Cast iron is a very popular pipe material with a carbon content of more than 1.5%. From prehistoric times, cast iron pipes are in use mainly for water, gas, and sewage transport. Cast iron pipe predominantly refers to grey iron pipe. However, in modern engineering applications, ductile iron pipes are prevalently used. For plumbing applications, cast iron pipes are providing reliability for centuries. Still, these pipes are used due to their pivotal role in ensuring the durability, longevity, and efficiency of the system. In this article, we will learn the characteristics, strengths, challenges, and modern applications of cast iron pipes in plumbing systems.
Types of Cast Iron Pipes
Cast iron pipes are a type of metallic piping material that has been in use since the 17th century, making them one of the oldest materials used for plumbing. These pipes are created by melting iron and pouring the molten metal into molds, resulting in a solid and highly durable pipe. There are five types of cast irons. They are
- Grey iron
- White cast Iron
- Ductile Iron
- Wrought Iron, and
- Mondi Iron
However, when it comes to cast iron pipes, majorly they are categorized into two main types: grey cast iron pipes and ductile cast iron pipes.
Grey Cast Iron Pipes:
Grey cast iron pipes are known for their excellent resistance to corrosion and their high compressive strength. The grey appearance of the grey cast iron pipes is mainly due to the presence of graphite flakes in their microstructure. They are often used in sewage systems and underground applications due to their ability to withstand external pressure and soil load.
Ductile Cast Iron Pipes:
Ductile cast iron pipes, also known as nodular cast iron pipes or simply “ductile iron” pipes, are a more modern variation of cast iron pipes. They are treated with magnesium to enhance their flexibility and ductility, making them suitable for a wider range of applications, including water distribution and sewer lines. The graphite in the microstructure is present in a spherical form which makes ductile iron pipes stronger and tougher than grey iron pipes.
ASTM A74 Classification of Cast Iron Pipes
Again, ASTM A74 classifies CI pipes based on the requirement of hubs for pipe joining into two groups.
- Hubless Cast Iron Pipes without any hub, and
- Hub and Spigot Pipes.
Hubless cast iron pipes and fittings are manufactured in only one class and wall thicknesses vary depending on size ranging from 1 1/2″ to 15″. To join hubless pipe and fittings, Metallic shielded couplings are used.
On the other hand, Hub and Spigot CI pipes (Fig. 1) can be with a single hub or double hub. There are two thickness classes for Hub and Spigot pipe and fittings known as Service (SV) and Extra Heavy (XH). As the name suggests, additional wall thickness is added to the outside diameter of Extra Heavy (XH). Hence, Service (SV) and Extra Heavy (XH) classes are not readily interchangeable.
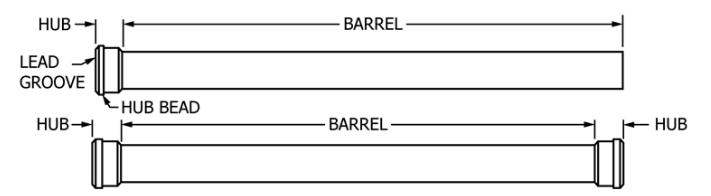
Codes and Standards for Cast Iron Pipes
Cast iron pipes are subject to various codes and standards that provide guidelines for their design, manufacturing, installation, and use in different applications. These codes and standards ensure that cast iron pipes meet specific requirements for safety, performance, and durability. The applicable codes and standards can vary based on the type of cast iron (grey cast iron or ductile cast iron) and the intended use of the pipes. Below are some of the widely recognized codes and standards for cast iron pipes:
ASTM Standards:
- ASTM A48: Grey Iron Castings
- ASTm A126: Gray Iron Castings for Valves, Flanges, and Pipe Fittings
- ASTM A888: Standard Specification for Hubless Cast Iron Soil Pipe and Fittings for Sanitary and Storm Drain, Waste, and Vent Piping Applications.
- ASTM A74: Standard Specification for Cast Iron Soil Pipe and Fittings.
- ASTM A278: Gray Iron Castings for Pressure-Containing Parts for
- Temperatures Up to 650°F (350°C)
- ASTM A395: Ferritic Ductile Iron Pressure-Retaining Castings for Use at Elevated Temperatures
- ASTM A536: Ductile Iron Castings
- ASTM A571: Austenitic Ductile Iron Castings for Pressure-Containing Parts Suitable for Low-Temperature Service
ISO Standards:
- ISO 6594: Ductile iron pipes, fittings, accessories, and their joints for water or gas applications.
- ISO 2531: Ductile iron pipes, fittings, accessories, and their joints for water applications.
EN Standards:
- EN 877: Cast iron pipes and fittings, their joints, and accessories for the evacuation of water from buildings.
- EN 545: Ductile iron pipes, fittings, accessories, and their joints for water pipelines.
- EN 598: Ductile iron pipes, fittings, accessories, and their joints for sewerage applications.
ASME Standards:
- ASME B16.39: Malleable Iron Threaded Pipe Unions, Classes 150, 250, and 300.
- ASME B16.4: Gray Iron Threaded Fittings.
CSA Standards:
- CSA B70: Cast Iron Soil Pipe and Fittings for Sanitary and Storm Drain, Waste, and Vent Piping Applications.
- CSA B602: Ductile Iron Pipe, Centrifugally Cast in Metal Moulds or Sand-Lined Moulds for Water or Other Liquids.
AWWA Standards:
- AWWA C150: Thickness Design of Ductile-Iron Pipe
- AWWA C151: Ductile-Iron Pipe, Centrifugally Cast
- AWWA C153: Ductile-Iron Compact Fittings for Water Service
- AWWA C104: Cement Mortar Lining for Ductile Iron pipe and Fittings for water
- AWWA C110: Ductile and Grey Iron Fittings for Water
- AWWA C111: Rubber Gasket Joints for Ductile Iron Pipe and Fittings
Joining Cast Iron Pipes
Cast iron pipes are joined using various jointing methods. Some of the most common cast iron pipe joining methods are:
- Hub-and-Spigot Joint
- Mechanical Joint
- Flanged Joint
- Push On Joints
Hub-and-Spigot Joint: The hub-and-spigot joint (Fig. 2) is a traditional method used for connecting cast iron pipes. The hub (bell) end of one pipe fits over the plain (spigot) end of another pipe, creating a tight seal.
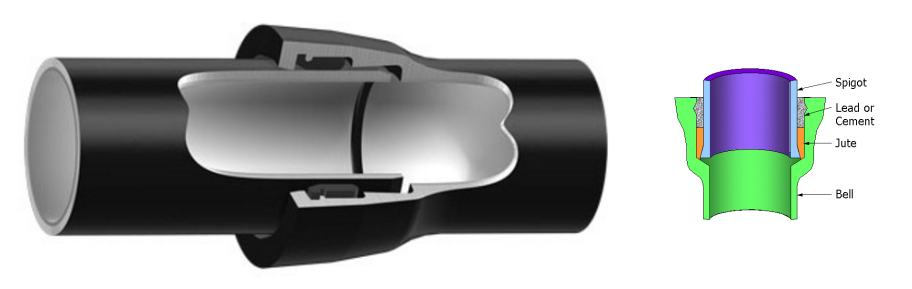
Mechanical Joint: Mechanical joints use a combination of bolts, gaskets, and glands to create a tight and secure connection between pipes.
Flanged Joint: Flanged joints involve attaching flanges to the pipe ends and bolting them together, creating a sturdy and easily assembled connection.
Push on Joint: The connection involved a bell containing a sunken channel that accommodated a rubberized gasket. By gently inserting a lubricated, tapered spigot section into this connection, care was taken to avoid displacing the rubberized gasket. Once in place, the joint formed a waterproof seal. This method of joining is commonly used today with ductile iron and polyvinyl chloride (PVC) pipes.
Cast Iron Pipe Fittings
Cast iron pipe fittings are essential components in plumbing systems that are designed to connect, divert, control, and regulate the flow of fluids within cast iron pipe networks. These fittings are crucial for creating a complete and functional plumbing system. Cast iron pipe fittings come in various shapes, sizes, and configurations to accommodate different applications. Here are some common types of cast iron pipe fittings:
- Elbow
- 45 Degree Offset Fittings
- Tee
- Cross
- Reducer
- Coupling
- Flange
- Bend
- Wye
- Cleanout
- Plug
- P-Traps
Strengths of Cast Iron Pipes
CI pipes provide various advantages including,
- Durability: Cast iron pipes are renowned for their exceptional durability and longevity. Properly installed and maintained cast iron pipes can last for over a century, making them an excellent investment for infrastructure projects.
- Corrosion Resistance: Grey cast iron pipes form a protective layer on their inner surfaces over time, which helps resist the effects of corrosion caused by sewage and wastewater. Ductile cast iron pipes, on the other hand, are even more resistant to corrosion due to their improved chemical composition.
- Sound Insulation: Cast iron pipes exhibit superior sound insulation properties compared to other materials like PVC. This makes them ideal for applications where noise reduction is important, such as in commercial buildings or multi-story structures.
- Fire Resistance: Cast iron pipes have high fire resistance, which can contribute to containing fires in buildings and preventing their rapid spread.
- Flexibility: Cast Iron pipes are suitable for both above-ground and underground installations.
Challenges of Cast Iron Pipes
There are some drawbacks to Cart iron pipes as well including
- Weight: Cast iron pipes are significantly heavier than some modern alternatives, such as PVC or PEX pipes. This can make installation more labor-intensive and require specialized equipment for handling and installation.
- Cost: Cast iron pipes tend to be more expensive than certain other piping materials. However, the initial investment is often justified by their long lifespan and durability.
- Rusting and Scaling: While cast iron pipes are generally resistant to corrosion, improper maintenance, and harsh conditions can lead to rusting and scaling over time, potentially affecting water quality and flow.
Applications of Cast Iron Pipes
Cast iron pipes have been used for centuries in various applications due to their durability, strength, and resistance to corrosion. While their use has somewhat diminished with the introduction of modern materials, they still find relevance in certain applications. Here are some common applications of cast iron pipes:
1. Sewer and Drainage Systems: Cast iron pipes have historically been widely used in sewer and drainage systems. Their resistance to corrosion makes them suitable for carrying sewage and wastewater, especially in areas with aggressive or corrosive substances.
2. Stormwater Management: Cast iron pipes are also used in stormwater management systems to handle rainwater runoff. Their robust construction makes them capable of withstanding external pressures and the weight of soil and debris.
3. Water Distribution Systems: In some areas, cast iron pipes are used for water distribution networks. Ductile cast iron pipes, with their improved flexibility, can handle the pressures and demands of distributing potable water.
4. Plumbing Systems in Historic Buildings: Cast iron pipes are often chosen for restoration or maintenance projects in historic buildings to maintain the authenticity of the plumbing system while ensuring durability.
5. Industrial Applications: Cast iron pipes are used in various industrial settings where the pipes need to handle high temperatures, corrosive chemicals, or abrasive materials. They are commonly used in manufacturing and processing plants.
6. Sound Insulation: Cast iron pipes’ natural density and composition offer superior sound insulation compared to other materials. They are used in environments where noise reduction is essential, such as commercial and residential buildings.
7. Fire Sprinkler Systems: Cast iron pipes’ fire-resistant properties make them suitable for fire sprinkler systems, helping to contain fires and prevent their rapid spread.
8. Soil and Vent Systems: Cast iron pipes are used in soil and vent systems to carry waste gases from plumbing fixtures to the outdoors. Their durability ensures long-lasting performance.
9. Municipal Infrastructure: In some regions, cast iron pipes are still used for municipal infrastructure projects, such as bridges and culverts, where their strength and durability are advantageous.
10. Agricultural Drainage: In agriculture, cast iron pipes can be used for subsurface drainage systems to remove excess water from fields, helping to improve soil quality and crop yields.
Maintenance of cast iron pipes involves regular inspection for rust, scaling, and cracks. When detected, these issues should be addressed promptly to ensure the pipes’ longevity and maintain water quality.
Conclusion
Cast iron pipes have stood the test of time as a reliable choice for plumbing systems. Their durability, corrosion resistance, and other unique properties continue to make them relevant in specific applications, despite the rise of newer piping materials. When considering plumbing materials, it’s important to weigh the strengths and challenges of cast iron pipes to determine their suitability for a given project. With proper installation and maintenance, cast iron pipes can provide efficient and long-lasting plumbing solutions for various needs.