The concept of “PLUGGING” heat exchanger tubes refers to the intentional blocking or sealing of individual tubes within a heat exchanger. To seal heat exchanger tubes, heat exchanger tube plugs are a convenient way. The plug usually consists of a cylindrical ductile material that is inserted into the open end of the tube at the tube sheet. It also has one or more resilient seal rings and a longitudinally extending blind central opening in the body.
Heat exchangers are devices designed to transfer heat between two fluids, typically a hot fluid and a cold fluid, without allowing them to mix. The tubes within a heat exchanger provide a pathway for the fluids to flow through, allowing heat transfer to occur.
Reasons for Plugging Heat Exchanger Tubes
Plugging tubes in a heat exchanger is done for various reasons, including:
Tube Maintenance:
Over time, tubes in a heat exchanger may develop leaks, corrosion, or other defects. Plugging these tubes prevents the affected fluid from mixing with the other fluid, ensuring the continued operation of the heat exchanger while the damaged tube is repaired or replaced. Tube plugging is sometimes done in thin wall thickness areas.
Performance Optimization:
In some cases, it may be necessary to adjust the flow distribution within a heat exchanger to optimize its performance. By selectively plugging certain tubes, the flow rate and pressure drop of the fluids can be manipulated to achieve better heat transfer characteristics or address uneven fluid distribution issues.
Process Changes:
When there are changes in the process requirements, such as modifications in fluid properties or flow rates, plugging tubes can help adapt the heat exchanger to new conditions. By altering the flow path, heat transfer can be adjusted to meet the updated process requirements.
System Isolation:
Plugging tubes can be used to isolate a section or segment of the heat exchanger. This may be necessary during maintenance, repairs, or when a particular part of the heat exchanger is no longer needed in the current operation.
Plugging tubes can be accomplished using various techniques, such as mechanical plugs, expansion plugs, or welding. The specific method used depends on the type of heat exchanger, tube material, and the reason for plugging. There are several types of plugs that can be used for plugging a leaking heat exchanger tube. The choice of plug depends on factors such as the type of heat exchanger, tube material, operating conditions, and the severity of the leakage.
Types of Plugs for Heat Exchanger Tube Plugging
Here are some common types of plugs used for tube plugging:
Tapered or Tapered Pin Plugs:
These plugs are conical in shape and are inserted into the tube to create a tight seal. Tapered plugs are typically made of materials such as brass or stainless steel and are often used for low-pressure applications (preferably below 200 psi). When using tapered plugs, tubes need to be pierced before using them to prevent a plug blowout, posing a safety hazard.
Mechanical or Expandable Plugs:
Mechanical plugs are designed to expand radially when inserted into the tube, creating a secure fit. They can be expanded using tools like wrenches or hydraulic pressure. These plugs come in various designs, including single-sized plugs, multi-sized plugs, and inflatable plugs.
Even though, they are commonly used for both low-pressure and high-pressure applications, the mechanical plug is ideal for plugging tubes exposed to an effective pressure of up to 7,000 psi and can withstand up to 2,000°F. For tubes exposed to higher temperatures and higher pressure, mechanical seals are ideal.
Welded Plugs:
In cases where the leakage is severe or the tube cannot be effectively plugged using mechanical methods, welding can be used to permanently seal the tube. Welding involves closing off the tube ends or attaching a welded patch to cover the leaking area. This method is generally used for tubes made of materials suitable for welding, such as carbon steel or stainless steel.
Epoxy or Adhesive Plugs:
Epoxy or adhesive plugs involve using specialized sealants or adhesives to seal the leaking tubes. These plugs are typically temporary solutions and are used when other methods are not immediately available. They are commonly employed for emergency repairs until more permanent measures can be implemented.
Rubber or Elastomeric Plugs:
Rubber or elastomeric plugs are flexible plugs made of materials like rubber or silicone. They are inserted into the tube and expanded using a mechanical or hydraulic device to create a tight seal. These plugs are commonly used for temporary or low-pressure applications.
Threaded Plugs:
Threaded plugs have external threads that match the internal threads of the heat exchanger tube. They are screwed into the tube to provide a secure seal. Threaded plugs are often made of materials like brass or stainless steel and are used for both low-pressure and high-pressure applications.
Friction Fit Plugs:
Friction-fit plugs, also known as drive-fit plugs, rely on a tight fit between the plug and the tube to create a seal. These plugs are inserted into the tube with a hammer or a specialized tool. They are commonly used for temporary or low-pressure applications.
Heat-Shrink Plugs:
Heat-shrink plugs are made of materials that shrink when heated. These plugs are inserted into the tube, and upon heating, they shrink and conform tightly to the inner surface of the tube, creating a seal. Heat-shrink plugs are often used for temporary or emergency repairs.
Composite or Wraparound Plugs:
Composite or wraparound plugs consist of a combination of materials, such as metal and elastomer. These plugs wrap around the exterior of the tube and are secured in place to provide a seal. They are commonly used for temporary repairs or situations where accessing the tube interior is challenging.
Push-in or Snap-in Plugs:
Push-in or snap-in plugs are designed for quick and easy installation. These plugs have a tapered or expanding design that allows them to be easily inserted into the tube without the need for additional tools. They are commonly used for temporary or low-pressure applications.
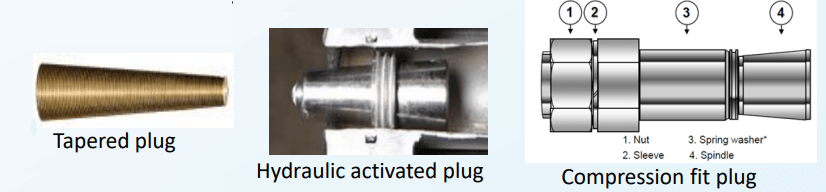
Ring & Pin Plugs:
This is a two-piece styled plug. It consists of a bushing ring that sits inside the tube and a tapered pin plug. The plug is hammered in through the bushing. Additional secondary rings can be added to increase the sealing area of the plug.
It’s worth noting that the availability and suitability of these plug types may vary depending on factors such as the specific heat exchanger design, tube dimensions, and operating conditions. Therefore, it’s advisable to consult with experts or manufacturers who can provide guidance on the most appropriate plug type for your specific heat exchanger and leakage situation.
Steps for Effective Heat Exchanger Tube Plugging
The following steps are used to effectively plug leaking heat exchanger tubes.
Identification of the leaking tube: The first step is to identify tube leaks by inspecting for corrosion signs. A tube leak test gun can be used in this process. Once the leaking tube is found, isolate it from the other tubes in the heat exchanger.
Cleaning of the Tube: In the next step clean the heat exchanger tube where the plug will be installed. Remove any debris or corrosion that might be present.
Venting the tube before plugging: Tube venting is a process by which a small puncture is made inside of the tube, releasing any pressure or chemicals that may be trapped inside. This reduces the risk of deposits filling the leak path and causing a build-up of pressure.
Plugging the Tube: The tube now can be plugged. Depending on the type of heat exchanger plugs, the plugging method may differ slightly. The most common method is to use a mechanical plug which can be inserted into the tube and then expanded to create a seal.
Inspection: When the heat exchanger plug is in place, inspect the tube leaks. A pressure test on the heat exchanger is the most ideal way to do this. If no leak is found, the heat exchanger can be returned to service.
As a general rule, a maximum of 10% of the tubes can be plugged in one pass, if the surface area is designed to 110%. Otherwise, it is a better decision to replace all tubes.
Sometimes, during tube manufacturing some inherent pinhole defects are developed and not traced during hydro testing. At a later stage during usage, these pin holes give way by leaking. The scaling is also a serious problem in heat exchanger tubes due to the poor quality of cooling towers, in dusty environments. This could be somewhat controlled by side stream filters. The MIC in cooling towers is also a great reason for tube leakage.
Very detail explanations to know how industrial uses of Hex Plugs.