Atmospheric Storage Tanks are an integral part of any refinery or process plant as they are used to store fluids for various purposes for short or long duration. Feedstock tanks and product tanks provide buffer capacity between process plants, which are generally in continuous operation, and the supply/dispatch of feedstock/products, which are batch operations in general. Intermediate tankage is provided where there is a requirement to buffer the flow of an intermediate from one process unit to another. Component tanks are the intermediate tanks between the process units and the blenders. These tanks are necessary to de-couple blender operation from process unit operation, in order to give the blender sufficient degrees of freedom to blend the product optimally.
Swing Tanks
In determining the requirements for feedstock/product, intermediate and component tankage, it may become apparent that some of the tanks will only be in service for a relatively small proportion of the time. In these circumstances, there is potential for specifying/designing tank(s) for more than one duty. Reducing the number of tanks can have a significant impact on capital costs. Such multi-purpose tanks are often referred to as “swing tanks”.
Tanks are frequently used at the start and finish of a process and it is, therefore, necessary to know the quantity and quality of the contents. Most fixed roof tanks are calibrated after construction, and a dip hole is frequently fitted to the top of the tank so that the depth of the liquid within can be measured accurately with dip tape. This dip hole is often used to collect samples using a specialist container that can be opened once it has reached the required depth.
Modern-level instrumentation can be very accurate and has in many cases replaced the need for regular tank dipping. However, it is good practice to retain the dip pipe both as a means of checking the level instruments and as a means of getting samples. Storage tanks can be of the following types:
Roofless Tanks
This type of tank (Fig. 1) is normally used for water services including fire water, cooling water and service water. Potable water will normally be stored in a tank with a roof. Although open-top tanks are sometimes made of steel, it is common to construct them from concrete, or glass-reinforced plastic (GRP). The main advantage of a roofless tank is its low cost.
Fixed Roof Tanks
Fixed roof tanks (Fig. 1) usually make up the majority of tanks used in a typical tank farm. The tanks are generally used for low vapour pressure materials rather than higher vapour pressure materials, as these would tend to give high VOC emissions during tank breathing and could generate an explosive mixture in the vapour space.
Fixed roof tanks are used typically for gas oil, fuel oil, and sometimes for kerosene in cold locations.
Tanks are very good settling vessels and any water or similar liquid that is not completely removed by the processing unit is likely to settle in downstream tanks. This can affect the material selection for the tank, the provision of drains, or the provision of mixers if it is necessary to keep the two phases in suspension.
Floating Roof Tanks
Floating roof tanks are used for higher vapour pressure materials as they reduce both evaporative losses and the concentration of explosive mixtures. However, it is essential that the vapour pressure can never reach atmospheric pressure.
The design of the floating roof can be pan, pontoon, or double skin. However, regardless of type, all floating roofs need to have a seal. These are to minimise the losses from the tanks and to prevent the ingress of rainwater into the tank. Most modern tanks are fitted with double seals to reduce VOC emissions. A scraper seal is fitted if the tank contents are prone to adhering to the tank walls. Floating roof tanks are used typically for crude oil, naphtha, gasoline, and kerosene in tropical locations.
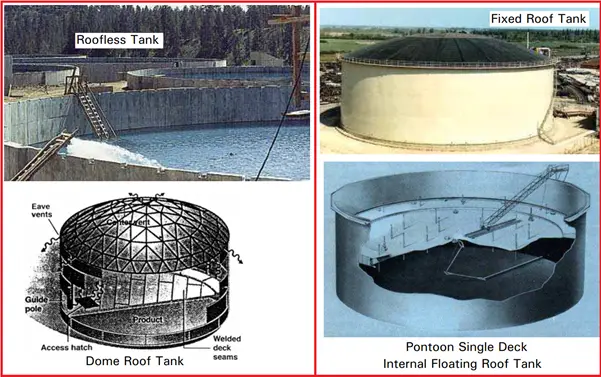
Internal Floating Roof Tanks
Internal floating roof tanks (Fig. 1) are becoming of increased importance as a result of tighter environmental requirements. They are more expensive than conventional fixed or floating roof tanks, but they do offer a number of advantages.
- They can be used in place of a conventional floating roof tank where there is a need to exclude the possibility of air contamination. In this case, an internal floating roof tank can be nitrogen blanketed.
- They can be used for floating roof applications where there are heavy snowfalls. Snow can sink a conventional floating roof. Tanks built for this reason may be provided with ample ventilation apertures in the sidewalls just below the roof.
- They can be used where the exclusion of water is very important. Rainwater has been known to find its way around roof seals and leak rainwater into the tank. This type of tank is used for Jet Fuel where water should be eliminated from the product.
- They can be used to reduce VOC emissions since the vapour space above the internal roof can be vented via emission control equipment.
There are some disadvantages to IFRTs in addition to increased cost.
- The vapour space above the internal roof, unless specially ventilated, will be prone to the production of explosive mixtures. This often has to be blanketed.
- In practice, there are likely to be limitations in tank size (maximum diameter approximately 40 m ) resulting in an increase in the number of tanks.
- In order to work in association with other facilities like vapour removal units, the tanks may need to be designed for slightly higher pressures
Dome Roof Tanks
Sometimes there is a need to store materials, such as very light naphthas, that have vapour pressures in excess of atmospheric pressure but are not sufficiently high to justify a sphere or a bullet.
API 620 allows for such instances by permitting designs up to a design pressure of 15 PSIG. Such vessels can have a variety of shapes, but the most commonly employed is the dome-roofed tank. A pressurised dome roof is always more costly to fabricate than a coned one. This is usually due to the major additional cost of the foundations. The additional pressure is likely to push out the flat floor, and a special foundation is usually required to stop the tank from deforming. Over/under pressure protection for such tanks is also more like those facilities provided for pressure vessels.
There are instances when tanks such as these are needed, but most installations avoid their use by ensuring that the light hydrocarbon streams involved are safely disposed of without storing them.
Design Standard for Atmospheric Storage Tanks
Atmospheric storage tanks are essential components in various industries, storing a wide range of liquids and gases under ambient pressure. API 650: Welded Tanks for Oil Storage is the most widely used design standard for Atmospheric storage tanks.
API 650 covers the design and construction of welded, cylindrical, atmospheric tanks. It provides guidelines on material selection, tank design, and testing to ensure the tanks can safely handle the intended contents. Key aspects include:
- Material Specifications: Steel grades, thicknesses, and welding practices.
- Design Requirements: Minimum requirements for tank strength, stability, and safety features.
- Inspection and Testing: Procedures for ensuring tanks meet performance standards and are free of defects.
Differences Between Fixed Roof Tank and Floating Roof Tanks
The major differences between a fixed roof tank and a floating roof tank are tabulated below:
Feature | Fixed Roof Tanks | Floating Roof Tanks |
---|---|---|
Roof Type | Fixed, non-movable roof | Roof that moves up and down with the liquid level |
Construction | Permanent, rigid structure | Floating structure that adjusts with liquid level |
Applications | Used for a wide range of liquids including water, chemicals, and oil | Primarily used for volatile liquids like gasoline and crude oil |
Ventilation | Usually requires a vent or pressure relief system | Floating roof reduces vapor space, often requires fewer vents |
Vapor Loss | Higher potential for vapor loss and emissions | Reduced vapor loss and emissions due to reduced vapor space |
Maintenance | Easier to inspect and maintain due to fixed nature | Requires careful inspection and maintenance of the floating mechanism |
Construction Cost | Generally lower due to simpler design | Higher cost due to complexity of the floating roof system |
Operational Cost | Potentially higher due to greater vapor losses | Lower operational costs due to reduced vapor emissions |
Sealing Efficiency | Less efficient in sealing against vapors | Highly efficient in sealing against vapors due to the floating roof |
Safety Considerations | More prone to atmospheric contamination and fire hazards | Better at minimizing fire hazards due to reduced vapor space |
Flexibility in Size | Suitable for various sizes and volumes | Typically used for larger tanks with high volatility liquids |
Temperature Control | May require additional measures for temperature control | Floating roof can help with temperature control by minimizing vapor space |
Environmental Impact | Higher potential for environmental impact due to vapor loss | Lower environmental impact due to reduced vapor emissions |
Leak Detection | Easier to detect leaks at the roof level | More complex due to the floating roof mechanism and need for specialized detection |
Additional Notes:
- Fixed Roof Tanks: These are straightforward in design and construction, making them less costly initially. However, they may incur higher long-term operational costs due to greater vapor losses and the need for more frequent ventilation and environmental controls.
- Floating Roof Tanks: These are more complex and expensive to build and maintain but are advantageous for storing volatile liquids. The floating roof helps minimize vapor loss, reduces environmental impact, and often improves safety by limiting the amount of vapor space that could potentially ignite.
Design Pressure
Although atmospheric storage tanks are intended to operate at about atmospheric pressure, in practice they do have a design pressure, even if it is only a few millibar gauges.
Tank Breathing
When the gas enters or leaves a vapour space in a liquid storage tank, the tank is said to be breathing. Breathing can occur from a number of causes.
- A rise or fall in the liquid level.
- A rise or fall in the tank temperature (consider the effect of a rain shower on a tank that has been exposed to the sun all day).
- The escape of gases coming out of solution, or even the ingress of gases being absorbed such as vapour breakthrough.
- The escape of gases entering the tank from other sources.
The vents on the tank have to be large enough to pass all coincident vapour flow, both in-breathing and out. API RP 2000 forms the basis for establishing tank breathing rates.
The type of vent to be used depends on the pressure to be held in the tank. If the tank is to be held as close as possible to atmospheric pressure, and air ingress is acceptable, then a covered vent (to keep out birds etc.) will be used. The only pressure generated will be from the frictional resistance of the gas entering or leaving.
If the tank is to be blanketed, then it will probably need to operate at a slightly higher pressure so that sufficient margins can be allowed between in-breathing and out-breathing for the blanketing controls to work. It would be normal to expect a blanketed tank to be fitted with a pressure/vacuum valve (PVV) and have a controlled supply of blanket gas. Under normal operation, in-breathing by the tank will cause the blanket gas to be introduced. Should it fail, then the vacuum facility will permit air ingress on the grounds that it is better to take in the air than to collapse the tank. Out-breathing causes the pressure section of the PVV to operate. The control signal for the letdown control of the blanket gas must come directly from the tank, as the frictional pressure drop from the controller to the tank is likely to be significant in comparison with the set pressure.
When out-breathing is required to pass to some kind of treatment facility, then clearly higher pressures are required as a driving force. In these circumstances, it is normal to provide PVVs with flanged outlets.
Inerting
Fixed roof tanks and internal floating roof tanks normally have a vapour space that can accumulate volatile gases and/or contain air. If explosive mixtures can be produced in the vapour space, or if it is necessary to exclude air for reasons of contamination, then these tanks will require a gas blanket. In most cases, the most appropriate blanketing gas will be nitrogen. However, occasionally fuel gas may be used. When fuel gas is to be used, it is essential to ensure there are no inadvertent releases to the atmosphere, and that any PVVs discharge to an appropriate disposal system.
Very Helpful information. Thanks bro.
I am looking to stop the N2 blanketing of an IFR tank which is storing Naphtha. Now from Naphtha contamination point of view or contact with air point of view there is no concern at the downstream Naphtha user end, however, there is a safety concern of explosive mixture between the fixed and floating roof may get formed if i allow air instead of N2 above the floating roof. Can you suggest ways to take care of my concern.
Thanks
If the nitrogen seal of the storage tank is stopped, it is necessary to increase the ventilation window on the tank wall, enhance the air dilution ability of the gas phase space inside the tank, and reduce the oil and gas concentration in the gas phase space below LEL.