Vibration monitoring can be defined as the monitoring of the rotary equipment (pumps, compressors, turbines, fans, etc.) using a set of tools to find out equipment health continuously or at a predetermined interval that can develop vibration (or equipment malfunction) in the system. These tools sense the vibration signals and convert them into some physical phenomena so that the condition of the equipment’s health is determined. In this article, we will explore the vibration monitoring basics.
Why is vibration monitoring important?
Vibration with plant machinery is a serious problem with plant operations. Its severity sometimes leads to even plant shutdown. So It must be monitored. Vibration monitoring systems help to detect equipment damage or malfunction in good time to prevent major consequences like equipment failure or plant downtime.
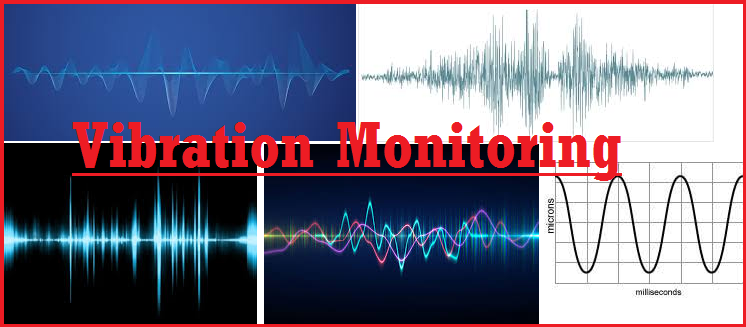
Machinery in an operating plant requires attention to perform at desired levels of performance-approach towards equipment. Various types of maintenance approaches are taken for rotary equipment as listed in Fig. 1:
Condition Monitoring
The main advantages of condition monitoring are:
- Extended asset life
- Reduced maintenance costs
- Cost savings on prematurely replaced resources
- Reduced downtime
Condition monitoring can be of two types:
- A) Vibration Monitoring: Online vibration monitoring and Offline Vibration Monitoring.
- B) Lubricating Oil Monitoring: Oil properties analysis and wear Debris analysis.
Online Monitoring
In Online condition monitoring, the rotary equipment is continuously monitored. So, online monitoring is a non-interrupted permanent process that produces data continuously including the most critical moments.
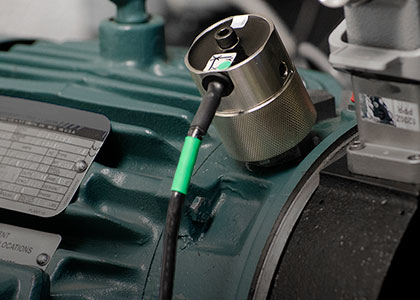
The major features of online vibration monitoring are:
- Permanently mounted probes.
- All rotary equipment above 500 KW.
- Bently Nevada makes systems
- Shaft Vibration as well as Casing Vibration.
- Provide real-time data for equipment health.
- Vibration sensors are wirelessly connected to a remote condition monitoring system.
Online vibration monitoring is applied to:
- Monitor Highly Critical Assets
- Monitor Troubled Assets
- Monitor Hard-to-Reach Assets
Offline Monitoring
Offline vibration monitoring is employed for less critical equipment where a periodic check is sufficient. Manual or Semi-automated equipment is used for offline monitoring. The main features of offline condition monitoring are
- Periodic Data collection
- Portable and Semi-Automatic Data Analyzers.
- All Rotary equipment above 22 KW up to 500 KW.
- CSI Make System
Condition of Equipment
Physical Condition:
- Appearance
- Color
- Temperature
- Vibrations
- Sound or Noise
- Looseness
Internal Condition:
- Vibration Spectrums
- Frequency Analysis
- Rotor Position
- Bearing Metal Temperature
- Oil Condition – Oil Degradation, Metals, Wear Particles in Oil.
Three Stages in Vibration Monitoring
- What to measure from the machine? Identification of parameters and machine
- How to measure? Instrumentation requirement
- When to measure? Frequency of CM
Basics of Vibration
What is Vibration?
Vibration can be defined as the cyclic or oscillating motion of a component from its mean position.
Units of Vibration Measurement
- Displacement: m, mm, microns. mils
- Velocity: m/sec, mm/sec, in/sec
- Acceleration : m/sec2, g
What causes Vibration?
Various factors can cause vibration in a system like
- Unbalance
- Misalignment
- Shaft and Bearing Wear
- Bent shaft
- Mechanical Looseness
- Eccentricity
- Resonance
- Anti-friction bearing
- Journal bearing
- Aerodynamics and hydraulic problem
- Electrical problem
- Gear problem
- Belt-drives problem
- Bearing Failure
Units of Vibration:
- Amplitude: It is the magnitude of the vibration signal. How much is it vibrating? Size (severity) of the problem.
- Frequency: How many times does oscillation occur for a given time period? What is vibrating? Source of the vibration.
- Phase Angle: The Phase Angle is the angle (in degrees) the shaft travels from the start of data collection to when the sensor experiences maximum positive force. How is it vibrating? Cause of the vibration.
Units of Amplitude
- Displacement: The distance a structure moves or vibrates from its reference or rest position.
- Velocity: Rate of change of displacement. It is the measure of the speed at which the mass is vibrating during its oscillation.
- Acceleration: It is the rate of change of velocity. The greater the rate of change of velocity the greater the forces (F=ma) on the machines.
When To Use Displacement / Velocity / Acceleration (Fig. 4)?
Systems / Tools for Vibration Monitoring
Transducers (Fig. 5):
It is a basic device, which converts mechanical motion into an electrical signal which can be amplified, filtered, analyzed, and displayed to indicate the vibrations and allow diagnosis of the overall machinery health.
Seismic Sensor –
- Works on piezo-electrical / moving coil principle
- Indirect measurement of shaft vibration.
- Directly mounted on machine casing / bearing house.
- Absolute vibration in terms of mm/sec or g
The VELOCITY PICK-UP is a contact-type transducer.
Within the velocity pick-up, a spring-mass suspension system is used, which is designed to have a low frequency. It is a permanent magnet mass suspended on a spring and surrounded by a coil attached to the protective housing. Damping fluid is used to dampen the natural frequency Velocity pick-up is limited to low frequency (between 10 Hz and 1500 Hz) for practical purposes.
Accelerometer (Fig. 6)
The accelerometer consists of a stack of piezoelectric crystals (such as quartz) to which a mass is attached.
When a piezoelectric crystal is stressed, it produces an electric voltage output that is proportional to the stress/force. When the accelerometer is attached to a vibration body, the crystal is stressed by the inertia of the mass caused due to the vibration. The electrical voltage output is proportional to the vibration acceleration.
Vibration Signals for Vibration Monitoring
- A frequency that is an integral multiple (´2, ´3, etc.) of a fundamental (´1) frequency.
- Sub-harmonic- A frequency that is an integral submultiple (´1/2, ´1/3, etc.) of a fundamental (´1) frequency.
- Vibration components (on rotating machinery) that are related to shaft speed.
- Sub-synchronous- Components of a vibration signal whose frequency is less than 1´ shaft speed.
- Unidirectional vibrations. i.e. severity is more in radial directions as compared to axial.
- The phase difference is 90° in radial directions.
- Highly sensible w.r.t. machine rpm. It is directly proportional to machine speed.
Frequency Spectrum(Fig. 8) for Vibration monitoring data
Frequency Spectrum is a plot of frequency V/s amplitude. The frequency axis may be scaled indirect frequency units Hz or in order of shaft rotative speed ie. 1X, 2X, etc. depending on the requirement. Baseline data can also be superimposed on the existing data to view changes in rotor response from known conditions.
BODE PLOT (Fig. 9) for Vibration Monitoring Data
Bode Plot is a transient data plot and the display is either 1X or 2X vibration amplitude and phase with respect to shaft rotative speed. This plot is only available as startup or shutdown data.
This plot is useful in determining the slow roll speed range, balance resonant frequencies, synchronous amplification factor, heavy spot location, and rotor mode shape.
Very informative presentation on vibration monitoring. Thanks for sharing the content!
Dear Mr.Anup
can you help me to sent my presentation for vibration level 1