As per Merriam-Webster dictionary, “a pump is a device/machine that raises, transfers, delivers, or compresses fluids by suction or pressure or both”. So a pump is a piece of mechanical rotary equipment that moves fluids/slurries from the inlet through the outlet to transfer fluid to a desirable location. It increases the pressure (energy head) of the fluid and imparts velocity (energy) to help in the liquid movement. Refer to Fig. 1 which shows various types of Industrial Pumps used in Processing Plants.
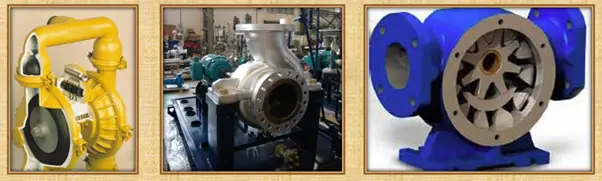
Where are pumps used?
Starting from irrigation, water supply, gasoline supply, etc the pump finds its application in air conditioning systems, refrigeration, chemical movement, sewage movement, flood control, marine services, and finally in all industries like powerplants and process industries. Process Industries (Refinery, Oil & Gas, Chemical and Petrochemical Plants) can not be thought of without the application of pumps. That’s why pumps are called the heart of a process plant.
What are the Types of Pumps?
Refer to the following charts that show the major types of pumps used in industries:
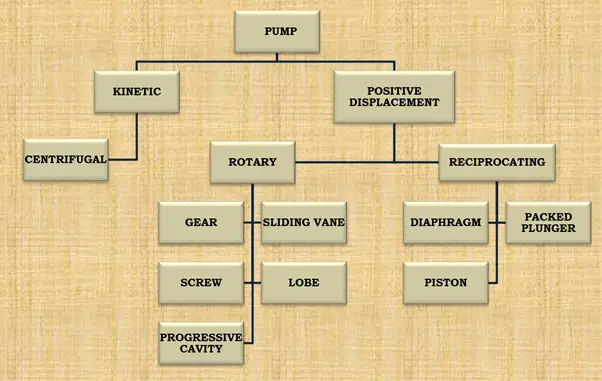
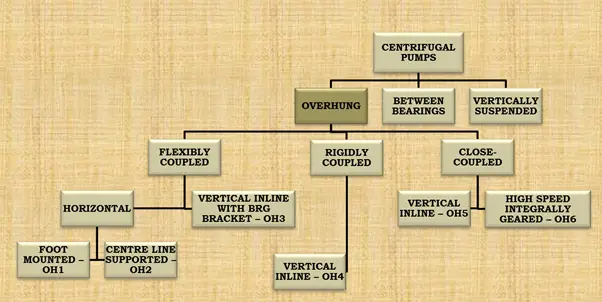
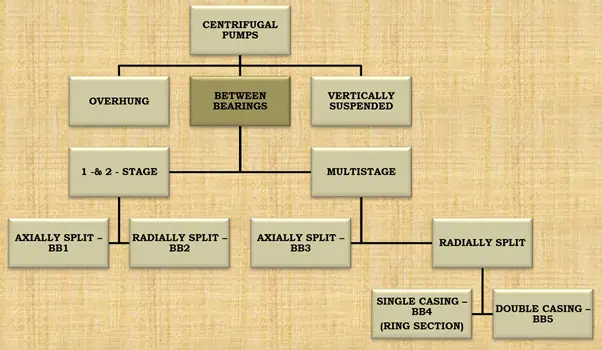
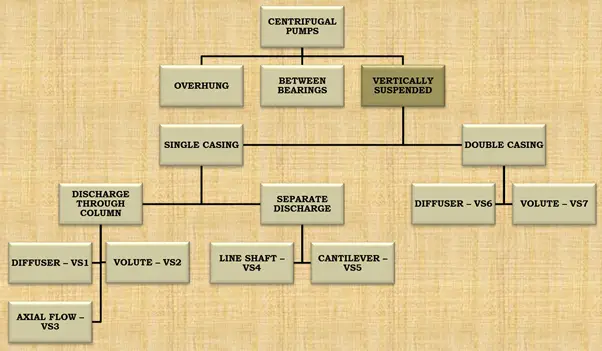
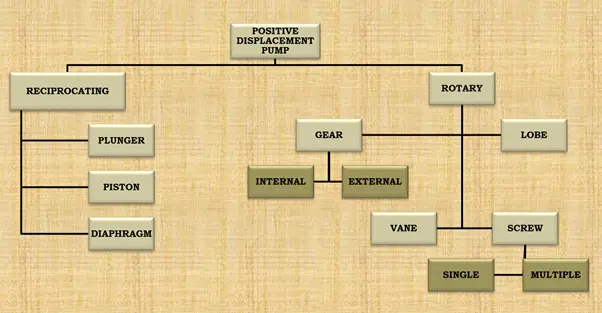
Brief Working Principle of Pumps
Kinetic Pumps
In Kinetic Pumps, a centrifugal force of the rotating element called an impeller, “impels” kinetic energy to the fluid, moving the fluid from pump suction to the discharge.
Positive Displacement Pumps
A positive displacement pump uses the reciprocating action of a piston or the squeezing action of meshing gears, lobes, or other moving bodies to displace the media (entrained in the cavity) from one area to another (from suction to discharge).
Items in a Pump Package
Refer to the following image that explains the major items that constitute a complete pump package.
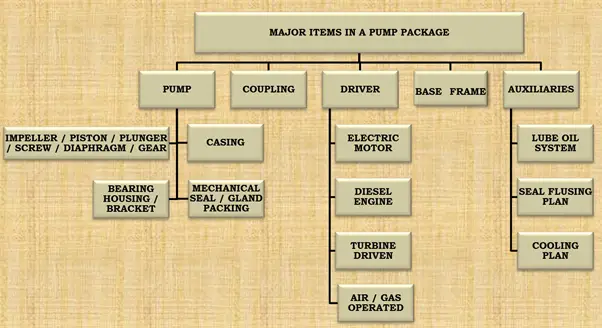
Codes and Standards for Pumps
Some of the major codes and standards that are used in process industries are listed below:
- API 610 – Centrifugal Pumps
- ANSI B 73.1 – Horizontal Centrifugal Pumps
- ANSI B 73.2 – Vertical inline Centrifugal Pumps
- API 674 – Positive Displacement-Reciprocating pumps
- API 675 – Positive Displacement-Controlled volume Pumps
- API 676 – Positive Displacement-Rotary Pumps
- ISO 2858 – End Suction Centrifugal Pumps
- ISO 5199 – Centrifugal Pumps
- HI – Hydraulic Institute
Pump Selection Criteria in Brief
The selection criteria of a pump is a very vast topic/study based on the different experiences/performances of various pumps in various fields/services.
Below listed selection criteria below are only a brief of the vast pump selection criteria.
- Generally, a centrifugal pump is used for high flow, low to moderate head, and low viscosity. Whereas, a positive displacement pump is used for low flow (constant flow), high head, and high viscosity.
- In the case of a centrifugal pump, the flow varies with the head. In the case of a positive displacement pump, the flow remains constant (at a constant speed) even if the pressure is varied. Hence for metering services, positive displacement pumps are preferred. Flow can be varied by the use of either stroke adjustment or variable speed drive (VSD).
Centrifugal Pump
Depending on the flow, head, and vendor’s design range, the pump may be single-stage or multistage. For a high head, either a multistage or a high-speed integrally geared pump is used.
For sumps/tanks, vertical centrifugal pumps are preferred. Also if the NPSHA is less (mostly in the case of high vapor pressure services), a vertical barrel pump (VS6 / VS7) is preferred which uses a vertical can/barrel as a casing for the impeller. This arrangement adds to the positive head on the suction side ultimately increasing the NPSHA
Positive displacement pumps
Gear Pump
These are used for very high pressures and low flow/metering services. The disadvantage with the gear pump is, that if there is the presence of abrasive particles in the fluid, there may be erosion/damage of gears during the meshing of the gears. Also, shear-sensitive fluids cannot be pumped with these pumps
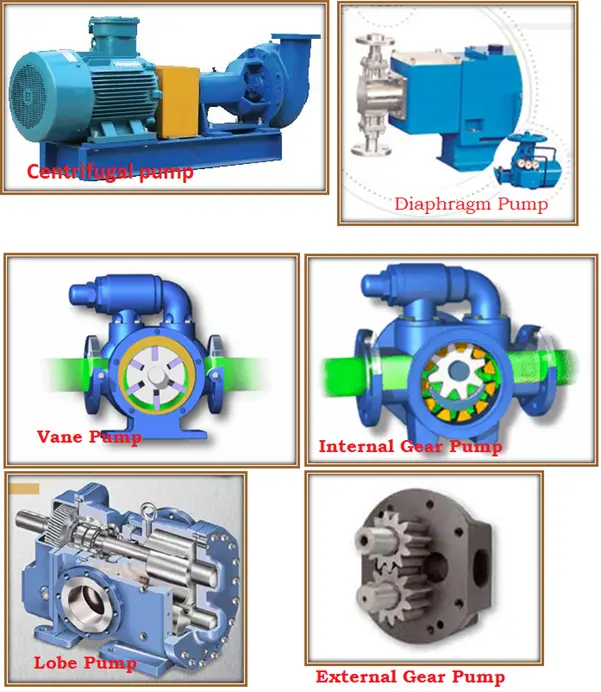
Vane Pumps
Similar in construction to internal gear pumps, these pumps have vanes that are free to move in a slot. These pumps can pump fluid containing vapor or gases. The limitation of these pumps is the discharge pressure. It can be used only up to moderate pressures. Fluid with solid suspension cannot be pumped with these pumps.
Diaphragm pump
These are used for the metering applications giving accurate flow and toxic applications (where diaphragm rupture sensors are provided for detection of diaphragm rupture). In these pumps, the mechanical seal/gland packing is not required for sealing the process fluid and hence preferred over piston/plunger pumps in toxic applications. For very high viscosities, there is a limitation to the use of these pumps. Pulsations are also a limitation.
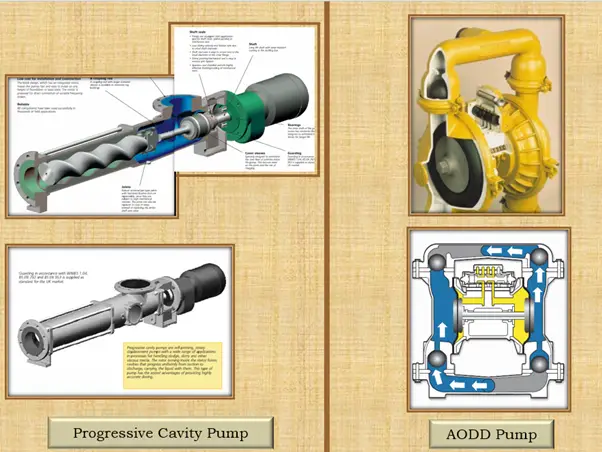
Piston / Plunger Pumps
Similar to other positive displacement pumps, this type is also used for high pressure, moderate/low flows, and high viscosity. The disadvantage of this pump is pulsations. However, a pulsation dampener may be used to reduce the pulsation problem. For lower flows, a plunger pump is used, for moderate flows, a piston pump is preferred.
Progressive cavity pumps
These are preferred for very high viscosities, abrasives liquids, slurry service, and shear-sensitive liquids. Widely used in pulp, oil fields, food products, paint, and coating industries. The advantage is fewer pulsations and good efficiency due to close clearance. The limitation of these pumps is the speed. The rotor is eccentric, and the increase in speed may lead to vibrations. High temperature is another limitation since the stator is lined with an elastomer material (Nitrile rubber etc).
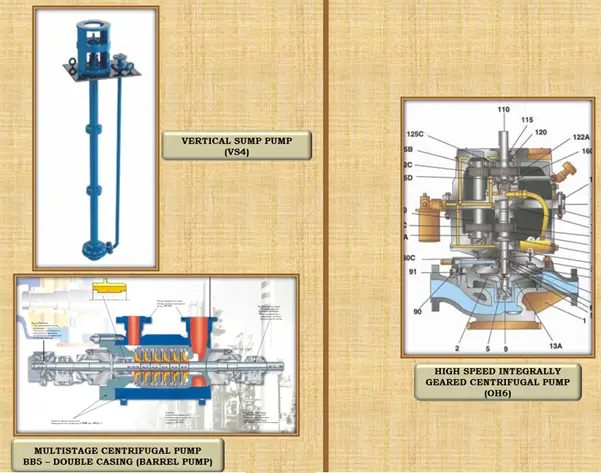
Multiple screw pumps
These are preferred for high viscosities, high pressures, and moderate flow (higher flow as compared to gear pumps). One of the advantages of a screw pump is No pulsations in the flow as compared to the piston/plunger/diaphragm pumps.
Magnetic drive pumps
These are used for toxic/hazardous fluids where leakage of the fluid to the atmosphere is not permitted. These are sealless pumps with a canister, drive magnet, and driven magnet. These are used for moderate pressures.
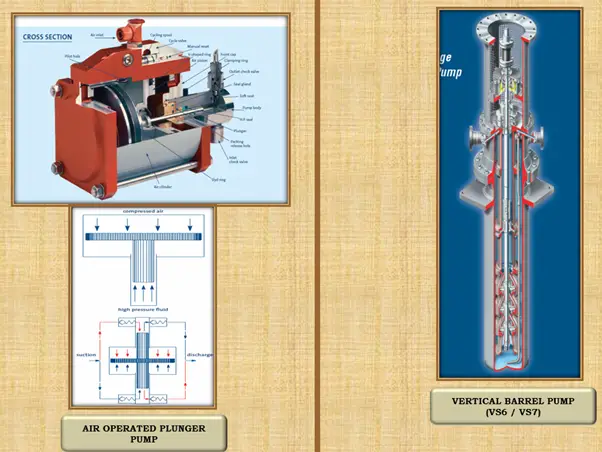
Lobe pumps
These are widely used in food and drug industries where frequent cleaning/flushing of the pump internals is mandatory. Since then there has been no metal-to-metal (timing gear is used for driving the driven lobe) there is minimal damage to the product. These pumps are suitable for CIP (clean in place). Due to complete drain-ability, the cross-contamination of the products is minimized/prevented.
Actual installation photographs
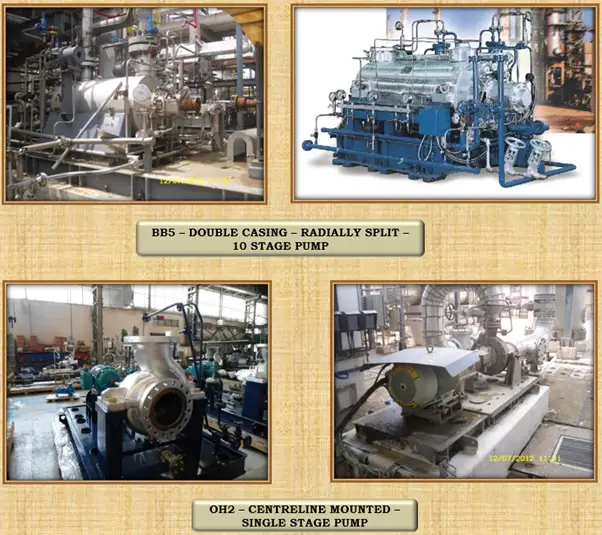
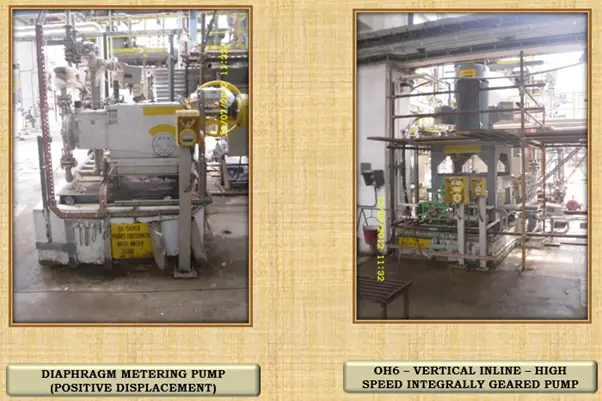
Pumps are indispensable devices in various industries, facilitating the movement of fluids for a wide range of applications.
Nice Work.
It’s nice that you mentioned how the selection criteria of a pump is a very vast topic based on the different experiences of various pumps in various fields. I was looking into an industrial equipment catalog earlier and I saw a variety of pumps. From what I’ve seen, it seems there are ANSI pumps now too.