Sucker rod pumps are a critical component of the oil extraction process, especially in areas where other forms of lifting may not be effective. These pumps have been utilized for decades and continue to be a vital technology in the oil and gas industry. They are also known as beam pumps or jack pumps. In this article, we will explain the mechanics of sucker rod pumps, their components, advantages, and importance.
What are Sucker Rod Pumps?
Sucker rod pumps are a type of artificial lift system used primarily in oil wells. They operate by converting rotary motion from a motor at the surface into reciprocating motion that drives a piston down the well, lifting fluids to the surface. This method is particularly effective for extracting crude oil and is widely used due to its reliability and efficiency.
They are also called beam pumps. The term “beam pump” often describes the surface unit that converts rotary motion into reciprocating motion, while “sucker rod pump” emphasizes the rods used to connect the surface unit to the pump assembly down in the well.
Fig. 1 below shows a simplistic sucker rod pump diagram.
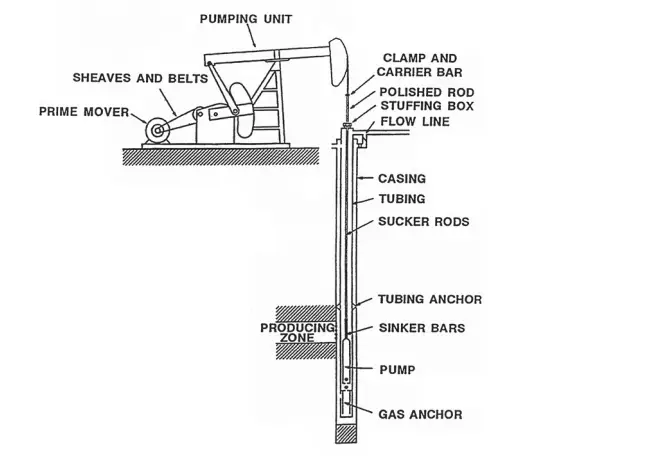
The invention of the sucker rod pump dates back to the early 19th century. Originally developed in the United States, these pumps emerged as a solution to the challenges of lifting oil from deeper wells. Over time, advancements in materials and engineering have enhanced their performance, leading to the sophisticated designs we see today.
Components of Sucker Rod Pumps
A sucker rod pump consists of several key components, each serving a distinct purpose. Understanding these parts is essential for grasping how the pump operates.
Sucker Rods
Sucker rods are long, slender steel rods that connect the surface drive mechanism to the pump assembly located in the well. They are typically made from high-strength steel to withstand the tension and bending forces encountered during operation.
Pump Barrel
The pump barrel is a cylindrical casing that houses the pump components. It is designed to withstand high pressures and is usually made from steel or other durable materials. The barrel contains the plunger and the valves, which regulate fluid flow.
Plunger
The plunger is a cylindrical piece that moves up and down within the pump barrel. As it moves, it creates a suction effect that draws fluid into the pump. The size and design of the plunger can vary depending on the specific application and well conditions.
Standing Valve and Traveling Valve
These valves control the flow of fluid within the pump. The standing valve is located at the bottom of the pump and prevents fluid from flowing back down the well when the plunger moves upward. The traveling valve, located at the plunger’s end, opens to allow fluid in during the downward stroke and closes to seal the fluid during the upward stroke.
Drive Mechanism
The drive mechanism, usually located at the surface, converts the rotational motion from an electric or diesel motor into the vertical motion needed to operate the sucker rod. This mechanism can be a simple gear reduction or a more complex system, depending on the specific application. Refer to Fig. 2 and Fig. 3 which explain the components of a beam pump.
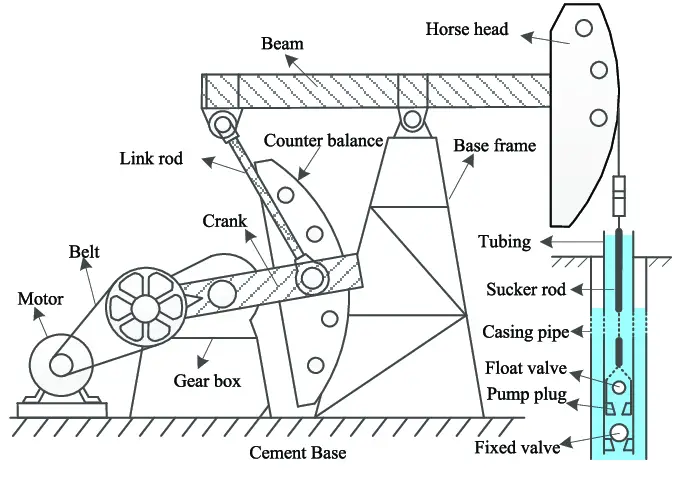
How Sucker Rod Pumps Work
The operation of a sucker rod pump can be broken down into a series of steps:
- Rotational Motion: The motor at the surface generates rotary motion, which is transmitted to the sucker rods.
- Reciprocating Motion: This rotary motion is converted into vertical motion by the drive mechanism, causing the sucker rods to move up and down.
- Suction Phase: During the downward stroke, the traveling valve opens, allowing oil to enter the pump barrel from the well.
- Compression Phase: As the plunger moves upward, the traveling valve closes, and the standing valve opens, allowing the oil to flow up to the surface.
- Discharge: The oil is lifted to the surface through a production tubing string, where it can be collected and transported for processing.
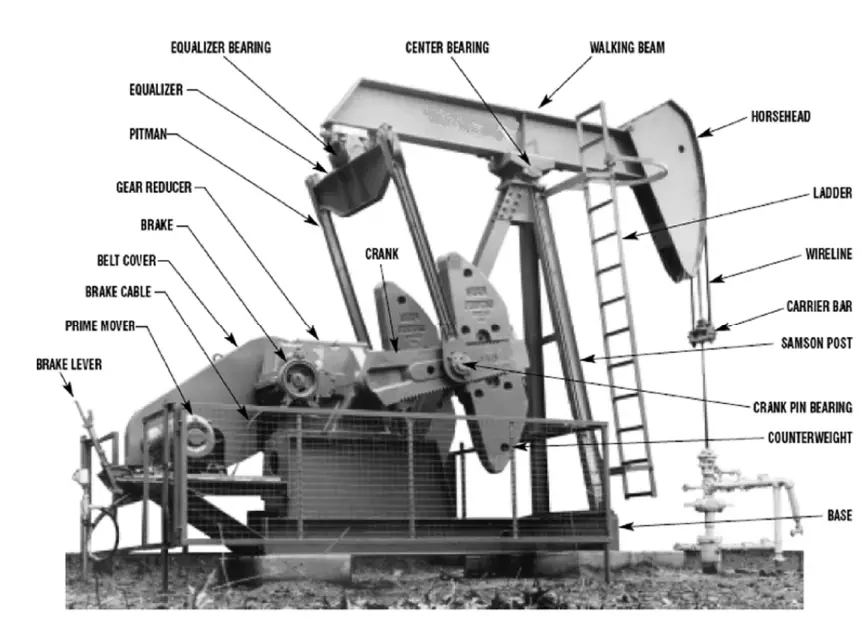
Advantages of Beam Pumps
Sucker rod pumps offer several advantages that make them a popular choice in the oil industry:
- Reliability: These pumps have a proven track record of reliability and can operate for extended periods with minimal downtime.
- Cost-Effective: Compared to other artificial lift methods, sucker rod pumps can be more economical, especially in medium to low-flow applications.
- Versatility: Sucker rod pumps can be adapted to a wide range of well conditions and fluid types, making them suitable for various applications.
- Simple Design: The straightforward design of sucker rod pumps facilitates easy maintenance and repair, reducing operational costs.
- Low Power Requirement: They generally require less energy compared to other artificial lift systems, leading to lower operating costs.
Challenges in Sucker Rod Pump Operations
While sucker rod pumps have many advantages, they are not without challenges:
- Mechanical Wear: The constant motion can lead to wear and tear on components, requiring regular maintenance and replacement.
- Fluid Type Limitations: Sucker rod pumps may struggle with highly viscous fluids or fluids with high gas content, which can impact performance.
- Well Depth: As the depth of the well increases, the efficiency of the sucker rod pump may decrease due to friction and other factors.
- Temperature Sensitivity: Extreme temperatures can affect the performance of the pump and its components, necessitating specialized materials or designs.
- Installation Complexity: Proper installation and alignment are critical for optimal performance, and errors can lead to significant inefficiencies.
Codes and Standards for Beam Pumps
The design, manufacturing, and operation of beam pumps (or sucker rod pumps) are governed by various codes and standards to ensure safety, reliability, and efficiency. However, the following two API standards are the most widely used standards for Sucker rod pumps:
- API Spec 11B: This specification covers the design and manufacturing of sucker rod pumps and associated components.
- API RP 11G: Provides guidelines for the design and installation of sucker rod pumping systems.
- API 11E: Specification of Beam Pump unit.
Beam Pump System Considerations
- Beam pumps are suitable for lower-volume stripper wells and have proven to be cost-effective. Operators are usually familiar with these simple systems, making them easier to manage, even for less experienced personnel. Beam pumps can efficiently handle a wide range of production rates and depths, and they have a high salvage value. With proper care, surface units and gearboxes can last over 30 years if not overloaded.
- Beam systems are effective for lifting moderate volumes from shallow wells and small volumes from intermediate depths. They can lift up to 1,000 barrels per day (BPD) from about 7,000 feet deep and around 200 BPD from about 14,000 feet deep, though special rods may be required. Typically, they lift lower rates from depths around 7,000 feet, and few operate below 10,000 feet.
- Standards Compliance: Many parts of the beam system meet standards set by the American Petroleum Institute (API). Numerous manufacturers produce compatible components, though some non-API certified parts are available, such as downhole pumps of varying sizes.
- Cyclic Fatigue: The sucker rod string experiences cyclic fatigue loads. Rods must be protected from corrosion and damage, as corrosion can lead to early failures. High-strength and fiberglass rods are options for increased durability.
- Well Compatibility: Beam systems are often not suitable for deviated wells, even with protective devices. However, wells with smooth profiles and low dogleg severity may still work well, even at angles up to 30-40 degrees. Special devices like rod protectors can help, but high glass content can increase wear on tubing.
- Fluid Handling: Beam systems have limitations when dealing with sand-laden fluids, though special filters can be used. Some pumps are designed to manage sand effectively.
- Paraffin and Scale Issues: Paraffin and scale can disrupt operations. Special wiper systems and hot treatments help manage paraffin, while hard scales can lead to equipment failure.
- Gas Separation: Free gas entering the pump can reduce production and cause problems. Proper gas separation techniques should be used, and pumps should be filled with liquid to minimize gas interference. Setting the pump intake below gas zones is crucial for efficiency.
- Stuffing Box Leaks: A common issue with beam pumping systems is leaks at the polished rod stuffing box. Special pollution-free stuffing boxes can help, and practices like avoiding over-tightening and ensuring unit alignment are important.
- Pump Efficiency: Attempting to produce more liquid than the reservoir can supply can lead to incomplete pump filling, causing damage and reducing efficiency. Adjustments in pumping speed and stroke length can help match pump capacity to production potential.
- Pump-off Control (POC): POC systems can detect when the pump is not fully filled and will stop pumping to allow fluid to enter the well. Simple timing adjustments can optimize the pump’s performance, ensuring it operates efficiently.
To conclude, sucker rod pumps remain a cornerstone of oil extraction technology, providing a reliable and cost-effective means of lifting fluids from the earth. Their straightforward design, adaptability, and proven performance have solidified their role in the oil and gas industry. However, challenges such as mechanical wear, fluid limitations, and depth restrictions require careful consideration and proactive maintenance.