In industry, gasification is usually carried out auto-thermally. In this way, less than the stoichiometric amount of oxygen is reacted with the carbon-rich feedstock, in this case, the waste. The ranges of this operation are usually between 700 and 1300ºC, depending on the technology chosen. There is a wide and varied range of technologies available for gasification. Many of them are shown in the figure below, as mentioned in my previous article.
The main objective of this technology is to convert fossil fuels, such as natural gas or oil, into usable synthesis gas. Subsequently, it produces hydrogen, ammonia, or Fischer-Tropsch liquids.
One of the most promising and booming products is synthetic jet fuel (SPK). Biomass and waste are the first materials to be used today for their production, due to their renewable nature and low environmental impact. However, they present problems of variability in their composition and sometimes low energy density.
Detailed Description
Fluidized bed gasification can be either a circulating or bubbling bed.
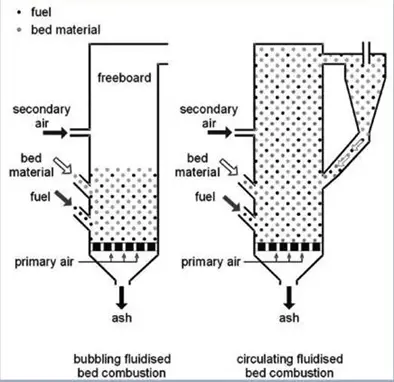
There are several commercially available circulating fluidized bed (CFB) gasification technologies.
Initially for coal gasification, and later for biomass gasification, the U-Gas technology was designed. This gasification technology consists of a single-stage circulating fluidized bed, which was designed to process all ranges of coal and provide medium-low calorific value syngas.
For feedstocks from waste, bubbling fluidized bed technologies have been developed, and it is this technology that is the focus of this article.
The bed is heated by direct injection of oxygen and steam. Thus, the gasifier receives the feed (biomass) and gasifies it using oxygen and superheated steam. In addition, it is heated using a high-temperature flue gas passing through tubes inserted in the gasifier, thus indirectly providing heat to the process. This provides better temperature control. It also improves the control of the syngas composition.
This indirect heating is not implemented by all bubbling fluidized bed gasification technologies, but they simply inject oxygen and steam into the bed.
Feeding
Biomass and waste are potential fuel sources for gasification. However, their heterogeneous nature means that their composition is characterized as containing both combustible and non-combustible materials.
Therefore, for many gasification technologies, waste must be pre-treated to form a fuel to specification.
Pretreatment generally involves the removal of components such as glass, metals, or concrete. To reduce operating costs, the moisture content must be reduced, and the waste homogenized.
The behaviour of the main compounds involved
Pressure
The effects of pressure change are not as important as other parameters.
Methanization and methane reforming are the only reactions that are significantly affected by an increase in pressure. This makes the product gas richer in methane. Tar formation is also favoured by increased pressure. On the other hand, H2 and CO concentrations are reduced.
While the objective of combustion is to produce as much heat as possible by oxidizing all the combustible material, the objective of gasification is to convert most of the combustible solids into gases such as hydrogen, carbon monoxide, and methane.
Temperature
In general, higher temperatures enhance gasification reactions. There are different temperature ranges for different compounds:
CH4 concentration increases when the gasification temperature varies from 660 to 800 °C, while a decrease in its concentration is observed from 800 °C onwards. The initial increase in temperature can be explained by the fact that temperature favours the dealkylation of tars and the cracking of hydrocarbons to methane.
With increasing temperature, methane shifts towards H2 and CO due to the exothermic nature of the methanation reaction.
With a constant oxygen stream, the H2 content increases throughout the logical range. The H2/CO ratio undergoes a strong variation at low temperatures.
CO and CO2 concentrations show opposite trends. In the range from about 600 to 750 °C, the CO2 concentration increases slightly. In this range, CO increases rapidly.
Oxygen
Oxygen, and thus the equivalent ratio (ER), has a clear effect on the temperature and, to a lesser extent, on the syngas yield.
The gas yield increases linearly in the common range of gasification.
In contrast, tar and coal yields decrease with increasing ER. An increase in ER implies a greater amount of available oxygen and thus a greater extent of partial oxidation reactions.
The hydrogen content starts to decrease as the equivalence ratio increases above certain amounts. In this case, the H2 concentration decreases as the amount of O2 increases above a certain limit.
Similarly, the concentration of CH4 decreases under the same conditions.
Evolution of HCN, NH3, and H2S in the synthesis gas (vs. T)
The contaminants considered for a general analysis are NH3, HCN, and H2S.
The main component at low temperatures is NH3. The effect of gasification temperature (from 600°C to 800°C) shows the decrease of NH3 and H2S, while the concentration of HCN increases to a lesser extent.
These compounds have been selected to follow the evolution of nitrogen in the gas phase, as they have been identified as the main gaseous nitrogen compounds in the pyrolysis and gasification processes.
Feed nitrogen is converted to ammonia (NH3), hydrogen cyanide (HCN), and nitrogen oxides (NO, NO2, N2O, and other NOx), as well as to its stable form of N2.
NH3 is the most abundant and depends on the nitrogen content of the feedstock. As the temperature increases without additional oxygen supply, the ammonia concentration decreases and N2 becomes the predominant compound.
In the whole gasification range, HCN appears in a much lower concentration compared to NH3. The HCN concentration remains at an almost stable level, while the amount of NH3 decreases in the same temperature range.
H2S is identified as the main sulphur compound in the syngas, although it also appears to a lesser extent in the form of COS and CS2.
Under gasification conditions, the release of sulphur in the synthesis gas then occurs as H2S, while the other sulphur compounds, including also thiophenes, appear in concentrations about 20 times lower.
H2S undergoes evolution in its concentration in the temperature range. At temperatures of 600-850, the amount of hydrogen sulphide decreases, reaching a minimum at this temperature. Once 850°C is reached, H2S tends to increase its concentration again.
As for the effect of temperature, organic sulphur in biomass is generally released at low temperatures during the volatilization stage. On the other hand, inorganic sulphates show higher stability, remaining in the solid coal unless high temperatures are reached and gasification/combustion reactions of the coal occur to a greater extent.
In addition to sulphur release from the fuel, the effect of temperature on H2S release could also be related to the presence of some elements in the fuel ash (mainly Ca and K).
In the study performed by Berrueco et al., 2015, the evolution of HCl, HCN, NH3, and H2S in the produced gas is studied. The analysis was performed using ion-selective electrodes after retaining the ions in specific solutions.
In the whole range studied, HCN appeared in a higher concentration compared to NH3.
The difference from the above, as indicated in the same study, may be due to the mechanisms of the formation of nitrogenous compounds during pyrolysis.
Although the mechanisms of formation of nitrogenous compounds during gasification are still not well understood, especially in the case of biofuels, several studies give an idea of the reasons for the variation of these different studies. Factors affecting fuel-N conversion are fuel type, nitrogen functionality, initial oxygen concentration, reactor temperature, residence time, heating rate, and particle size or bed material, among others.
The study points out that the main nitrogen-containing pyrolysis product will be HCN when the nitrogen fuel is present in pyrrole and pyridinic forms, while NH3 will appear when the fuel nitrogen is present in amino groups.
This fact would explain the higher level of NH3 detected during biomass and municipal solid waste gasification.
In addition, other authors hypothesize that NH3 formation takes place mainly in thermal cracking reactions of coal, and would be favoured at low temperatures, low heating rates, and large particle sizes. This argument explains the decrease in NH3 formation concerning temperature in the present study.
On the other hand, these studies also describe the evolution of the nitrogen present in the fuel concerning the increase in temperature, showing a significant increase in the conversion to HCN.
Finally, H2S is identified as the main sulphur compound in the synthesis gas. The evolution of the hydrogen sulphide concentration in the syngas experiences a general increase in the range of 700-850 °C, with a minimum of around 750 °C.
Moisture in the inlet stream vs composition
A decrease in carbon monoxide is observed for an increase in the amount of moisture.
On the other hand, H2 and CH4 compositions are known to vary slightly, not greatly affecting the final syngas content.
Steam
The steam flow, which acts as a fluidizing agent, is adjusted.
The composition hardly varies. This is one reason why steam is used as a fluidizing agent. In this way, steam becomes a variable with which to control parameters such as fluidization rate, control the bed temperature by supplementing with oxygen, or adjust the gas velocity. The behaviour of steam in the system is detailed below.
The steam is therefore adjusted to achieve the desired fluidization velocity.
Additionally, the oxygen flow would be adjusted to match the MSW feed rate. The bed temperature is adjusted as needed.
The fluidization state of the reactor bed is defined as the ratio of the gas surface velocity to the minimum fluidization velocity. The fluidization state together with the particle diameter defines the different fluidization regimes.
The influence of a variation in the fluidization state translates into the influence that a variation of the surface velocity in the gasifying agent exerts on the process. The influence can be related to the existing gas-solid contact, the presence and formation of bubbles, the turbulence present, and the residence time of the gas in the gasifier. An increase in the value of the fluidization state causes a decrease in the residence time of the different components in the reaction zone. A consequence of this behaviour is a decrease in carbon conversion.
Once the temperature has been selected, it is necessary to control it. The main variables that influence the temperature value are the calorific value of the fuel and the amount of oxidizing agent and steam used. Steam acts as a temperature moderator and its feed temperature must be above the saturation temperature at the gasifier pressure to avoid condensation. Therefore, the steam is generally injected superheated to about 300-400 ºC and at a pressure slightly higher than the operating pressure. In addition to this steam, an inert gas such as nitrogen or carbon dioxide can also be used.
The carbon content of the inlet stream
As the carbon content increases, the H2 content decreases, as does the steam content.
Conversely, the CH4, CO2, and CO content increases.
It should be noted that if the carbon content increases, the oxygen content may be decreasing. Therefore, to maintain a constant temperature, more heat or oxygen must be supplied to the reactor.
Therefore, there is a decrease in temperature.
A correct integration involves an increase in the oxygen stream injected into the reactor, considering that more carbon has to react.
Conclusion
To achieve more excellent syngas production from waste, further development of the technologies described above is desirable to improve efficiency and reduce costs.
On the one hand, gasifying with direct oxygen and steam injection has several advantages over other gasifying agents, as described above. Through oxygen injection, a higher calorific value is achieved, and the gas produced contains fewer pollutants, in addition to improving the combustion reactions in gasification. Therefore, the cost attributed to reactor preheating is lower. Steam, on the other hand, improves the reforming reactions so that higher concentrations of H2 and CO are achieved.
However, this technology may require a steam generation plant, which may require more energy and therefore raise costs. Oxygen supply is also an aspect to be considered in the economic model.
Therefore, other technologies are also developed in which the heat in the reactor is supplied by high-temperature combustion gases passing through tubes inserted in the gasifier (Shahabuddin et al., 2020).
The residue is fed from the lower sidewall, which reacts with the superheated steam supplied from the bottom of the gasifier. The main advantages of this gasifier are the high quality of the syngas due to indirect heating and the easy control of the H2/CO ratio by adjusting the main parameters.
The most important feature of both technologies is the downstream stage of the reactor. A cyclone separator is installed at the top of the gasifier to separate the particles from the syngas. In this way, the unreacted carbon is separated from the mainstream, together with part of the ash and inerts, and transported to another reactor, where partial oxidation takes place.
The resulting synthesis gas is sent to downstream treatment units to produce various high-value products for industry.