A progressive cavity pump is a positive displacement type pump mainly used for handling high-viscous fluids and tough pumping applications. They are also known as cavity pumps, progressing cavity pumps, PC Pumps, progg cavity pumps, progressive cavity screw pumps, or eccentric screw pumps. As the pump transfers fluids by means of the progress of fixed discrete cavities through the pump when the rotor turns, it is known as a progressive cavity pump. It is a versatile pump having various applications to handle abrasive, high-viscous fluids. In this article, we will learn the working, design, applications, advantages, and disadvantages of a Progressive Cavity Pump.
Working of a Progressive Cavity Pump
Progressive cavity pumps consist of a helical rotor and a twin helix stator. The pumping fluid enters the pump through the inlet suction nozzle. The fluid is then fed into a long casing having the helical rotor and stator assembly. When the rotor turns and contacts the stator surface, a series of small cavities are generated in between. The pumping fluid is progressed through these cavities and is finally expelled through the outlet. The sealed cavities are the main cause of the transfer of the fluid.
Progressive cavity pumps are not allowed to run dry as the heat generated by the rotor and stator may cause pump failure. They are self-priming pumps with higher pressure per stage and high suction lift. The working theory of progressive cavity pumps is invented by René Moineau, a pioneer of aviation, in 1930.
Design of Progressive Cavity Pumps
The rotors of the PC pump are usually made of Steel with a smooth hard surface coating and the stator is usually made of a molded elastomer inside a metal tube body. The complex cavities are formed in the elastomer core of the stator. Angled link arms and bearings allow the rotor to roll around the inner surface of the stator. There are two designs of stators in a cavity pump. They are equal-walled and unequal-walled. The unequal-walled stator design has a greater elastomer wall thickness at the peaks. Because of the increased ability of the stator to distort under pressure, the large-sized solids can pass through the unequal-walled designs.
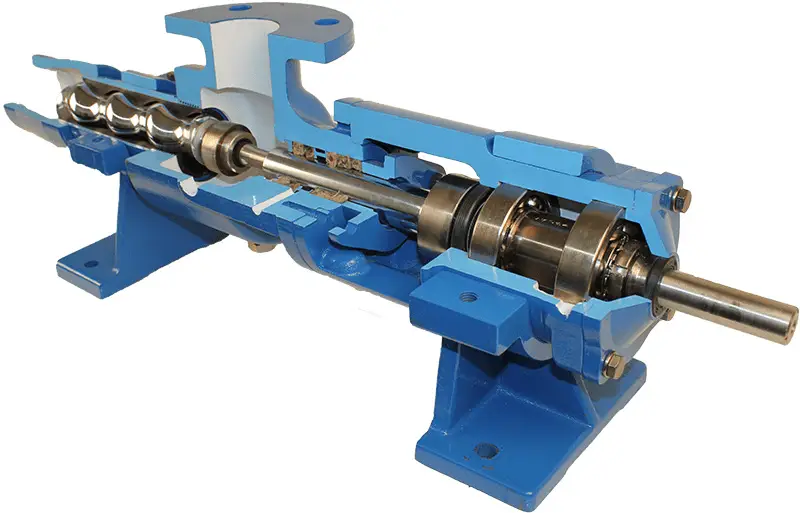
Other pump components like pump body, joints, driver, coupling, connecting rod, bearing, packing, sealing, etc are common for all types of pumps.
Applications of Progressive Cavity Pumps
Progressing cavity pumps are used in a range of industries specifically for handling high-viscous fluids and slurries. Some of the common applications of PC pumps are:
- Sewage and sludge pumping
- Oil pumping
- Grout or cement pumping
- Food and drink pumping
- Coal slurry pumping
- Limited energy well water pumping
- Mining slurry pumping
- Viscous chemical pumping
- Stormflow screening
- Transferring paint, varnish
- Oilfield directional drilling
- Pumping cosmetics, creams, and lotions
- Marine diesel fuel pumping
- Lubrication oil pumping
- Transferring shear-sensitive fruits and vegetables
Specifically, they are used for the purpose of pumping, dosing, and metering chemicals, shear-sensitive materials, and heavy-viscous fluids. The industries that make frequent use of progressive cavity pumps are:
- Wastewater industry
- Oil Lubrication industry
- Chemical manufacturing industry
- Cement industry
- Sewage treatment plants
- Food and Beverage industries
- Pulp and Paper industries
- Oil Drilling Industries
- Petroleum production, etc
Advantages of Progressive Cavity Pumps
Progressive cavity pumps have several advantages like
- They are suitable for solids and other difficult mediums.
- They can easily handle multi-phase fluids, air-entrained fluids, and abrasive fluids.
- They provide good precision in dosing.
- PC pumps can provide continuous, gentle, and low pulsation flow.
- They are self-priming
- They do not create vapor locks.
- They have a high suction capability.
- Accurate to act as a metering pump.
- Reverse rotation and flow are possible.
- Quiet operation.
- PC pumps can be operated vertically.
Disadvantages of Progressive Cavity Pumps
However, there are certain drawbacks of Progressive cavity pumps. The main disadvantages of Progressing cavity pumps are
- PC pumps can not run dry. They need a lubricating fluid film for their operation.
- They usually are slow-moving with less flow amount.
- Their pumping capacity is limited. They can pump up to a limited distance.
- When slippage occurs between the rotor and the stator, the efficiency considerably decreases.
FAQs of Progressive Cavity Pumps
Is the progressive cavity pump the same as the screw pump?
A screw pump also has rotors and is quite similar to PC pumps. But the main difference between a screw pump and progressing cavity pump is the application. While screw pumps are used specifically for nonabrasive fluids, Cavity pumps are used mainly for abrasive fluids, slurries, etc.
Can progressive cavity pumps pump water?
Progressive cavity pumps are normally used for sheer sensitive and highly viscous liquids like slurries. For less viscous liquids like water, PC pumps are usually not used.
Are progressive cavity pumps reversible?
yes, progressive cavity pumps can operate in either direction with equal efficiency.
Can the progressive cavity pump run dry?
No, Progressive Cavity Pumps cannot be run dry. If it is run dry then the heat generated will damage the stator. That is why dry-run protection devices like stator temperature probes are used.
How do you prime a progressive cavity pump?
PC pumps are usually self-priming pumps. The Priming of cavity pumps can be done by filling the pump with the medium to be transferred. Priming of pumps is essential for proper lubrication of the rubber stator.