Pipeline block valves are one of the critical components in a pipeline network that ensures the proper management of liquids and gases that it transports. These valves play a crucial role in regulating the flow, controlling pressure, and facilitating maintenance activities along the pipeline route. In this comprehensive guide, we’ll delve into the world of pipeline block valves, exploring their function, types, importance, maintenance, and safety considerations.
What is a Pipeline Block Valve?
A pipeline block valve is a type of valve installed at strategic points along a pipeline to control the flow of fluid or gas. Unlike other valves that regulate flow continuously, block valves are primarily designed to completely stop the flow when necessary. They serve as barriers, isolating sections of the pipeline to facilitate maintenance, repair, or in emergencies such as leaks or ruptures.
How Do Pipeline Block Valves Work?
Pipeline block valves operate on the principle of obstruction. When activated, these valves shut off the flow of fluid or gas by closing a barrier within the pipeline. This barrier, often a gate, ball, or butterfly valve, blocks the passage of the substance through the pipeline. Block valves are typically actuated either manually, through mechanical means, or automatically, using hydraulic or pneumatic systems. The choice of actuation method depends on factors such as the size of the pipeline, the nature of the transported substance, and operational requirements.
Types of Pipeline Block Valves
Several valves can be used as a pipeline block valve. Some of the notable ones are:
- Gate Valves: Gate valves employ a wedge-shaped gate to control the flow. They are suitable for applications requiring full flow or complete shut-off.
- Ball Valves: Ball valves utilize a spherical closure element to regulate flow. They offer quick operation and tight sealing, making them ideal for high-pressure applications.
- Butterfly Valves: Butterfly valves feature a disc-shaped closure element that rotates to control flow. They are compact, lightweight, and well-suited for large-diameter pipelines.
- Check Valves: While not traditionally considered block valves, check valves prevent reverse flow in pipelines, adding a layer of protection against unintended flow.
What is a Pipeline Block Valve Station?
A pipeline block valve station, also known simply as a block valve station, is a critical component of a pipeline system designed to control the flow of fluids or gases along the pipeline route. It typically consists of a series of block valves strategically placed at intervals along the pipeline to isolate sections of the pipeline when necessary.
The primary function of a pipeline block valve station is to provide a means for shutting off the flow of fluid or gas in case of emergencies, maintenance activities, or operational adjustments. By closing specific block valves within the station, operators can isolate a segment of the pipeline to contain leaks, perform repairs, or redirect flow as needed.
Key features of a pipeline block valve station may include:
- Multiple Block Valves: The station comprises several block valves spaced at regular intervals along the pipeline route. These valves are typically equipped with actuators for manual or automatic operation.
- Access and Control Infrastructure: Infrastructure such as access roads, platforms, and control panels are provided to facilitate operation and maintenance activities at the station.
- Monitoring and Control Systems: Block valve stations may incorporate monitoring and control systems to enable remote operation, real-time monitoring of pipeline conditions, and automated responses to anomalies.
- Safety Features: Safety measures such as pressure relief devices, emergency shutdown systems, and environmental containment measures may be incorporated into the design to mitigate risks associated with pipeline operations.
- Regulatory Compliance: Block valve stations must adhere to relevant industry regulations, standards, and guidelines governing the design, installation, operation, and maintenance of pipeline infrastructure, including block valves.
Importance of Pipeline Block Valves
The significance of pipeline block valves cannot be overstated, particularly in industries such as oil and gas, petrochemicals, and water distribution. Here’s why these valves are indispensable:
- Safety: Pipeline block valves serve as critical safety measures, allowing operators to isolate sections of the pipeline in case of emergencies such as leaks, ruptures, or equipment failures.
- Operational Efficiency: By enabling targeted shutdowns for maintenance or repairs, block valves minimize downtime and disruption to operations, thereby enhancing overall efficiency.
- Environmental Protection: Rapid response to pipeline incidents facilitated by block valves helps mitigate the environmental impact of spills or leaks, safeguarding ecosystems and communities.
- Asset Protection: By controlling pressure surges and regulating flow, block valves help protect pipeline infrastructure from damage, extending its service life and reducing maintenance costs.
- Regulatory Compliance: Compliance with industry regulations and standards often mandates the installation and proper maintenance of pipeline block valves to ensure the safety and integrity of the system.
Installation and Maintenance
Proper installation and regular maintenance are essential for ensuring the optimal performance of pipeline block valves. Key considerations include:
- Location: Block valves should be strategically placed along the pipeline route, considering factors such as accessibility, terrain, and proximity to sensitive areas.
- Inspection: Routine inspections should be conducted to check for signs of wear, corrosion, or leaks. Any anomalies should be promptly addressed to prevent potential failures.
- Testing: Periodic testing of block valves, including functional tests and leak tests, is crucial to verify their proper operation and integrity.
- Lubrication: Moving parts of block valves should be adequately lubricated to minimize friction and ensure smooth operation.
- Training: Operators and maintenance personnel should receive proper training on the operation, maintenance, and emergency procedures related to pipeline block valves.
Safety Considerations
While pipeline block valves enhance safety, certain precautions must be observed to mitigate risks effectively:
- Emergency Response: Clear protocols and procedures should be established for responding to pipeline incidents, including the activation of block valves and coordination with emergency responders.
- Monitoring Systems: Implementing remote monitoring and control systems can provide real-time visibility into pipeline conditions, allowing for proactive intervention in case of abnormalities.
- Pressure Management: Proper pressure management strategies, including pressure relief devices and surge control measures, are essential for preventing overpressure situations that could compromise block valve integrity.
- Environmental Protection: Containment and mitigation measures should be in place to minimize the environmental impact of potential spills or leaks occurring during block valve operations.
Common Problems Associated with Pipeline Block Valves
The most common problems associated with pipeline block valves are
- Leakage: Over time, seals and gaskets can degrade, leading to leakage around the valve.
- Corrosion: Exposure to corrosive substances or environmental factors can cause the deterioration of valve components, compromising their integrity.
- Obstruction: Debris or buildup within the valve can impede proper operation, leading to flow restriction or blockage.
- Mechanical Failure: Wear and tear on moving parts, such as stems or discs, can result in malfunction or failure of the valve to open or close properly.
- Sticking or Binding: Improper lubrication or accumulation of debris can cause valves to stick or bind, affecting their responsiveness.
Design Guidelines for Pipeline Block Valve Stations
- The requirement of a block valve station is decided either by Quantitative risk analysis or by assessing in line with ASME B31.8 section 846.1.1.
- The number of BVS must be limited to a minimum.
- A BVS, including above-ground pipework, shall be designed according to the same code as the pipeline (B31.4 or B31.8). The piping beyond the bypass valves may be however designed to B31.3.
- The location of each BVS is determined by carrying out a study for each pipeline.
- For pipelines designed with a hoop stress design factor higher than 0.6, the block valve stations shall be designed with a design factor of 0.6, to increase safety margins.
- For pipelines designed with a factor of less than 0.6, the block valve stations shall be designed with a factor equal to that of the pipeline.
- The design pressure of the BVS shall be equal to that of the pipeline.
- The maximum and minimum design temperature of the buried pipeline within the BVS shall be the same as for the buried pipeline outside the BVS. For above-ground pipework within the BVS, the design temperatures shall be the same as for the pipeline pig traps.
- For piping in intermittent service acceptable maximum velocities are 8 m/s in the case of oil and 40 m/s in the case of gas.
Components of a Pipeline Block Valve Station
The main components of a pipeline block valve station are:
- Pipework that includes the main pipeline, bypass line, drain line, and flare/vent lines.
- Valves like Mainline isolation valve, bypass valve, throttle valve, relief valve, etc.
- Branch connections.
- Pressure Indicator.
- Pig Signallers.
- Pipe Supports, etc.
Refer to Fig. 1 and 2 below which explain a typical pipeline block valve system layout for liquid and gas pipelines respectively.
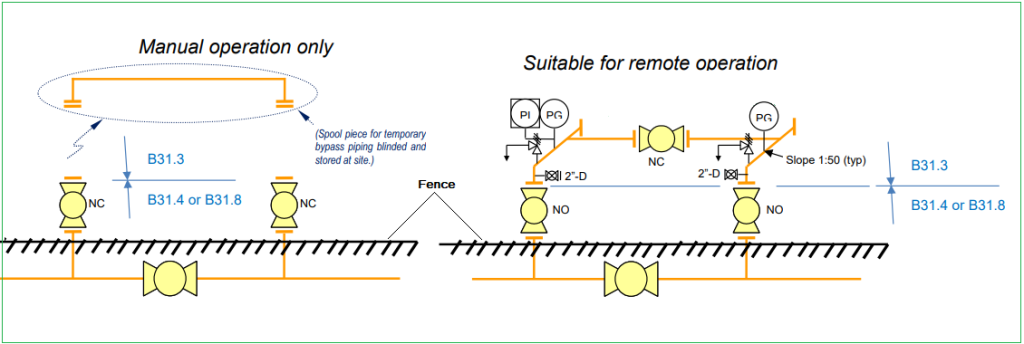
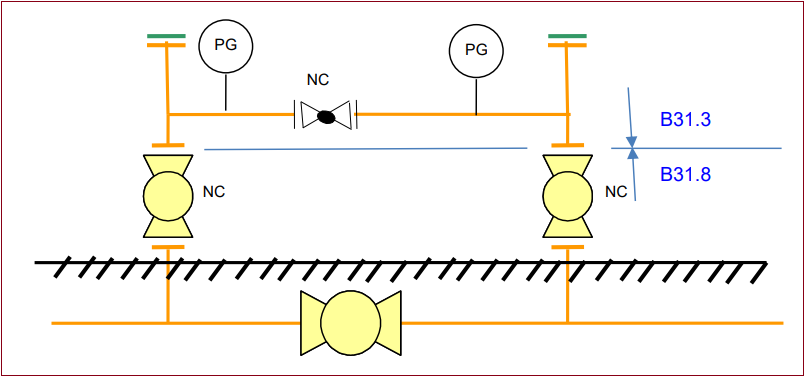
Pipeline block valves are indispensable components of pipeline infrastructure, playing a crucial role in ensuring the safety, efficiency, and integrity of fluid and gas transportation systems. Understanding their function, types, importance, maintenance, and safety considerations is essential for operators, engineers, and stakeholders involved in pipeline operations. By adhering to best practices in installation, maintenance, and safety protocols, we can harness the full potential of pipeline block valves to support sustainable and reliable energy transportation worldwide.
This article provides a thorough exploration of pipeline block valves and their integral role in managing fluid and gas transportation within pipeline networks. It covers various aspects such as function, types, importance, maintenance, and safety considerations, offering valuable insights for professionals in the field.
As someone deeply engaged in piping engineering, I’m intrigued by the evolution of pipeline block valve technology over time. How have advancements in materials and manufacturing processes influenced the design and performance of these valves, particularly in demanding environments such as high-pressure applications or corrosive fluids? Additionally, what research or development efforts are underway to address emerging challenges in pipeline infrastructure, such as the integration of smart technologies for real-time monitoring and control of block valve systems?
B31.3 not used on pipelines, including inside compressor or pump stations.
Look at the scope 1.0 in B31.4 and .8
You do not have process piping here.