materials. Seal material is usually Fluorocarbon, EPDM, Perfluoroelastomer, or Silicone.
Selection of Pressure Regulators
Even though pressure regulators are found in various sizes and constructions, Some parameters must be considered for proper selection. Common parameters that influence the selection process of pressure regulators are:
- Operating temperature and pressure range (Both inlet and outlet temperature and pressure)
- Fluid service medium and properties (Gas or liquid, Corrosive or Non-corrosive, Hazardous or Non-toxic, Explosive nature, etc)
- Capacity or flow required (Maximum, minimum, and flow variation)
- Material requirements
- Accuracy required
- Connection Size
- Dimension, weight, and size
Installing Pressure Regulators
Installation of pressure regulators must be performed considering manufacturer guidelines. In general, the following steps are followed for pressure regulator installation:
- Step 1: Connect the pressure source to the inlet port and the reduced pressure line to the outlet port. These ports are usually marked, else contact the manufacturer.
- Step 2: Turn on the supply pressure gradually to avoid any shock.
- Step 3: Set the regulator at the desired outlet pressure. Slight adjustments can be done to get the desired pressure.
Pressure regulators are fundamental to the safe and efficient operation of oil and gas systems. From wellheads to refineries, these devices help control the flow of gases and liquids, protect equipment, and ensure worker safety. By selecting the right type of pressure regulator and maintaining it properly, oil and gas companies can optimize their processes, reduce risks, and comply with environmental and safety regulations.