The oil and gas industry is one of the most critical sectors in global energy production. To ensure efficient and safe operations, various equipment and technologies are employed. Among these essential components are sight glasses, which play a vital role in monitoring processes and enhancing safety within the industry. Sight glasses provide visual access to observe fluids, gases, and their behaviors in equipment and pipelines. This article explores the significance, types, and applications of sight glasses in the oil and gas industry.
What is a Sight Glass?
A sight glass, also known as a sight window, viewport, or sight port window, is a specialized type of transparent visual window for observing working fluids at high temperatures and pressures. Widely used in tanks, process vessels, boilers, reactors, and many other industrial equipments, Sight glasses are made from robust glass materials that can resist such extreme environments. One can use these sight glasses to look at the process inside the equipment safely. Resembling a glass disc between two metal frames, sight glasses are strong enough to break or usual failures.
Importance of Sight Glasses
In oil and gas facilities, the ability to visually inspect processes, fluids, and equipment is invaluable. Sight glasses allow operators and maintenance personnel to monitor
- fluid levels,
- flow rates,
- color changes,
- phase separations,
- production stages,
- fluid quality, and
- the presence of contaminants or bubbles.
These observations help identify potential issues, such as leaks, pressure imbalances, or equipment malfunctions without having to open the equipment which allows for timely interventions and preventing costly downtime or hazardous situations. Fig. 1 below shows some typical sight glasses:
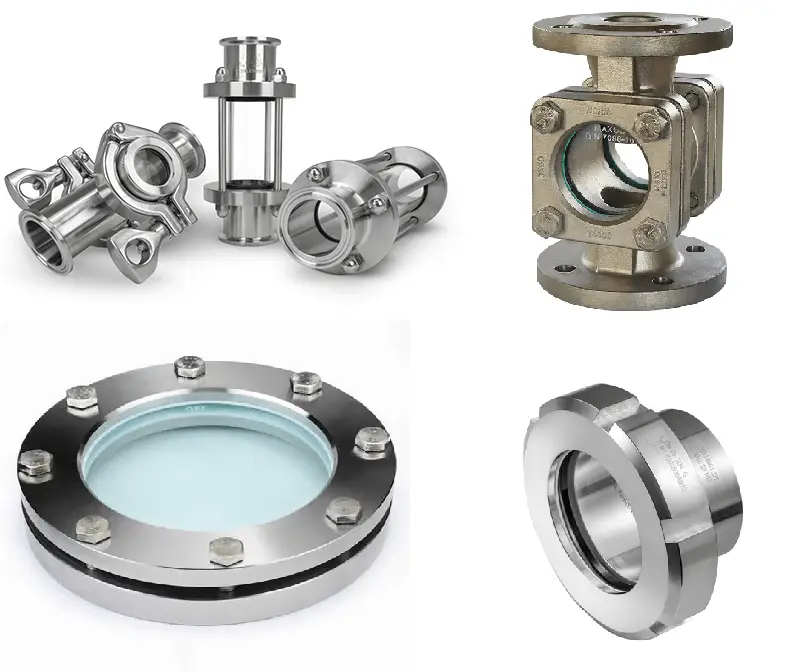
Types of Sight Glasses
Transparent Sight Glasses:
These sight glasses are made from materials such as tempered borosilicate glass or polycarbonate. They offer excellent visibility, high resistance to chemicals and thermal shock, and are suitable for high-pressure applications. Transparent sight glasses are commonly used in storage tanks, pipelines, and process vessels.
Reflex Sight Glasses:
Reflex sight glasses have a prism on one side that refracts light, resulting in a contrast difference when viewed from different angles. The change in appearance indicates the presence or absence of fluid within the sight glass. These glasses are advantageous when dealing with transparent fluids, as they enhance visibility by highlighting the fluid level. Reflex sight glasses are commonly used in low-pressure applications and steam systems.
Magnetic Sight Glasses:
Magnetic sight glasses incorporate a magnetic strip or float inside a glass tube. As the fluid level changes, the position of the magnetic float varies, providing a visual indication of the level. These sight glasses are particularly useful when dealing with opaque or hazardous fluids, as they eliminate the need for direct contact with the medium. Magnetic sight glasses are widely used in oil separators, compressor systems, and hydraulic reservoirs.
Again depending on the construction of the sight glasses there are two types of sight glasses that are used in the oil and gas industries. they are:
- Conventional glass disc window sight glass which consists of a glass disc sandwiched between two gasketed metal rings suitable for low-pressure and non-critical processes; and
- A fused sight glass for high-performance applications where the glass window is fused to the metal carrier ring during its construction.
Materials for Sight Glasses
Depending on the application environment requirements, various types of glass materials are used for making sight glasses.
- For low-pressure-temperature, non-critical applications sight glass windows are manufactured from standard soda lime glass. For a temperature of up to 536°F, borosilicate glass (Pyrex®) or acrylic plastics are used for constructing sight glass windows.
- For equipment involving temperatures above 536°F, sight glass windows are generally made using quartz or sapphire glass. these materials are thermal shock or corrosion-resistant.
- For some sanitary processing applications, high-grade specialty plastics such as acrylic (plexiglass or PMMA (Polymethyl methacrylate)) or polycarbonates are used for making sight glasses.
The metallic frames are normally made from stainless steel. So the materials used for constructing sight glasses can be summarized as follows:
- Borosilicate Glass: Borosilicate glass, such as the popular brand Pyrex®, is widely used in sight glasses. It offers excellent clarity, high resistance to thermal shock, and good chemical compatibility with a wide range of fluids. Borosilicate glass is suitable for both low and high-pressure applications and is often used in transparent sight glasses.
- Tempered Glass: Tempered glass is heat-treated glass that is stronger and more impact-resistant than standard glass. It undergoes a controlled heating and rapid cooling process to increase its strength. Tempered glass sight glasses are preferred in applications where there is a higher risk of mechanical stress or impact, such as in industrial environments.
- Polycarbonate: Polycarbonate is a durable, lightweight, and shatter-resistant thermoplastic material. It offers excellent impact resistance and is often used as a safer alternative to glass in applications where the risk of breakage is high. Polycarbonate sight glasses are commonly used in industries where safety is a priority, such as oil and gas, chemical processing, and food processing.
- Acrylic: Acrylic, also known as plexiglass or PMMA (Polymethyl methacrylate), is a transparent thermoplastic material. It offers good optical clarity, and impact resistance, and is lighter than glass. Acrylic sight glasses are commonly used in lower-pressure and temperature applications where chemical resistance is not a critical requirement.
- Stainless Steel: In some cases, sight glasses may have metal frames or housings, especially when the operating conditions are severe or the sight glass is exposed to corrosive environments. Stainless steel is often used for such applications due to its high strength, corrosion resistance, and durability. Stainless steel sight glasses are commonly used in oil and gas equipment, chemical processing, and offshore installations.
- Teflon (PTFE): Teflon, or polytetrafluoroethylene (PTFE), is a fluoropolymer known for its excellent chemical resistance. It is often used as a gasket or sealing material in sight glasses to provide a reliable and leak-free connection between the glass and surrounding equipment for low-temperature applications.
Selecting Sight Glasses
Selecting the right sight glass for a specific application requires careful consideration of several factors. These factors include:
Fluid Compatibility:
The sight glass material must be compatible with the fluid being observed. Some fluids may be corrosive, abrasive, or reactive with certain materials. It is crucial to choose a sight glass material that can withstand the chemical properties of the fluid without degradation or damage.
Pressure and Temperature:
Consider the operating pressure and temperature of the system where the sight glass will be installed. The sight glass should be able to withstand mechanical stress and thermal conditions (thermal shock) without compromising its integrity or visibility. Ensure that the selected sight glass has an appropriate pressure and temperature rating for the application.
Visibility and Clarity:
The visibility requirements of the application should be considered. Some applications may require high clarity and transparency to observe fine details or color changes in the fluid. In such cases, materials like borosilicate glass or tempered glass are preferred. Assess the optical properties of the sight glass material to ensure it provides the desired visibility.
Mechanical Strength and Impact Resistance:
Depending on the application, the sight glass may be subject to mechanical stress or impact. Consider the robustness and strength of the selected material to ensure it can withstand the anticipated forces without breaking or cracking. Tempered glass or polycarbonate are often chosen for applications requiring high-impact resistance.
Safety Considerations:
Safety is paramount in the oil and gas industry. Evaluate the risk of potential accidents, such as glass breakage, and consider materials that minimize the hazards associated with shattered glass. Polycarbonate or acrylic, which are shatter-resistant materials, may be preferred in safety-critical applications.
Environmental Factors:
Assess the environmental conditions surrounding the sight glass installation. Factors such as exposure to harsh chemicals, UV radiation, extreme weather conditions, or abrasive particles may impact the longevity and performance of the sight glass. Choose a material that can withstand these environmental factors and ensure its durability.
Regulatory and Industry Standards:
Consider any applicable regulatory requirements or industry standards for sight glass selection. Some industries, such as oil and gas, may have specific guidelines or standards that dictate the use of certain materials or designs. Ensure compliance with relevant regulations and standards to maintain operational and safety standards.
Maintenance and Cleaning:
Evaluate the ease of maintenance and cleaning for the selected sight glass material. Some materials may require specialized cleaning procedures or have restrictions on cleaning agents. Consider the accessibility of the sight glass for routine inspections and maintenance activities.
Specifying a Sight Glass
Specifying a sight glass involves providing detailed information and requirements to ensure that the selected sight glass meets the specific needs of the application. Here is the key information to specify a sight glass effectively:
- Application Details: Clearly define the application where the sight glass will be used. Understand the purpose of the sight glass, whether it is for monitoring fluid levels, observing flow patterns, or detecting the presence of contaminants. Identify the specific equipment or system where the sight glass will be installed, such as storage tanks, pipelines, reactors, or separators.
- Operating Conditions: Provide information about the operating conditions of the system. This includes factors such as pressure range, temperature range, and the type of fluid or media being observed. Note any potential variations or fluctuations in pressure or temperature that the sight glass may encounter during operation.
- Sight Glass Type: Determine the most suitable type of sight glass based on the application requirements and operating conditions. Consider factors such as transparency needs, pressure rating, and the ability to detect specific fluid properties (e.g., color changes, fluid level). Choose from options such as transparent sight glasses, reflex sight glasses, or magnetic sight glasses.
- Material Requirements: Based on the fluid compatibility, pressure, temperature, and visibility requirements, specify the appropriate sight glass material. Consider factors such as chemical resistance, mechanical strength, impact resistance, and safety considerations. Common materials include borosilicate glass, tempered glass, polycarbonate, or acrylic.
- Specify Dimensions and Connections: Provide the required dimensions of the sight glass, including the diameter or length of the glass tube or window. Specify the connections or fittings needed to integrate the sight glass into the equipment or system, such as threaded, flanged, or welded connections.
- Consider Additional Features: Determine if any additional features are necessary for the sight glass. This may include protective coatings for enhanced chemical resistance, special gaskets or seals, lighting arrangements for improved visibility, or pressure relief devices. Specify any specific requirements or preferences for these additional features.
- Compliance and Standards: Ensure that the specified sight glass complies with applicable industry standards, regulations, and safety guidelines. Consider any specific certifications or approvals required for the sight glass, especially in safety-critical applications.
- Quantity and Delivery Timeframe: Specify the number of sight glasses you require, as well as any specific delivery timeframe or schedule. This will help the vendor provide accurate pricing and determine their ability to meet your timeline.
- Any Other Relevant Information: Provide any additional relevant information that might assist the vendor in understanding your requirements accurately. This may include any specific preferences, previous experiences, or challenges you have encountered with similar equipment.
Applications of Sight Glasses in the Oil and Gas Industry
Storage Tanks and Vessels:
Sight glasses allow operators to monitor liquid levels, flow patterns, and the presence of sediments or contaminants in storage tanks and vessels. By providing real-time visual information, sight glasses help optimize storage capacity, prevent overflow or underfilling, and ensure the quality of stored materials.
Reactors and Separators:
Sight glasses provide a direct view into reactors and separators, allowing operators to observe chemical reactions, phase separations, and the accumulation of impurities or byproducts. Monitoring these processes in real-time facilitates adjustments to operating conditions and helps maintain the efficiency and safety of the equipment.
Piping Systems:
Sight glasses installed in pipelines aid in the detection of leaks, blockages, or changes in fluid behavior. By visually inspecting the flow, operators can identify issues such as turbulence, cavitation, or the formation of hydrates, enabling prompt maintenance and preventing system failures.
Offshore and Subsea Applications:
In offshore and subsea oil and gas operations, sight glasses are used to monitor the condition of subsea equipment, pipelines, and risers. By visually inspecting these critical components, operators can detect corrosion, fouling, or the presence of hydrates or blockages, ensuring the integrity and reliability of subsea infrastructure.
The industries that widely use sight glasses are:
- Oil & Gas
- Chemical & Petrochemical
- Food & Beverage
- Biofuels
- Pharmaceutical
- Utility Industry
- Biogas
- Biotech
- Wastewater Treatment
What is a Boiler Sight Glass?
A boiler sight glass, also known as a sight gauge or water level gauge, is a transparent tubular device used to visually monitor the water level inside a boiler or steam generator. It provides a direct indication of the water level, allowing operators to ensure the safe and efficient operation of the boiler.
The boiler sight glass typically consists of a glass tube or window mounted on the boiler’s water drum or steam drum. The glass tube is usually made of tempered borosilicate glass, which is able to withstand high temperatures and pressure. The sight glass is installed at a convenient location on the boiler, allowing operators to easily observe the water level. The sight glass operates on the principle of communicating vessels. As the water level inside the boiler changes, the water level in the sight glass also rises or falls accordingly. By observing the position of the water level in the sight glass, operators can determine if the boiler has sufficient water for safe operation or if it needs to be replenished.
What is a Tank Sight Glass?
A tank sight glass, also known as a liquid level gauge or tank level indicator, is a transparent device used to visually monitor the liquid level inside a storage tank or vessel. It provides a direct indication of the fluid level, allowing operators to monitor inventory, prevent overfilling or underfilling, and ensure efficient operation of the tank.
Tank sight glasses typically consist of a transparent glass or plastic tube or window installed on the side or top of the tank. The material used for the sight glass depends on the specific application and the properties of the fluid being stored. The sight glass is connected to the tank through fittings or flanges, allowing the liquid to reach the same level inside the sight glass as it does in the tank.
Conclusion
Sight glasses play a crucial role in the oil and gas industry, enabling operators and maintenance personnel to visually monitor processes, fluids, and equipment. By providing real-time visibility, sight glasses contribute to enhanced efficiency, improved safety, and timely interventions to prevent costly downtime or hazardous situations. The availability of different types of sight glasses allows for their widespread use in various applications, including storage tanks, piping systems, reactors, and offshore operations. Incorporating sight glasses as an integral part of oil and gas infrastructure is a prudent investment that ensures the industry’s smooth functioning while minimizing risks and maximizing operational performance.