To ensure that old flanges continue to work smoothly without any issues with their joint integrity flange facing is required to be performed. Flange facing is a machining service on flange surfaces performed during the maintenance and repair period. Timely maintenance and repair of flanges must be performed to avoid leakages and corrosion, which in turn increases the service life of the flanges.
What is Flange Facing?
Flange facing is the process by which the flanges are resurfaced by machining work to create new mating surfaces that ensure a perfect seal when assembled. Flange facing is done using a tool known as a flange facing tool, flange facing machine, or flange facers.
Flange facing is a very important activity in oil and gas, petrochemicals, refinery, pharmaceutical production, pipelines, food processing, chemical, and power generation industries. Additionally, the following industries use the flange facing operation while maintenance and shot down of their plant:
- Nuclear industry
- High-Purity industry
- Diesel Engined
- Defense
- Tube Processing
- Shipyards
- Fluid control industris
Why is Flange Facing Required?
Flanges are always pressurized during operation and hence continuously experience damage due to turbulent flow. Additionally, they experience impacts with other components while construction and installation, or cuts from gasket leaks.
Flange facing cuts the flanges and provides a spiral grooved finish that helps flanges to be less susceptible to leakages as fluids are forced to travel in a spiral path rather than across the flange face. During plant shutdowns or maintenance activities, Flange facing is one of the most important repair jobs.
Applications of Flange Facing
The flange-facing work is required for the following activities:
- Re-facing of pipe or pipeline flanges.
- Repairing of a heat exchanger and other equipment nozzle flanges.
- Re-surfacing large pump base housings.
- Re-machining the gasket seal on tube sheets.
- For sealing, weld preparation, facing, and beveling of the pipe are required.
- Repairing flat face raised face and phonographic finish flanges.
- Ship thruster mount facing, drilling, and milling.
- Repairing piston rod mating flanges.
- Boiler feed pump flanges.
- Cutting new grooves or repairing ring grooves.
- Vessel and plate weld prep.
- Re-facing ship hatch sealing surfaces.
- Re-machining bearing surface of rotary cranes.
- Re-facing valve flanges and repairing heat exchangers.
- Flange milling wind tower section
Flange Facing Machine
Flange-facing machines or Flange facers are very useful tools to mechanically polish or cut disks, collars, rings, or flanges. Flanges in the piping industry usually get deformed (scratches, dents, etc) or corroded during operation or handling. To ensure the flange joint’s integrity, these damages are removed using a split frame/clamshell cutter known as a flange-facing machine.
A flange-facing machine is also known as a portable lathe machine as they allow to repair of flanges of any diameter without replacing them.
Working of Flange Facing Machine
The cutting tool of the flange-facing machine travels in a spiral path across the flange face and removes the damage from the flange face. This machining or cutting/polishing operation is done by successive strips to ensure face flatness and regularity. Once the flange facing is done, the quality of the flange and the proper sealing capability are achieved.
Finishes as per ASME B16.5 specifications are created and achieved using geared fixed feeds. Flange-facing machines are flexible in operation. They can be mounted at any angle, including the inverted orientation. The facing arm of the flange facer is balanced using adjustable counterweights when not mounted horizontally.
The flange-facing process usually involves the following steps:
- Cleaning of the flange face surface
- Machining with a cutting tool
- Low rotation, low feeding.
- Fine machining with insert bits.
Types of Flange-Facing Machines
Depending on how the flange-facing machines are powered, various types of flange-facing machines are available in the market. The common types of flange facers are:
- Pneumatic flange facing machine
- Hydraulic flange facing machine.
Depending on the mounting mechanism, flange-facing machines are of two types:
- Internal Diameter (ID) mounted flange facer and
- Outside Diameter (OD) mounted flange facing machine.
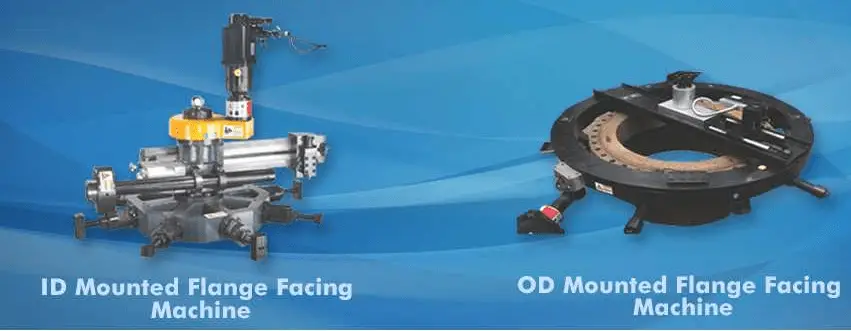
Selection of a Flange-Facing Machine
The following parameters dictate the selection of an appropriate flange-facing machine:
- Flange Size (Smaller machines are used for 2″ to 12″; Larger ones for 45″ to 120″ sizes)
- Pneumatic or Hydraulic type
- ID or OD mounted
- Price
- Toolkit required
Hello Kumar Dei, my name is Christopher Egbodo from Nigeria, I am interested in Piping technology, please advise me on how to commence, I am already a mechanical engineer, how do I reach or speak to you?
Kind regards
CHRISTOPHER EGBODO
+2348186120007