Two types of storage tank erection methodology have become widely accepted and popular. The first one is the Conventional Method of Tank Erection & the other is the Tank Jacking method. Both of these tank erection methods are accepted by the API 650 and the constructor. The selection of the tank erection method basically depends on the site location or workshop where we are making these tanks.
There is a popular myth that API 650 guides us to adopt the tank erection methodology. But that is not true. API 650 only guides us in the design, fabrication, welding, hydro testing & inspection of storage tanks.
Conventional Method of Tank Erection
In conventional methods, cranes are used for tank erection as a sheet-by-sheet method. At first, the bottom and annular plates are erected. Then the lower course shell is erected and finally, the upper course shell is erected. Refer to Fig. 1 which shows an example of a double-deck floating roof Tank erection by the conventional method. Suppose there are a total of 9 shells in a Tank so the tank erection sequence shall be 1st shell coarse, 2nd shell coarse, 3rd, and then in last 9th shell coarse.
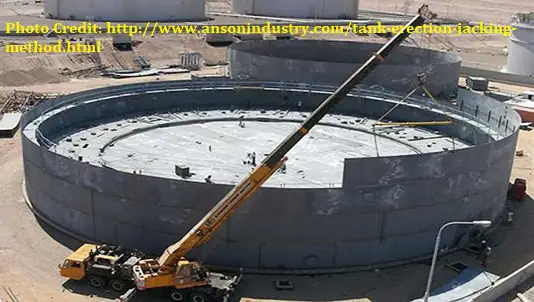
In the case of a small diameter Tank, the tank is fabricated at the workshop and then brought to the site by a trailer for erection. But the handling should be proper to avoid buckling, bending, and any damage.
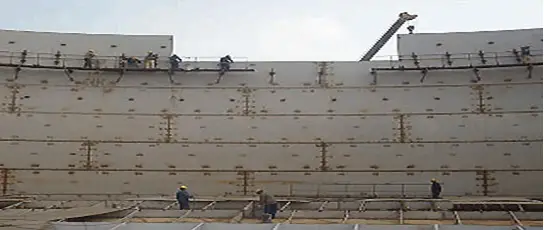
In the case of Shop fabrication, the tank fabrication, erection, & assembly is done by EOT (electric overhead traveling) crane at the shop and then shifted to the site by a trailer.
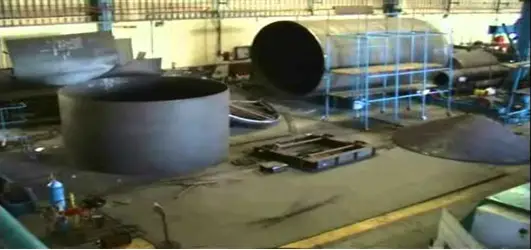
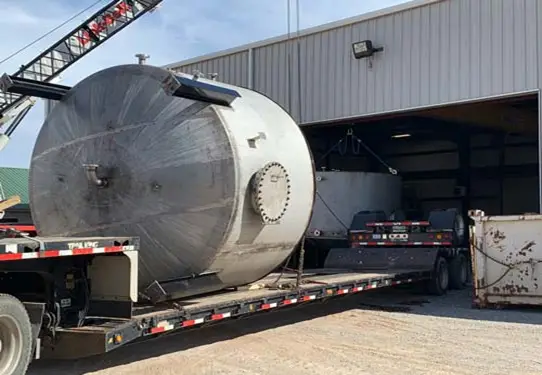
Tank Erection by Jacking Method
A jacking method is an advanced form of tank erection. The jacking method uses the technology of the Swedish Company Bygging Uddemann AB. A number of hydraulic Jacks are placed inside the tank to be erected. Refer to Fig. 5. In recent times this method is widely used in all developed countries.
A system of hydraulic pressure hoses interconnects the hydraulic jacks which are energized by the action of a hydraulic pump.
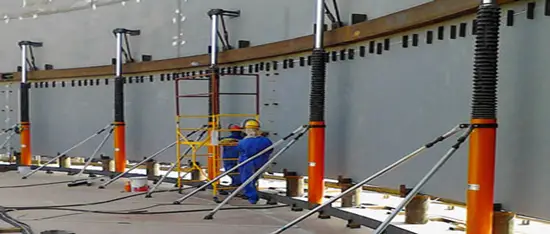
This method is just the opposite of the conventional method. The construction sequence is just the reverse of the conventional one. If there are a total of 9 shell courses, the erection in the jacking method will start from the 9th, then the 8th, 7th, and in the last 1st shell course will be erected.
The number of hydraulic jacks is decided based on the total weight of the roof & shell courses except for the bottom courses. Standard practice is to keep a 3000 mm distance between two jacks. However, the number of hydraulic jacks can be increased to meet additional wind load. Fig. 8 shows a typical jack used for tank erection.
Tank Jacking Procedure
The following steps are followed while erecting tanks by jacking procedure:
- Tank pad to be checked and tolerances to be verified.
- Since jacks are to be mounted on the annular plates, these need to be placed.
- Annular plate joints are to be aligned and welded.
- Next, erect the floor plates and align the joints to complete the welding of the bottom seams.
- After that, Erect the top 2 courses. Align properly and weld. All the works on these two courses including the erection of the curb angle, wind girder for Floating Roof Tanks (or) roof structure, and roof for Cone Roof Tanks, hand railing, etc to be completed.
- Next, Place the hydraulic jacks along the circumference of a circle drawn about 100 mm from the shell plate circle. The maximum arc distance between the two Jacks shall not exceed 3000 mm.
- Jacks are available in 8 T / 12T capacities. So arrange hydraulic jacks of predetermined quantities before starting the erection. Anchor the jack supporting columns to the base plate.
- When, the sub-assembly consisting of the top 2 courses, roof structure/roof (or wind girder) railing, etc. is lifted, erect the shell plates of the third course from the top, after lifting the entire subassembly to the required height.
- Align the vertical joints and weld. Next, the sub-assembly is lowered to complete the alignment and welding of the girth seam.
- The hydraulic jacks can be released and lowered after the alignment of the girth seam,
- In a similar way, erect the other shell courses till all courses are erected.
- Finally, Align the shell to the bottom joint and check for the verticality of the completed tank. Weld the shell to the bottom joint.
- Now, all other balance works like fixing and welding of shell manholes, nozzles, etc. can be completed.
Various terms are used while erecting tanks as mentioned below:
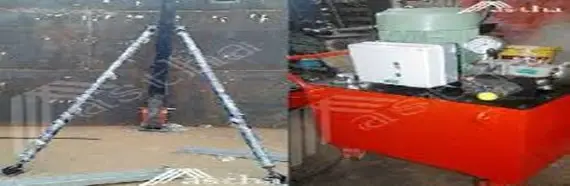
- Power Pack Machine (Fig. 6): This Machine is used to lift the Jack. This machine Pumps the oil to Jack through the hose pipes to lift the jack.
- Stay Pipes (Fig. 6): Also known as supporting pipes; These pipes provide support to jack and trestle pipes. Basically, these pipes are supporting the vertical trestles to maintain verticality.
- Trestle Pipes (Fig. 7): These are the vertical members in the Jacking system that carries loads of Jacks. While installing this assembly we need to take extra care of these vertical members so that the verticality of the Tank is maintained. Jacks Move over the Trestles by teeth. These get support from base plates in the Tank bottom.
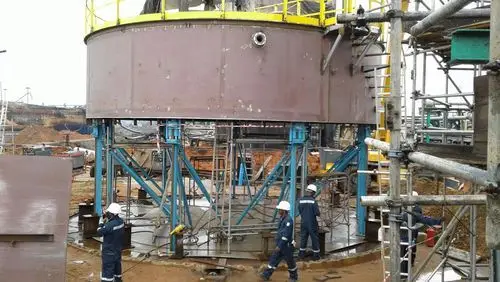
Difference between the Conventional and Jacking Methods
The main differences between the conventional tank erection and jacking tank erection methods are provided in a tabular format below:
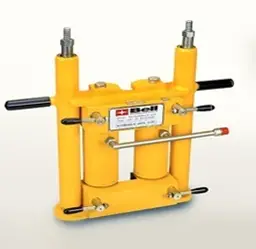
Conventional Tank Erection Method | Tank Erection by Jacking Method |
Suitable for all types of tanks with any diameter and height | Large diameter tanks with higher plate thickness requiring double-sided welding are not possible to erect by this method. Not fully feasible for double-wall tanks. |
Very good dimensional control is possible: Shell and bottom shapes obtained can be close to the designed dimensions. | Dimensional control is comparatively less. |
Erection time is comparatively more | Erection time is less. |
Safety issues as working at height | Safe erection as working at ground level. So lower risks. |
Resource requirement is more, hence more costly | Economical erection. |
Possibility of wind damage while erection. | Protective tank roofs and wind girders eliminate the possibility of wind damage. |
Inspection Access is difficult | Easily accessible |
Lower productivity | Better productivity |
High-capacity cranes are required | The involvement of high-capacity cranes is comparatively less. |
Difficult operation with less efficiency | Smooth operation with high efficiency |
To summarize, the tank erection methodology by jacking method has many advantages over the conventional ones which include easy to operate, safe and reliable, accurate control of the weld gap and the height of the lifting rod, good quality of the project, and providing an outstanding economic benefit.
References and Further Studies:
- https://www.iqpc.com/media/8544/24895.pdf
- https://3.imimg.com/data3/TQ/MO/MY-3035455/tank-erection-jack.pdf
Very good article request you to kindly send me by email rameshraja2004@gmail.com
Very nice and useful topic ….
Sìberia the tank arrived rolled tight in a bobbing it was then stoòd up and pulled out by tracters in minus 40c ànd a final seal welď and then the roof fitted out.
Mine job related article. Plz be continue to share. Shakeel
Usefull. any idea about partial lifting of tank shell for changing of annular plates.
Good Job.
Kindly update shop fabricated tank procedures.
Thank you
Hii, during erection and fixing of top two to three shell plates along with cone roof loads shell change the shape across the width that’s buckling when we measure flatness of individual sheela with 1m steel rule. Can you help me to find how much buckling/ovalty/distortion from flatness for individual shell plates will be accepted as per api 650 or other reference standard.
Very useful article sir
Interesting to know how erecting a tank can be done through the jacking method which incorporates hydraulic pumps to literally jack up the structure. If I was in this industry, I would understand the relevance of trying out different methods that would be most efficient. It would be nice to hire these services as well to ensure that you get the benefits of updated equipment from reputable companies.
VERY GOOD INFORMATIONS.