In the world of oil and gas extraction, the term “sucker rod” may not be as familiar to the general public as terms like “drilling rig” or “pipeline.” However, sucker rods play an essential role in the extraction of hydrocarbons, specifically in the operation of pumping units that are pivotal for many oil wells. This article will explain the intricacies of sucker rods, their construction, types, functions, and importance in the oil industry.
What is a Sucker Rod?
Definition
A sucker rod is a long, slender metal rod used in the oil and gas industry, primarily in beam pumping systems. It connects the surface pumping mechanism to the downhole pump, transferring the motion needed to lift oil from the reservoir to the surface.
Physical Characteristics
Sucker rods typically range from 20 to 30 feet in length and come in various diameters, usually between 5/8 inch and 1 inch. They are often made from high-strength steel alloys to withstand the harsh conditions they encounter during operation.
They are connected to form a rod string by threading them together at the ends. Manufacturers produce these rods in different grades of tensile strength to meet specific well requirements. The most common grades are C and D, while grade K offers the highest corrosion resistance. The American Petroleum Institute (API) sets the standards for these graded strengths. Fig. 1 shows examples of API sucker rods.
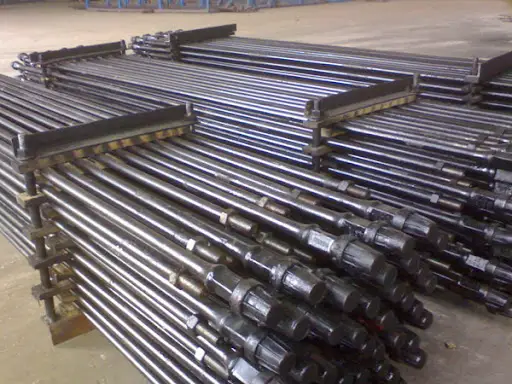
The rods connect the mechanical lift system to the downhole pump, where a plunger uses the rods to bring fluids to the surface through an oscillating motion driven by a prime mover. Operators use components like a walking beam, pitman arm, Samson post, and saddle bearing to ensure the rod string is lifted vertically at all times.
Main Functions of Sucker Rods
Sucker rods play a crucial role in the artificial lift process. This process helps bring oil or gas to the surface when natural reservoir pressure is too low. Here are the main functions:
Transmitting Power
Sucker rods transfer the up-and-down motion from the surface pumping unit to the downhole pump. This motion creates the suction needed to lift fluids to the surface.
Supporting the Downhole Pump
Sucker rods support the weight of the downhole pump. They keep it suspended at the right depth in the well, ensuring stability and controlling its vertical movement.
Withstanding High Loads
These rods are built to handle high tensile loads and torque during pumping. They must be strong, durable, and resistant to corrosion to ensure efficient and reliable oil and gas production.
The Anatomy of a Sucker Rod
Design Features
- Rod Body: The main shaft that provides structural integrity.
- Threads: Located at both ends for connecting multiple rods together or attaching to a pump.
- Rod Couplings: Used to join two rods end-to-end to achieve the desired depth.
- End Fittings: These may include various connectors designed to interface with the downhole pump or the surface unit.
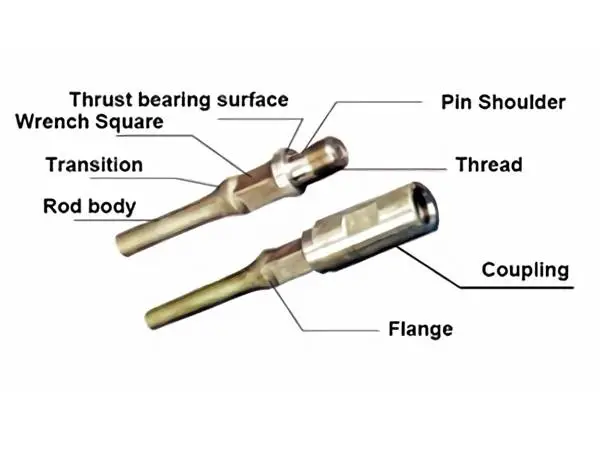
Materials
Sucker rods are primarily made from:
- Carbon Steel: Standard for most applications, providing good strength and ductility.
- Alloy Steel: Offers enhanced strength and resistance to wear, corrosion, and fatigue.
- Fiberglass: An emerging alternative for specific applications, especially in corrosive environments.
Types of Sucker Rods
In the oil and gas industry, sucker rods come in various types, each tailored to meet specific operational needs and environmental conditions. Below are some of the most common types:
Standard Rods
Standard rods are the most widely used type in oil production. Constructed from high-strength carbon or alloy steel, they are available in various sizes and lengths. These rods are typically solid, featuring a continuous body without any hollow sections. Standard rods perform reliably across a range of well conditions, making them ideal for typical oil and gas operations. These are also known as conventional sucker rods in most oil fields and are characterized by their high tensile strength and versatility.
Hollow Rods
Hollow rods feature a hollow interior, providing distinct advantages in certain well scenarios. They are lighter than standard rods, which helps reduce the load on the pumping unit and enhances overall pumping efficiency. These rods are particularly beneficial in wells with high fluid volumes, viscous fluids, or when minimizing the weight of the rod string is essential.
Continuous Rods
Continuous rods are specifically designed for use in wells with deviated or crooked boreholes. They incorporate flexible joints or couplings that allow them to bend and adapt to the wellbore’s shape without the risk of breakage. This flexibility minimizes stress and fatigue, ensuring reliable operation in challenging well environments.
Spray Metal or Fiberglass Rods
Fiberglass and spray metal rods are suitable for corrosive or high-temperature environments where traditional steel rods might fail. Spray metal rods are coated with corrosion-resistant materials, such as aluminum, to guard against chemical reactions. On the other hand, fiberglass rods are made from composite materials that provide excellent corrosion resistance and strength. These alternatives ensure durability and reliable performance in harsh well conditions.
Polished Rods
While not technically rods, polished rods play a crucial role in the rod string. They connect the downhole pump to the rod string, facilitating the transmission of reciprocating motion from the surface unit. Typically made of steel, polished rods feature a smooth, polished surface to minimize wear and friction between the rod string and the pumping unit.
Threaded Sucker Rods
These rods come with specialized threaded ends that allow for tighter and more secure connections, which are crucial for deep wells.
Special Application Sucker Rods
Certain applications require unique design features, such as sucker rods equipped with sensors to monitor downhole conditions or those designed for high-temperature environments.
How Sucker Rods Work
The Pumping Mechanism
The sucker rod is integral to the operation of a beam pump, also known as a jack pump. The mechanism works as follows:
- Drive Mechanism: The surface unit, often powered by a motor, creates a rotary motion.
- Vertical Motion: This motion is transformed into a vertical motion through a series of linkages, causing the sucker rod to move up and down.
- Pump Activation: As the sucker rod moves down, it opens the downhole pump, allowing oil to flow in. When it moves up, the pump closes, trapping the oil and lifting it to the surface.
Stroke Length and Frequency
The efficiency of a sucker rod system depends on the stroke length and frequency. The stroke length refers to the distance the rod moves during each cycle, while the frequency pertains to how many cycles occur per minute. Both factors can affect oil production rates significantly.
Importance of Sucker Rods
Operational Efficiency
Sucker rods are crucial for maintaining efficient operation in beam pumping systems. They allow for the effective lifting of oil from deep reservoirs, which is essential for maximizing production. They significantly enhance production efficiency, allowing for the economical extraction of oil and gas from low-pressure reservoirs.
Economic Impact
- Cost-Effectiveness: Sucker rods contribute to the overall efficiency of pumping systems, which can lead to lower operational costs.
- Production Rates: By ensuring consistent oil flow, sucker rods play a pivotal role in determining the economic viability of an oil well.
Reliability and Durability
Sucker rods are designed to endure extreme conditions, including high pressures, corrosive environments, extreme temperatures, and mechanical wear. Their robust construction ensures long-lasting and reliable performance, minimizing the risk of failures. Their reliability ensures that oil production can continue with minimal downtime, significantly impacting overall operational costs.
Role in Artificial Lift
Sucker rods are a critical part of the artificial lift system, helping to counteract the natural decline in well pressure over time. By transmitting reciprocating motion from the surface to the downhole pump, they create the necessary pressure differentials to lift fluids, including oil, to the surface.
Monitoring Capabilities
These rods also provide a means for monitoring downhole conditions. By analyzing the rod’s performance, including vibrations, load, and stress levels, operators can gain valuable insights into well performance and identify potential issues such as rod fatigue or pump failures.
Load Bearing and Stability
Sucker rods experience significant operational stresses, including tension, compression, and bending forces. They must maintain structural integrity under these loads. High-quality rods exhibit excellent strength, durability, and corrosion resistance, ensuring reliability and longevity in challenging downhole conditions.
Transferring Power
Sucker rods serve as a conduit for transferring mechanical power from the surface pumping unit to the downhole pump. This power is essential for lifting fluids, such as oil and gas, to the surface. As the surface unit reciprocates, it imparts an up-and-down motion to the rods, driving the downhole pump effectively.
Innovations and Technological Advancements
The sucker rod industry is continually evolving, with new materials and technologies being developed to improve performance. Innovations such as smart sucker rods equipped with sensors provide real-time data on downhole conditions, enabling operators to optimize production strategies.
Maintenance and Troubleshooting
Common Issues
While sucker rods are designed for durability, they are not immune to failure. Some common issues include:
- Rod Wear: Over time, rods can experience wear due to friction with the tubing.
- Corrosion: Particularly in water-heavy wells, corrosion can weaken sucker rods.
- Fatigue Failure: Repeated stress can lead to fatigue failure, necessitating regular inspections.
Maintenance Practices
To ensure the longevity of sucker rods and the overall pumping system, regular maintenance is crucial. This may include:
- Inspection: Routine checks for wear, corrosion, and fatigue signs.
- Lubrication: Ensuring all moving parts are adequately lubricated to minimize friction.
- Replacement: Timely replacement of worn or damaged rods to prevent failure.
Troubleshooting Techniques
When issues arise, operators can employ several troubleshooting techniques:
- Visual Inspection: Checking for visible signs of damage or wear.
- Vibration Analysis: Monitoring vibrations to identify mechanical issues.
- Performance Monitoring: Analyzing production rates to detect inconsistencies that may indicate sucker rod problems.
Conclusion
Sucker rods are a fundamental component in the oil and gas extraction process, serving as the vital link between surface pumping units and downhole pumps. Their importance cannot be overstated; they enhance operational efficiency, contribute to economic viability, and ensure the reliability of oil production.
Frequently Asked Questions
What is a sucker rod, and what is its purpose?
A sucker rod is a long, slender metal rod used in oil and gas extraction. Its primary purpose is to connect the surface pumping unit to the downhole pump, transmitting the motion needed to lift oil or gas from the reservoir to the surface.
What are the different types of sucker rods?
There are several types of sucker rods, including:
- Standard Rods: Commonly used and made of high-strength steel.
- Hollow Rods: Lighter rods with a hollow interior, suitable for high fluid volumes.
- Continuous Rods: Designed for wells with crooked boreholes, featuring flexible joints.
- Fiberglass or Spray Metal Rods: Used in corrosive or high-temperature environments.
- Polished Rods: Connect the downhole pump to the rod string, facilitating motion transfer.
Why are sucker rods important in the oil and gas industry?
Sucker rods are crucial because they enhance production efficiency, allow for the economical recovery of resources, and support various downhole pump configurations. They also help overcome the natural decline in reservoir pressure, ensuring consistent oil and gas extraction.
How do sucker rods contribute to pumping efficiency?
Sucker rods enable the effective transfer of mechanical power from the surface unit to the downhole pump. By providing a reliable means of transmitting motion, they create the necessary suction and lifting action to bring fluids to the surface efficiently.
How do sucker rods contribute to well safety?
Sucker rods play a vital role in maintaining the integrity of the downhole pump assembly. By providing stability and controlling the vertical movement, they help prevent issues like pump misalignment or failure, which can lead to unsafe conditions in the well.
Are sucker rods susceptible to wear and corrosion?
Yes, sucker rods can be susceptible to wear and corrosion, especially in harsh downhole environments. Regular inspections and maintenance are essential to detect any signs of damage and to ensure their longevity and reliability.
Can different well conditions affect the selection of sucker rods?
Absolutely. Different well conditions, such as fluid viscosity, depth, and temperature, can influence the selection of sucker rods. Operators may choose specific types of rods based on these factors to optimize performance and ensure efficient production.