Reliable fire protection is the requirement for industrial valves in sensitive applications where fire accidents can happen easily. The valves used in the oil and gas, refinery, chemical, and petrochemical industries must guarantee a reliable and safe shut-off in case of fire. Fire-safe design is an important criterion for such industrial valves. The term fire-safe means the ability of the valve to minimize the amount of process lost (leakage) downstream or to the atmosphere after a fire test.
1. What is a Fire-Safe Valve?
Fire-safe valves are specialized valves designed to prevent the escape of fluids and gases in the event of a fire. These valves are engineered to maintain their functionality even under extreme temperatures, ensuring that flammable substances do not leak, thus minimizing the risk of fire spread and explosions.
So, fire-safe valves are various types of valves typically installed in piping systems where the process fluids pose a potential fire hazard. They are designed to ensure a safe and reliable shut-off in the event of a fire.
2. Fire-safe Valve Standards
Industrial valves are not an entity of fire hazards. For valves used in the oil and gas industries, the American Petroleum Institute (API) has developed fire tests. After years of refinement, API 607, ISO 10497, API 6FA, BS 6755, and BS 5146 have been accepted as the standards of fire tests of valves. There are some other standards and procedures like API RP6F, FM 6033, Exxon BP3-14-1, OCMA FSV-1, etc. Using these standards as guidelines, many organizations make their internal procedure for fire-safe valves.
A universally accepted firefighting strategy mentions that if a fire is not beaten in one-half hour, a withdrawal and containment policy is instituted. Structural failures like flange bolt failures, pipe rack collapse, and concrete eruptions will occur. Based on this concept, a fire test duration of one-half hour (30 minutes) has been established.
3. Principle of Fire Testing of Valves
The idea behind the fire tests is that any fire-safe valve under pressurized conditions must operate after being burnt at a specified high temperature for a specified period and leakage after burning should be within specified limits. The usual principle of fire testing of valves or fire-safe valve testing is as follows:
The water-filled pressurized closed valve is fully enveloped uniformly in high-temperature flames of around 750 °C to 1000 °C for a period of 30 minutes. When the valve is completely enveloped in fire, exposing the seat and sealing areas to burn temperature, the heat intensity is monitored with thermocouples and calorimeter cubes. During this period, the external and internal leakage past the valve is measured. This leakage should be within acceptable limits. Also, once the valve is cooled after the fire test, the pressure-containing capability of the same valve seats, shell, and seals is tested.
- The stem and bore are usually kept in the horizontal position. Check valves are tested in their normal operating position.
- The temperature is measured using two thermocouples. One is located 25 mm below the valve under test and the other 25 mm from the upper stem packing box on the horizontal centerline.
- The piping to valve end connections for joint leakage are not part of valve fire testing.
4. Fire-Safe Valve Design
In some situations, a valve may need to open or close while exposed to a severe fire. Manufacturers offer two main options for achieving this:
- Robust Materials: Fire-safe valves are constructed from strong materials and seals that can withstand high temperatures without sustaining damage.
- Fail-Safe Mechanisms:
- Pneumatic Actuators: These typically use springs or compressed air to achieve a fail-safe mode. If there is a power failure or loss of air pressure, the actuator is driven to its fail-safe position by the spring or compressed air.
- Electric Actuators: Many include a battery backup to ensure they can move to the fail-safe position during a power outage. Some electric actuators may also use a mechanical spring mechanism similar to pneumatic designs.
- Manual Operation: Manual valves can be integrated into a larger system with fail-safe features. For instance, an alarm system can alert personnel to operate certain valves manually in the event of a fire.
- Temperature Protection: A protective system can prevent the actuator from overheating, which could lead to seal failure or distortion of components. This system aims to keep the actuator within a safe temperature range during a fire, protecting the valve’s parts from extreme heat damage.
4. 1 Design Variations
The fire-safe design of valves can vary by manufacturer. Here are some common features:
- Fire-Safe Butterfly Valves: These often feature three sealing layers. They use a soft insert for a tight seal under normal conditions, alongside a metal-to-metal seal that closes securely even if the soft seal is compromised. These seals are typically made from specialized materials like graphite or PTFE (polytetrafluoroethylene), which resist heat, fire, and chemical exposure. They generally operate in temperatures ranging from -73 to 232 °C (-100 to 450 °F) and pressures up to 102 bar (1480 psi), meeting the tight sealing standards of MSS SP-61.
- Spring-Driven Actuators: Some fire-safe designs utilize spring-driven actuators that automatically close the valve when a fire is detected.
- Floating-Ball Valves: Commonly used in fire-safe designs, these valves feature PTFE seat rings and multiple sealing layers to prevent external leakage. Seals are located between the stem and gland flange, the gland flange and body, and the body and adapter. One layer typically includes an o-ring, while another consists of a graphite gasket. The graphite gasket serves as a backup to prevent leakage if the o-ring is damaged by heat.
5. Selection of Valves for Flammable Services
In the chemical processing and refining industries, choosing valves that can safely handle flammable fluids is crucial. Manufacturers offer specialized designs known as fire-safe valves for this purpose. Selecting the right valve for ensuring shut-off in the event of fire begins with a clear understanding of what “fire-safe” means, along with the standards set by users and independent testing organizations.
It’s important to note that a valve intended for fail-safe operation may not need to perform under fire conditions for many years, and ideally, never at all. Therefore, the selected valve should provide a tight shut-off under normal operating conditions as well as during and after a fire. Reviewing the construction features of various fire-safe valve types will aid in making an informed selection.
According to the Manufacturers Standardization Society, the terms “fire safe” or “fire tested” are not definitive and should not be used without accompanying specifications that outline the requirements. These specifications may include defined test protocols or limitations on valve failure modes. Examples of such limitations include:
- Leakage Control: The destruction of elastomeric materials in the valve should not lead to significant pressure-boundary leakage.
- Leakage Rates: Any damage to elastomeric materials must not result in leakage exceeding specified rates when the valve is closed.
- Pressure Management: External heating of the valve should not cause uncontrolled pressure buildup in the body cavity of a double-seated valve.
Three critical criteria for evaluating fire safety in valves, which are major concerns for testing authorities, are external leakage, internal leakage, and operability after a fire.
- Minimal External Leakage: The best valve designs reduce external leakage by eliminating large gasketed joints and utilizing effective stem sealing with fire-resistant materials.
- Minimal Internal Leakage: For fire-safe sealing integrity, some valve designs employ metal-to-metal seating before, during, and after exposure to fire, minimizing reliance on complete destruction of primary resilient seals or any supplementary mechanisms to achieve contact.
- Continued Operability: A truly fire-safe valve must remain operable even after fire damage. The optimal design prevents heat distortion of the valve body and operating mechanisms caused by thermal and piping stresses during a fire. While some increase in torque may be expected, actuators should be selected with an adequate safety factor to ensure functionality under worst-case scenarios.
6. Types of Valves Used in Fire Safe Service
A fire-safe valve is designed to withstand high temperatures during a fire while providing an acceptable level of shut-off under specific conditions. Due to the extreme heat, these valves are typically constructed from metal. Consequently, gate and globe valves were among the first types recognized as fire-safe, thanks to their metal-to-metal seating. However, because of this seating design, they can leak under normal operation and may experience increased leakage if distorted by heat.
Currently, there are no standardized tests to evaluate the fire-safe capabilities of gate or globe valves. As a result, soft-seated fire-safe valves have become more popular for several reasons:
- They provide a tight shut-off during normal operation as well as during and after a fire.
- They are cost-effective.
- They are easier to automate compared to gate or globe valves.
- They are designed and manufactured to meet established fire-safe valve standards.
Today, soft-seated rotary valves, including ball valves, high-performance butterfly valves, and some plug valves, are commonly used. These valves achieve bubble-tight shut-off while also ensuring fire safety by employing two types of seating arrangements.
The first and most common is known as a two-stage seat system. This design requires the complete burn or melt of the resilient seat before achieving metal-to-metal sealing. In the case of a fire-safe ball valve, metal sealing occurs when the floating ball moves downstream to contact a machined surface in the valve body that matches the ball’s contour. However, if a fire is quickly extinguished or conditions prevent complete seat burn, the floating ball may not fully contact the downstream metal seat, leading to excessive internal leakage and undermining the testing standards.
A second system, utilized by some high-performance butterfly valve manufacturers, does not rely on total seat burn. In this design, the resilient seat and metal seat make contact with the disc simultaneously. This ensures that even if the resilient seat is only partially burned, there is still a reliable metal-to-metal contact that provides an established leakage rate.
External leakage is another challenge. The most common leakage occurs past the valve stem once the thrust washer melts, necessitating a secondary metal-to-metal seating arrangement. This is typically achieved by expanding the outer diameter at the stem’s base to contact a machined lip in the valve body. In manually operated valves, this design is effective as long as the handle does not obstruct vertical movement of the stem. For automatically actuated valves, the drive coupling must accommodate this motion.
For valves with a two- or three-piece body design, it’s crucial to pay attention to body seal materials to prevent leakage during a fire. High-performance butterfly valves often feature a rigid disc and stem connection, and the packing material is typically graphite-based to withstand temperatures up to 1300°F (700°C). Many high-performance valves use a one-piece body design to eliminate the risk of body seal leakage.
7. How Testing Houses Define Fire
Users of fire-safe valves often work with in-house or independent testing committees to create fire-safe test standards that meet their specific needs. Here are key factors to consider for fire-safe valve test specifications:
- Valve Type: This includes designs with metal-to-metal seating, which can be further divided into:
- Continuous Contact Seats: These have constant metal-to-metal contact when closed.
- Two-Stage Seats: These rely on secondary mechanisms, like overtravel or pressure, to achieve metal-to-metal contact during a fire.
- Stem Position: The position of the valve stem is important for evaluating the severity of a fire test. It can affect how the valve performs under high temperatures, especially with different fluid pressures.
- Bore Position: For testing, the bore is often placed horizontally to ensure that the closure element’s weight does not affect the seal, particularly in floating ball valves.
- Valve Open or Shut: Testing an open valve is generally more severe. Open valves may sag and not close completely after a fire, leading to leakage.
- Test Pressure During Burn: Standards organizations typically set a low-pressure requirement for testing, assuming most valves are not used at maximum pressures. This approach needs to consider good piping practices for safety.
- Test Medium: Water is safe and easy to measure but may make it hard to detect leaks. Hydrocarbons, while riskier, provide clearer indicators of leaks due to their viscosity and flammability.
- Burn Duration: The test duration should depend on the valve type and size. Smaller valves may completely fail while larger ones might only partially fail, making both types of testing necessary.
- Leakage Measurement Timing: Seat leakage is measured during and after the fire in some tests, while others measure leakage only after the fire.
- Allowable Leakage: This is critical for safety, especially regarding toxic leaks. Standards like MSS-SP 61 and API 598 set specific leakage rates for new valves.
- Operability: Tests may require the valve to open and close multiple times when hot. This ensures the valve functions correctly even after exposure to fire.
- Overall Assessment: Despite differences in testing methods, existing tests generally indicate whether a valve is fire-safe. Users may need to combine or modify tests to fit their specific requirements. A key point is that during a fire, a fire-safe valve may shift from having a complete seal to a partially or fully destroyed one. A partial burn test is a better predictor of how a valve will perform in a real fire.
8. API 607 vs API 6FA
The most widely used standards for fire testing of industrial valves are API 607 and API 6FA. Both standards are devised by the API. So, what are the differences?
API 607 provides fire test criteria for quarter-turn valves and other valves with nonmetallic seating under pressure, whereas API 6FA provides the fire testing requirements for API 6A and API 6D valves. API 6FA is applicable for metal seated valves.
9. Fire Safe by Design vs Fire Safe Tested
There are some confusing terms often used related to fire-safe valves. They are:
- Fire Safe by Design: A “fire safe by design” valve is designed to make the valve fire-safe. However, the valve hasn’t been tested.
- Fire Safe Tested: A “fire safe tested” valve could have been tested. However, the valve has not been approved by a governing third party.
- Fire Safe Approved and Certified: The term “fire safe approved and certified” for valves signifies that they have been tested, approved, and certified by a governing third party following the guidelines mentioned in common standards like API 607, API 6FA, ISO 10497, etc.
10. Fire-Safe Ball Valves
For applications involving explosive or fire-risk environments, fire-safe ball valves are produced. These valves are specially designed to limit the spread of fire. The fire-safe ball valves are normally fire-tested to API 607, API 6FA, and BS 6755-Part 2. Fig. 1 below shows a typical fire-safe ball valve diagram.
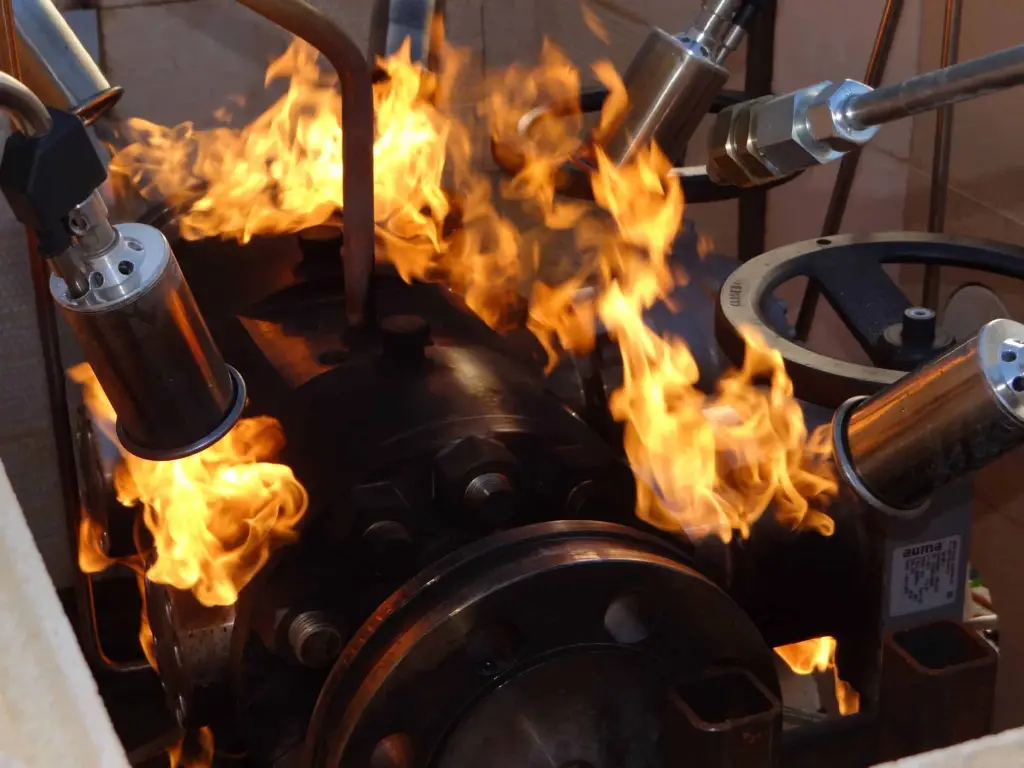
In conclusion, fire-safe valves are critical components in maintaining safety in various industries. Their ability to function under extreme conditions can save lives and protect assets.
FAQ: Fire Safe Valves
1. What are fire-safe valves?
Fire-safe valves are specially designed valves that can withstand high temperatures during a fire while ensuring a reliable shut-off to prevent leaks of hazardous fluids.
2. Why are fire-safe valves important?
They are crucial for protecting against fire hazards in industries that handle flammable materials. These valves help prevent the escape of toxic or flammable substances during a fire, enhancing safety and minimizing environmental impact.
3. What standards govern fire-safe valves?
Fire-safe valves are typically tested according to standards such as API 607 and API 6FA, which outline requirements for fire testing and leakage performance.
4. What materials are used in fire-safe valves?
Fire-safe valves are often made from robust materials such as carbon steel, stainless steel, and specialized sealing materials like graphite and PTFE, which can withstand high temperatures and resist thermal degradation.
5. How do fire-safe valves function during a fire?
In the event of a fire, fire-safe valves are designed to maintain their integrity. They can operate normally or move to a fail-safe position, depending on the actuator type (pneumatic or electric) and valve design.
6. What types of fire-safe valves are available?
Common types include fire-safe butterfly valves, ball valves, and gate valves. Each type has specific features designed to enhance performance under fire conditions.
7. How is leakage tested in fire-safe valves?
Leakage is typically tested during and after exposure to fire. The tests assess both external and internal leakage rates to ensure compliance with established standards.
8. Can fire-safe valves be used in all applications?
While they are suitable for many applications involving flammable materials, it’s essential to choose the right type of fire-safe valve based on the specific requirements of the process, including pressure, temperature, and fluid characteristics.
9. What maintenance is required for fire-safe valves?
Regular inspections and maintenance are necessary to ensure optimal performance. This includes checking seals, actuators, and overall valve integrity, especially after exposure to extreme conditions.
10. How do I choose the right fire-safe valve for my application?
Consider factors such as the type of fluid being handled, operating temperature and pressure, leakage requirements, and compliance with industry standards. Consulting with manufacturers or industry experts can also help in making an informed decision.
Thanks for the post
What type of thread lubricant or tape do you recommend on a NPT threaded API 607 tested valve?
Hi Anup,
Is the leak tightness (Class 1 to 4) also tested along with Fire test?
fire safe API6A Certificate validity- how many years?
It is valid till you dont change the design.
thanks for post
Nice explanation about fire safe valve requirements
If the valve is fire tested to BS 6755 Part 2 – does it meet the requirements for USCG 46CFR56.20-15(b) 2 since the valve is not operated after the test.
Hi Anup Kumar Dey, I found this blog very informative. Would love to keep reading your blog.