Spiral steel pipe or spiral welded pipe are other terms for spiral pipe. Steel strip coil is used as the raw material, then extruded at room temperature and welded using an automatic double wire double-sided submerged arc welding technique—the outer diameter. The wall thickness formula defines the requirements of spiral welded pipe, which is utilized for oil and natural gas pipelines. The weld joint’s hydrostatic test, tensile strength, and cold bending performance must all be in line with the regulations for the spiral welded pipe. Spiral welded pipes are available in various sizes. However, they are mostly used for sizes in excess of 20 inches NPS.
Applications of Spiral Welded Pipes
Spiral Welded Pipes are commonly used to convey liquids (oil, water, etc.), gases (air), steam, etc in
- Chemical Industries
- Petrochemical industries
- Water and Wastewater engineering
- Electrical power industry
- Construction industry
- Agricultural industry
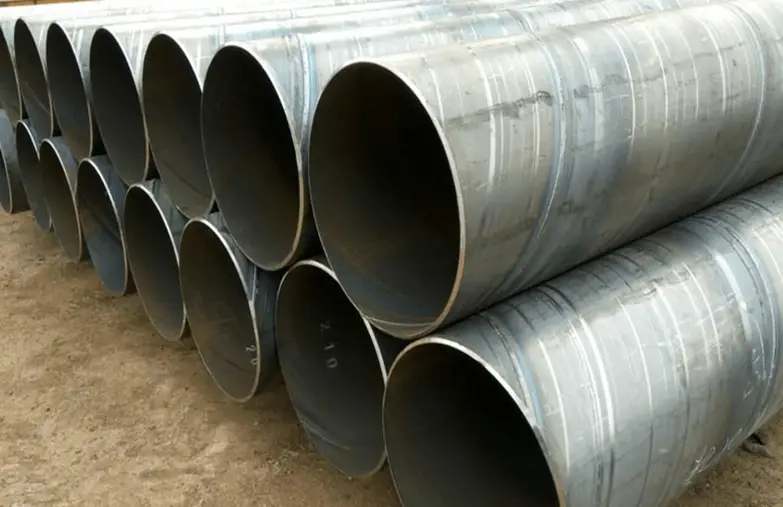
The Spiral Welded Pipe Manufacturing Process
- Steel strip coil, welding wire, and flux are the raw ingredients. Before being used, it must pass stringent physical and chemical tests.
- After the steel pipe is rolled, use automatic submerged arc welding to repair welding using single-wire or double-wire submerged arc welding.
- The strip is leveled, cut, planed, surface cleaned, and pre-bent before forming.
- Control the pressure of the cylinder on both sides of the conveyor with an electric contact pressure gauge to ensure that the strip is conveyed smoothly.
- Roll molding is controlled externally or internally.
- The amount of misalignment and the weld gap are rigorously regulated using the weld gap control device to ensure that the weld gap fulfills the welding standards and the spiral welded pipe diameter.
- Single-wire or double-wire submerged arc welding using Lincoln welding equipment from the United States is used for internal and external welding.
- In non-destructive testing, the final welds were evaluated by an online continuous ultrasonic automatic defect detector, ensuring 100 percent coverage of the spiral welds. If there are any problems, an automatic alarm will sound, and a spray mark will appear, allowing the production worker to alter the process parameters at any time to eliminate the errors as quickly as possible.
- An air plasma cutting machine sliced the spiral welded pipes into individual pieces.
- The spiral welded pipe was tested for mechanical properties, chemical composition, and bonding conditions.
- After manual ultrasonic and X-ray inspection, the part of the weld with continuous acoustic fault detection marks, If the spiral welded pipe has a flaw, must be subjected to nondestructive examination following repair until the defect is proven to remove.
- X-ray television or film is used to inspect the spiral welded pipe where the butt weld of strip steel and the t-joint intersecting the spiral weld are located.
- A hydrostatic pressure test is performed on each spiral welded pipe, and the pressure is radically sealed.
Spiral Welded Pipe Surface Treatment Method
1. Cleaning:
Solvent and emulsion are used to clean the spiral welded pipe surface, removing oil, grease, dust, smoothing agents, and other organic matter. However, it cannot remove rust, oxide skin, flux, or other organic matter from the steel surface. It is used as an additional measure in spiral welded pipe anti-corrosion production.
2. Rust Removal Tool:
The spiral welded pipe is polished using wire brushes to remove loose or elevated scale, rust, welding slag, and other contaminants. The hand tool’s rust removal can reach the Sa2 level, while the power tool’s rust removal can reach the Sa3 level. The rust removal result of the tool is not ideal if the spiral welded pipe surface is attached with a strong iron oxide scale.
3. Pickling:
Chemical and electrolytic procedures are commonly used for pickling disposal. Only chemical pickling can remove oxide scale, rust, and old coatings and is applied as sandblasting following rust removal. Chemical cleaning can achieve the necessary cleanliness and roughness, but the anchor pattern is shallow, making the situation simple to contaminate.
4. Blasting with abrasive materials:
Abrasive blasting uses a high-powered engine to spin the spray (throwing) blade at high speed, allowing abrasives like steel grit, steel shot, wire segment, and mineral to be sprayed (throwing) on the surface of the steel tube under the influence of centrifugal force. Not only can rust, oxides, and dirt be fully removed, but under the influence of abrasive impact and friction, the spiral welded pipe may also achieve the needed average roughness.
After spraying (polishing) and eliminating rust, as well as the mechanical adhesion between the anti-corrosion layer and the spiral welded pipe’s outer surface. As a result, spray (polishing) rust removal is an excellent approach for removing rust from pipes. Sandblasting descaling is mostly utilized for internal and exterior pipe treatment, while shot blasting (sand) descaling is primarily used for pipe surface treatment.
Advantages of Spiral Welded Pipes
(1) Steel pipes of the same width can be utilized to make steel pipes of different diameters, especially when using narrow strip steel to make big-diameter steel pipes.
(2) The spiral weld is subjected to less stress than the straight seam, which is 75 percent to 90 percent of the straight seam welded pipe, and hence can bear immense pressure under the same pressure settings. The wall thickness can be lowered by 10% to 25% under the same pressure as a straight seam welded pipe of the same outside diameter.
(3) The size is precise, with a general diameter tolerance of less than 0.12%, a deflection of less than 1/2000, and an elasticity of less than 1%. In most cases, the size and straightening process is straightforward.
(4) It can be created indefinitely. In theory, it can make infinitely long steel pipes with a minimal cutting head and tail cutting losses, increasing the metal utilization rate by 6% to 8%.
(5) It is more flexible in operation and easy to modify the variety than straight seam welded pipe.
(6) The equipment is lightweight and requires a minimal initial cost. It can be built into a piece of trailer-type portable equipment, and the welded pipe can be produced on-site at the pipeline installation site.
(7) Mechanization and automation are simple to implement.
Disadvantages of Spiral Welded Pipes
Because the raw material is coiled steel, there is a crescent bend, and the welding point is in the elastic strip edge area. Aligning the welding torch is problematic, affecting welding quality. Set up complex weld tracking and quality inspection devices to accomplish this.
Spiral Welded Pipe vs Longitudinal
- As the name suggests, the manufacturing processes of spiral welded pipe and longitudinal welded pipe are distinctly different. While Spiral-weld pipes are rolled and welded according to a preferred helical angle, the longitudinal welded pipes are created by bending and forming metal, and finally welded together down the length of the pipe to create a straight, longitudinal seam.
- Spiral welded pipes are produced using a continuous process under stable working conditions. On the other hand, the manufacturing of longitudinal welded pipes is carried out in stages.
- Longitudinal pipes are normally preferred for smaller-diameter applications whereas spiral welded pipes are best for applications requiring large-diameter pipes with thinner walls.
Spiral Welded Pipe Specification
Spiral welded pipes are also known as helical welded pipes. Common industrial spiral welded pipes are available in the following specifications:
- Materials: Carbon Steel, Alloy Steel, Mild Steel (IS 3589, API 5L, A53, A572, DIN 2458, IS 1239, BS 1387, EN10217, etc)
- Outer Diameter Range: 14″ to 100″
- Wall Thickness Range: 4.8 mm to 25 mm
- Typical Length: Fixed Length of 6m or 12 m, Also manufactured in random length as per requirements.
- Test Certificates: As per EN10204
Common Defects of Spiral Welded Pipes
i) The main cause of the bubbles in the center of the weld bead is hydrogen is concealed within the weld metal as bubbles. Thus, to eliminate this defect, remove the wire and weld the rust, oil, water, moisture, and other things, and then fully dry the flux to remove moisture. Furthermore, a higher current slows the solidification rate of liquid metal, limiting welding speed.
ii) Cracking of sulfur (crack caused by sulfur). The sulfide in the sulfur segregation zone enters the weld metal and causes cracks when welding plates with a strong sulfur segregation zone (particularly soft boiling steel). The explanation for this is the existence of hydrogen in steel and low-melting iron sulfide in the sulfur segregation zone. As a result, using semi-ballasted or ballasted steel with a lower sulfur-containing segregation zone is an effective way to avoid this. Cleaning and drying the weld surface and the flux is also required.
iii) Thermal cracking is a type of cracking caused by heat. Thermal cracks in the weld bead can form in submerged arc welding, particularly at the arc initiating and extinguishing arc craters. Backing plates are installed at the arc starting and arc extinguishing sites to eliminate such cracks. The spiral welded pipe can be reversed and welded into the overlap welding after the coil butt welding. When the weld stress is high, hot fractures are more prone to form.
iv) The presence of welding slag. Welding slag involvement refers to the amount of welding slag that remains in the weld metal.
v) There is a lack of penetration. The overlap between the inner and outer weld metals is insufficient, and the weld is not penetrated. Insufficient penetration is the term for this condition.
References:
- https://www.nucorskyline.com/globalnav/products/pipe/spiralweld.
- https://www.dmitubes.com/spiral-welded-pipes.html.
hi
this is Mr Ghiat from Morocco ,
Dear Anup
if we have any restrictions from standards to avoid manufacturing the pipe miters from spiral welded pipes ?