Considerations for Hydrostatic Field Test of GRE lines
The hydrostatic field test or hydraulic test on the GRP/GRE line, or on the section of it, is required to verify the hydraulic sealing of the system at the testing pressure and then, indirectly, its structural integrity. The liquid used for hydraulic testing is generally water (γ = 1); in particular cases, the liquid could be seawater (γ = 1.025).
Before proceeding with the filling of the line, check that the same can be pressurized, i.e. complete vents, drains, valves, and/or blind flanges, and every fitting or accessory required by design documents. If the line is above ground, check that the bearings have been executed correctly and that the thrusts due to the hydraulic internal pressure are all correctly sustained.
If the line is underground, check that this is completely ballasted and that the thrusts due to the hydraulic internal pressure are all sustained by the soil or by thrust anchoring blocks.
The joints will be visible, in order to allow the inspection unless otherwise stated by the Client or its representative.
It is preferable to test lines, or segments of the line, whose length doesn’t exceed 1000-1500 m.
Hydrostatic Field Testing Pressure
The hydrostatic testing pressure is generally 1.5 times the design pressure in the lowest point of the section of the line being tested.
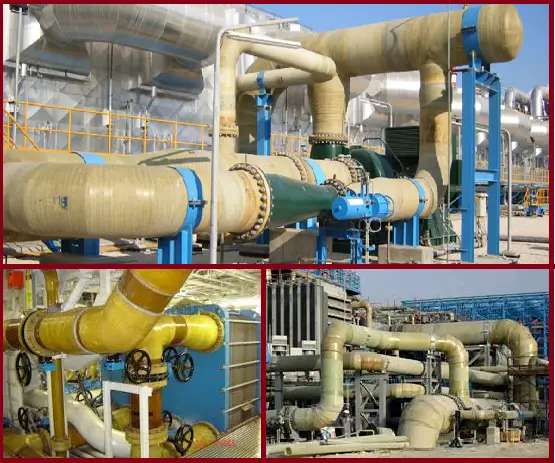
Instrumentation for the Test
All the equipment and the instruments that are required to perform the testing will have to be available and connected to the GRP piping system.
Connect the metering and recording instruments to the line, possibly in the lower point (X point) of it. Otherwise, for the evaluation of the pressure, consider the geodetic gradient of the gauge compared to the X point and the specific weight of the fluid used for the testing (sweet water or seawater) in order to adjust the reading of the same. The value of the pressure of testing will be:
Pp = Pm ± ΔH
where:
- Pp Testing pressure
- Pm manometric pressure
- ΔH geodetic gradient
- γ specific weight of the water
- ± higher/deeper gauge compared to X point
NB: the instruments must be set before and after the test.
Liquid Filling on the Line for Test
- The filling of water will be performed after the cleaning of the line.
- Verify that suitable pumps are available for the filling of the line and for its pressurization.
- Verify that all the vents have been opened.
- Fill the line slowly, possibly from the lower part, in order to facilitate the escape of the air through the vents.
- When the line is completely full, be sure that all of the vents and the valves are well closed. Ascertain furthermore that there aren’t any leakages, by doing a visual control along the run of the line. In case a leakage is found, empty the line if necessary and make the repair. Then fill the line again as above.
GRP Line Stabilization
- This phase of the testing procedure is required to allow the complete thermal and mechanical stabilization of the pipeline.
- In this phase insert the measuring and recording tools. The pressure will have increased up to reaching the value of the design pressure.
- The increase of pressure won’t be greater than 1 bar every 10 minutes for ND>500mm, or 1 bar every 5 minutes for ND ≤ 500mm.
Acceptance Criteria
- Once the required pressure is achieved, maintain the pressure until its stabilization, up to a maximum of 12 hours if no visible leakages are found. Possible pressure drops can be balanced by switching on the pumping system
- Pressure drops are due to temperature change, entrapment of air, settlement of the soil or of anchoring blocks, or expansions of non-rigid joints. Periodically check the vent valves if automatic, or open them to let the air escape.
- The stabilization phase can be considered finished when pressure variations do not occur for at least two hours, without water integration.
Non-Acceptance Criteria
The test will have to be considered invalid and will have to be stopped in the following cases:
- ascertained leakage
- clear deformation of the pipe’s supports and settlements in anchor blocks or in the soil, that are not becoming stable, and that can cause damage to the pipeline;
- after 12 hours if it is not possible to maintain a steady pressure, without integration, for at least 2 hours.
- After having repaired the possible damages that occurred to the piping and/or support system, submit again the pipeline for testing.
- If it is not possible to find out the reason for the lack of pressurization, deeper investigations are required, for example, uncovering buried parts, checking the sealing of the valves, and where it is possible, inspecting the inside of the pipeline.
Pressure Testing
- The pressure will be increased until one achieves the value of the pressure of testing. In this phase compile a minute of testing, reporting the values of pressure and temperature at the beginning of the testing.
- The increase of pressure won’t be higher than 1 bar every 10 minutes for ND>500 mm and 1 bar every 5 minutes for ND≤ 500mm.
- The line will be kept at this value of pressure for a time not lower than 2 hours.
- At the end of this period verify the values of the measurements (pressure, temperature, etc.) and transcribe these final values on the minute of testing.
Acceptance Criteria and Conclusion of the Test
The hydraulic testing will be considered positive if, at the end of the 2 hours of testing, one of the following points is achieved:
- During the period of the hydraulic test, the pressure will stay stable.
- No leakages are visible at any point of the pipeline, or in the joints, or in the testing equipment.
- The change of pressure between the beginning and the end of testing is due to the change in temperature of the testing water.
- The change of pressure between the beginning and the end of testing is due to the presence of air in the line.
- When the joints of the line are manufactured with elastomeric gaskets and there is a decrease in pressure, the initial pressure has to be restored by pumping an amount of water not greater than (from the Std. AWWA M 11 – Manual of water supply practice):
Q = 0.0001⋅D ⋅ L ⋅H
where:
- Q amount of water (liters)
- D diameter (mm)
- L length of the line (m)
- H test time = 12 hours
- A combination of the above points.
Failed Test
- In case of failure of the test, find the cause of the leakage, empty the line and start immediately the repair of the line or replace the defective pieces.
- The pipeline can then be tested again according to the procedure.
Online Video Course of FRP/GRP/GRE Pipeline Stress Analysis using Caesar II
If you are interested in learning FRP/GRE/GRP Piping Stress Analysis using Caesar II software, you can have a look at the following online video course
What is the formula for the hydrotesting of Underground GRE pipe.
Also can I know the acceptance criteria for the Graph considering the Pressure and Temperature drop.
What are the different thickness available and what is the max pressure this pipe can withstand ?
is it necessary to test GRE piping for Air Vent Line / Pressure Safety Valve Discharge Line / Tank Overflow Line / Open Ended Gravity Line. Normally these lines does not have any pressure.
Will only visual inspection is sufficient?
Hi,
Is there any international code references (like AWWA, ASTM etc.) mentioning hydrotest shall be conducted for 2 hours?
also, is there any limit (2 times, 3 times, 4 times etc.) for doing pressure test before putting the pipe into operation?
please reply with proper international code references.
thank you
Mohammed
Infrastructure Engineer
Dear Anup Kumar,
very nice to see you. I am working as a Mechanical Superintendent in Saudi Arabia and very much impressed with the content given for the Hydrotest. Its very useful for the people who are in the same line. I would suggest you to start videos too parallelly to give good information to the field people.
Thanks & Regards
Kishore Kumar Kagitha
Mechanical Superintendent