Zero Velocity Valve consists of a Power-assisted Spring-loaded closing disc that prevents the reverse flow when pump trips. These valves protect the system from harmful water hammers or surge problems. The design principle of Zero velocity valves is to arrest the quick-moving water column at zero velocity. So it eliminates the establishment of any return velocity which subsequently eliminates pressure peaks.
The zero-velocity valve constitutes an outer shell and an inner fixed dome. In the center, the valve closing disc is mounted. One or more conical compressed springs held this disc in a close position in situations when there is no water flow. A bypass connects the upstream and downstream of the disc. The springs produce such forces that the disc will be in a fully open position when the water velocity is 25% of the maximum design velocity. Again, when the velocity becomes less than 25% of the maximum velocity, the disc starts closing and fully closed at zero velocity. At this stage, the upstream water column is prevented from creating pressure surge waves.
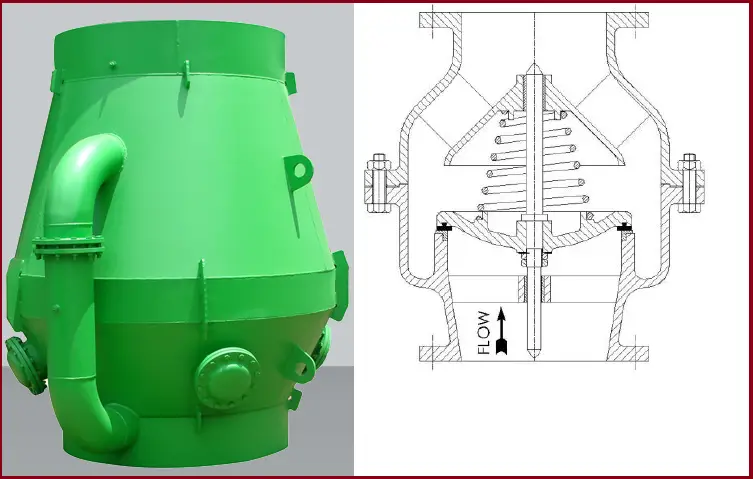
Zero velocity valves are made of barrel or flanged ends as per requirements. To keep the valve free from corrosion, a high-quality epoxy coating finish is provided.
Advantages of Zero Velocity Valves
As the zero velocity valves are self-actuating, they can be installed at remote locations. The major advantages of Zero-velocity valves are:
- Controlled closing characteristics and
- Low head loss due to the streamlined design
Other benefits of a zero-velocity valve include
- Long life
- Low maintenance
- Trouble-free, smooth operation
- Robust construction provides heavy-duty operation.
- High-quality leak-proof sealing
- Cost-effective solution
- Easy installation
- Silent operation.
Working Principle of Zero Velocity Valves
The working principle behind the design of zero velocity valves is to arrest the forward-moving water column at zero momentum. When the velocity is zero, no return velocity is established.
When a pump suddenly trips, the forward velocity of the water column decreases due to gravity and friction. When the forward velocity becomes less than 25%, the flaps of the zero-velocity valve close at the same rate as the water velocity. The flap comes to the fully closed position when the forward velocity approaches zero magnitudes. Thus the water column on the upstream side of the valve is prevented from getting a reverse velocity to create a pressure surge. The bypass valve maintains balanced pressures on the disc. It also avoids the vacuum creation on the downstream side of the valve if that column experiences a certain reversal.
Installation of Zero Velocity Valves
The following steps are usually performed while installing zero-velocity valves in piping/pipeline systems:
- Clean the pipeline thoroughly by flushing it to remove any material that may damage the valve.
- Clean the valve from the inside and outside to remove any foreign particles.
- Zero velocity valves are usually installed in horizontal or inclined pipelines.
- During installation ensure proper alignment of the valve flange and pipe flange.
- Adequately support the upstream and downstream piping
Zero velocity valves are usually manufactured of carbon steel, cast iron, S.G. Iron, cast steel, and fabricated steel material. However, depending on the requirement, other materials can be used. The common size range for the zero velocity valves is 80 mm to 3000 mm.
Hi sir, I’ve read the information about the Zero velocity valve and it is very much useful for me.Now Iam confused about the installation of Zero velocity valve.Can you tell me the approximate distance of fixing the Zero velocity valve from pump house.
totally confused….if momentum becomes zero how comes velocity take it forward. This valve is known only in INDIA as there is now way it can be tested
need your guidance