As per layman’s language, Piping Stress analysis is the analysis of stresses in the piping system. Now the question arises what are these stresses? Piping Stress is generated whenever a load acts on a piping system and tries to deform it. Due to the inertia effect, the piping system will resist that force with an internal resistance force creating stress. So, first, we need to know the loads that create these stresses. There are various kinds of loads that generate stresses in a piping system as listed below:
- Weight Loads: Pipe Weight, Fluid Weight, Insulation Weight, Valve, Actuator, Flange Weights (Rigid Weights), Snow weight (in snowfall areas), Sand Weights (where frequent sand storms happen); Rail and Truck weights for buried piping.
- Pressure: Internal and External Design and Operating Pressures, Hydrotest Pressure.
- Temperature Change: Both maximum and minimum temperature range, Black Bulb temperature, steam out temperature condition.
- Occasional Loads: Slug force, Surge force, Vibration, Seismic Events, High-Speed Winds, Relief Valve popping, Settlement.
As we know the loads that create stresses in a piping system, let’s proceed to explore the types of stresses in a Piping System.
Types of Piping Stresses
The following kinds of piping stresses are generated in a piping system.
Normal Stresses
Normal stresses act in a direction normal to the face of the material crystal structure. Normal stresses may be tensile or compressive and can be applied in more than one direction depending on the application and type of loads. Three types of normal stresses exist in a piping system. They are:
- Longitudinal or Axial Stress
- Hoop or circumferential Stress and
- Radial Stress.
Axial Stress or Longitudinal Stress in a Piping System:
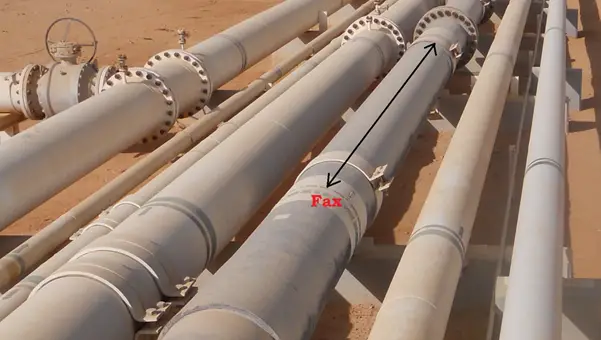
Axial Stresses or Pipe Longitudinal Stresses are the normal stresses that act parallel to the longitudinal axis of the pipe centreline axis. In a piping system, Longitudinal stress can be generated for three reasons:
- An Axial force of some kind
- Internal Design Pressure
- Bending Moment
Refer to Fig. 2 and let’s assume that force Fax is acting in the pipe Axially. So this force will generate axial pipe stress or longitudinal stress in the pipe metal, SL
Hence, The Longitudinal Stress, SL=Fax/Am.
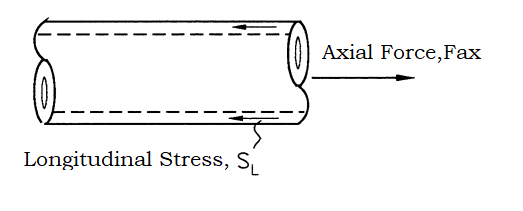
Here, Am is the pipe metal cross-sectional area that can be calculated as follows
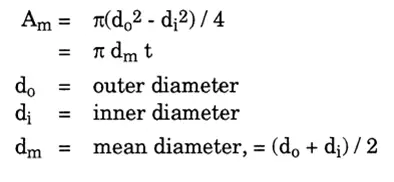
Now this Axial Load, Fax can be created due to internal pressure, P which acts on internal pipe area Ai. So in that situation, the longitudinal force will be given by:

As dm is always greater than di, P di2/4dmt <Pdi2/4dit = Pdi/4t
Conservatively, the longitudinal pressure stress is approximated as
SL=Pdo/4t
Again, the axial load, Fax can be generated by bending which is given by the following equation:
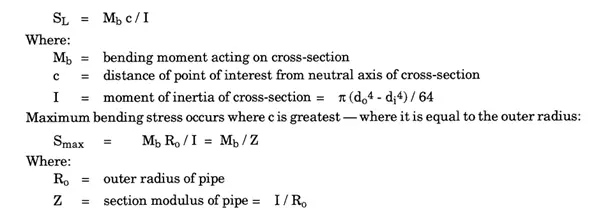
Now adding all the above component stresses we get,
SL=Fax/Am+Pdo/4t + Mb/Z
Hoop Stress or Circumferential Stress in a Piping System:
The Normal Stress that acts perpendicular to the axial direction or circumferential direction is known as Hoop Stress. Hoop stress is caused by Internal pressure.
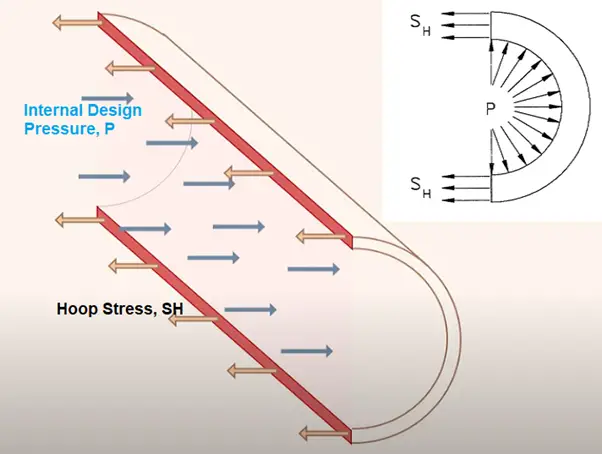
The Hoop stress is conservatively calculated as
SH=Pdo/2t
As can be seen from the simplified equations of pressure stresses, Hoop stress is twice the longitudinal stresses and hence is of utmost importance.
Pipe material thickness is normally calculated/decided considering this Hoop Stress Equation.
Radial Stress in a Piping System:
Radial Stress is the normal Stress that acts parallel to the pipe radius and is caused by internal pressure. It varies between the internal design pressure at the inside pipe surface and atmospheric pressure at the outside pipe surface as shown in Fig. 4 below.
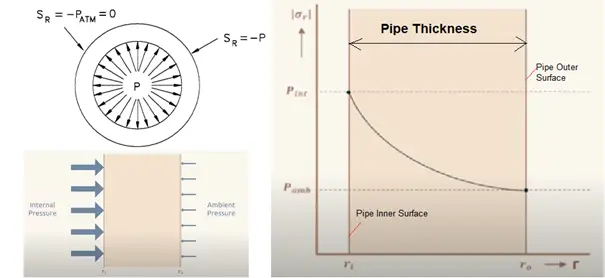
Now if we compare, radial stress with respect to longitudinal pressure stress or hoop stress we can find that radial stress is many times lesser than those two stresses. This is the reason radial stress for piping systems is ignored most of the time.
Shear Stress in a Piping System:
Shear stresses act in a direction parallel to the face of the plane of the material crystal structure. This stress provides a slipping tendency to one plane against the other. Shear forces can be caused by
- the shear forces acting on the pipe cross-section or
- the twisting or torsional moments.
Since the shear stresses caused by shear forces in a piping system are very small, this is neglected. However, Shear Stresses caused by torsion are of considerable amount.
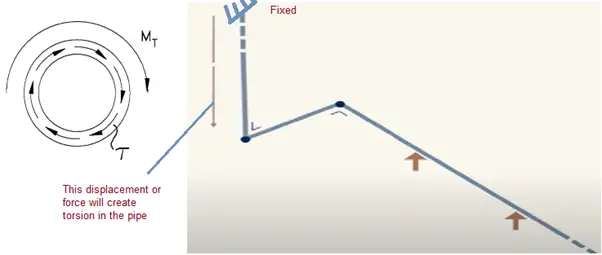
Shear Stresses caused by torsion are calculated by the following equation:
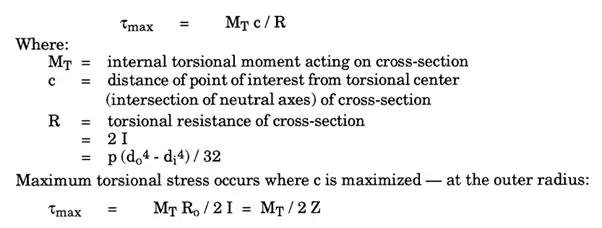
Thermal or Expansion Stresses in a Piping System:
Thermal or expansion stress in a piping system is generated when the free thermal movement of the pipe is restricted. The pipe is installed at ambient or atmospheric temperature and during operation, it carries fluids of different temperatures. So with a change in temperature, the pipe length is changed. As this free thermal movement is restricted by the supports or end equipment connections expansion stress is created.
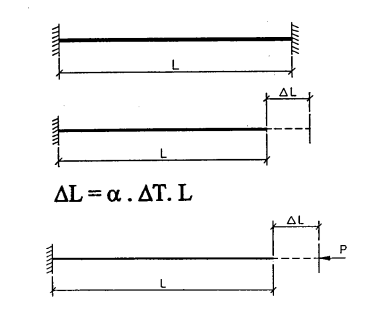
In the above figure due to the change in temperature ΔT, the pipe length changes ΔL= α.ΔT. L.
Thermal Strain= ΔL/L= α.ΔT
So Thermal Stress= Thermal Strain X E= E.α.ΔT
Piping Stress Types as Per Piping Code
As per the piping code, piping stresses are categorized into three groups.
- Sustained Stress
- Expansion Stress and
- Occasional Stress
Sustained stress is the stress present throughout the plant operating life. Weight and Pressure are called Sustained stresses.
Expansion stress is a displacement-driven secondary stress generated due to temperature changes from installed to operating conditions.
Occasional stresses are stresses those are present in a piping system for a very short period of time. Stresses due to Seismic events, Surges, Wind, Vibration, etc. are called occasional stresses.
Few more related resources for you.
Basics of Pipe Stress Analysis
What does a Pipe Stress Engineer need to know?
Piping Stress Analysis Basic Theories
Piping Stress Analysis using Caesar II
Piping Stress Analysis guides using Start-Profs
Video Tutorial on Pressure Stresses in Piping System
The following video tutorial by the EngineeringTrainer team provides a very clear insight into the pressure stresses in the piping system.
Anup Sir please Explain why sustain and expansion stresses they have different allowable limits in code? Is there any derivation for that? Why sustain and expansion two different stresses exist? Why don’t we calculate stress for direct operating case(W+P+T+D) using principles stresses and theories of failure like von mises?Please Explain in brief.
Very nice blog
Made by hard work
You have good articles but somehow i guess people do not appreciate your work by encouraging you with comments.
Well explained Sir!! Really fruitful!!
The article is very important. I would like to receiver technical literatura about stress pipings.
Very educative article
Well articulated.
Very well explained Sir.
A perfect synthesis of the fundamental concepts of Piping Stress Analysis. I have saved the pdf of this article as a basic reference handbook.
what about Hoop Stress considerations according to ASME B31.4??