Ammonia is a very important and versatile chemical compound used in a wide variety of industrial and commercial applications. It can be found in products such as fertilizers, cleaners, and refrigerants, among others. In this article, we will learn about the various ammonia production processes and then discuss the Haber-Bosch process of ammonia production in detail.
Applications of Ammonia
Ammonia has a wide variety of industrial and commercial applications. Some examples are:
- Fertilizers: ammonia is an important component of many fertilizers, as it provides nitrogen to plants. Nitrogen is essential for plant growth and ammonia is one of the most common ways of supplying it.
- Refrigeration: Ammonia is a very effective refrigerant and is commonly used in industrial and commercial refrigeration systems.
- Nitric acid production: Nitric acid is a chemical compound used in the production of explosives, plastics, and medicines. It can be produced from ammonia and air.
- Food processing: Ammonia is sometimes used as a preservative in food processing because it kills bacteria and keeps food fresh.
- Cleaning and sanitizing: Ammonia is a powerful cleaning agent commonly used in cleaning products and disinfectants.
- Organic chemistry: Ammonia is used as a reagent in the production of many organic chemicals, such as aniline and ammonium chloride.
Ammonia Production Processes
The main ways of producing ammonia are:
Haber-Bosch process: this process consists of reacting natural gas with air, using high temperatures and pressures. The chemical reaction produces ammonia and water. The Haber-Bosch process is the most widely used method for producing ammonia.
Ammonia production from biomass: Instead of using natural gas as a feedstock, biomass, such as organic waste or biogas, can be used to produce ammonia. This can reduce dependence on fossil fuels and promote sustainability.
Ammonia production from ammonium nitrate: Ammonium nitrate is a natural fertilizer that can be used as a feedstock to produce ammonia. The process involves the oxidation of ammonium nitrate with sulfuric acid and heat.
Ammonia production from nitrogen and hydrogen: Another way to produce ammonia is by the reaction between nitrogen and hydrogen. This reaction is carried out at high temperatures and pressures and uses an iron catalyst.
Haber-Bosch Process of Ammonia Production
The most widespread production of ammonia is carried out by a chemical process known as Haber-Bosch, developed in the early 20th century. This process consists of reacting natural gas with air, using high temperatures and pressures. The chemical reaction produces ammonia and water.
The Haber-Bosch process is a method of ammonia production that is carried out using the following compounds and equipment.
- Natural gas: It is used as a feedstock to produce ammonia. It is a mixture of hydrocarbons extracted from the earth and processed to remove impurities and contaminants.
- Air: it needs to react with natural gas to produce ammonia. Air is composed mainly of nitrogen and oxygen.
- Catalysis: A catalyst is used to accelerate the chemical reaction between natural gas and air. One of the most common catalysts is iron.
- Pressure: the production of ammonia requires high pressures, which are achieved using pumps or compressors.
- Temperature: the chemical reaction between natural gas and air occurs at high temperatures, which are achieved through heaters.
Once all the ingredients are gathered and the equipment is prepared, the ammonia production process begins by mixing natural gas and air. This mixture is heated and subjected to high pressures in a reactor, using the catalyst and heater. The chemical reaction produces ammonia and water.
The ammonia is separated from the water and purified by distillation to remove impurities and contaminants. Once purified, the ammonia is stored and transported to the location where it is needed for final use.
The stages of the Haber-Bosch process are presented in more detail below:
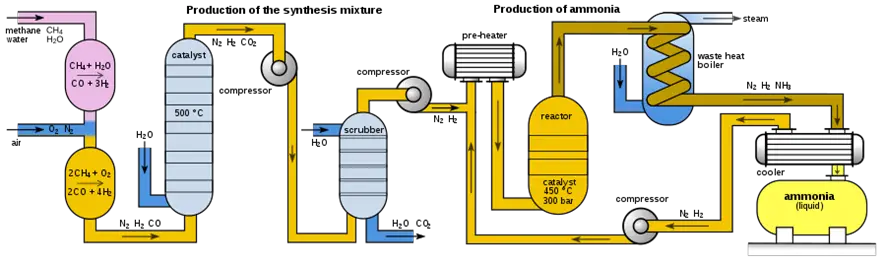
1. Feedstock preparation for the ammonia production process:
The first step is to obtain natural gas, which will be used as feedstock to produce ammonia. Natural gas is extracted from the ground and processed to remove impurities and contaminants.
2. Mixing natural gas and air:
Once the natural gas is obtained, it is mixed with air in an appropriate proportion. The air is necessary to react with natural gas to produce ammonia.
3. Heating and pressurization:
The mixture of natural gas and air is subjected to high temperatures and pressures in a reactor. This is achieved using heaters and pumps or compressors.
4. Chemical reaction during ammonia production:
During the chemical reaction, natural gas reacts with air to produce ammonia and water. The iron catalyst accelerates the chemical reaction.
The reactor is a key component of the Haber-Bosch process for ammonia production. It is a closed vessel in which natural gas is mixed with air and subjected to high temperatures and pressures to promote the chemical reaction that produces ammonia and water.
The size and capacity of the reactor will depend on the amount of ammonia to be produced. Reactor sizes can range from small laboratory reactors to large industrial reactors. Reactors can also have different shapes and designs, depending on the needs and requirements of the process.
In the Haber-Bosch process, the reactor is a key component, and it must be properly designed and constructed to ensure the efficiency and safety of the process. The reactor must be able to withstand the high temperatures and pressures necessary to promote the chemical reaction and must also have safety measures in place to prevent accidents.
5. Ammonia separation and purification:
Once the ammonia is produced, it is separated from the water and purified by distillation to remove impurities and contaminants.
To separate the ammonia from the water, the mixture is heated at a high temperature so that the ammonia evaporates. The evaporated ammonia is collected and condensed, forming droplets of pure ammonia liquid. The water does not evaporate at the same temperature as the ammonia and remains at the bottom of the vessel.
Once the ammonia has been separated from the water, it is necessary to purify it to remove impurities and contaminants. Chemical and physical processes such as fractional distillation, filtration, and precipitation can be used for this purpose.
6. Ammonia storage and transport:
Once the ammonia has been purified, it is stored and transported to where it is needed for final use. Fig. 2 below shows a typical ammonia production plant.
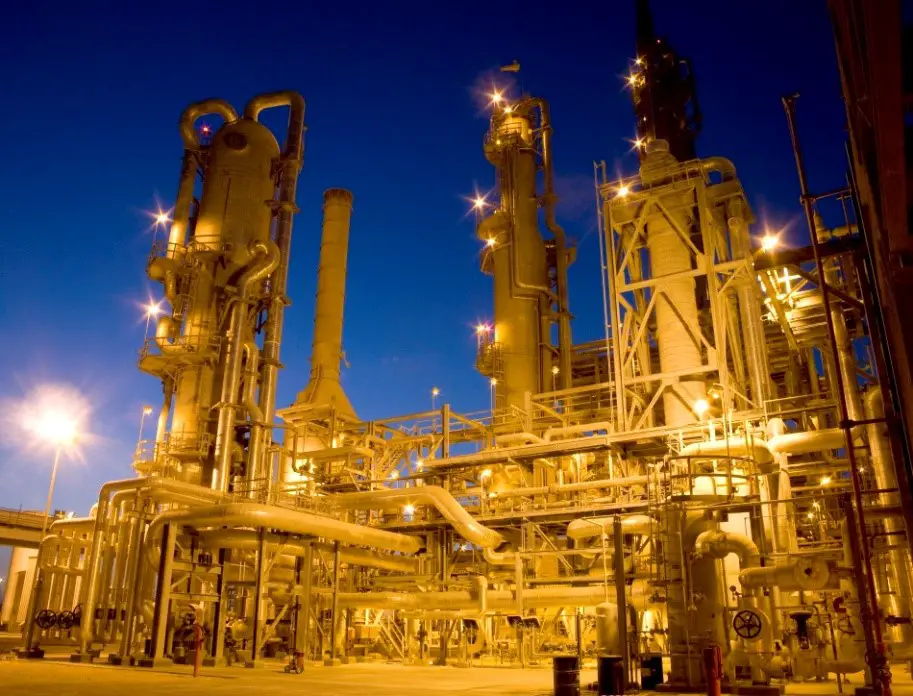
Measures to Reduce Environmental Impact during Ammonia Production
It is important to note that ammonia production can be a very polluting process, as it produces large amounts of nitrogen dioxide, a greenhouse gas.
In addition, the ammonia production process requires a large amount of energy, which can contribute to climate change.
For this reason, it is important for companies that produce ammonia to implement measures to reduce their environmental impact and promote sustainability.
Some measures that can help reduce the environmental impact of ammonia production include:
- Use renewable energy sources to provide the energy needed for the process.
- Capture and recycle greenhouse gases produced during the process.
- Apply carbon capture and storage technologies to reduce greenhouse gas emissions.
- Use clean and more sustainable production techniques, such as ammonia production from biomass.
Conclusions
In summary, ammonia production is a chemical process that is carried out through the reaction between natural gas and air, using high temperatures and pressures. Although it is a very important and versatile compound, ammonia production can have a significant environmental impact. For this reason, companies producing ammonia must take steps to reduce their impact and promote sustainability.
Pablo
Possibly you maybe open to a conversation, we are partnered with a Spanish company whom have zero emission technology that uses hydrocarbons, (all types of plastics) to produce Low Carbon Energy, of which we have several projects in Spain, The technologies can be seen working Spain. The reason for the contact is that we have live projects in Morocco where the prime aspect is to produce Ammonia. My partners are based in Madrid, we are looking to bring a company or individual to the table for the project, Our next meeting with the Moroccan GOV is 14th March, we would like to open up a discussion before then.