Importance of Flare
All of you are aware that the flare is the last line of defense in the safe emergency release system in a refinery, chemical, petrochemical, or pharmaceutical plant. It uses to dispose of purged and wasted products from respective plants, unrecoverable gases emerging with oil from oil wells, vented gases from blast furnaces, unused gases from coke ovens, and gaseous water from chemical industries. So its design and construction have to be accurate and quality must be maintained.
Why use a Checklist for the Flare Package?
Checklists are very important tools for improving the quality and accuracy of any job. It helps engineers and designers to verify all important points while carrying out any work. It helps to reduce failure by compensating for the potential limits of human memory and attention. Any engineering design activity can be verified for accuracy, consistency, and completeness using a checklist. Checklists are an important document for quality audits. They are important in every task.
This checklist will highlight a few important points that should be checked before the commissioning of any flare packages. This list is not exhaustive, Readers are requested to add more points in the comments section.
Pre-Commissioning Checklist
- The tag number and location coincide with the P&ID drawing number.
- Check the Equipment visually for defects if any.
- Confirm whether the vendor representative should be available for the commissioning
- Check the equipment layout, and nameplate rating, and ensure conformity to specification.
- Inspect and ensure the correct assembly of the equipment with the vendor P&ID
- Check the insulation, if required, has been applied in accordance with the specification.
- Check the suitability of flanges, facing, and gaskets for service conditions.
- Check the alignment record of the equipment. All records should have the signature of the Owner’s Construction Representative.
- Remove all temporary construction materials, facilities, and equipment.
- Confirm that equipment grounding has been properly installed.
- Confirm that all instruments have been installed in their proper locations
- Confirm the equipment pre-commissioning/ commissioning procedure is available from the vendor and that operating personnel is thorough with the procedure.
- Check the installation and support of all piping to ensure against vibration and fatigue in operation.
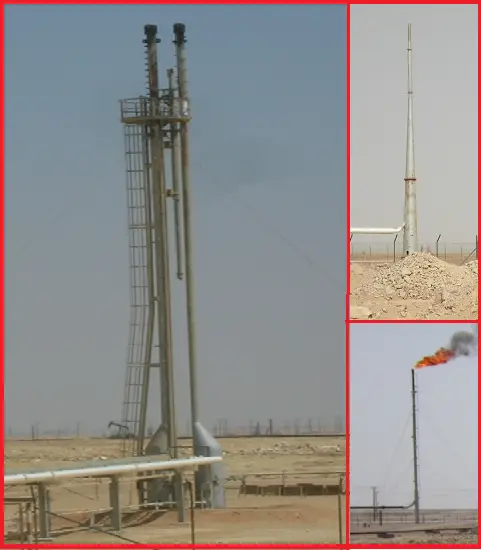
- Provide scaffolding, safety lines, and barriers. Rope off the working area to keep out unauthorized personnel.
- Check the inspection records of equipment.
- Confirm that access ladders are properly fitted and fastened to the support clips provided
- Check platforms have been installed to allow safe access to all valves and instrumentation that is located on the skid and they have been fitted with guard rails
- Confirm that all connecting piping and valves have been installed on the skid, including isolation, control, instrumentation, and relief. Also, confirm that all instruments (local and those with transmitters) are properly installed.
- Clean out all debris and test all drain systems free and clear, ready for start-up.
- Check all operating blinds are installed as detailed in the drawing.
- Remove all temporary construction materials, facilities, and equipment.
- Confirm that the Manufacturer’s Test Certificate is available and that the information on the skid nameplate agrees with the certificate and is legible.
- Confirm that the final external paint coating has been applied
- Wherever applicable vessel, piping, pump, tank, the checklist should be applied.
Commissioning Checklist
- Operational testing of the equipment including leak testing (at maximum operating pressure) Is carried out.
- Operational and functional testing of instrumentation, control, and safety systems, including loop checking logic checking, operational testing of DCS/ESD systems, and package control systems.
- Testing of CP system and all electrical power systems equipment, all motor runs, and test on lighting, power, and earthing systems. Energizing of switchboards and transformers
- PSV inlet and outlet valves open and by-pass valves closed.
- Check all the drain and vent valves.
- The procedure for the start-up as per the Operating manual is clear to the Operator
Few more useful Resources for you…
Routing Of Flare And Relief Valve Piping: An article-Part 1
Flare systems: Major thrust points for stress analysis
Stress Analysis of PSV connected Piping Systems Using Caesar II
Articles related to Process Design
Piping Layout and Design Basics
Piping Stress Analysis Basics
Good work Mr. Kumar…. I am a Chemical Engineer but Currently Undergoing Facility Inspection in a Process. Refining and Petro-Chemical to be precise.
We are getting close for Pre-Commissioning when i came across your work. Good work i must Commend and i will be in touch.