Fitness-for-Service (FFS) is an assessment method using the best industry practices and standards to ensure the structural integrity of any asset or component. The FFS evaluation process confirms if any asset/component is suitable for its intended purpose. Also known as Fitness for Purpose, the Fitness-for-Service assessment gives a quantitative measure of asset integrity management for the in-service components. The FFS assessment methods highlight repair or replacement needs for the asset.
The fitness for service assessment methods is used to assess the critical pressurized components and welded elements for identification of the mitigation needs to safely use the assets. Various industries such as power generation, process plants, aerospace, oil and gas, marine industry, etc make use of fitness for service methods throughout different stages of the asset’s lifecycle.
Example of Fitness for Service Assessment
Let’s understand an example of fitness for service assessment requirements. A pipeline has been transferring crude oil for the past 10 years from location A to location B with a certain pressure and temperature. Let’s assume the pipe size is 24 inches and the initial design thickness was 12 mm. During one of the inline inspections using Intelligent pigs with sensors, it detects certain anomalies such as corrosion, cracks, and dents. In most locations the anomalies are minor and within the acceptable range. However, in one location of the pipeline, it is found that the material thickness has corroded expensively and only 3 mm of material is remaining. So, the situation is very dangerous, and needs to decide whether the pipeline should be kept in operation or not. In such a situation, the Fitness for Service Assessment needs to be performed.
Similarly, Fitness-For-Service is used for numerous in-service components like Pressure vessels, Tanks, Piping Systems, Piping components, turbines, boilers, reactors, heaters, etc.
Advantages of Fitness-for-Service Assessment
Even though Fitness-for-Service is prevalent for application in the asset’s operating stage, It can be applied throughout the other life cycle stages such as the design, and fabrication. The main benefits that Fitness for Service provides are:
- FFS is applicable in plant life management, the operating life of the asset can be increased.
- The requirement for unnecessary repairs and replacements can be reduced a lot.
- Fitness for Service improves plant safety.
- The residual life of the equipment is known beforehand which increases the utilization of the asset.
- The maintenance and inspection plan can be optimized by the prior knowledge of FFS assessment to increase plant operating time and reduce downtime.
- Overall, reduction in capital expenditure.
Importance of Fitness for Service in Industry
For proper performance of every asset fitness for service can be a very important assessment method. The FFS is usually performed in two levels. The low-level FFS will primarily highlight if the component is fit for continued service with limited data. This is also known as screening assessment Once the item is found to be critical as per low-level FFS assessment, a high-level detailed FFS assessment can be done with more data to reliably indicate the asset’s condition.
API 579 Fitness for Service Assessment
API 579 by the American Petroleum Institute is a real boon for fitness for service assessment. API RP 579 provides guidelines to demonstrate the structural integrity assessment of the in-service degraded equipment or component. From 2007 onwards, the standard API 579 was renamed as API 579-1/ASME FFS-1 Fitness-For-Service and now comes under the purview of the API and ASME Fitness-For-Service Joint Committee.
API-579 provides clear guidelines if a piece of equipment with minor damage can be operated without replacement, repair, or reducing the pressure rating. A range of damage types such as cracks, localized corrosion, dents, creeps, blisters, weld misalignment, shell distortions, hydrogen damage, fire damage, etc is covered in the API 579 FFS assessment techniques. The fitness for service assessment tools also provides a projected remaining life and in-service margin of the asset which is very much essential for safely running the asset.
API 579 Fitness for Service Assessment Procedure
The API-579 FFS assessment procedures are detailed in the standard based on damage type and mechanism. Even though the fitness for service assessment for each type of flaw varies significantly the general FFS approach is somewhat similar which consists of the following steps:
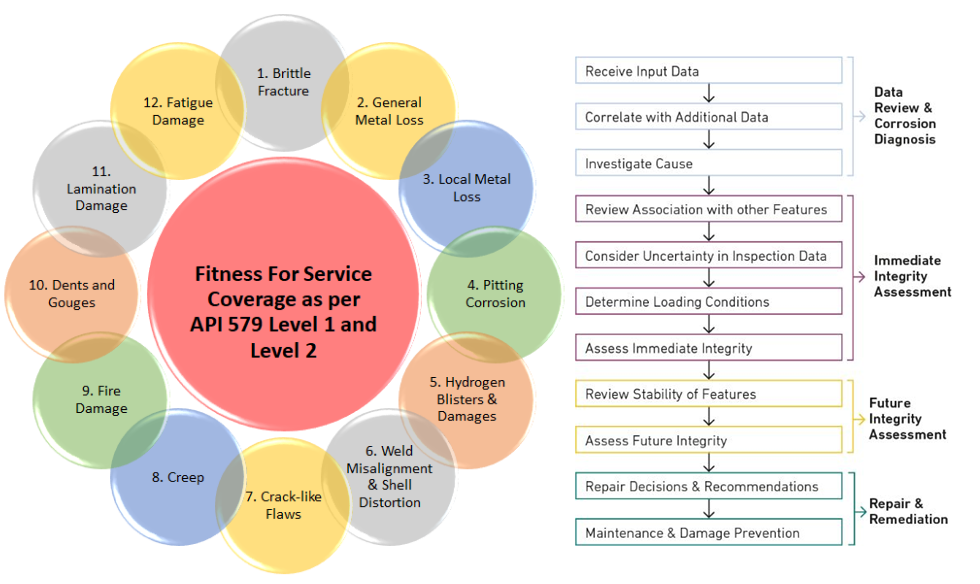
- Flaw and Damage Mechanism Identification
- Selecting the assessment procedure based on the applicability and limitations of the FFS assessment procedures as devised in the API 579 standard.
- Asset Data collection (Design data, maintenance, operational history, expected future service, flaw data, material properties, etc)
- Assessment technique finalization based on damage mechanisms present.
- Estimating remaining life and inspection interval.
- Devising remediation techniques to control future damage or flaw growth.
- In-service monitoring
- Recording all information and decisions in a proper format.
Types of Flaws and Damages in Fitness-For-Service
In Fitness for Service (FFS) assessments, various types of flaws and damage are considered to evaluate the structural integrity of equipment accurately. These flaws and damage mechanisms can arise from a combination of factors including material degradation, operational conditions, and environmental factors. Here are some common types of flaws and damage observed in industrial equipment:
- Brittle fracture
- Hydrogen Blisters, HIC, and SOHIC damage
- General metal loss
- Tank shell and edge settlement
- Mechanical vibration
- Thermal and mechanical fatigue
- Local metal loss
- The heater tube remaining life
- Pitting corrosion
- Hot tap thermal analysis
- Erosion Problems
- Hydrogen blisters and hydrogen damage
- Weld misalignment and shell distortions
- Local PWHT of weld repairs
- Crack-like flaws, including creep, stress corrosion, fatigue, and corrosion-fatigue crack growth
- Bulges and out-of-roundness distortion
- Operation in the creep range
- Fire damage
- Dents, gouges, and dent-gouge combinations
- Laminations
- Blast loading and other dynamic effects
- High-Temperature Hydrogen Attack
- Wind-induced vibration of towers, stacks, and pipelines
When is Fitness-for-Service Used?
Fitness for Service (FFS) assessments are used in various scenarios across different industries to evaluate the structural integrity of equipment and determine its suitability for continued operation. Here are some common situations where Fitness for Service assessments are employed:
1. In-Service Inspection:
- Routine Maintenance: FFS assessments are conducted as part of regular inspection and maintenance programs to monitor the condition of equipment and identify any degradation or damage that may have occurred during operation.
- Scheduled Shutdowns: During planned shutdowns or turnarounds, FFS assessments help prioritize inspection activities and determine the extent of repairs or replacements needed to ensure equipment reliability and compliance with regulatory requirements.
Damage Assessment | Post-Failure Analysis:
- Incident Investigation: Following equipment failures, accidents, or incidents, FFS assessments are performed to assess the extent of damage, identify the root causes, and determine the feasibility of repairing or returning the equipment to service.
- Emergency Response: In emergencies such as leaks, ruptures, or structural failures, quick FFS assessments may be conducted to evaluate the immediate safety risks and determine the appropriate response measures.
Regulatory Compliance:
- Compliance Audits: FFS assessments are conducted to ensure compliance with regulatory requirements, industry standards, and codes of practice governing the integrity and safety of equipment in specific industries, such as oil and gas, petrochemicals, power generation, and aerospace.
- Regulatory Reporting: Operators may be required to submit FFS assessment reports to regulatory authorities to demonstrate the fitness for continued operation of critical equipment and obtain necessary permits or approvals.
Life Extension Study:
- Aging Infrastructure: For aging or deteriorating infrastructure, FFS assessments help assess the remaining useful life of equipment, identify degradation mechanisms, and implement appropriate mitigation measures to extend service life and optimize asset management strategies.
- Upgrades and Modifications: FFS assessments are conducted when implementing upgrades, modifications, or changes in operating conditions to ensure that equipment remains fit for its intended purpose and complies with safety and performance requirements.
Fitness for Service Software
Various user-friendly software packages are already available in the market for performing API 579 Fitness for Service assessment. Some of the well-known API 579 fitness for service software packages are:
- Signal Fitness-For-Service software by the Quest Integrity group.
- Inspect API 579-1 FFS by Codeware
- IntegriWISE, CrackWISE, and RiskWISE fitness for service software by TWI
- BechtFFS by Becht Engineering
- FITest Fitness-For-Service (FFS) assessment software by Lifetech Engineering
- α-phe FFS software by Ankaa Consulting
Codes and Standards for Fitness for Service
Even though API 579-1/ASME FFS-1 is the most widely used Fitness-For-Service standard, some other standards can be referred to. Some of these fitness-for-service codes and standards are:
- BS 7910
- DNV-RP-F101
Additionally, API 579 suggests to refer the following codes:
- API-510
- API-570
- API-653
- NB-23
- ISO 16809
- ASME B31G
Fitness for Service Training
Various renowned organizations provide Fitness for Service Engineering Training to prepare professionals suitable for those jobs. Below are some of the available FFS training courses:
- Failure Prevention, Fitness-for-Service, Repair, and Life Extension of Piping, Vessels, and Tanks (Virtual Classroom) by the ASME
- CSWIP Plant Inspector Levels 2/3 Module 4: Fitness-for-Service (FFS) Assessment, based on API and ASME by TWI (The Welding Institute)
- API 579 Fitness for Service (FFS) Training Course by Wilkinson Coutts
- Fitness-for-Service of Degraded & Damaged Tanks, Vessels, and Piping Systems following API 579-1/ASME FFS-1 and Repair Options by ASME PCC-2 course by Becht Engineering
- Fitness-for-Service Course – Presented by Equity Engineering Group, Inc.
- Fundamentals of Fitness for Service C137 -API 579 Certification Course by ABS group Training Solutions
This fitness for the service training course will help the candidates to
- Analyze, evaluate, and monitor pressure vessels, piping, and tanks for continued operation
- Explain applying the background information on fitness-for-service assessment.
- Identify the main parts of the API/ASME standards along with annexures
- Explain the practical application of the techniques incorporated in API 579-1/ASME FFS-1
Some basic quick questions about FFS from an Intrument Engineer.
1. Is a FFS assessment only carried out after a defect or damage has been found by other means e.g. planned inpection or wall thickness check or damage seen by a casual observer?
2. Is a FFS Assessmnt something that would done on a planned regular basis, e.g. once a year, or is it too involved and detailed to be an ‘across the board’ assessment, reserved for equipment with known damage?
3. During a Due Diligence exercise (prior to asset acquition) would it be prudent to ask to see any live or previous FFS Assessments for the asset?
4. Could FFS Assessment actually be carried out during a Due Diligence to allow informed decision on proceeding with the acquisition or does it take too long?