A Heat Exchanger is a mechanical device that is used to exchange heat between fluids. The fluid used for heat transfer operation can be in the gas or liquid phase as per the availability. The number of fluids used for heat transfer operation maybe two or more. A properly designed heat exchanger can be used for both heating & cooling operations.
Heat exchangers are widely used in chemical plants, refrigeration and air conditioning systems, petrochemical facilities, food and beverage industries, and nuclear and power industries. As the heat exchanger does not have any rotating component, they are known as static equipment. Most of the heat exchangers are designed based on ASME BPVC Sec VIII codes or TEMA guidelines.
Heat exchangers are usually manufactured from materials that are heat-resistant. Some of the most common heat exchanger materials are Carbon Steel, Stainless Steel, Alloy Steel, Aluminum, Copper, Titanium, DSS, Hastelloy, Ceramics, Composite Plastics, etc. In this article, we’ll learn about the Classification of Heat Exchangers.
Classification of Heat Exchangers
Classification of Heat exchangers is dependent on several factors such as
- Flow configuration,
- Pass configuration
- Heat transfer mechanism,
- Construction method,
- Function and application,
- Fluid phases, etc.
A. Heat Exchanger Types based on the Flow Configuration
Flow configuration simply refers to the arrangement (path) provided within the heat exchanger. This is an indication of the fluid traveling direction of the heat exchanger. Flow configuration in heat exchangers consists of the following four types:
- Co-Current Flow
- Counter Current Flow
- Cross Flow, and
- Hybrid Flow
Co-Current Flow Heat Exchangers:
Co-Current flow Heat exchangers are also known as parallel flow heat exchangers. In this type of heat exchanger, the flow of fluid streams is parallel to each other and the operating fluids are moving in the same direction. Co-Current flow heat exchangers provide thermal uniformity across heat exchanger walls and usually have lower efficiency.
Counter Current Flow Heat Exchangers:
The heat exchangers where the direction of the fluid is parallel but opposite (divergent) to the other are known as counter-current type heat exchangers. They usually have the highest heat exchange and greatest temperature change.
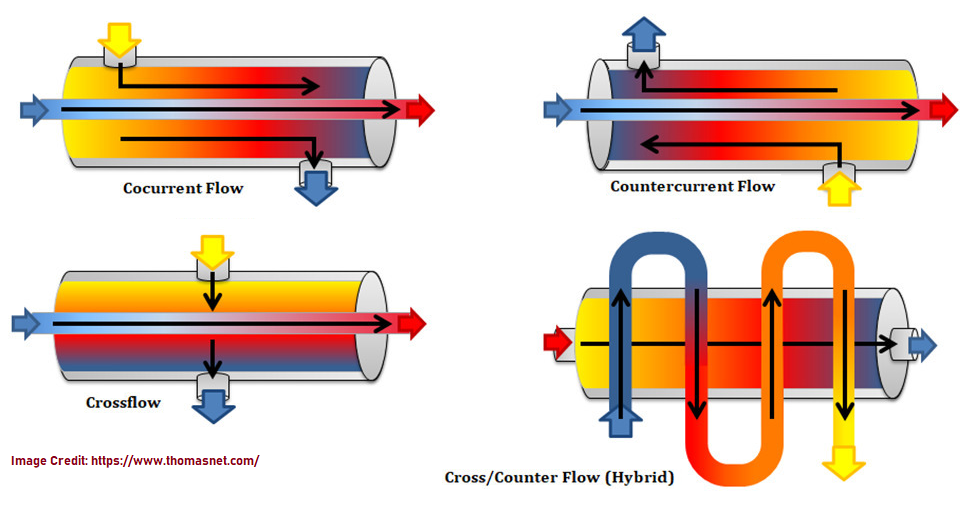
Cross Flow Heat Exchangers:
When the flow of the fluids inside the heat exchanger is perpendicular (formation of right angle ~ 90° while flowing) to each other, they are called cross-flow heat exchangers. In terms of efficiency, a cross-flow heat exchanger gives better efficiency than the parallel flow configuration type heat exchanger.
Hybrid Flow Type Heat Exchanger:
Hybrid flow configuration uses a combination of the above-mentioned flow configurations, i.e. Co-Current, Countercurrent, or Cross Flow any of the mentioned combinations may be used within the single process. To accommodate the limitations of a single type of heat exchanger, this type of heat exchanger is produced.
B. Types of Heat Exchangers based on the heat transfer mechanism
According to the heat transfer process, heat exchangers are classified into direct contact type heat exchangers & indirect contact type exchangers.
Direct contact type heat exchanger:
This type of heat exchanger does not contain a wall tube for different fluids for the heat transfer process. The fluids come into direct contact to exchange heat between each other & exit via their respective outlet nozzles or line. Due to direct heat exchange, very close temperatures can be attained. Examples: Direct contact type process utilizes by the cooling tower, desuperheater, and Scrubber.
Indirect contact type heat exchangers:
This type involves the heat exchange between hot & cold fluid across a construction wall (The separating wall used is generally a tube/ pipe/vessel). As the wall separates the fluid, they do not mix during the whole heat transfer process.
Indirect contact type heat exchangers are further classified into
- Direct transfer type,
- Storage Type, and
- Fluidized Bed type.
Direct Transfer Type heat exchangers: This type of heat exchanger consist of a separate path for each fluid including their respective passes. The heat transfer is based on the temperature gradient (difference). Direct transfer type heat exchangers are also known as recuperators. Continuous heat exchange occurs from the hot fluid to the cold fluid.
Examples of direct transfer type heat exchangers are Shell & Tube heat Exchangers (STHE), Plate type heat exchangers, tubular heat exchangers, and economizers used in power engineering.
Storage Type heat exchangers: This type of heat exchanger is provided with a fixed bed area across which fluid is about to pass through each bed. Hot & cold fluid passed through their beds respectively & valves at the inlet, the outlet is adjusted so that hot fluid is passed through the cooled fluid bed, same is applicable for the cold fluid which is passed through the hot fluid bed, and hence heat transfer takes place through this mechanism.
Example of Storage Type: An air preheater is a suitable example for this type of heat exchanger, ambient air taken into APH & hot fluid heated from the heater emit flue gases which need to be taken out through a stack, flue gas at high temperatures emissions give lower efficiency to the heater so the temperature of flue gas to be lowered by the ambient air whose temperature is increased at the APH Outlet, hence flue gas temperature decreases as both flue gas & ambient air simultaneously passed through each other.
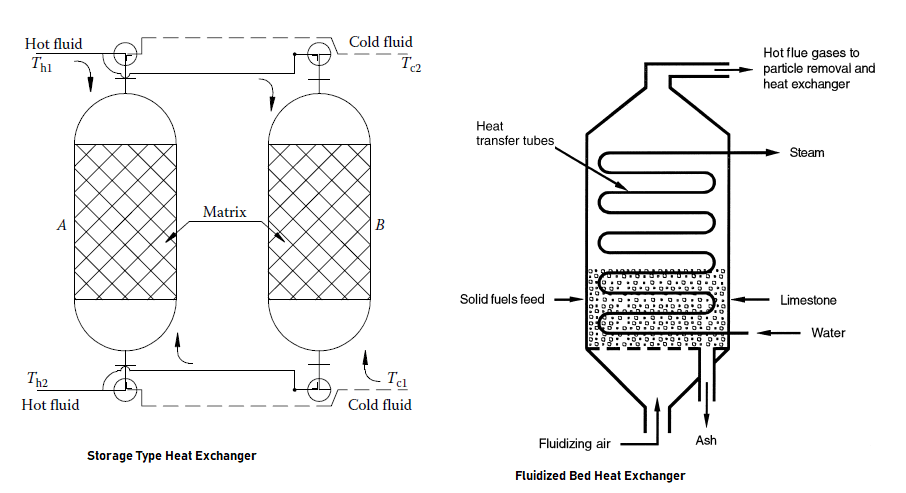
Fluidized Bed type: Fluidized bed type heat exchangers consist of two-compartment; one for hot fluid & cold air for the inlet distributor plate is placed in each section (i.e. hot gas, cold air). The bed is completely filled with alumina pallets. The hot gas causes the alumina to fall into the lower chamber which is primarily used to heat the cold air. It gets heated up from hot gas which is flowing in the upper chamber. A recirculation path or arrangement is incorporated for recycling purposes.
In the Fluidized bed heat exchanger, solid particles or pallets are placed at the bottom, at low operating fluid velocity fluid is passed through the pallet bed, high velocity causes the solid particles to float in the entire section volume as drag force of fluid is greater than the weight of fluid.
C. Heat Exchanger Types based on the pass configuration:
Depending on the pass configuration used in the heat exchangers they can be grouped into any one of the following types:
Single-pass heat exchanger: In this type of heat exchanger, the fluid can pass once through the length of the heat exchanger.
Multi-pass heat exchanger: This type of passing arrangement utilizes the U bends and the fluid moves through the heat exchanger length more than once. The design of a multipass heat exchanger involves a series of tubes.
D. Types of Heat Exchangers based on the available Fluid phases:
Depending on the fluid media phases involved in the heat transfer process, three types of heat exchangers are found. They are
- Gas – Liquid: This type involves the application in the compressor oil cooling arrangement is required.
- Liquid – Liquid: This type of Heat Exchanger is used very commonly in the process industry. Shell & tube heat exchanger is a common example.
- Gas – Gas: This type of heat exchanger is used in a process where air pre-heating is required which is through APH (Air pre-heating).
E. Heat Exchanger Classification based on Functions and Usage
Depending on the process function and application, there are various types of heat exchangers as listed below:
- Exchangers
- Coolers
- Condensers
- Chillers
- Reboilers
- Non-fired Heaters
- Evaporators
- Steam generators
F. Classification of Heat Exchangers based on Construction
Depending on the construction features, heat exchangers can be classified into different types as follows:
- Shell and tube heat exchangers
- Plate-type heat exchangers
- Air-cooled heat exchangers
- Spiral heat exchangers
- Finned tube heat exchangers
- Double-pipe heat exchangers
Selection of Heat Exchangers
Selecting the proper type of heat exchanger from such different options available is a difficult task. The selection of a specific type of heat exchanger is usually done by the process engineer during the design phase. Many parameters must be considered while selecting the right heat exchangers. Some of these factors that impact the heat exchanger selection process are:
- The type of fluids, the fluid stream, and their properties (Fouling characteristics of the fluids)
- The desired thermal outputs (Temperature driving force)
- Size limitations (Plot plan & layout constraints)
- Application
- Design and Operating pressures & temperatures
- Available Utilities
- Costs
- purchase cost
- installation cost
- operating cost
- maintenance cost
In general, more than 50% of all heat exchangers installed are Shell-and-tube heat exchangers. The following image provides a rough idea of how the heat exchanger selection varies with design temperature and pressure.
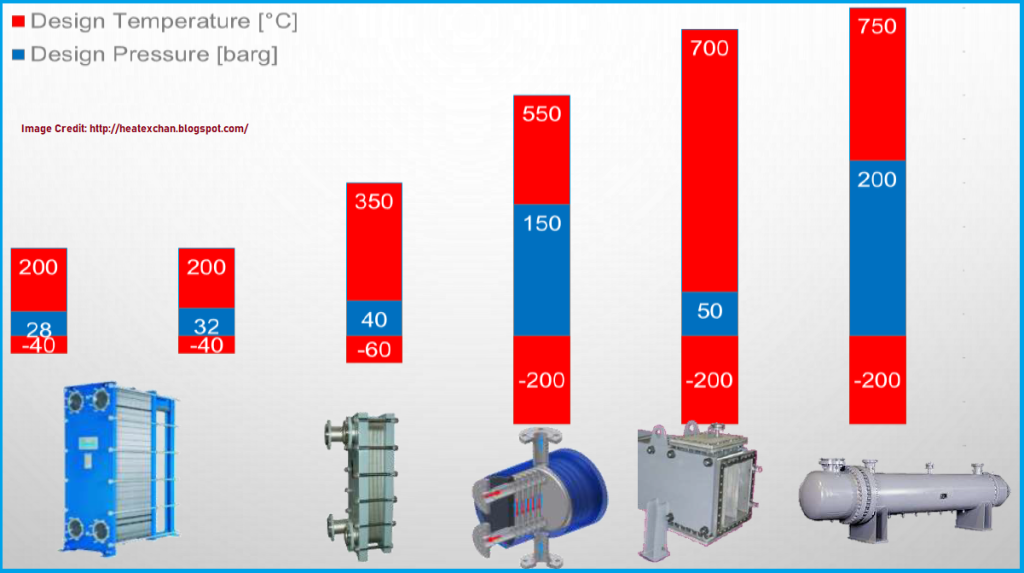
It’s a wonderful thing I benefitted slot I’m a mechanical engineering student.
welldone
Very good content on the exchanger,pl prepare a note on shell and tube and others