Super Duplex Stainless Steel (SDSS) has become increasingly popular in industries such as oil and gas, chemical processing, and marine applications due to its exceptional properties. The duplex steel that was created to fight against corrosion, has improved to make SDSS. In this article, we will find the unique characteristics, applications, and benefits of SDSS, focusing on its role in the oil and gas industry.
What is Super Duplex Stainless Steel?
Super Duplex Stainless Steel is a type of stainless steel that combines the desirable qualities of both austenitic and ferritic stainless steel. It contains a mixed microstructure of approximately 50% ferrite and 50% austenite, giving it superior strength and corrosion resistance compared to standard duplex stainless steel. The term “super” refers to its enhanced pitting resistance performance, particularly in highly corrosive environments or extreme stress. The term “Super-Duplex” was initially introduced in the 1980s to denote highly alloyed, high-performance Duplex steel with a pitting resistance equivalent of 38 to 45.
Super-duplex stainless steel is a subset of Duplex stainless steels, which are categorized based on their corrosion resistance and alloy content. Modern Duplex stainless steels are typically classified into four main groups:
- Lean Duplex: Includes grades like 2304, which do not have deliberate additions of molybdenum (Mo).
- Standard Duplex: Such as 2205, which is the most widely used, accounting for over 80% of Duplex applications.
- 25 Cr Duplex: Includes alloys like Alloy 255 and DP-3, which contain 25% chromium.
- Super-Duplex: Characterized by higher chromium content (25-26%), along with increased molybdenum and nitrogen compared to 25 Cr grades. Notable Super-Duplex grades include 2507, Zeron 100, UR 52N+, and DP-3W.
Chemical Composition
The chemical composition of SDSS is carefully balanced to optimize its mechanical and corrosion-resistant properties. The typical composition includes:
- Chromium (Cr): 24-28%
- Nickel (Ni): 6-8%
- Molybdenum (Mo): 3-4%
- Nitrogen (N): 0.24-0.32%
- Carbon (C): Less than 0.03%
- Other elements: Iron (Fe), Manganese (Mn), Silicon (Si), and minor amounts of elements like Copper (Cu).
The high chromium, molybdenum, and nitrogen content provides excellent resistance to pitting, crevice corrosion, and stress corrosion cracking (SCC), which are critical in harsh environments. The following table provides the chemical compositions of a list of the duplex stainless steels covered in ASTM specifications for plate, sheet, and bar products.
UNS Number Duplex Grades | Type | Carbon | Manganese | Phosphorus | Sulfur | Silicon | Chromium | Nickel | Molybdenum | Nitrogen | Copper | Other |
S31200 | … | 0.030 | 2.00 | 0.045 | 0.030 | 1.00 | 24.0-26.0 | 5.5-6.5 | 1.20-2.00 | 0.14-0.20 | … | … |
S31260 | … | 0.03 | 1.00 | 0.030 | 0.030 | 0.75 | 24.0-26.0 | 5.5-7.5 | 2.5-3.5 | 0.10-0.20 | 0.20-0.80 | W 0.10-0.20 |
S31803 | … | 0.030 | 2.00 | 0.030 | 0.020 | 1.00 | 21.0-23.0 | 4.5-6.5 | 2.5-3.5 | 0.08-0.20 | … | |
S32001 | … | 0.030 | 4.0-6.0 | 0.040 | 0.030 | 1.00 | 22.0-23.0 | 1.00-3.00 | 0.60 | 0.05-0.17 | 1.00 | |
S32205 | 2205 | 0.030 | 2.00 | 0.030 | 0.020 | 1.00 | 19.5-21.5 | 4.5-6.5 | 3.0-3.5 | 0.14-0.20 | … | |
S32304 | 2304 | 0.030 | 2.50 | 0.040 | 0.030 | 1.00 | 21.5-24.5 | 3.0-5.5 | 0.05-0.60 | 0.05-0.20 | 0.05-0.60 | |
S32520 | … | 0.030 | 1.50 | 0.035 | 0.020 | 0.80 | 24.0-26.0 | 5.5-8.0 | 3.0-4.0 | 0.20-0.35 | 0.50-2.00 | |
S32550 | 255 | 0.04 | 1.50 | 0.040 | 0.030 | 1.00 | 24.0-27.0 | 4.5-6.5 | 2.9-3.9 | 0.10-0.25 | 1.5-2.5 | |
S32750 | 2507 | 0.030 | 1.20 | 0.035 | 0.020 | 0.80 | 24.0-26.0 | 6.0-8.0 | 3.0-5.0 | 0.24-0.32 | 0.50 | |
S32760 | … | 0.030 | 1.00 | 0.030 | 0.010 | 1.00 | 24.0-26.0 | 6.0-8.0 | 3.0-4.0 | 0.20-0.30 | 0.50-1.00 | W 0.50-1.00; Cr+3.3Mo+16N =40 min. |
S32900 | 329 | 0.06 | 1.00 | 0.040 | 0.030 | 0.75 | 23.0-28.0 | 2.5-5.0 | 1.0-2.0 | … | … | |
S32950 | … | 0.03 | 2.00 | 0.035 |
Properties of Super Duplex Stainless Steel
Corrosion Resistance:
SDSS offers superior resistance to uniform corrosion, particularly in chloride-containing environments. This makes it ideal for offshore platforms, subsea pipelines, and other marine applications.
Its high resistance to pitting and crevice corrosion is particularly valuable in the oil and gas industry, where exposure to seawater and aggressive chemicals is common.
Mechanical Strength:
SDSS boasts twice the yield strength of standard austenitic stainless steels like 304 and 316. This allows for the design of thinner-walled components, reducing weight and material costs.
Its high tensile strength also makes it suitable for high-pressure applications, ensuring structural integrity under extreme conditions.
Stress Corrosion Cracking Resistance:
SDSS is highly resistant to stress corrosion cracking (SCC), a common failure mode in stainless steel exposed to tensile stress and corrosive environments. This resistance is crucial for long-term reliability in oil and gas operations.
Weldability:
While SDSS is more challenging to weld than austenitic stainless steels, it can still be welded using appropriate procedures. The key is to maintain a balanced microstructure and avoid excessive heat input, which could lead to the formation of brittle phases.
Applications in the Oil and Gas Industry
The oil and gas industry demands materials that can withstand extreme conditions, including high pressures, temperatures, and corrosive environments. SDSS is particularly well-suited for several applications in this industry:
Offshore and Subsea Pipelines:
SDSS is commonly used in offshore and subsea pipelines due to its excellent resistance to seawater corrosion and high mechanical strength. It ensures the integrity of pipelines transporting oil and gas from offshore platforms to onshore facilities.
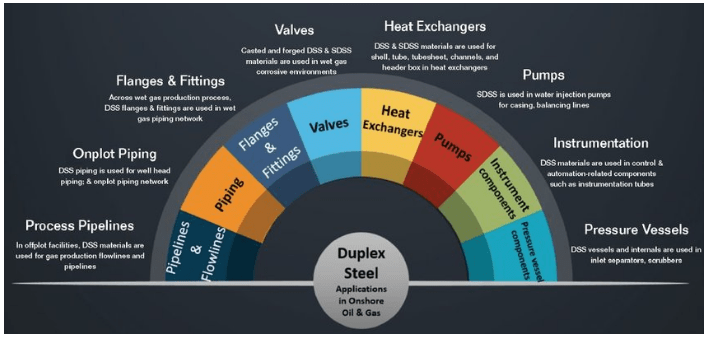
Heat Exchangers:
In oil refineries and petrochemical plants, heat exchangers are exposed to high temperatures and aggressive chemicals. SDSS provides the necessary corrosion resistance and mechanical strength to ensure long-term performance.
Pressure Vessels:
Pressure vessels used in the oil and gas industry must withstand high pressures and corrosive fluids. SDSS’s high yield strength and resistance to SCC make it an ideal material for these critical components.
Valves and Pumps:
SDSS is often used in the manufacture of valves and pumps that operate in corrosive environments. Its durability and resistance to corrosion ensure reliable operation and reduced maintenance costs.
Desalination Plants:
SDSS is also employed in desalination plants, where seawater is processed to produce fresh water. The material’s resistance to pitting and crevice corrosion ensures long-lasting performance in these highly corrosive conditions.
Other applications of Super Duplex Stainless Steel (SDSS) include:
- Tubes and pipes used in the production and transportation of gas and oil.
- Mechanical and structural components requiring enhanced strength and durability.
- Flue Gas Desulfurization (FGD) systems in the power industry.
- Pipes in process industries that handle chloride-containing solutions.
- Utility and industrial systems, including rotors, fans, shafts, and press rolls, where its high corrosion fatigue strength is advantageous.
- Cargo tanks, vessels, piping, and welding consumables for chemical tankers.
- High-strength, corrosion-resistant wiring for demanding applications.
Challenges of SDSS
While SDSS offers numerous advantages, there are some challenges and considerations to keep in mind:
Cost:
The cost of SDSS is higher than standard stainless steels due to its alloying elements and complex manufacturing process. However, the material’s long-term performance and reduced maintenance costs often justify the initial investment.
Weldability:
As mentioned earlier, welding SDSS requires careful control of heat input and post-weld heat treatment to avoid the formation of brittle phases. Proper welding techniques and qualified welders are essential to ensure the integrity of welded joints.
Availability:
SDSS may not be as readily available as standard stainless steel, which could lead to longer lead times for projects. It’s essential to plan accordingly and work with reliable suppliers.
In the end, Super Duplex Stainless Steel is a high-performance material that offers exceptional strength and corrosion resistance, making it ideal for demanding applications in the oil and gas industry. Its unique combination of properties allows for the design of lighter, more durable components that can withstand the harsh conditions typical of offshore platforms, pipelines, and refineries.
Despite its higher cost and welding challenges, SDSS’s long-term benefits, including reduced maintenance and enhanced reliability, make it a valuable investment for critical oil and gas infrastructure. As the industry continues to push the boundaries of exploration and production, materials like Super Duplex Stainless Steel will play a crucial role in ensuring safety, efficiency, and sustainability.
FAQ on Super Duplex Stainless Steel
1. Is Super Duplex Stainless Steel better than SS316?
Super Duplex Stainless Steel (SDSS) generally offers superior performance compared to SS316 in terms of strength and corrosion resistance. SDSS has higher yield strength, which allows for the design of thinner and lighter components, and better resistance to pitting, crevice corrosion, and stress corrosion cracking. However, SS316 may be preferred in less demanding environments due to its lower cost and easier machinability.
2. Is 2205 Duplex or Super Duplex?
Grade 2205 is classified as a Duplex stainless steel, not a Super Duplex. It is a common and versatile grade with a balanced microstructure of austenite and ferrite, but it does not possess the enhanced properties of Super Duplex grades.
3. Is S32750 a Duplex or a Super Duplex?
S32750 is a Super Duplex Stainless Steel grade. It is known for its high chromium, molybdenum, and nitrogen content, which provides superior corrosion resistance and strength compared to standard Duplex grades.
4. What is the ASTM grade for Super Duplex Stainless Steel?
The ASTM grade commonly associated with Super Duplex Stainless Steel is ASTM A890. This standard covers various Super Duplex grades, including ASTM A890 Gr. 1A (UNS S32750) and ASTM A890 Gr. 1B (UNS S32760).
5. What is Super Duplex Stainless Steel density?
The density of Super Duplex Stainless Steel typically ranges between 7.8 and 8.0 grams per cubic centimeter (g/cm³). The exact density can vary slightly depending on the specific alloy and heat treatment.
6. What is the Super Duplex Stainless Steel price per kg?
The price of Super Duplex Stainless Steel can vary based on market conditions, supplier, and specific grade. As of recent estimates, the price typically ranges from $6 to $15 per kilogram. For the most accurate pricing, it is recommended to contact suppliers directly or check current market rates.
7. What are Super Duplex Stainless Steel casting grades?
Super Duplex Stainless Steel casting grades include:
- ASTM A890 Gr. 1A (UNS S32750)
- ASTM A890 Gr. 1B (UNS S32760)
These grades are designed to provide superior mechanical properties and corrosion resistance in cast forms.
8. What are the Super Duplex Stainless Steel pipe fittings?
Super Duplex Stainless Steel pipe fittings are components designed to connect, control, or regulate the flow of fluids in pipelines. Common fittings include:
- Elbows: Used to change the direction of the pipe.
- Tees: Used to split or combine flow in a pipeline.
- Reducers: Used to connect pipes of different diameters.
- Flanges: Used for connecting pipes, valves, and other equipment.
- Caps: Used to close the end of a pipe.
- Couplings: Used to join two pieces of pipe together.
These SDSS pipe fittings are available in various sizes and configurations to match the requirements of different piping systems.
Thank you for your wondaful articles
Hi
Thank you for the comprehensive article about SD. Could you advise how to find the altentave to ASME/ASTM material grade in BSEN?
Regards,