User-defined SIF is the stress intensification factor that the user input into the stress analysis program. The SIF values are usually calculated using FEA programs and then manually entered in the input screens of the stress analysis programs. To increase the accuracy of the output results of a stress analysis problem using the beam method, It is always suggested to extract the amount of SIFs from a Finite Element Analysis (FEA) and then implement them in stress programs like CAESAR II, AutoPIPE, Start-PROF, or Rohr II.
With the deletion of Appendix D from the 2020 edition of ASME B31.3, the use of ASME B31J and other FEA programs will be increased while stress analysis of piping systems. Hence, User-defined SIF values will be very important for stress analysis aspects.
For a branch connection (Tee), The user has to put the amount of extracted SIFs in all 3 elements that form the connection, i.e. two elements for the header and one for the branch, considering the fact that the amount of SIFs for the branch and header are different. For example, for the connection shown in the below figure (Fig. 1), the amount of the header SIFs is entered at nodes 20.1 and 20.2 while the branch SIF is defined at node 20.4.
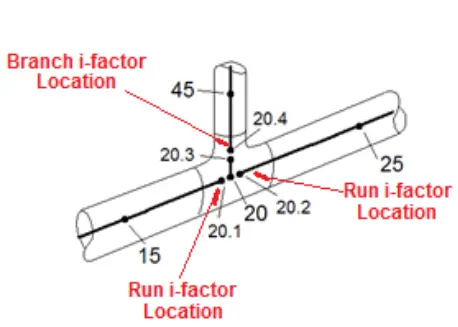
In order to do this, the “SIFs & Tees” box in elements 20.4-45 should be checked, and then the In-Plane and Out-Plane SIFs and also torsion and axial SIFs (if it is necessary) are defined at node 20.4. The same method should be implemented for header elements (at nodes 20.1 and 20.2). The key point in this method is that referring to Fig. 2 below, the type of connection must be blanked.
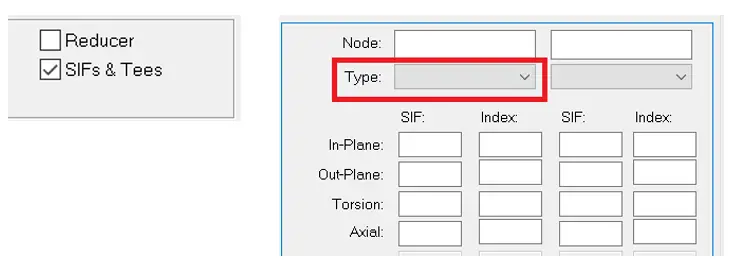
Indeed, in the old method of defining of SIFs, when the type of connection (such as UFT, RFT, and …), is determined in one node, the program will consider that node as an intersection and apart from the calculation of the amount of SIFs, the “Effective section modulus” named “Ze” in B31 codes, is used for the calculation of the amount of the stresses in the branch section.
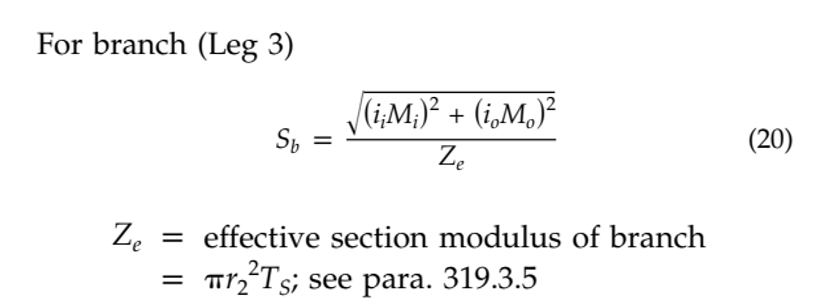
But, In the new method, since the value of branch SIFs is extracted and defined directly, therefore, the section modulus of the branch pipe must be used instead of the effective section modulus. This issue has been mentioned in the edition 2016 of the B31.3 code:
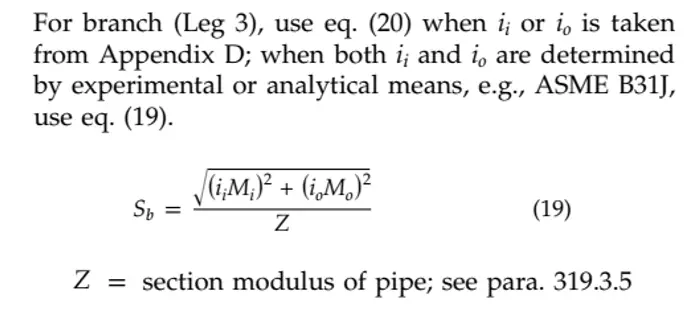
In Caesar II, When the type of an intersection is left blank, the real section modulus of pipe elements will be used in stress calculation.
However, leaving the type section blanked causes a problem that must be considered by the user and then a proper solution must be implemented as has been described in the following.
What is the problem? What is the solution?
In Caesar II, as soon as the “SIFs & Tees” box is checked for a particular node and then the type of connection is determined, that node will be considered as an intersection and both the in and out planes will be specified automatically. The procedure of how Caesar II determines these planes has been described in the “User Guide” of the program.
But if the type of connection is not determined, the related node won’t be considered as an intersection and then the in and out planes won’t be determined.
Indeed, using the new method for SIFs determination and when the type is not specified, the program will assume that the user is defining the SIFs for 3 straight elements separately. The In-plane and Out-Plane directions are meaningless for a straight element. However, the program will consider these directions even for a straight element based on the procedure that has been mentioned in detail again in the “User Guide” and then each SIF is assigned to the relevant plane(direction).
The main concept of the Caesar II program for the determination of the in and out planes of a straight element is that there are local coordinate directions and axes for each element named a, b, and c and the program always considers the moment around the b axis as the In-plane moment. The local coordinates in Caesar II are defined in this order:
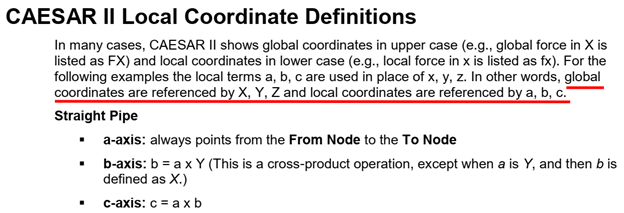
But, sometimes, based on the orientation of an intersection in the global coordinate system, the In-Plane and Out-Plane directions of the 3 straight elements that form that intersection will be different from the real In-Plane and Out-Plane directions of the mentioned connection. In this case, in order to force the program to calculate the stresses correctly, the extracted SIFs from FEA software are needed to be entered in reverse order.
Some examples
Please consider the below example (Fig. 6) for instance:
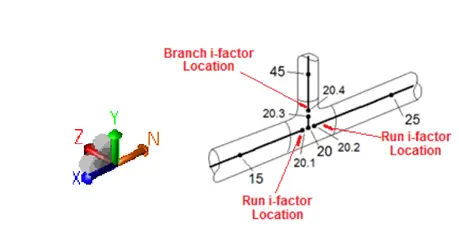
Referring to the above figure it is obvious that for this intersection, the moment around Z-axis is the In-plane bending moment while for the straight element from node 20.4 to node 45, the moment around X-axis will be the In-plane moment. Now, assume that the In-Plane and Out-Plane SIFs related to the branch side of this connection have been extracted from an FEA program as 3 and 11 respectively and the user wants to import them in Caesar II and at node 20.4. Based on what was mentioned above, these amounts need to be imported in reverse order as has been shown in the below figure (Fig. 7).
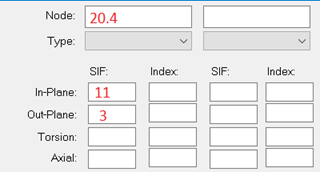
Considering the straight elements of the header, it is obvious that the MZ is the In-Plane moment for both the straight elements and also the connection itself. Therefore, there is no need to import the extracted SIFs of the header in reverse order.
Now, please consider another example referring to the below figure.
This is a welding Tee and the amount of In-Plane and Out-Plane SIFs are 2.55 and 3.067 respectively. The outer diameter and the thickness of the header and branch are shown in the following figure.
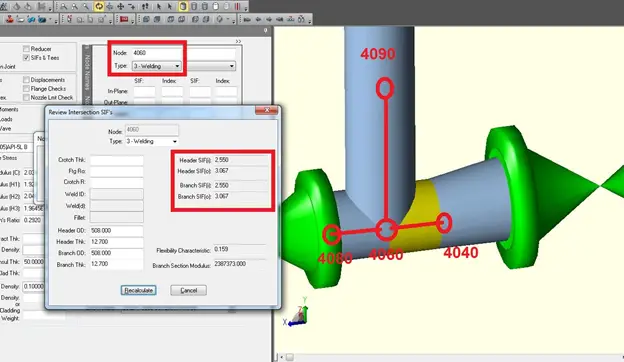
In the first try, the “SIFs box” of the connection has been checked at node 4060 and on the element 4040-4060.
Referring to the below figure (Fig. 9), the amount of bending stress at the branch section is 71.25 Mpa
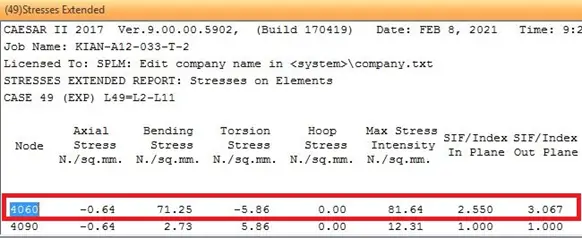
On the next try, the SIFs of the branch element are imported equal to what was obtained on the first try and also the type of the intersection is left blanked. We may expect to obtain the same results!
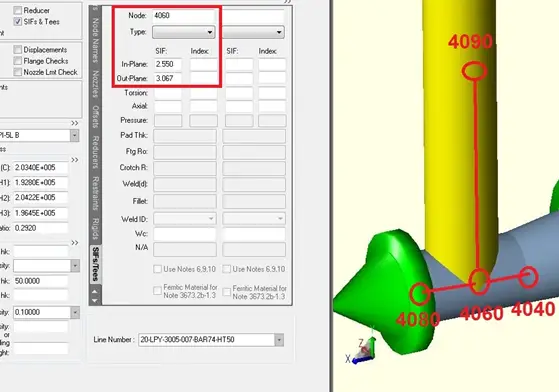
But, The below figure reveals that the bending stress has changed to 78.41 Mpa.
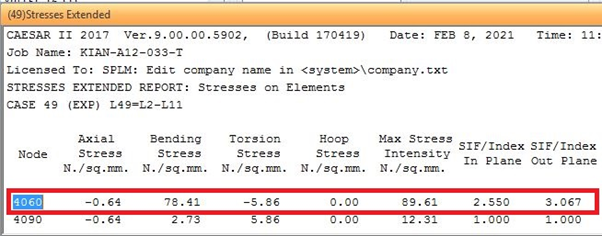
In the last try, the obtained values of the In-Plane and Out-Plane SIFs are imported again, but, this time in reverse order, and the type is left blanked again.
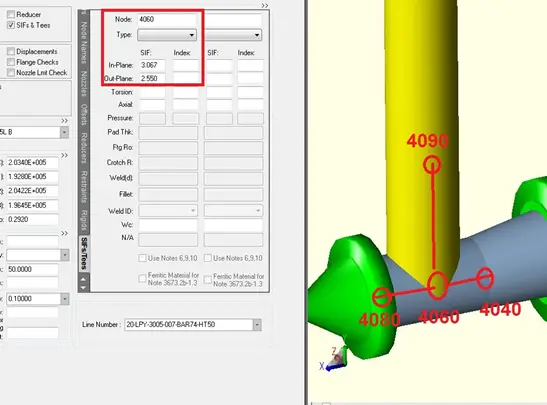
Referring to the below figure, the amount of bending stress at node 4060 is again 71.25 Mpa similar to what was obtained on the first try.
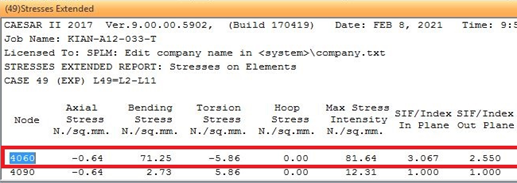
Indeed, for this intersection, the In-Plane direction of the branch straight element is different from the real In-Plane direction of the connection and therefore the SIFs must be imported in reverse order in order to calculate the bending stress correctly.
Finally, it should be noted that the approach of the B31.3 code is that in the absence of more applicable data, the axial SIF is supposed to be equal to Out-plane SIF (only for branches). Therefore, if the extracted Out and In-Plane SIFs are needed to be imported in reverse order, you will also have to import the amount of axial SIF manually and equal to the real Out-plane SIF of the connection in order to force the program to calculate the total code stress correctly. You may also get the axial SIF from a better source such as an FEA.
Few more related articles for you.
Stress Intensity Factor (SIF), Flexibility Factor: ASME B31.3 vs ASME B31J
Piping Elbow or Bend SIF (Stress Intensification Factor)
How to use ASME B31J-2017 and FEM for SIF and k-factors for Stress Analysis
Importance & Impact of Stress Intensification Factor (SIF) in Piping
Thanks for explaining this SIF issue so clearly. I was often puzzled about the different stresses I would get in caesar 2018, when I check and uncheck the branch type field while entering user defined SIF at branches. Also these problems were happening in some branches and not in other branches..
Going through the article helped me in understanding the real reason behind the anomaly..
Would request you check the line mentioned in your article:
“Referring to the above figure it is obvious that for this intersection, the moment around Z-axis is the In-plane bending moment while for the straight element from node 20.4 to node 45, the moment around X-axis will be the In-plane moment.”
Shouldn’t it be “moment around X-axis will be the Out-plane moment”
I I believe it is correct. The straight element from node 20.4 to 45 is along Y global axis and so the local axis “b” is defined as X global. Therefore, the moment around X (Mx) will be the
In-Plane moment for this straight element. Indeed, in this example the In-plane directions of the Tee itself and the straight element of the branch, are different and this causes the mentioned problem.
I hope it helps.
Ok. Thanks. Understood.
I had it confused that we are talking in respect of the fitting and not the single element..
Very good and indeed post.
The problem persists when we are calculating Branch stresses
1. in Reduced branch intersection (i.e. d/D<=0.5 & D/T<100)
2. when effective section modulus turned on in configuration file.
We can eliminate this problem by turning off effective section modulus in configuration file when we are using B31J or FEA SIFs.
We have issues when we are mixing SIFs in a single calculation (app D SIF for some branches and B31J or FE SIF for some branches)
Can you tell me which Item in CFG editor you’re talking about?
There are some options like “Reduced Z fix” and the other “Reduced Intersection”, and both are related to B31.1 not B31.3.
The method mentioned in this article works for all codes.
This method is also implemented automatically by FEA TRANSLATOR and the SIFs will be imported in reverse order, whenever is needed.
so applicable paper…
thanks