Thermal relief valves are also known as thermal safety valves, temperature relief valves, or thermal expansion relief valves. It is a safety device employed in liquid piping and pipeline systems to protect the equipment and system. When the thermal expansion of a liquid creates excessive pressure inside a closed system, the thermal relief valve pops up to release some fluid and bring down the pressure back to an acceptable limit. In general, when liquid heats up, it expands a little. When the temperature increase is quite high, the volume change of the liquid, though not by a large percentage, may increase the system pressure. To protect against this overpressure situation and to avoid explosion, thermal relief valves prove to be a good device.
What is a Thermal Relief Valve?
A thermal relief valve is a type of safety valve designed to release excess pressure from a system when it is subjected to temperature-induced expansion. When fluids or gases are heated, they expand, potentially leading to an increase in pressure that could exceed the system’s design limits. Thermal relief valves are engineered to mitigate this risk by allowing the excess pressure to escape, thus preventing potential damage or failure of the equipment. Fig. 1 below shows some typical thermal relief valves that are used in various industries.
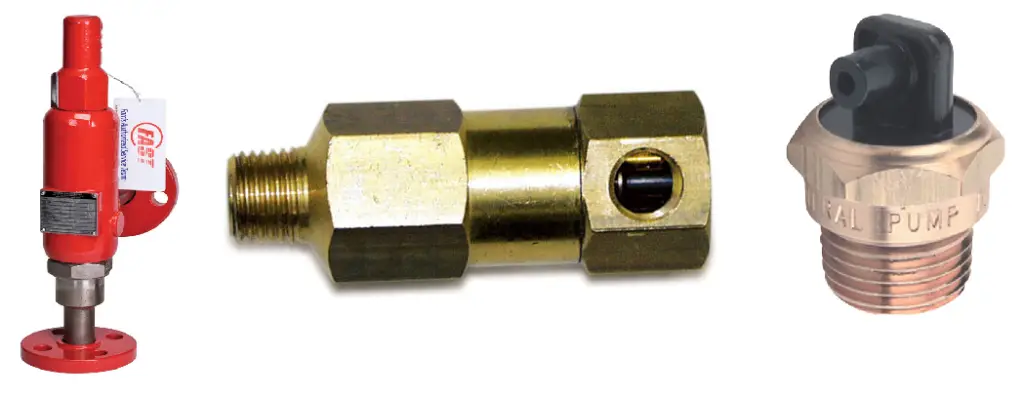
Design Consideration for Thermal Relief Valves
The common size for thermal relief valves is relatively small. The usual size of thermal safety valves used for piping and pipeline systems are generally (1”x1”) or (¾”x1”) with a flanged end having a minimum orifice area of 0.110 in2.
Depending on the design code requirements a lifting device may or may not be required for thermal relief valves. In general, for air, hot water, or steam services with temperatures in excess of 600C lifting devices are normally specified.
Thermal relief valves are normally not vented directly to the environment. So, some sort of containment method is always suggested.
Thermal relief valves are usually designed based on API 526 or EN 14597 codes.
Applications of Thermal Relief Valves
Thermal safety valves are used for protection in case of excessive temperature for liquid applications in long pipes/pipelines exposed to the environment (sunlight), closed vessels, water heater applications, cooling water return side of heat exchangers between isolation valves, and pumps that recirculate water where heat buildup can be a problem. Piping in transport pipelines or storage areas, that will be regularly blocked during normal operation and can have a pressure rise due to solar heating or heat tracing calls for TRV installation.
The principal benefit of using a thermal relief valve in pump systems is that it allows an operator to run the unit in a bypass mode for an extended period, reducing the chances of premature seal wear on the high-pressure pump.
In general, thermal expansion relief valves are not intended for:
- Process plant piping
- Two-phase flow lines
- Storage or transport piping sections that are not normally shut in for operational or emergency purposes
- Systems that are not fully liquid filled, i.e. less than 95% liquid filled.
Thermal relief valves are employed in a variety of industries and applications. Some common areas where TRVs are used include:
- Hydraulic Systems: In hydraulic systems, TRVs protect pumps, hoses, and other components from pressure spikes caused by thermal expansion. They ensure that the hydraulic fluid is maintained within safe pressure limits.
- Compressed Air Systems: In air compressors and pneumatic systems, TRVs prevent pressure build-up due to temperature increases, safeguarding the compressor and associated equipment.
- Boilers and Pressure Vessels: TRVs are crucial in boilers and pressure vessels to release excess pressure that may build up due to thermal expansion. This prevents catastrophic failures and ensures safe operation.
- Chemical Processing: In chemical processing plants, where reactions can cause significant temperature and pressure changes, TRVs help maintain safe operating conditions by relieving excess pressure.
Working Principle of Thermal Relief Valves
TRV works mostly similarly to pressure relief valves. Even though the name is a thermal safety valve, the pressure increase is the main cause for its working. Under normal operation, the TRV remains closed by the spring force. When the force due to fluid expansion is great enough and exceeds the internal spring force, the valve pops up. Once the pressure reduces, the spring force again closes the thermal relief valve in a position to work smoothly.
Thermal safety valves work in an automatic manner and when the temperature falls below the set point it automatically reset.
Thermal relief valves are usually placed in a remote location without easy access. Also, normally temperature sensors, processors, or solenoid-type sensors are not used to control TRV systems. So, thermal expansion relief valves must be designed to be durable and work properly in case of system failure.
The basic mechanism of a TRV involves a spring-loaded valve that remains closed during normal operating conditions. When the system experiences a temperature-induced pressure rise, the valve opens to release excess pressure, thus protecting the system from damage.
- Thermal Expansion: As temperatures increase, the fluid or gas inside a closed system expands. This expansion raises the internal pressure.
- Pressure Threshold: The TRV is set to open at a specific pressure threshold. This threshold is usually predetermined based on the system’s maximum allowable working pressure.
- Valve Actuation: Once the internal pressure exceeds the threshold, the TRV opens, allowing the excess fluid or gas to escape. This reduces the pressure back to a safer level.
- Valve Closure: After the pressure decreases to a safe level, the TRV closes, and the system resumes normal operation.
Types of Thermal Relief Valves
There are three main types of thermal relief valves as mentioned below:
- Spring-Loaded Thermal Relief Valves
- Pilot-Operated Thermal Relief Valves
- Balanced Bellows Thermal Relief Valves
1. Spring-Loaded Thermal Relief Valves
Description:
- Mechanism: Utilizes a spring to keep the valve closed until the pressure exceeds a set point. When the pressure rises due to thermal expansion, it overcomes the spring force, causing the valve to open and release excess pressure.
- Operation: The spring is calibrated to the pressure at which the valve should open. When the pressure increases beyond this point, the valve opens to relieve the excess pressure.
Advantages:
- Simplicity: Straightforward design and operation.
- Cost-Effective: Generally less expensive compared to more complex valve types.
Applications:
- Commonly used in hydraulic systems, compressed air systems, and other systems where thermal expansion is a primary concern.
2. Pilot-Operated Thermal Relief Valves
Description:
- Mechanism: Features a pilot valve that controls the main relief valve. The pilot valve responds to pressure changes and opens or closes the main valve accordingly.
- Operation: The pilot valve operates at a lower pressure and controls the main valve to open at a higher pressure set point, providing precise control over the pressure relief process.
Advantages:
- Precision: Offers more precise control of pressure relief.
- High-Pressure Applications: Suitable for systems requiring accurate pressure control and handling higher pressures.
Applications:
- Used in applications with high-pressure conditions or where precise pressure control is essential, such as in large-scale industrial systems.
3. Balanced Bellows Thermal Relief Valves
Description:
- Mechanism: Includes a bellows element that helps to balance the pressure on both sides of the valve seat, reducing the effects of varying pressures and temperatures on the valve operation.
- Operation: The bellows maintain a constant force on the valve seat, allowing it to open and close smoothly despite fluctuations in system pressure.
Advantages:
- Stability: Provides stable operation under varying pressure and temperature conditions.
- Reduced Sensitivity: Less affected by changes in the system’s pressure and temperature.
Applications:
- Used in applications where pressure and temperature fluctuations are significant, such as in chemical processing or high-temperature systems.
Thermal Relief Valve Symbols
In P&IDs, the thermal relief valve symbol is provided as per Fig. 2 shown below:
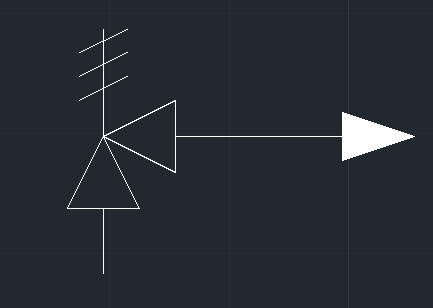
The Importance of Thermal Relief Valves
Thermal relief valves (TRVs) are crucial components in various fluid and gas systems, serving essential roles in protecting equipment, ensuring safety, and optimizing performance. Here’s a detailed look at why thermal relief valves are important, using the key data provided:
1. Protection Against Catastrophic Failure
Thermal relief valves are crucial for protecting the integrity of systems from overpressure caused by temperature changes.
- Prevention of Catastrophic Failures: When a system experiences a rise in temperature, the expansion of fluids or gases can lead to a significant increase in pressure. Without a TRV, this overpressure could exceed the design limits of the system, potentially resulting in catastrophic failures such as ruptures or explosions. By opening at a predetermined pressure, TRVs release the excess pressure, thus preventing such severe outcomes.
- Cost Avoidance: Catastrophic failures often result in costly repairs or complete replacements of damaged equipment. By maintaining pressure within safe limits, thermal relief valves help avoid these significant financial burdens.
- Safety Hazards Prevention: Overpressure situations can pose serious safety hazards to personnel working with or near the affected systems. By preventing overpressure, TRVs contribute to a safer working environment and help avoid injuries or fatalities.
2. Regulatory Compliance
Thermal relief valves are often required by industry standards and regulations, ensuring safety and legal compliance.
- Adherence to Standards: Organizations such as the American Society of Mechanical Engineers (ASME) and the Occupational Safety and Health Administration (OSHA) mandate the use of thermal relief valves in specific applications. Compliance with these standards is not only crucial for legal reasons but also for ensuring the safety of personnel and the protection of the environment.
- Avoidance of Legal Liabilities: Failing to comply with regulatory requirements can result in legal liabilities, fines, or penalties. By installing and maintaining TRVs as required, organizations can avoid such legal issues and ensure that their systems meet safety and operational standards.
3. System Performance and Efficiency
Thermal relief valves contribute to the optimization of system performance and operational efficiency.
- Energy Waste Reduction: By releasing excess pressure, TRVs help prevent energy waste associated with overpressure conditions. This contributes to a more efficient operation of the system, as it avoids unnecessary strain and energy loss.
- Reduced Wear and Tear: Excessive pressure can accelerate wear and tear on system components, leading to more frequent maintenance and shorter equipment life. TRVs help mitigate this issue by controlling pressure levels, thus extending the life of the components and reducing maintenance needs.
- Improved Overall Performance: Maintaining optimal pressure levels helps ensure that the system operates efficiently and effectively. This can lead to enhanced overall system performance and reliability.
Difference between TRV and PRV
Even though the working mechanisms of both thermal relief valves (TRV) and Pressure relief valves (PRV) are almost similar, they have some differences.
- A TRV is usually small, whereas a PRV can be of big sizes.
- TRV acts when overpressure occurs because of temperature increases and relieves a small quantity of fluid, whereas PRV is sized to protect from any kind of overpressure and usually releases large quantities of fluid.
- Safety is the main purpose of both TRV and PRV.
Thermal relief valves are vital components in various fluid systems, providing essential protection against pressure buildups caused by thermal expansion. Understanding their function, types, applications, and maintenance is crucial for anyone involved in the design, operation, or maintenance of hydraulic systems, compressors, or pressure vessels.
Dear Anup kumar Dey,
I was reading your blog regarding the TSV & PSV was very useful to me. Thank you so much for this block to under stand the TSV & PSV. Will please share this type of simplified technical document to my email sundar.ak@gmail.com
Thanks & Regards,
K. Sundar
Required Thermal Relief Valves
please send the quotation
Size: 1/2″ x 1/2″ to 2” x 2″
1/2 ” Dia Thermal pressure valves
Hi Anoop
Thanks for sharing your knowledge on the web. This blog does help in understading the difference between a PRV and TRV.
Cheers,
Ajit
Hello Anup,
I am a reader of www.whatispiping.com, I was wondering if you are so kind to help me understand the minimum pipe length/volume that a thermal relive valve is needed.
In LNG facilities, I have seen where the volume of trapped cryogenic liquids (trapped between two block valves) is NOT large, there is NO TRV installed. I was wondering in these cases (where TRV does not exist), how thermal expansion of cryogenic liquids are accommodated?
I appreciate your time and looking forward to hearing from you.
Regards,
Ebrahim
Can you share sizing calculation for Thermal relief valve installed on piping ?? I am not sure how to calculate flow rate ‘Q’ required in API 520 Sizing calculation formula.
Wow, this article provided a fresh perspective on the topic! I appreciate the thorough research and the clear way the information was presented. It’s always great to learn something new. Thank you for sharing!
Wow, this article provided a fresh perspective on the topic! I appreciate the thorough research and the clear way the information was presented. It’s always great to learn something new. Thank you for sharing.
Another fantastic read on how technology is shaping the future of industry!
Good Day Sir,
I’m new to the oil refining business and am working on a project that requires a thermal relief valve. I was wondering your thoughts on tying the piping into that valve into the side of a pipe line rather than coming up off the top. I would have that piping 90°up off of the side and the TRV would be placed after a small gate valve with the TRV oriented vertically. Do you think that is acceptable or should it always come of the top of the pipe run? Thank you for your time and consideration.
Sincerely,
Andrew Edwards