The oil and gas industry is a complex and multifaceted sector that relies heavily on various types of equipment to ensure efficient and safe operations. All the equipment can be categorized into two groups; static equipment and rotary equipment. Among these, static equipment plays a crucial role in processing, storing, and transporting hydrocarbons.
The majority of mechanical types of equipment found in oil and gas facilities belong to the static equipment group, which comprises pressure vessels, heat exchangers, storage tanks, fired Heaters, pig launchers, etc. In this article, we will briefly describe some of the static equipment.
What is the Static Equipment?
Static equipment refers to the fixed machinery and components that do not undergo significant movement during their operation. They are also known as stationary equipment. Unlike rotating equipment, such as pumps and turbines, static equipment remains stationary, often functioning under high pressures and temperatures. This category includes:
- Pressure Vessels
- Heat Exchangers
- Storage Tanks
- Columns and Towers
- Reactors
- Flares
Types of Static Equipment
Depending on the purpose they serve, there are various types of static equipment. Some of the most common stationary types of equipment are:
1. Horizontal & Vertical Pressure Vessel:
A pressure vessel is a container designed to hold fluids, i.e, gases or liquids, at a pressure substantially different (higher or lower) from the ambient pressure. They are either vertical or horizontal. Pressure vessels are designed following ASME BPVC codes. In oil and gas applications, they are often used for:
- Storage: Storing hydrocarbons and chemicals under pressure.
- Separation: Facilitating the separation of oil, gas, and water.
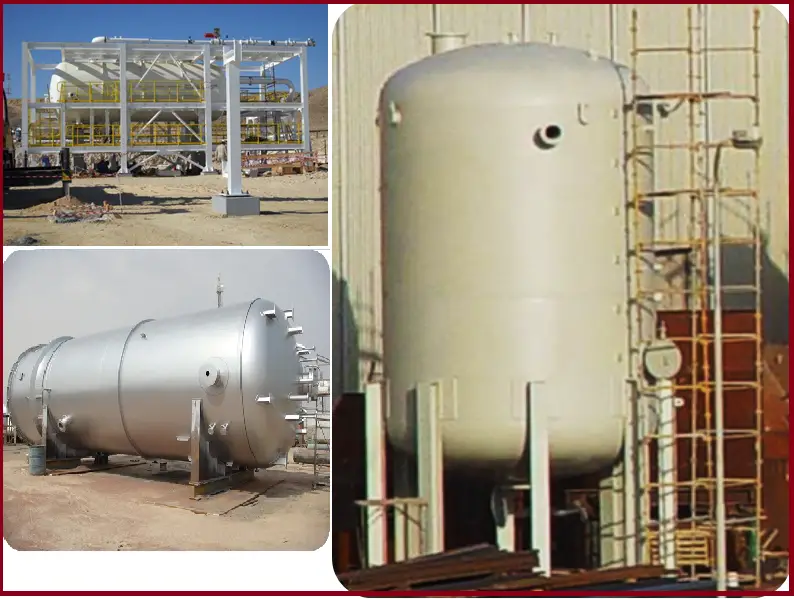
2. Columns and Towers:
Columns and towers are tall vertical pressure vessels. They have internals like trays, packing, distributors, demisters, etc. for separation and other applications. Used primarily in refining processes, columns and towers facilitate the separation of different components through distillation. They play a key role in:
- Absorption and Stripping: Removing impurities or desired components.
- Fractionation: Separating crude oil into its constituent parts.
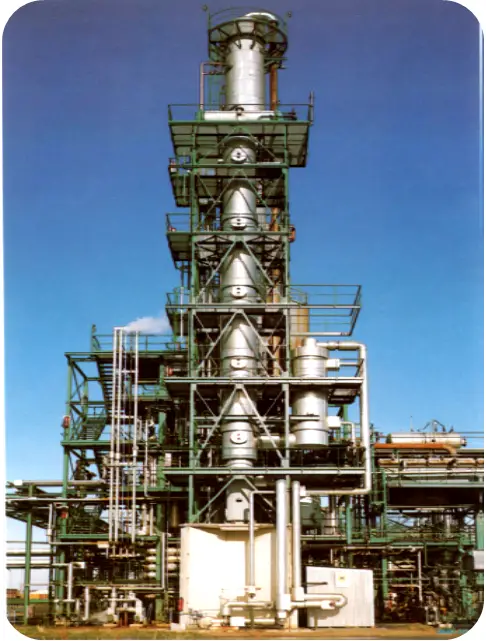
3. Buried/ Mounded Storage Bullets:
Bullets are large, high-pressure storage vessels. Generally used for storing LPG / LNG. Buried / Mounded to safeguard against any accident. They are designed based on API 620.
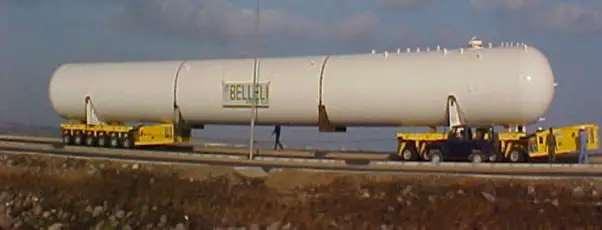
4. Atmospheric Storage Tanks:
Storage tanks are large, atmospheric-pressure storage equipment. Depending on the fluid stored, the tank roof design will be of the fixed roof or floating roof type. Click here to learn more about various atmospheric storage tanks. Storage tanks hold crude oil, refined products, and other chemicals. Designed following API 650, they come in various designs, including above-ground and underground tanks, and serve multiple purposes:
- Safety: Providing safe storage of hazardous materials.
- Buffer Storage: Managing supply and demand fluctuations.
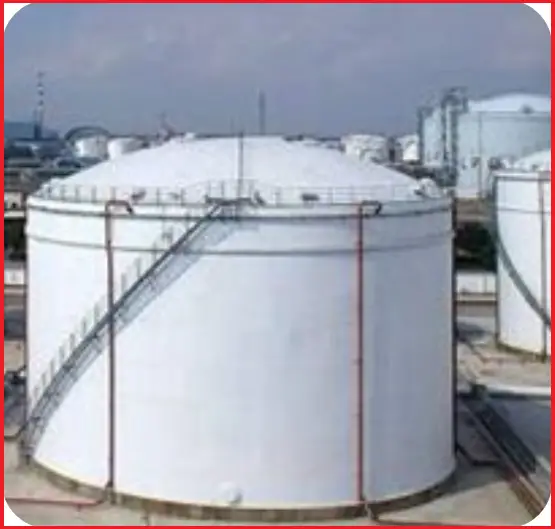
5. Storage Spherical tanks:
A spherical storage tank is a type of tank used to store liquids or gases under pressure. Its spherical shape provides strength and minimizes surface area, which reduces the risk of leaks and structural failure. These tanks are commonly used for storing liquefied gases like propane and butane.
Spheres are very large, high-pressure storage equipment. Generally used for storing huge quantities of LPG / LNG / NGL. Spherical storage tanks are designed following API 620.
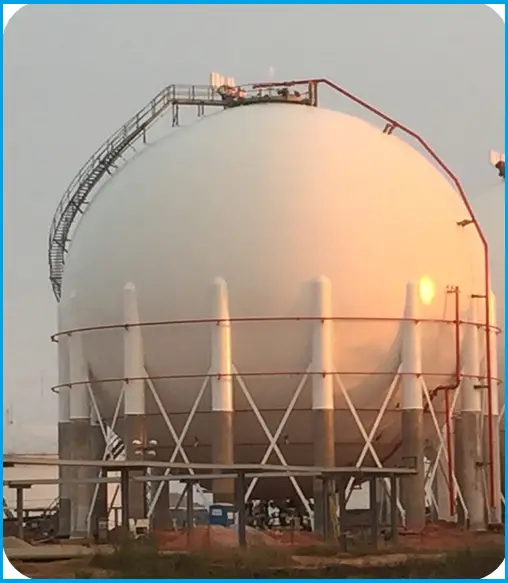
6. Heat Exchangers
Heat exchangers transfer heat between two or more fluids, critical for:
- Cooling: Reducing the temperature of process streams.
- Heating: Preheating feedstock to optimize reaction rates.
The most common heat exchangers used in the oil and gas industries are
6.1 Shell & Tube Heat Exchangers:
Most commonly used heat exchanger. Used for high-pressure, high-duty applications. A shell and tube heat exchanger consists of a series of tubes, one set carrying the hot fluid and the other carrying the cold fluid. The heat exchange occurs as the fluids flow past each other, allowing for efficient thermal transfer. This design is widely used in oil refineries and chemical plants.
6.2 Air-Cooled Heat Exchangers:
Also called dry-type cooling towers, air is used as a cooling medium. An air-cooled heat exchanger uses ambient air to cool process fluids. It typically consists of finned tubes through which the fluid flows, and a fan to enhance air circulation. These exchangers are often used in locations where water is scarce or for cooling high-temperature fluids.
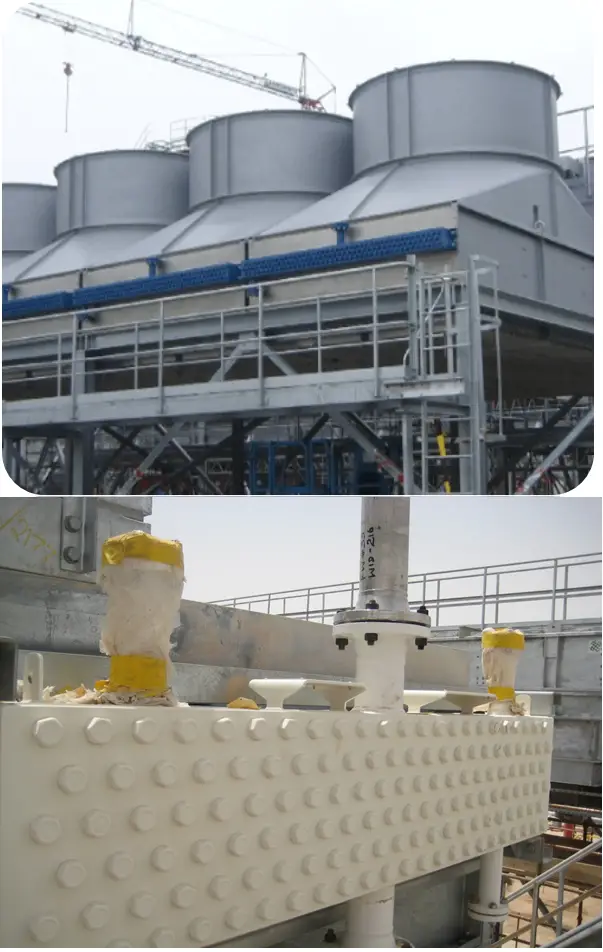
6.3 Plate Type Heat Exchangers (Fig. 7):
A compact type heat exchanger, used for medium-pressure, high-duty applications. It can work with very low approach temperatures. A plate type heat exchanger comprises thin plates arranged in a stack to create channels for the fluids. The design allows for a large surface area for heat transfer while minimizing the volume. This type is known for its efficiency and is commonly used in various process industries, including oil and gas.
7. Fired Heaters (Fig. 7):
A fired heater comprises a furnace where the flame impinges directly on the tubes/surfaces containing the fluid to be heated, which include process fluid, thermic fluids, air, water, and so on.
The furnace is also called a radiant zone as major heat transfer is by radiation, followed by the convection zone wherein the heat transfer is predominantly by convection.
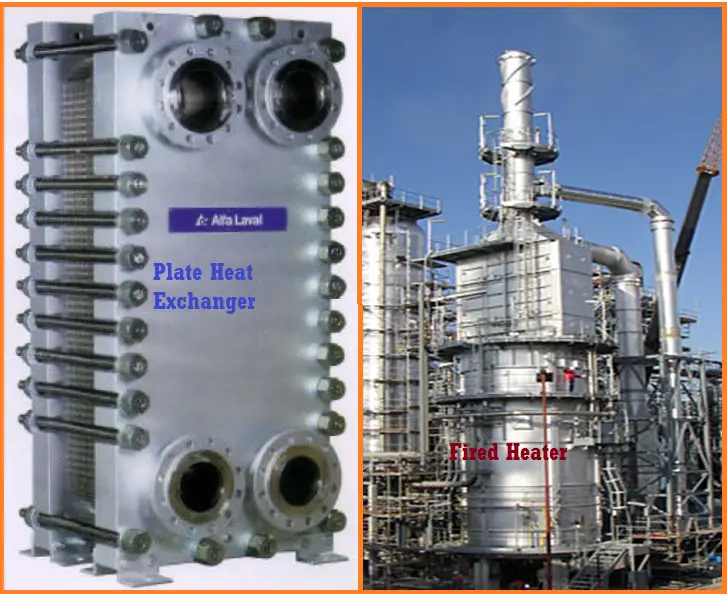
8. PIG Launchers / Receivers:
A pig launcher is a device that uses a pressurized container to shoot a cleaning device (“pig”) through the pipeline to perform a variety of functions including cleaning, monitoring, and maintaining the pipe.
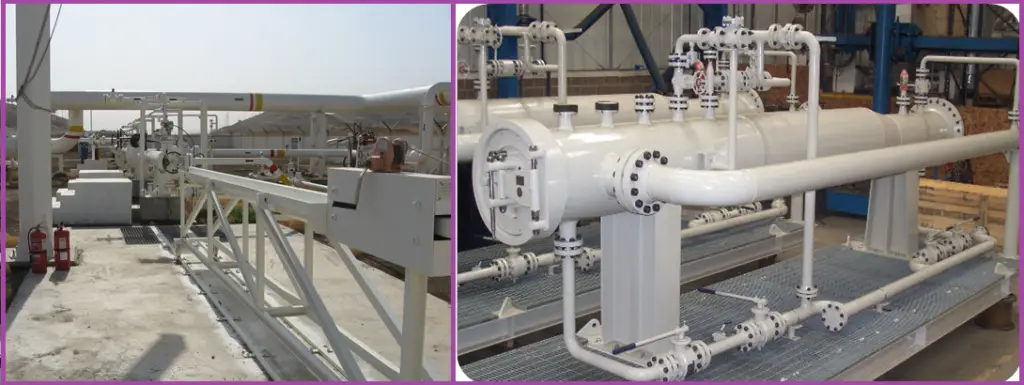
9. Flare Stack and Flare:
A flare stack is a safety device used to burn off excess hydrocarbons that cannot be processed or captured. This prevents the accumulation of flammable gases, reducing explosion risks. Flare stacks are essential in maintaining safety and environmental compliance. Fig. 9 below shows an example of a flare stack.
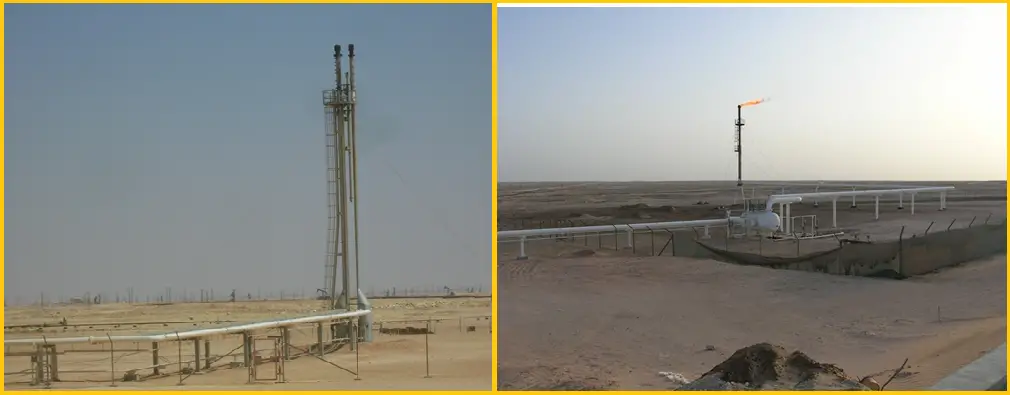
10. Knock Out Drum:
A knock out drum (Fig. 9) is a vessel designed to separate liquids from gases in a pipeline system. It allows for the removal of liquids that may condense from gases, ensuring that only vapor enters downstream equipment. This prevents damage and ensures optimal operation.
11. Jet Ejector:
A jet ejector is a device that uses a high-velocity jet of fluid to create a vacuum or to mix fluids. It is often used in applications like transporting fluids and gas, separating phases, or creating suction for gas lifting in oil wells.
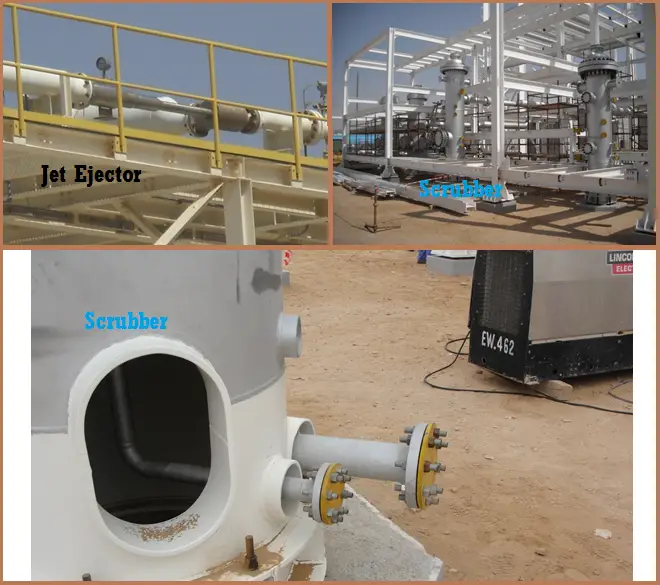
12. Scrubber
A scrubber is a device used to remove pollutants or particulates from gas streams. In the oil and gas industry, scrubbers are used to clean process gases and prevent emissions of harmful substances, enhancing environmental compliance.
13. MSV Skid:
A multiport valve skid (MSV skid) is a compact, pre-assembled system designed to manage the flow of fluids in various directions within a pipeline network. It incorporates multiple valves—often including gate, ball, or check valves—configured in a single unit. Fig. 11 below shows a typical diagram of MSV skid.
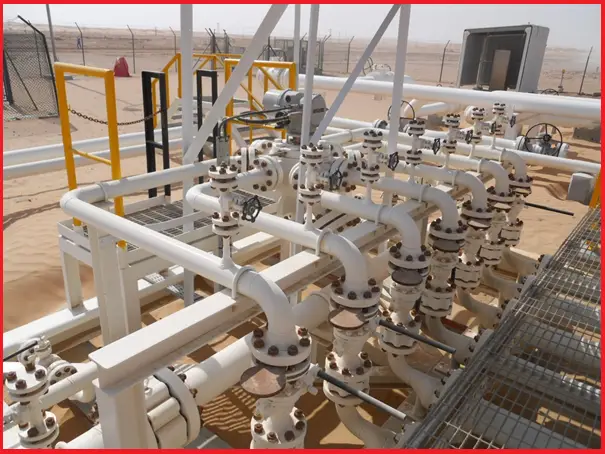
14. Wellhead:
A wellhead is the structure at the surface of a well that provides the interface for drilling and production equipment. It contains valves, gauges, and fittings to control the flow of oil or gas and ensure safety during extraction.
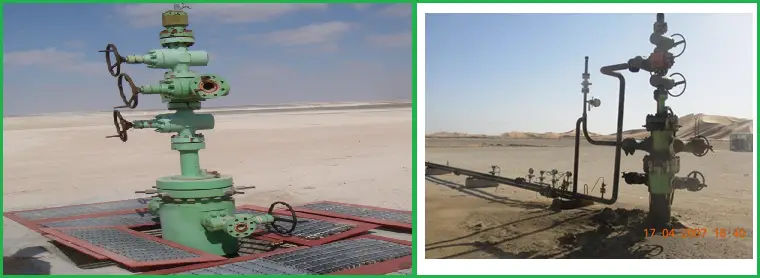
15. Boilers
Boilers are vessels used to generate steam or hot water by heating a fluid. In the oil and gas industry, they are often used for providing steam for processes, heating, and driving turbines.
16. Filters
Filters are devices used to remove particulates, impurities, and contaminants from fluids. In oil and gas operations, filters help maintain the quality of process fluids and protect equipment from damage.
17. Furnace
A furnace is an industrial heating device used to raise the temperature of materials or fluids. In oil refining, furnaces are used to heat crude oil before it enters the distillation column.
18. Reactors
Reactors are vessels where chemical reactions occur to convert raw materials into products. In the oil and gas industry, reactors can be used for processes like cracking and reforming hydrocarbons.
19. Deaerator
A deaerator is a device used to remove dissolved gases (mainly oxygen) from water or other fluids, preventing corrosion in boilers and other equipment. It enhances the efficiency and longevity of systems using water.
20. Steam Drums
Steam drums are vessels in a steam generation system that separate steam from water. They play a crucial role in ensuring the quality of steam used in processes and are commonly found in boiler systems.
21. Static Mixer
A static mixer is a device used to mix two or more fluids without moving parts. It typically consists of a series of stationary elements that create turbulence, ensuring uniform mixing. These are often used in chemical processing and oil refining.
22. Surge Tank
A surge tank is a vessel used to absorb changes in pressure and flow within a system, protecting equipment from pressure fluctuations. It helps maintain system stability in pipelines and processing units.
23. Electrostatic Precipitator
An electrostatic precipitator is a device that removes particulate matter from gas streams by charging particles and collecting them on plates. This is crucial for reducing emissions and meeting environmental standards.
24. Coalescer
A coalescer is a device used to separate immiscible liquids, such as water from oil. It allows smaller droplets to merge into larger ones, making separation easier. Coalescers are vital in oil refining and processing.
25. Separator
A separator is a vessel that separates different phases of a mixture, typically oil, gas, and water. In the oil and gas industry, separators are essential for ensuring product purity and quality.
26. Demister
A demister is a device used to remove mist or small droplets from gas streams. It is often employed in conjunction with separators to enhance product quality by ensuring that gas is free from liquid contaminants.
27. Cyclone
A cyclone is a separation device that uses centrifugal force to separate particles from a gas or liquid stream. Cyclones are commonly used for removing dust or solid particulates in gas streams.
28. Silo
A silo is a large storage structure used for holding bulk materials, such as solid fuels or chemicals. In the oil and gas industry, silos may store solid materials used in drilling or processing.
29. Electrolyzer
An electrolyzer is a device that uses electricity to split water into hydrogen and oxygen through electrolysis. In the oil and gas industry, electrolyzers are gaining attention for producing hydrogen, which can be used as a clean fuel or in refining processes.
Importance of Static Equipment in Oil and Gas Operations
The reliability and efficiency of static equipment directly impact the overall safety, productivity, and profitability of oil and gas operations. Here are some key reasons why they are indispensable:
- Safety: Properly maintained static equipment reduces the risk of leaks, explosions, and other hazardous incidents, safeguarding workers and the environment.
- Operational Efficiency: Efficient static equipment ensures smooth processes, reducing downtime and improving throughput.
- Regulatory Compliance: Adherence to industry regulations and standards is critical to avoid penalties and ensure safe operations.
- Cost Management: Investing in the maintenance of static equipment can prevent costly repairs and operational disruptions down the line.
Hence, static equipment forms the backbone of operations in the oil and gas industry. These components are essential for processes such as separation, storage, and heat exchange, playing a crucial role in the efficiency and safety of operations, particularly in the oil and gas industry.
FAQ regarding Static Equipment
What Are The Static Equipment Used in a Refinery?
Static equipment in a refinery includes components that do not have moving parts during normal operation. Common examples are:
- Storage Tanks: For crude oil and refined products.
- Heat Exchangers: For transferring heat between fluids.
- Pressure Vessels: Including reactors and separators.
- Pipes and Pipelines: Used for transporting fluids.
- Columns: Such as distillation columns for separation processes.
Is Valve A Static Equipment?
Valves are typically classified as dynamic equipment because they control the flow of fluids and have moving parts. However, in the context of EPC organizations, a valve is considered a piping item, not equipment.
Are Piping and Pipeline Static Equipment?
In the context of EPC organizations, piping, and pipelines are considered different from equipment categories. So, there is confusion regarding whether piping and pipelines are to be considered static equipment or not.
Is A Separator Static Equipment?
Yes, separators are classified as static equipment. They are designed to separate different phases of a mixture (such as oil, gas, and water) without any moving parts during the separation process.
Is A Compressor Static or Rotary?
A compressor is classified as rotary equipment. It has moving parts that compress gases to increase their pressure.
What Is Static Equipment Engineering?
Static equipment engineering involves the design, analysis, and maintenance of equipment that does not have moving parts. This includes ensuring structural integrity, pressure vessel design, heat transfer efficiency, and compliance with safety regulations.
Which is the most widely used static equipment in the oil and gas industry?
The most widely used static equipment in the oil and gas industry includes storage tanks and pressure vessels, as they are essential for the storage and processing of hydrocarbons.
What is the difference between static and rotary equipment?
The primary difference lies in their operational characteristics:
- Static Equipment: Does not have moving parts; examples include tanks, heat exchangers, and separators.
- Rotary Equipment: Contains moving parts and performs work on fluids; examples include pumps, compressors, and turbines.
What is the normal flow for static equipment design?
The normal flow for static equipment design includes several steps:
- Define Requirements: Understand the operational requirements and specifications.
- Select Material: Choose appropriate materials based on fluid properties and environmental conditions.
- Design Calculations: Perform necessary calculations for pressure, temperature, and structural integrity.
- Draft Design: Create detailed engineering drawings and specifications.
- Review and Approvals: Ensure compliance with industry standards and obtain necessary approvals.
What is static plant equipment?
Static plant equipment refers to the fixed installations in a facility that are essential for processing and storing materials. This includes all static equipment like storage tanks, heat exchangers, reactors, and pipelines that support the refinery operations without moving parts during normal function.
What Are the Common Materials Used in Static Equipment?
Common materials for static equipment include carbon steel, stainless steel, and various alloys. The choice depends on factors such as temperature, pressure, and the corrosiveness of the fluids involved.
How is the Maintenance of Static Equipment Different from Rotary Equipment?
Maintenance of static equipment often focuses on inspections for structural integrity, corrosion, and leakage, while rotary equipment maintenance may involve lubrication, alignment, and wear monitoring of moving parts.
What Standards Govern the Design of Static Equipment?
Design standards for static equipment are governed by various codes and regulations, such as ASME (American Society of Mechanical Engineers) for pressure vessels and API (American Petroleum Institute) standards for tanks and pipelines.
What Factors Influence the Design of Static Equipment?
Key factors include the type of fluid being processed, operating temperature and pressure, environmental conditions, and safety regulations.
What Is the Role of Static Equipment in Process Safety?
Static equipment plays a crucial role in process safety by containing fluids under pressure, preventing leaks, and ensuring safe storage and handling of hazardous materials.
Can Static Equipment Be Used for Dynamic Processes?
While static equipment is primarily designed for steady-state operations, some components (like heat exchangers) can also be involved in dynamic processes, such as fluctuating flow rates, under certain conditions.
How Do You Determine the Lifespan of Static Equipment?
The lifespan of static equipment is determined by factors like material degradation, maintenance practices, operational conditions, and adherence to safety standards.
What Are the Challenges in Designing Static Equipment?
Challenges include managing thermal expansion, ensuring structural integrity under pressure, preventing corrosion, and optimizing for efficiency while adhering to safety regulations.
How Do You Ensure Compliance with Environmental Regulations for Static Equipment?
Ensuring compliance involves conducting environmental impact assessments, implementing leak detection systems, and adhering to regulations set forth by local and national environmental agencies.
This is very useful for all as
You are good writing for oil and gas refinery.so I am special thanks Mr Anup Kumar. You are all statics equipment briefly discussed.
Very good can u send more static/rotating equipment functions &details
Alexbovas020@gmail.com
I want your guidance, and want to connect with you.
Hi Sir,
Useful piece of explanation about static equipment, please send us your blog on industrial equipment’s to my mail ID. hums1980@gmail.com
Hai Sir,
This is very useful for beginners.
Hey Mr. Anup
Keep up the excellent work, these collections and descriptions are a great way to get insight appreciate you putting your time and effort into compiling this.