Reboilers are typical heat exchanger that produces vapor to drive fractional distillation separation. In classical fractional distillation services, all the vapor to drive the separation comes from the reboiler. (Alternatively, externally generated vapor, feed preheat, or inter-reboiler systems may be used). Proper reboiler operation is vital to effective distillation. Reboilers are specific types of heat exchangers that are used to generate a vapor flux to feed to a distillation tower. For any distribution column, reboilers are an essential part and they play an important role in the proper distillation process.
What is a Reboiler?
A reboiler is a heat exchanger used in distillation or other types of chemical processes where a liquid mixture needs to be separated into its individual components. The reboiler is a device that provides heat to the bottom of the distillation column, where the liquid mixture is boiled and the vapor rises up the column to be condensed and collected.
The reboiler is typically located at the base of the distillation column, and it is used to re-vaporize the liquid that has condensed at the bottom of the column. The heat provided by the reboiler causes the liquid to vaporize and rise up the column again, where it can be separated from the other components in the mixture.
The term “reboiler” comes from the fact that it is used to reboil the liquid that has condensed at the bottom of a distillation column. In a distillation process, the liquid mixture is heated to its boiling point, causing it to vaporize and rise up the column. As the vapor rises, it cools and condenses at the top of the column, forming a liquid that collects in a tray or basin at the bottom of the column.
The reboiler is then used to reheat this liquid, causing it to vaporize again and rise up the column for further separation. Essentially, the reboiler reboils the liquid that has already been boiled once in the distillation process, hence its name.
Types of Reboilers
Reboilers are classified depending on the orientation of the reboiler and the type of circulation used.
Depending on the reboiler orientation there are two types of reboilers:
- Vertical Reboiler (Fig. 2) and
- Horizontal Reboiler (Fig. 1 and 3)
Vertical vs Horizontal Reboilers
The main differences between vertical and horizontal reboiler are their orientation, size, and heat transfer characteristics.
Vertical reboilers are designed with a vertical orientation, and the heat transfer surface is typically arranged in the form of tubes or bundles that run vertically through the reboiler. The liquid to be heated is typically circulated through the tubes, while the heat source is located at the bottom of the reboiler.
Horizontal reboilers, on the other hand, are designed with a horizontal orientation, and the heat transfer surface is arranged in the form of tubes or bundles that run horizontally through the reboiler. The liquid to be heated is typically circulated through the tubes, while the heat source is located at one end of the reboiler.
The choice of which type of reboiler to use depends on several factors, including the specific application, the available space, and the desired level of heat transfer. In general, vertical reboilers are preferred when there is limited horizontal space available, as they require less floor space than horizontal reboilers. Horizontal reboilers, on the other hand, are preferred when there is limited vertical space available, as they require less headroom than vertical reboilers.
In terms of heat transfer characteristics, vertical reboilers are generally better suited for processes that require high heat transfer rates, while horizontal reboilers are better suited for processes that require more gentle heat transfer.
Ultimately, the choice of which type of reboiler to use depends on the specific process requirements, and both types have their advantages and disadvantages.
Again, depending on the types of circulation, the following five types of reboilers are widely used
- Fired Reboilers
- Force Circulation Reboilers
- Kettle Reboilers
- Thermosyphon Reboilers
- Internal Reboilers
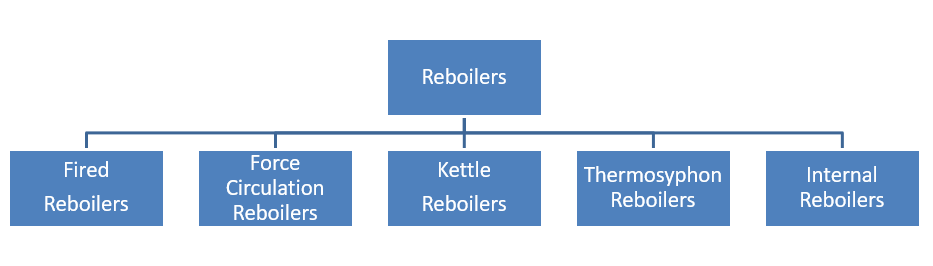
Fired Reboiler
A fired reboiler is a type of reboiler that uses a direct-fired burner to provide heat to the liquid mixture at the base of a distillation column. The burner is typically fueled by natural gas or fuel oil, and the heat generated by the burner is transferred to the liquid mixture through a heat transfer surface, such as a tube bundle or plate coil.
Fired reboilers are commonly used in distillation processes that require high heat input rates, such as those used in the petrochemical and chemical industries. They are typically more efficient than other types of reboilers, such as steam or electric reboilers, because they can provide a higher heat flux and faster heating rates.
Fired reboilers can be designed as either vertical or horizontal units, and they can be configured in various sizes and capacities to meet the specific needs of a given process. They can also be equipped with advanced controls and safety features, such as flame monitoring systems, to ensure safe and efficient operation.
One disadvantage of using a fired reboiler is that they require a continuous supply of fuel, which can be expensive and potentially hazardous. They also require periodic maintenance to ensure that the burner and heat transfer surfaces are functioning properly.
Forced Circulation Reboiler
A forced circulation reboiler is a type of reboiler that uses a pump to circulate the liquid mixture through the heat transfer surface, typically a tube bundle or plate coil. The liquid is heated by a heating medium, such as steam or hot oil, that flows over the heat transfer surface, and the heated liquid is then returned to the bottom of the distillation column.
The pump used in a forced circulation reboiler is typically a centrifugal pump, which provides the necessary pressure to overcome the pressure drop in the heat transfer surface and maintain the flow rate of the liquid.
Forced circulation reboilers are commonly used in distillation processes that require high heat transfer rates and efficient separation, particularly in processes where fouling or scaling is a concern. They are also commonly used in processes that require precise temperature control, as the flow rate of the liquid can be easily controlled using the pump.
One advantage of using a forced circulation reboiler is that it provides a high degree of heat transfer efficiency, as the liquid is continuously circulated over the heat transfer surface. This can result in a more efficient distillation process and a higher quality product.
Another advantage of using a forced circulation reboiler is that it can be easily scaled up or down to meet the needs of a specific process. The pump and heat transfer surface can be sized to match the flow rate and heat transfer requirements of the process, and multiple units can be used in parallel to increase production capacity.
However, one disadvantage of using a forced circulation reboiler is that it can be more complex and expensive to install and maintain compared to other types of reboilers. It also requires a source of heating medium, such as steam or hot oil, which can add to the overall operating cost of the distillation process.
Kettle Reboilers
A kettle reboiler is a type of shell and tube heat exchanger that is used as a reboiler in distillation processes. The kettle reboiler is a vertical cylindrical vessel that is mounted directly on top of the distillation column. The vessel contains a tube bundle that is suspended from the top of the vessel and extends down to the bottom, where it is connected to the distillation column. The tube bundle is heated by a heating medium, such as steam or hot oil, that flows through the tubes, and the liquid to be vaporized is heated by the tube bundle.
Kettle reboilers are commonly used in distillation processes that require high heat transfer rates, as they can provide a high degree of heat transfer efficiency due to their large heat transfer surface area. They are also commonly used in processes where fouling or scaling is a concern, as the tube bundle can be easily removed for cleaning or maintenance.
One advantage of using a kettle reboiler is that it can handle a wide range of liquid flow rates and compositions, making it suitable for a variety of distillation processes. It is also relatively easy to install and maintain, as it can be mounted directly on top of the distillation column.
However, one disadvantage of using a kettle reboiler is that it can be more expensive to operate compared to other types of reboilers, as it requires a large amount of heating medium to maintain the required heat transfer rate. It can also be less efficient than other types of reboilers, such as forced circulation reboilers, in terms of heat transfer per unit of the heating medium.
Thermosyphon Reboilers
A thermosyphon reboiler is a type of natural circulation reboiler that uses the natural circulation of the liquid to provide heat to the distillation process. In a thermosyphon reboiler, the liquid to be vaporized is heated by a heat transfer surface, typically a tube bundle or plate coil, that is located at the bottom of the reboiler. The heated liquid then rises up through the column due to the difference in density between the heated liquid and the cooler liquid at the top of the column, creating a natural circulation loop.
Thermosyphon reboilers are commonly used in distillation processes that require moderate to high heat transfer rates, as they can provide a high degree of heat transfer efficiency due to their large heat transfer surface area. They are also commonly used in processes that require low maintenance and are easy to operate, as they do not require any external power sources or moving parts.
One advantage of using a thermosyphon reboiler is that it is a simple and reliable means of providing heat to a distillation process. It can operate without the need for external power sources or moving parts, making it less prone to breakdowns and maintenance issues.
However, one disadvantage of using a thermosyphon reboiler is that it is less efficient than other types of reboilers, such as forced circulation reboilers, in terms of heat transfer per unit of the heating medium. It is also more sensitive to changes in the liquid flow rate and composition, which can affect the natural circulation loop and the efficiency of the reboiler.
Internal Reboilers
An internal reboiler is a type of reboiler that is installed within the distillation column itself, rather than being mounted externally. In an internal reboiler, the heating medium, typically steam or hot oil, is circulated through a coil or tube bundle that is located inside the column. The liquid to be vaporized is then heated by the coil or tube bundle, and the resulting vapor rises up through the column, where it is condensed and collected as the distillate.
Internal reboilers are commonly used in distillation processes that require a high degree of thermal efficiency and a compact design, as they can provide a large amount of heat transfer surface area within a relatively small space. They are also commonly used in processes that require a high degree of product purity, as they can minimize the number of impurities that are carried over with the vapor.
One advantage of using an internal reboiler is that it can provide a high degree of thermal efficiency, as the heat transfer surface area is located directly within the column where the vapor is being generated. This can also lead to a reduction in the size and cost of the distillation column, as the need for a separate reboiler vessel is eliminated.
However, one disadvantage of using an internal reboiler is that it can be more difficult to install and maintain compared to other types of reboilers, as it requires access to the inside of the distillation column. It can also be more prone to fouling or scaling, which can reduce its effectiveness and require more frequent cleaning or maintenance. Internal reboilers are also known as the Stab-in bundle reboiler.
Factors Influencing Reboiler Type Selection
The selection of the proper type of reboiler for any specific service is the most difficult job of reboiler design. Reboilers normally are shell-and-tube exchangers that heat up the fractionation column fluid utilizing the heat transfer from steam. Specific services may use other specialized designs including stab-ins, plate-fins, spiral-plate, and others. The purpose here is not to go into the design details of each specific type but rather to examine the selection criteria that favor one configuration over another. Since shell-and-tubes are so common, most of the discussion focuses on them but some factors favoring other designs are covered as well.
Many factors influence reboiler type selection. In the end, all these factors reduce economics. Every plant will weigh the trade-off between these factors differently. No one-size-fits-all selection exists. Major factors include:
- Plot space available
- Total duty required
- The fraction of tower liquid traffic vaporized
- Fouling tendency
- Temperature approach available
- Temperature approach required
- Corrosion of the fluid.
- Design temperature and Pressure.
- Characteristics of the reboiler boiling fluid.
- Heating medium requirements.
Reboiler Configurations
All of the above mentioned factors affect the desired configuration of the Reboiler. The major configuration selections include:
- Forced reboiler versus natural circulation reboiler
- Tube side versus shell side vaporization inside reboiler
- Once-through versus process recirculation reboiler
- Single-shell versus multiple-shell systems
- Vertical versus horizontal reboiler
- Stab-in bundles
- Other types
Figures 2 to 5 show common types of reboilers. Figure 2 shows two horizontal, shell-side boiling configurations. Figure 2A is a recirculating thermosyphon reboiler. Figure 2B is a once-through thermosyphon reboiler. Figure 3 shows vertical configurations. Figure 3C is a tube-side boiling configuration with the once-through flow and Figure 3D is a shell-side boiling recirculating thermosyphon. Figure 4E shows a kettle reboiler and Figure 4F shows a forced-circulation reboiler. Figure 5G illustrates a stab-in bundle and Figure 5H shows a forced-circulation, fired heater.
Reboiler Type Selection Table
Table 1 includes the major factors in making a choice for the reboiler type selection.
Factor | Favored types | Disfavored types |
Low bottoms product fraction compared to boil-up | Recirculating Kettle | Once-through |
High bottoms product fraction compared to boil-up | Once-through reboiler | Recirculating |
Low relative volatility systems | Recirculating | |
High relative volatility systems | Once-through | Recirculating |
Large exchanger size or high-duty requirements | Horizontal reboiler | Vertical reboiler |
Small exchangers | Vertical Stab-in | |
Leaks are hazardous or difficult to deal with | Stab-in | |
Exotic materials | Stab-in | |
Tight temperature approach | Spiral-plate Plate-fin | Shell-and-tube |
Solids present | Kettle Spiral-plate | Plate-fin |
Thermally unstable products | Recirculating (no baffle) | Kettle Once through |
Tight plot plan | Vertical | Horizontal |
Ample plot plan | Horizontal | |
High temperatures | Fired heaters | |
High heat fluxes | Forced circulation Flooded bundles | Natural circulation |
Other systems in addition to the ones shown here are also possible. Of course, every reboiler system’s final choice will depend upon specific design details involved. Many reboiler systems have specific characteristics that favor designs that might not be immediately apparent.
Benefits of using Reboilers
The advantages of using a reboiler in a distillation process include:
- Increased separation efficiency: By providing heat to the liquid mixture at the base of the distillation column, the reboiler promotes the vaporization of the liquid, which improves the separation efficiency of the process.
- Improved product quality: A reboiler can help improve the quality of the final product by separating impurities and unwanted components from the liquid mixture.
- Increased production capacity: A reboiler can help increase the production capacity of a distillation process by promoting faster and more efficient separation of the liquid mixture.
- Reduced energy consumption: Using a reboiler can help reduce the amount of energy needed to operate the distillation process by promoting faster and more efficient separation.
- Increased process control: A reboiler can be designed with advanced control systems to regulate the heat input and optimize the distillation process, which can improve the overall process control and efficiency.
Overall, the use of a reboiler in a distillation process can provide significant advantages in terms of separation efficiency, product quality, production capacity, energy consumption, and process control.
Reboilers vs Evaporators
A reboiler and an evaporator are both types of heat exchangers used in different types of processes. While they are similar in some ways, there are some key differences between the two.
The main difference between a reboiler and an evaporator is the purpose for which they are used. A reboiler is used in distillation processes to separate a liquid mixture into its individual components, while an evaporator is used to concentrate a solution by removing its solvent through vaporization.
Another difference between the two is the location where they are used in the process. A reboiler is typically located at the bottom of a distillation column, where it provides heat for the liquid mixture to be separated, while an evaporator is typically a standalone unit used to concentrate a solution.
The design of a reboiler and an evaporator also differs. A reboiler is designed to provide heat at a controlled rate to the liquid mixture, and it may have features such as internal baffles to promote mixing and heat transfer. An evaporator is designed to promote the vaporization of the solvent and may have features such as multiple stages to increase concentration and efficiency.
In summary, while both a reboiler and an evaporator are types of heat exchangers used to transfer heat to a liquid, the main differences lie in their purposes, locations in the process, and design features.
Boiler vs Reboiler
A boiler and a reboiler are both types of heat exchangers that are used in different applications. The main differences between a boiler and a reboiler are:
- Purpose: A boiler is used to generate steam or hot water for heating or power generation, while a reboiler is used to provide heat to a distillation column for the separation of liquids.
- Design: A boiler is typically a large vessel that contains a heating source, such as a burner or a nuclear reactor, and a heat exchanger that transfers heat to the water or steam. A reboiler, on the other hand, is a smaller vessel or heat exchanger that is mounted directly on top of a distillation column and provides heat to the liquid inside the column.
- Fluids: A boiler is designed to heat water or other fluids to a high temperature and pressure to generate steam or hot water, while a reboiler is designed to heat a liquid, such as a mixture of liquids in a distillation column, to its boiling point to generate vapor.
- Operation: A boiler operates by heating the water or other fluid to a high temperature and pressure, while a reboiler operates by heating the liquid to its boiling point, allowing the vapor to rise up through the distillation column and separate into different components.
While both boilers and reboilers are heat exchangers, they are designed for different purposes and applications. A boiler is used to generate steam or hot water for heating or power generation, while a reboiler is used to provide heat to a distillation column for the separation of liquids.
Conclusion
In the complex world of industrial processes, reboilers stand as silent workhorses, diligently providing the heat needed for distillation and fractionation operations. Their versatile designs cater to various applications, ensuring the efficient separation of mixtures into valuable components. As industries continue to evolve and demand higher efficiency, reboilers will undoubtedly remain a crucial component, driving innovation and sustainable production across the board.
Few more resources for you…
Piping Design and Layout
Piping Stress Analysis
Piping Materials
Piping Interface
Very good and informative blog.