Is Pipe Stress Analysis Required for Cold Water Piping Systems from Pump Stations? This is perhaps one of the most frequently asked questions in the water piping industry. Engineers often argue over this question which results in a dual answer. Some engineers say stress analysis is not required and others say it is required. In this article, we will explore the answer to the above question.
The answer to the above question is not straightforward. In general, as for water piping systems with pump stations, the difference between the maximum working temperature and installed temperature (generally 10 to 20 Degrees) is less, hence it is believed that pipe stress analysis of such water piping systems is not required. This could be valid up to a certain point if good engineering judgments are followed and the piping system is provided with sufficient flexibility.
But before we can conclude, a high level of assessment must be conducted to understand if pipe stress analysis is required. The parameters that substantiate the need for pipe stress analysis are:
How an increase in pipe temperature affects the system:
Even though it is believed that the water piping system will be near to installed temperature. Still, there could be variation due to the following reasons:
- Seasonal variation of temperature from winter to summer.
- Empty pipe exposed to sunlight.
- Full pipe exposed to sunlight.
- Temperature variation between day and night.
How external forces and displacements affect the water piping and Pump system:
Forces and displacements due to seismic, wind, and structural settlements may impose unacceptable levels of stress on the system. These stresses can not be estimated without proper pipe stress analysis.
Limitation of Pump Nozzle Loadings:
It’s difficult to estimate the nozzle loads without performing pipe stress analysis.
Support optimization:
Cold water piping systems usually have very large sizes along with large valves that result in huge structural loading. Without proper stress analysis, those loads can be overestimated and support optimization may not be possible.
Design of Expansion Bellows or Expansion Joints:
The use of rubber bellows or steel expansion joints at pump stations for water piping systems is quite common. In general pump stations are routed quite straight without much flexibility. So, these expansion joints are used to absorb thermal expansion which in turn reduces pump nozzle loads.
However, there is a concern as the subject of expansion joints is one of the most misunderstood components in the piping industry. In the usual case, simple untied bellows are used which is simply a flexible element between two flanges. It is true that they easily absorb the thermal expansion by compressing the bellow elements in all axial, lateral, angular, and torsional directions. However, a pressure thrust force is generated in untied expansion joints which must be calculated and considered in pipe stress analysis to get the actual effect. This pressure thrust force will be transferred to the pumps. In some situations, the pressure thrust force, itself, will be more than the allowable pump nozzle loads.
Another option is to use a tied expansion bellows. However, even though the tie rods will take care of the pressure thrust load, they will not compress to absorb axial movement and the thermal effect will be transferred to the nozzles. So, their position has to be such that the thermal movement is lateral.
A common misconception is to use tied bellows to a pump line with a gap in the tie nut and believe that the tie rods will take care of the pressure thrust force and the gap between the tie rod nuts will help in absorbing the thermal force by compressing. But as soon as any thermal expansion occurs, the tension in the tie-rods reduces and the pressure thrust load is transferred to the nozzle. So, this has to be carefully considered.
Typical Example of a Pump Station Cold Water Piping System
Fig. 1 below shows a typical example of a water piping system pump station.
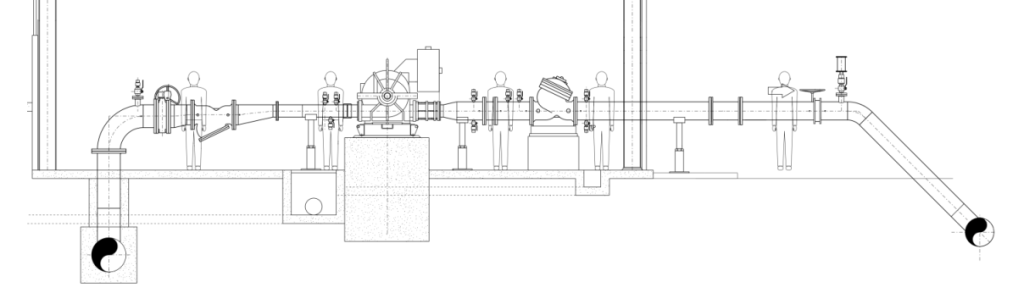
From the image, you can easily understand that the configuration does not have sufficient flexibility, and nozzle loads may increase the allowable.
From the above discussion, we can understand that pipe stress analysis for cold water lines from pump stations needs to be performed
- To compute nozzle loads.
- To study the effect of seismic and other displacements
- To design the pipe expansion joints.
- To optimize the supports.
- To study the thermal effects.
- To assure owners that the design is properly engineered.
References and further Studies
More details about the subject can be found here.