Metal grating is a very useful perforated metal product widely used as floors, trench covers, mezzanines, trailer beds, scaffolding, stair treads, fencing, grills, bridges, fire escapes, and maintenance platforms in various industries. They are produced by perforating metal sheets or joining metallic bars to form a grid. Various manufacturing methods like expansion, perforation, molding, welding, etc are used to produce metal gratings.
The most common metals that are used to make metal gratings are iron, carbon steel, aluminum, and stainless steel. Metal gratings must have sufficient strength to carry the load and should have a non-slip safe surface to serve as a secure work platform.
Types of Metal Gratings
To cater to the different industry application needs, various types of metal gratings are produced. The specific type of metal grating selection depends on some parameters like:
- thickness,
- metal bar dimensions,
- the configuration or pattern of the gaps or openings, which include oval, square, and diamond shapes.
- load to be carried,
- the work environment where used, etc.
In the following section, we will discuss the most common metal grating types.
Metal Grating Types
Expanded Metal Gratings
Expanded metal grating is produced by puncturing slits in a metal sheet. After the slits are cut, the metal sheets are stretched and pulled to expand them. Because of this expanding action, this type of metal grating is known as expanded metal grating. A diamond-shaped pattern with a slip-resistant surface is generated in the grating. The completed sheets are then cut to the required size to fit the application requirement. Common metals that are used to produce this type of metal gratings are carbon steel, stainless steel, and aluminum.
No waste is created while making expanded metal gratings and hence, this is very economical. The sheets have good structural strength. A Standard expanded process along with cold rolling to flatten the surface to a smooth even finish is usually used during manufacturing. Expanded metal grates are widely used in flooring, fences, security applications, steps, etc.
Bar Metal Grating or Bar Grating
This is the most common type of metal grating. Bar metal grating is constructed of parallel bars connected together to perpendicular bars using various methods like welding, riveting, press-locking, close meshing, etc. The joining method for bar grating is decided based on the thickness of the bars, the material being used, and the cost.
Steel and Aluminum are the most common metals to produce bar metal grating. Due to their high strength-to-weight ratio, they are used in industrial flooring, street drains, fire escapes, and bridges.
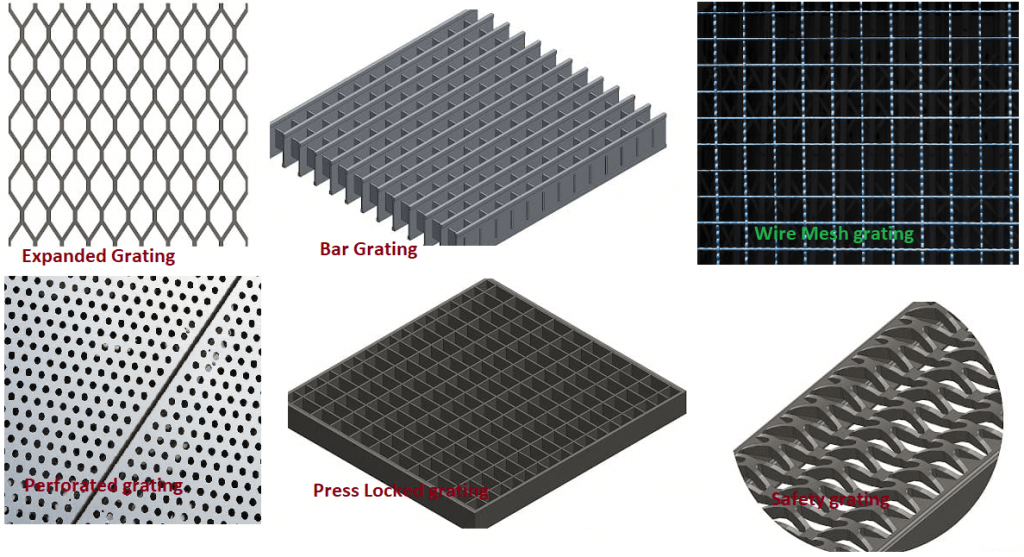
Wire Mesh Metal Grating
Wire mesh metal grating is also popular by names like wire cloth, wire fabric, wire grating, etc. This type of metal grating is produced by using rows and columns of intersecting wires. The popularity of wire mesh grating is due to its easy installation, high durability, flexibility, and versatility.
Depending on the manufacturer, wire mesh metal grating can be welded or woven. Welded wire metal grating is welded at locations where the row and columns intersect. On the other hand, woven wire metal grating is woven like cloth and thus has an array of intersecting wires with columns and rows going over and under at their connecting points.
Wire mesh metal grating is used for Separation and filtration, Security work, Ventilation, Screening and fencing, Material reinforcement, etc.
Perforated Metal Grating
Perforated metal grating is also known as perforated screen, perforated sheet, or perforated plate. They are produced by stamping, punching, or deforming metal sheets to create holes of a specific size, pattern, and shape. Exceptionally sturdy metals like stainless steel, carbon steel, and aluminum are used as metal sheets to make this type of metal grating. Holes are made by different metal fabrication processes like rotary pinning, die punching, laser cutting, etc.
Common applications of perforated metal grating are sound reduction, ventilation, screening, chemical purification, centrifuging, construction material development, etc.
Safety Grating
Also known as Grip Strut Grating, Safety grating provides a firm, solid, and skid-resistant walking surface. These types of metal gratings are designed to increase traction and prevent stumbling, slips, and falling. Small diamond protrusions are usually used in safety grating for greater grip and traction. The open surfaces prevent the accumulation of liquids and help in drainage and airflow. The increased grip of safety metal grating is due to the serration of the edges of the diamond openings created by cold stamping. Steel and Aluminum are the common materials for safety grating.
Compound Metal Grating
Compound metal grating is produced by combining two forms of grating and generally includes bar grating and steel plate grating. Usually, they are composed of a checkered plate sealed to the surface of a steel bar metal grating, with 3 mm to 6 mm steel plates. Compound metal grating is available in a variety of sizes and material types.
Press Locked Metal Grating
In Press locked metal grating, the cross and bearing bars are notched and pressed together and hence the name. They have a smooth even surface across the joined bars. Pressed locked metal gratings have an aesthetically appealing appearance and are generally produced from Steel and Aluminum with a wide variety of sizes and bar openings.
Common Materials Used to Make Gratings
Grating usually refers to any type of covering or frame used to cover holes, provide protection, offer support, or serve as a platform. A wide variety of materials can be used to manufacture grating. Even sturdy plastics can be used to make gratings.
In general, the metallic grating is more popular because of its strength and ability to adjust to many environmental conditions. Specialized metal gratings are used in various industries, airports, and manufacturing facilities and are very strong and durable.
Common materials used for manufacturing metal gratings are:
- Aluminum
- Light Duty Steel Metal
- Stainless Steel
- Galvanized Steel
- Heavy Duty Carbon
Applications of Metal Grating
The most common use of metal grating is to protect workers by providing a secure, stable, and firm work surface with excellent traction. Additionally, they are placed to provide a barrier in unsafe or hazardous situations to prevent accidents. Some of the common uses of metal gratings can be listed as follows:
Metal Gratings for Buildings: In building services, metal gratings can be used as flooring, walkways, platforms, and mezzanines to provide a safe, strong, and durable structure and a protective barrier.
Gratings in Filtration Systems: Due to their corrosion resistance and exceptional strength, metal gratings are popular in water filtration systems. They can easily capture plastic bags, boxes, and other forms of garbage.
Floor Metal Grating: Metal grading is widely used for flooring. In marine and wastewater conditions, Aluminum floor grates are used. For heavy-duty applications, steel metal floor grating is normally used.
Fencing with Metal Grating: Due to the aesthetically appealing appearance, high strength, and rigidity metal gratings find applications as fencing.
Sump Covers: Steel bar grating is used to cover pits or sumps where chemicals or water are collected.
Loading Ramps: Metal gratings also find applications as loading ramps for loading and unloading heavy cargo into elevated platforms or vehicles.
Rail Cars: A bar grating is usually used for running boards, brake steps, walkways, and platforms in locomotives, freight cars, or railcars.
Some other applications include:
- Bridge Sidewalks
- Concrete Reinforcement
- Dipping Trays
- Drainage Covers
- Fire Escapes
- Fork Lift Traffic
- Ladder Treads
- Landing Mats
- Light Guards
- Machine and Motor Bases
- Machine Bases
- Machinery Safety Guards
- Machinery Support
- Material Screens
- Motor Bases
- Ornamental Grills
- Overhead Signs
- Paint Booths
- Partitions
- Racks & Shelving
- Ramps
- Running Boards
- Security Screens
- Snow Fences
- Solar Screens
- Stage Flooring
- Stairs
- Strainers
- Tree & Pole Guards
- Trench Covers
- Trenches
- Truck Beds
- Truck Grills
- Ventilating Screens
- Wash Racks
- Window Guards
Metal Grating Standards
Metal grating standards and codes are guidelines and specifications established by various organizations to ensure the quality, safety, and performance of metal gratings used in different applications. These standards provide manufacturers, engineers, and users with a common set of criteria for designing, testing, and installing metal gratings. Compliance with these standards helps ensure that metal gratings meet industry requirements and are suitable for their intended use. Some of the prominent standards and codes related to metal gratings include:
- ANSI/NAAMM MBG 531: Metal Bar Grating Manual: This manual, published by the National Association of Architectural Metal Manufacturers (NAAMM), provides guidance for the design, fabrication, and installation of metal bar gratings, including specifications for different types of gratings.
- ANSI/NAAMM MBG 532: Heavy Duty Metal Bar Grating Manual: Another publication by NAAMM, this manual focuses specifically on heavy-duty metal bar gratings, providing guidelines for their design and application in high-load environments.
- ASTM A123/A123M: Standard Specification for Zinc (Hot-Dip Galvanized) Coatings on Iron and Steel Products: This ASTM International standard specifies the requirements for hot-dip galvanizing of steel, which is a common surface treatment for metal gratings to enhance corrosion resistance.
- ASTM A1011/A1011M: Standard Specification for Steel, Sheet and Strip, Hot-Rolled, Carbon, Structural, High-Strength Low-Alloy, High-Strength Low-Alloy with Improved Formability, and Ultra-High Strength: This standard covers the requirements for hot-rolled carbon steel used in the fabrication of metal gratings.
- ISO 14122 series: Safety of Machinery – Permanent means of access to machinery – Part 4: Fixed ladders: The ISO 14122 series of standards provide guidelines for the design and construction of fixed ladders, which are often integrated into metal grating structures.
- AS1657: Fixed Platforms, Walkways, Stairways, and Ladders – Design, Construction, and Installation: This Australian Standard outlines the requirements for the design, construction, and installation of fixed platforms, walkways, stairways, and ladders, including those that use metal gratings.
- OSHA (Occupational Safety and Health Administration) regulations: In the United States, OSHA sets safety standards for workplaces, including requirements for the design and use of stairs, platforms, and walkways, which may involve metal gratings.
It’s important to note that metal grating standards and codes may vary based on the country, industry, and application. Manufacturers and designers should refer to the appropriate standards that align with their specific needs and locations. Compliance with these standards ensures that metal gratings meet safety, quality, and performance requirements, providing reliable and safe solutions for their intended use.
How are Metal Gratings Made?
Metal gratings are typically made through a process called metal bar grating fabrication. The exact steps and techniques may vary depending on the type and application of the grating, but here is a general overview of the manufacturing process:
- Material selection: The first step is to choose the appropriate type of metal for the grating, based on factors such as the intended application, load-bearing capacity, corrosion resistance, and environmental conditions. Common metals used for gratings include steel, aluminum, stainless steel, and other alloys.
- Cutting the bars: Metal bars, which are the primary components of the grating, are cut to the desired length using various cutting methods like shearing, sawing, or laser cutting.
- Shaping and hole punching: The metal bars are then shaped and perforated to create the desired pattern. This involves stamping or punching holes through the bars in a regular grid pattern. The hole size and spacing determine the open area and load-bearing capacity of the grating.
- Joining bars and cross rods: For certain types of gratings, cross rods are attached to the main bars to form the final grating panel. Different methods like welding, swaging, or riveting may be used to securely join the bars and cross rods.
- Surface treatment: Depending on the application and environmental conditions, the metal grating might undergo surface treatment to enhance its properties. This can include processes like galvanizing (hot-dip or electro), painting, or applying other coatings to improve corrosion resistance.
- Cutting to size: Once the grating panels are assembled and treated, they may be cut to the required dimensions to fit the specific installation locations.
- Quality control: Before being shipped to customers, the metal gratings undergo rigorous quality control checks to ensure they meet industry standards and specifications.
What are Metal Grating Sheets
Metal grating sheets are large, flat panels made from metal bars that have been welded, press-locked, or riveted together in a grid pattern. They are commonly used for various industrial, commercial, and architectural applications due to their strength, durability, and open design, which allows for efficient drainage and ventilation. Metal grating sheets are available in different materials, such as steel, aluminum, stainless steel, and other alloys, each with specific properties suitable for different environments and applications.
The primary components of metal grating sheets are the bearing bars (metal bars running parallel to each other) and cross rods (bars that intersect and connect the bearing bars). The grid pattern formed by these bars creates an open and stable structure with excellent load-bearing capabilities.
Metal grating sheets are versatile and can be customized to fit specific project requirements. They can be further processed by cutting, bending, or galvanizing to enhance their performance and durability. Depending on the intended use, metal grating sheets may also undergo surface treatments, such as painting or coatings, to improve corrosion resistance and appearance.
Metal Grating Deck
A metal grating deck refers to a platform or flooring surface constructed using metal gratings. It consists of metal grating sheets that are assembled and secured to create a stable and open structure, providing a safe walking or working surface. Metal grating decks are commonly used in various industrial, commercial, and architectural applications due to their strength, durability, and excellent drainage and ventilation properties.
The term “deck” in this context refers to a flat, horizontal surface that is elevated above the ground or floor level. Metal grating decks are often installed on steel or aluminum frameworks, providing a strong and reliable support system. They can be found in various settings, including:
- Industrial platforms: Metal grating decks are used as elevated walkways, mezzanines, and work platforms in industrial facilities. They allow workers to access equipment, machinery, or storage areas safely.
- Outdoor bridges and walkways: Metal grating decks are commonly used in pedestrian bridges and outdoor walkways, especially in areas where corrosion resistance and durability are essential.
- Rooftop walkways: In commercial and industrial buildings, metal grating decks are sometimes used as rooftop walkways to provide safe access for maintenance and inspection.
- Stair treads and landings: Metal grating decks can be used as stair treads and landings, offering an anti-slip surface and enhancing safety in staircases.
- Catwalks and access platforms: In industrial settings, metal grating decks are often used as catwalks or access platforms to reach equipment and machinery at elevated heights.
Metal grating decks are available in different types, such as welded bar grating, press-locked grating, and riveted grating, each with specific load-bearing capacities and open area percentages to suit different applications and requirements. They can also be customized in terms of material, dimensions, and surface treatments to meet specific project needs.
Metal Grating Stairs
Metal grating stairs are staircases that incorporate metal gratings as the stair treads and landings. They are designed with an open and durable structure, providing several benefits such as improved traction, drainage, and ventilation. Metal grating stairs are commonly used in various industrial, commercial, and outdoor settings where safety, strength, and resistance to environmental elements are essential.
The main components of metal grating stairs include:
- Stair Treads: The horizontal surfaces of the stairs that people step on while ascending or descending. These treads are made from metal gratings, which are designed to offer a slip-resistant surface, allowing for safe movement on the stairs.
- Stringers: The vertical supports on either side of the stairs that provide stability and carry the load of the stair treads and the weight of individuals using the stairs.
- Handrails: Metal grating stairs often have handrails on one or both sides, providing additional support and safety for users.
Metal grating stairs can be found in various applications:
- Industrial settings: They are commonly used in industrial facilities, factories, and warehouses where stairs need to withstand heavy foot traffic and where there may be potential for liquids or debris on the stairs. The open design of metal grating stairs allows for easy drainage of liquids and prevents the accumulation of dirt.
- Outdoor environments: Metal grating stairs are frequently used in outdoor areas, such as pedestrian bridges, boardwalks, and access stairs for recreational facilities or waterfront locations. The open structure helps prevent the buildup of water or ice, reducing the risk of slipping.
- Fire escapes: Metal grating stairs are often used in fire escape systems, providing a safe and quick means of exit in case of emergencies.
The type of metal grating used for stairs may vary based on the application, load requirements, and environmental conditions. Common materials include steel, aluminum, and stainless steel, each offering different properties such as strength, corrosion resistance, and weight-bearing capacity. Additionally, metal grating stairs can be customized to meet specific project requirements, including size, shape, and finish.
Metal Grating Walkway
A metal grating walkway refers to a raised, open, and structured pathway constructed using metal gratings. It is designed to provide a safe and stable surface for pedestrians to walk on while allowing for efficient drainage and ventilation. Metal grating walkways are commonly used in various industrial, commercial, and public settings where there is a need for elevated pathways and walkable surfaces.
Key characteristics of metal grating walkways:
- Open structure: Metal gratings used in the walkways have a grid-like pattern, typically consisting of bearing bars (longitudinal bars) and cross rods (transverse bars). This open design ensures that rainwater, snow, and debris can pass through the grating, reducing the risk of slipping and maintaining a clean walking surface.
- Strength and durability: Metal grating walkways are capable of withstanding heavy foot traffic and loads, making them suitable for industrial environments, factory floors, construction sites, and other areas with high pedestrian activity.
- Customization: Metal grating walkways can be customized to suit specific project requirements in terms of size, shape, material, and surface treatment. They are available in various materials, such as steel, aluminum, stainless steel, and other alloys, each offering different properties suited for particular applications.
- Safety features: Metal gratings used in walkways are often designed with serrated surfaces or anti-slip coatings to enhance traction and reduce the risk of accidents, especially in wet or slippery conditions.
Decorative Metal Gratings
Decorative metal gratings are metal grating panels designed with an aesthetic focus, serving both functional and ornamental purposes. They combine the strength and durability of traditional metal gratings with decorative patterns or designs to enhance the visual appeal of spaces. Decorative metal gratings are widely used in architectural and interior design applications, offering a unique blend of style and practicality.
Key features of decorative metal gratings:
- Aesthetics: Decorative metal gratings come in a variety of patterns, shapes, and artistic designs that can complement the overall theme of a building or space. They add an element of visual interest and can be used as decorative accents, facades, or screens.
- Versatility: These gratings can be used in a range of applications, including decorative cladding, fencing, room dividers, sunscreens, and facade elements, allowing architects and designers to incorporate them creatively into their projects.
- Material choices: Decorative metal gratings are available in different materials, such as brass, bronze, stainless steel, and aluminum, offering various colors and finishes to suit specific design requirements.
- Customization: Like standard metal gratings, decorative metal gratings can be custom-made to fit specific dimensions and design preferences, providing flexibility in design.
Overall, decorative metal gratings combine functionality and aesthetics, making them a popular choice for architects, designers, and building owners looking to add visual interest and unique design elements to their spaces.