What is Chapter IX of ASME B31.3?
Chapter IX of ASME B31.3 is intended for use in high-pressure environments, but its use is not mandated beyond a certain pressure. In the words of the code (see [1]),
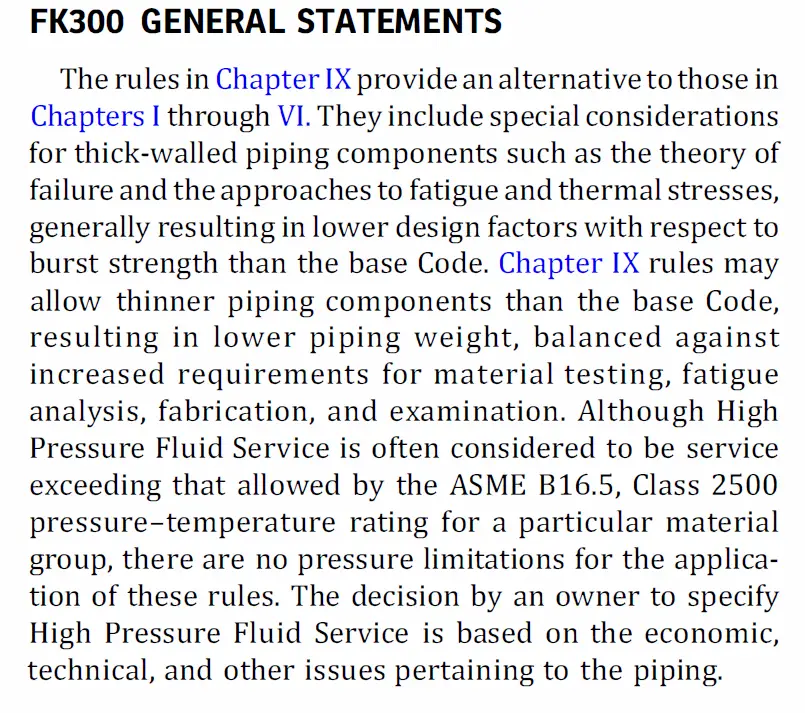
[3] States that the rules of Chapter IX have been used in high-strength steels in pressure as low as 5000 psi.
There is often confusion amongst end users on the applicability of Chapter IX. An example being, can it be used for the analysis of flowlines? As stated in the wording of B31.3 Chapter IX, although the intended use of this chapter is for pressure-temperature combination exceeding that of ASME B16.5 pressure class 2500, but this is more of a rule of thumb than mandated use. A lower pipe wall thickness can be used if this section is utilized for designing piping systems intended for pressure classes less than ASME B16.5 2500#.
Chapter IX provides equations that are different from the base code for computing pipe wall thickness and a more conservative approach to the failure mechanism of Ratchetting (incremental plasticity). Testing/inspection and material requirements are also other aspects where this chapter differs from the base code. In this article, we will cover the technical background of some of Chapter IX’s specific requirements.
When and where to use Chapter IX, ASME B31.3?
A good rule of thumb is to use it for pressure-temperature combinations higher than that permitted by ASME B16.5 Flanges, but this standard can also be utilized for lower pressures to technically justify the use of lower pipe wall thickness than what is computed by base code or where there is concern for significant magnitude of pressure cycling. On this issue, system-specific experience is of paramount importance over any rule of thumb. One important point is to keep in mind that elevated temperature creep effects are not included in Chapter IX; thus, the use of Chapter IX is limited to temperatures below the creep regime for materials of construction [3].
Chapter IX also does not make any provision for Category D and Category M fluid service classifications. Considering the pressure, Category D is not applicable. There are no provisions for category M fluid service. Although the concept of severe cycling is not used in Chapter IX, but the stringency of the rules of this chapter makes additional consideration of severe cyclic service unnecessary [3].
What are the special considerations when dealing with suppliers for Chapter IX piping/pipe fittings?
As all materials are to be impact tested, it is essential to engage with suppliers at a much earlier stage of a project. It is also very important to ensure that the materials to be used shall be below the temperatures at which creep properties would govern the allowable stresses, and hence it’s very important to engage with suppliers to ensure the suitability of the supplied materials. This chapter follows the ASME Boiler and Pressure Vessel Code, Section IX for qualifications of welders or welding operators, however, there are additional requirements and limitations. This may require engagement with fabrication companies in an earlier stage of a project. Branch connection fittings are required to be designed to permit 100% radiography. General fabrication requirements pertaining to end preparation, alignment, welding, preheat, and PWHT are mostly similar to base code, with some variations [3].
The pitfalls of using Chapter IX
Higher engineering analysis costs (requiring engineering staff trained and experienced in using this chapter whose technical requirements are more rigorous than the base code), higher material testing (all materials are to be impact tested), examination, and leak testing are some concerns with the use of Chapter IX [6]. This chapter should only be used when the use of lower pipe wall thickness can be shown to be more cost-saving than the additional costs associated with materials, testing, and engineering.
Technical background to various requirements of Chapter IX
Pressure thickness equation and its technical background
The technical basis behind the wall thickness equation is shown in what follows.
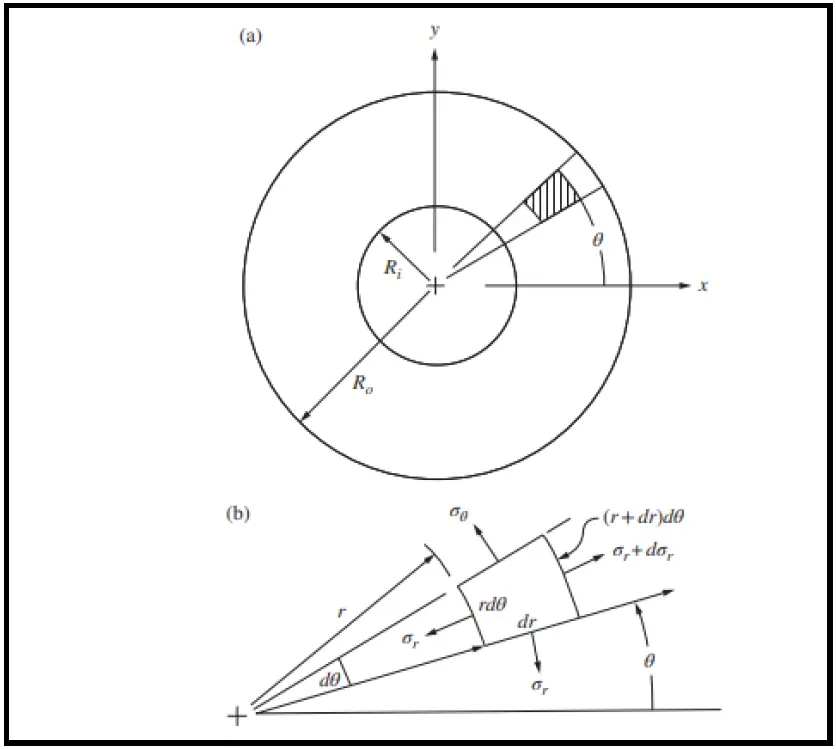
Summation of forces in 𝑟 direction gives
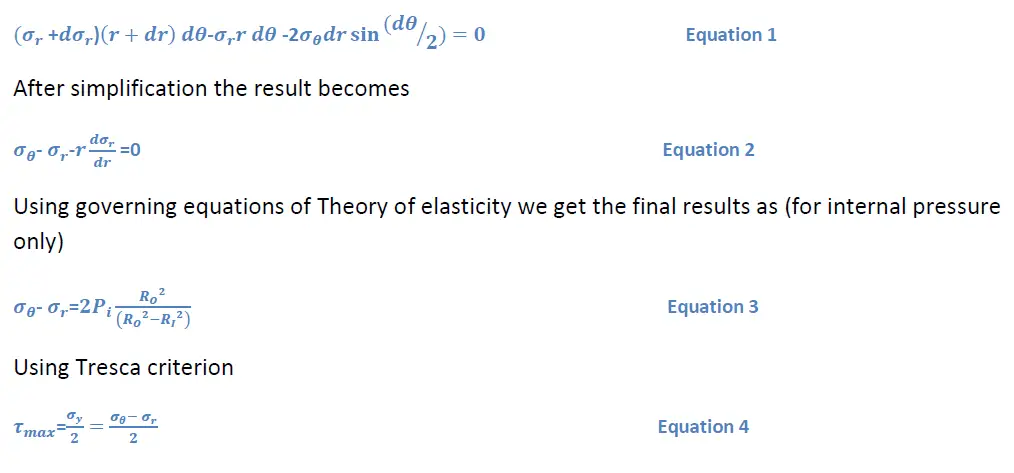
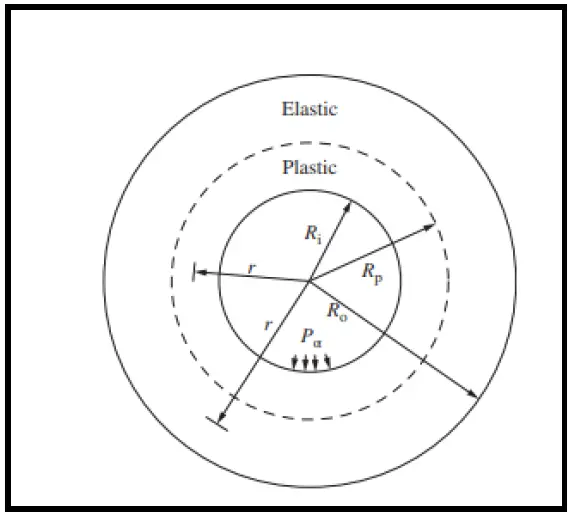
Using Tresca criterion,
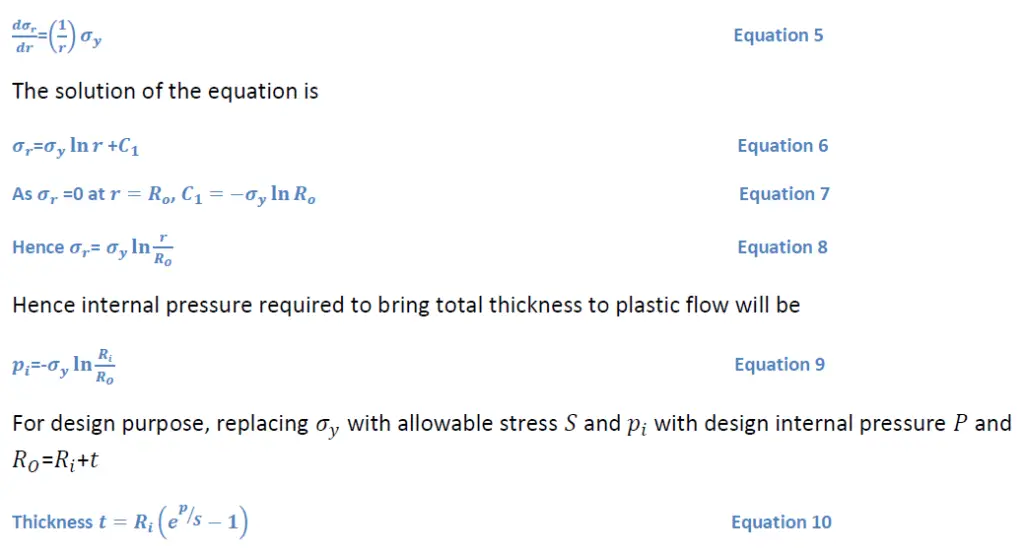
It’s worth noting that ASME Boiler and Pressure vessel code SEC VIII D2 also uses the same form of equation.
Equations used in Chapter IX are
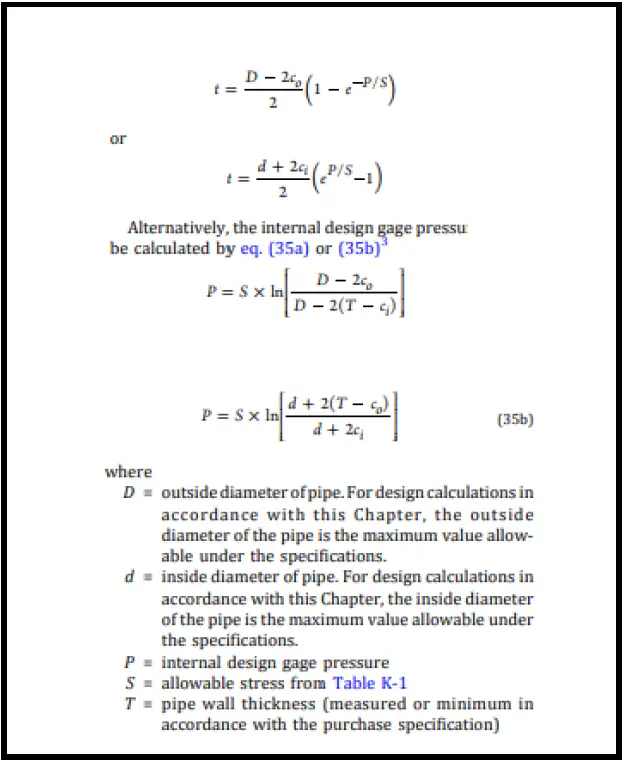
Closed-end cylindrical shell and burst pressure
The technical background requires an understanding of the development of ASME Boiler and Pressure Vessel code Sec VIII D3 as that forms the basis of the current edition of B31.3 Chapter IX. The development of Sec VIII D3 is in turn associated with the development of the Japanese High pressure vessel standard HPIS C106. We start with stating the Nadai equation and the Flow stress equation which are shown below.
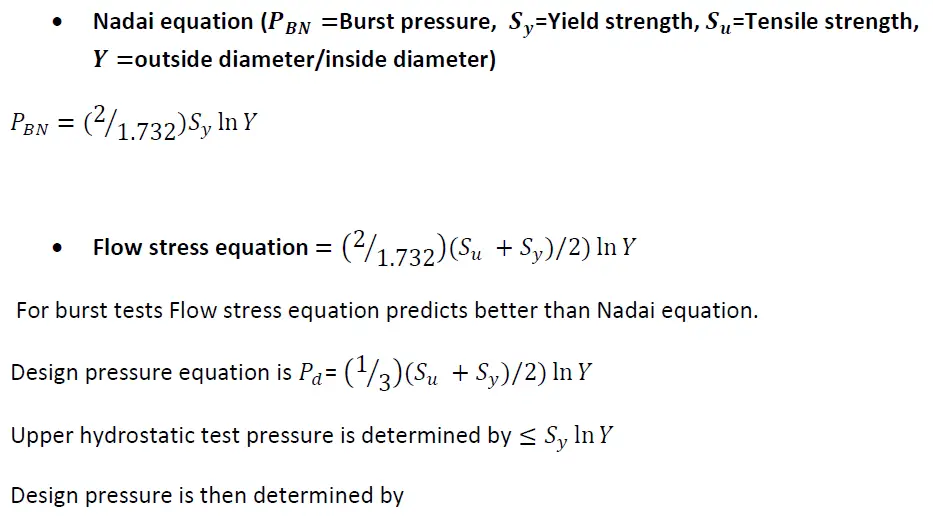
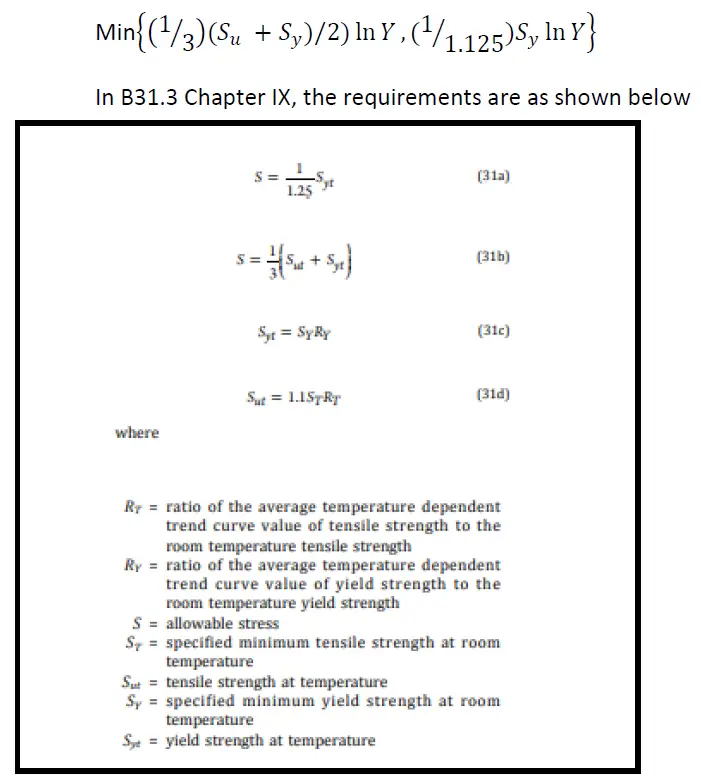
The issue of Fatigue analysis
Like the burst equations, Fatigue analysis of ASME SEC VIII D3 was also influenced by ASME V Boiler and Pressure Vessel code Sec VIII D3 which in turn was influenced by development of Japanese High pressure vessel standard HPIS C106. The main areas are highlighted and briefly discussed below.
Design fatigue curves for 17-PH
New design curves were developed [2] using test data and Manson’s modified universal slope equations. The new design curves for 17-4 PH were incorporated in ASME SEC VIII D3 in 2013 edition.
Surface roughness factors
Surface roughness affects high-cycle fatigue more than low-cycle fatigue. [2] Shows relation between surface roughness and surface factor which is defined as 𝜎𝑤/𝜎𝑤𝑜 where 𝜎𝑤= fatigue limit of arbitrary surface roughness and 𝜎𝑤𝑜=fatigue limit of maximum surface roughness less than 0.5𝜇𝑚.
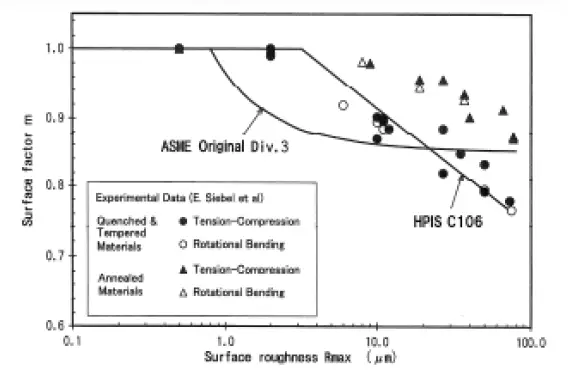
Based on research work [2] on effect of surface roughness on annealed and Q&T (quenched and tempered) steels, it was observed that fatigue strengths for Q&T steels were affected more by surface roughness than Annealed materials. The fatigue limit of Q&T steels is inversely proportional to surface roughness. It is this work on surface factor which formed the basis of [2] and was subsequently incorporated in ASME SEC VIII D3.
Mean stress correction procedure
Mean stress correction should be applied to best-fit curve and then the design curve should be developed. In the original (pre-2013 edition) of ASME SEC VIII D3 mean stress correction was used on the design curves. It was shown in [2] that the original version of ASME SEC VIII D3 showed much lower value of design life than the proposed method in HPIS C106. The reason for this discrepancy was the use of yield stress ( 𝑆𝑦) when mean normal stresses were calculated. To elucidate this point, Modified Goodman diagram from [2] is shown below. When design curve with design margin 2 on stress is used, 𝑆𝑦/2 instead of 𝑆𝑦 should be used for modified mean stress. In addition to this, when the proposed methods of HPIS C106 were compared with pre-2013 ASME SEC VIII D3, it was observed that ASME approach gave un-conservative results for compressive mean stress and conservative for tensile mean stress. While for some technicalities, details of which can be found in [2], ASME approach for compressive mean stress could not be changed in 2013 edition, but the approach for tensile mean stress based on HPIS C106 was introduced for non-autofrettaged vessels to take away excess conservatism.
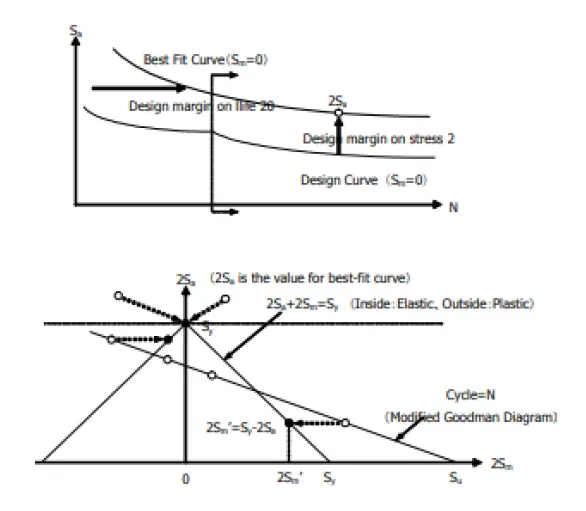
Ratchetting
Unlike the base code, Chapter IX does not check the phenomenon of Ratchetting and fatigue using one equation and the equation for Ratchetting also does not allow for taking credit of liberal stress.
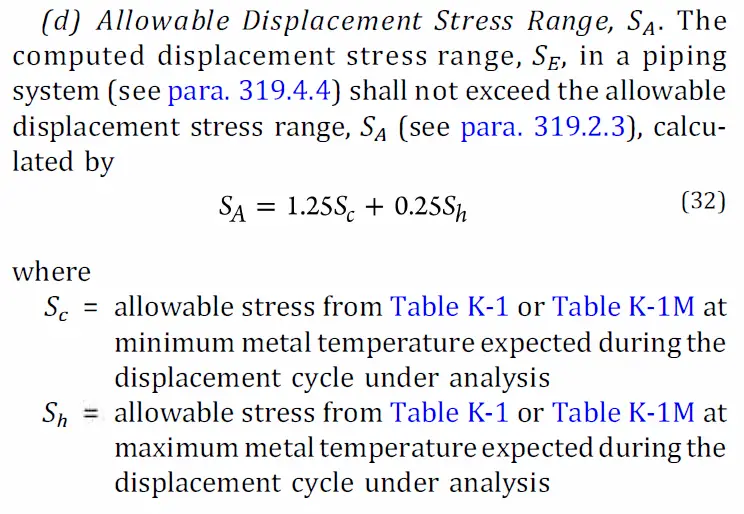
Fracture-mechanics based approach to Fatigue
2022 edition of B31.3 Chapter IX says:
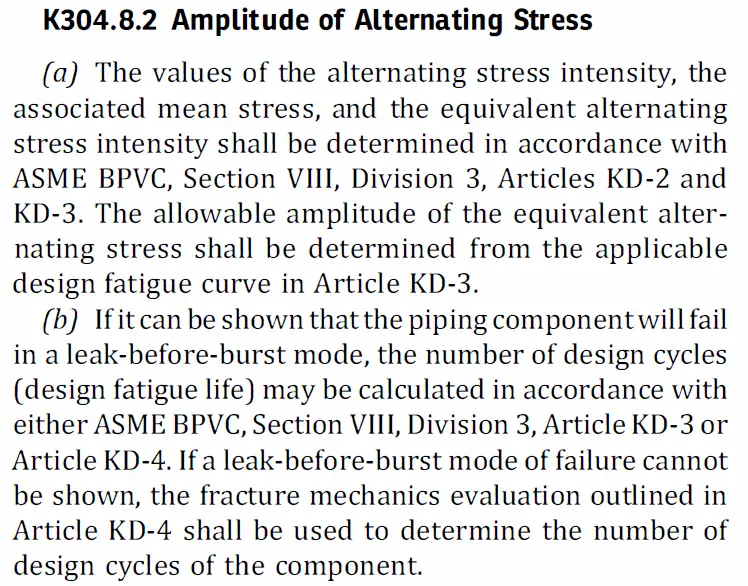
Hence, if leak-before-burst cannot be shown Fracture mechanics approach has to be used. The theoretical background behind “leak–before–burst” can be found in [5].
References
- ASME B31.3 process piping code – 2022 edition.
- Development of Japanese High pressure vessel standard HPIS C106 with ASME SEC VIII Division 3 – Susumu Terada, PVP 2017- 66082, ASME PVP conference July 2017, Hawaii, USA.
- Process piping, the complete guide to ASME B31.3- Third edition by Charles Becht IV, ASME Press.
- Stresses in ASME Pressure vessels, Boilers and Nuclear components – Maan H Jawad, ASME Press
- ASME B31.3 2020 changes with commentaries | Emveedo Energy