Internal pipe coating is a crucial process in the field of pipeline infrastructure, particularly in industries like oil and gas, water supply, and chemicals. It involves the application of protective coatings to the inner surface of pipes to prevent corrosion, improve flow efficiency, and enhance the longevity and reliability of the pipeline system. In this comprehensive guide, we will delve into every aspect of internal pipe coating, from its purpose and benefits to the various methods and materials used in the process.
What is Internal Pipe Coating?
Pipe internal coating refers to the process of applying a protective coating on the inner surface of pipes, typically used in oil and gas pipelines or water distribution systems. Internal pipe coating, also known as pipe lining, or pipeline coating, is a process used to apply protective coatings to the inner surface of pipes. The primary purpose of this coating is to prevent corrosion, reduce friction, and extend the service life of pipelines in various industries. The internal pipe coating also reduces the need for frequent maintenance and repairs.
Various types of coatings are available, including epoxy, polyurethane, and ceramic coatings. The selection of the coating type depends on the material being transported, the operating conditions of the pipeline, and the environmental factors in the area.
The process of applying pipe internal coating typically involves surface preparation, cleaning, and the application of the coating material using specialized equipment. The coating is usually applied as a liquid or powder and then cured through heat or chemical reaction, creating a durable protective layer on the inner surface of the pipe.
The purpose of this article is to provide brief information about different types of pipe internal coatings/linings, their uses, advantages, and limitations.
Purpose of Internal Pipe Coating
Pipe internal coating offers several advantages, including:
- Corrosion protection: The primary advantage of pipe internal coating is the protection of the parent pipe from corrosion. The coating prevents the metal surface of the pipe from coming into contact with the fluid or gas transported through the pipeline, thus reducing the risk of corrosion and extending the life of the pipeline.
- Improved flow efficiency: The coating provides a smooth, frictionless surface that can improve the flow efficiency of the pipeline. This can result in reduced pressure drop, decreased energy consumption, and increased flow capacity.
- Reduced maintenance costs: Coating the inner surface of pipes can help to reduce maintenance costs associated with pipeline corrosion and degradation. By preventing corrosion, the coating can help to extend the life of the pipeline and reduce the need for frequent maintenance and repairs.
- Improved product quality: In pipelines used for transporting liquids, coating the inner surface can prevent contamination and maintain the quality of the product being transported.
- Environmental protection: Pipe internal coating can prevent leaks and spills caused by pipeline degradation, reducing the risk of environmental contamination.
- Contaminant Control: In some applications, internal pipe coatings can be used to prevent the contamination of fluids by foreign materials, such as particles or impurities present in the pipeline.
- Minimizing deposit formation
Overall, pipe internal coating can help to improve pipeline performance, reduce maintenance costs, and extend the life of the pipeline, making it a valuable investment for pipeline owners and operators.
Types of Pipe Internal Coatings / Lining
There are several types of industrial pipe internal coatings, including:
- Epoxy coatings: Epoxy coatings are the most commonly used type of coating for industrial pipelines. They provide excellent corrosion protection and are resistant to chemicals and abrasion.
- Polyurethane coatings: Polyurethane coatings offer similar corrosion protection to epoxy coatings but are more resistant to impact and abrasion. They are often used in pipelines that are subject to heavy wear and tear.
- Ceramic coatings: Ceramic coatings are highly resistant to corrosion, erosion, and abrasion. They are typically used in pipelines that transport highly abrasive or corrosive materials.
- Polymer coatings: Polymer coatings are a type of liquid-applied coating that provides excellent corrosion protection and can be used on a wide range of pipeline materials, including steel, concrete, and plastic.
- Polyethylene coatings: Polyethylene coatings are a type of thermoplastic coating that is used to protect pipelines from corrosion and abrasion. They are often used in pipelines that transport water and other fluids.
- FBE (Fusion-Bonded Epoxy): FBE coatings are applied using a fusion process and provide excellent adhesion and corrosion protection. They are widely used in the oil and gas industry.
- Cement Mortar: Cement mortar linings are often used in water and sewage pipelines. They provide a dense, protective layer that resists chemical and biological attacks.
- Internal Plastic Coatings: These coatings are typically made from high-density polyethylene (HDPE) or polypropylene and are used for corrosion protection and abrasion resistance in industrial applications.
The selection of the type of internal pipe coating depends on several factors, including the type of material being transported, the operating conditions of the pipeline, and the environmental factors in the area.
Internal Pipe Coating Methods
There are several methods for applying internal pipe coatings, each with its advantages and limitations:
- Spray Application: This method involves spraying the coating material onto the interior surface of the pipe. It is suitable for a wide range of coating materials and pipe sizes.
- Brush or Roller Application: Manual application with brushes or rollers is used for small-diameter pipes or when access is limited. It requires more labor but can achieve good results.
- Flow Coating: In this method, the coating material is poured into the pipe, and the pipe is rotated to ensure uniform coverage. It is suitable for large-diameter pipes.
- Centrifugal Spinning: This method is used for applying cement mortar linings. The pipe is rotated, and a mixture of cement mortar is poured in, allowing centrifugal force to evenly distribute the lining.
- Electrostatic Spray: Electrostatic spray guns charge the coating material, ensuring even distribution and adhesion to the pipe’s surface. This method is used for specific coatings and industries.
- Internal Pipe Blasting: Before coating, the interior surface of the pipe may be abrasive blasted to remove rust, scale, and contaminants, creating a clean, rough surface for better adhesion.
The choice of coating method depends on factors like pipe size, material type, and project requirements.
Application Process
The application process for internal pipe coating involves several key steps:
- Mixing: The coating material is prepared according to the manufacturer’s instructions, ensuring proper consistency and quality.
- Application: The chosen method (e.g., spraying, flow coating, centrifugal spinning) is used to apply the coating to the interior surface of the pipe. Multiple coats may be applied, depending on the project’s requirements.
- Curing: The coating is allowed to cure or harden, typically under controlled temperature and humidity conditions. Curing time and conditions vary depending on the coating material.
- Inspection: After curing, the coated pipe is inspected to ensure uniform coverage, adhesion, and quality.
- Testing: Various tests, such as holiday detection (to identify pinholes or voids) and adhesion tests, may be performed to verify the coating’s integrity.
Applications of Internal Pipe Coating
Internal pipe coating is used in various industries and applications, including:
- Oil and Gas: Internal coating is essential in the oil and gas industry to protect pipelines from corrosion caused by transported fluids and harsh environments.
- Water and Wastewater: Coatings are used in water distribution and sewage pipelines to prevent corrosion and maintain water quality.
- Chemical Processing: Chemical pipelines often require specialized coatings to resist the corrosive effects of the chemicals they transport.
- Food and Beverage: In food processing, coatings help maintain the purity of fluids and prevent contamination.
- Pharmaceuticals: Pharmaceutical pipelines must meet stringent quality standards, and coatings help ensure product integrity.
- Mining and Slurry Transport: Coatings are used to protect pipes in mining operations where abrasive materials are transported.
- Power Generation: In power plants, coatings help protect pipes that transport water and steam.
- Marine and Offshore: Internal coatings are used in maritime applications to prevent corrosion in pipelines exposed to seawater.
Examples of Internal Pipe Coatings
In the next section, we will discuss about three most common pipe internal coating and linings used in the oil and gas industries. Common pipe internal coating and linings used for industrial piping systems are
- Fusion Bonded Epoxy (FBE) Coating
- Glassflake Coatings (Chemflake, Belzona, etc)
- PE (Polyethylene) Lining / ROTO Lining
FBE (Fusion Bonded Epoxy) Coating
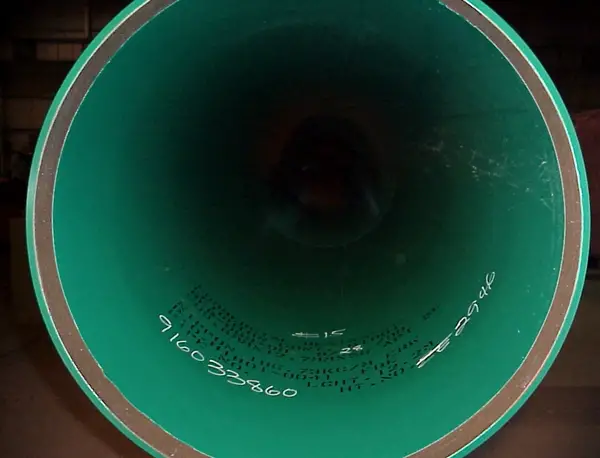
FBE or Fusion Bonded Epoxy is a high-performance anti-corrosion powder coating for moderate operating temperatures, generally suitable up to 80 °C. For higher temperature applications, special FBE grades such as TK-216 (up to 95 °C) & TK-236 (up to 120 °C) can be qualified subject to the Client’s approval.
FBE Coating Application Procedure
The following steps are generally followed for FBE coating application inside piping and pipeline systems:
- Visual inspection before blast cleaning to check the presence of oil, grease, etc.
- The steel surface is thoroughly cleaned by blast cleaning which removes rust, scale, etc, and produces a rough surface finish. The roughness value required is 50 – 100 microns.
- Heating: Induction heating or oven heating, usually in the range of 180 to 250 °C
The Application and Curing Stage
Internal surfaces of pipes are coated using a spray gun, which travels from one end to the other end of the heated pipe at a uniform speed, while the pipe is being rotated in its longitudinal axis. After coming in contact with the hot surface, the powder melts and transforms into a liquid form. This liquid FBE film flows onto the steel surface and soon becomes a solid coating by chemical cross-linking, assisted by heat. This process is known as “Fusion Bonding”.
Standard FBE coating thickness ranges between 250 to 500 microns (0.25 to 0.5mm).
After field welding of the pipe ends, FBE can be applied to the weld area as well.
FBE Coating Advantages
The main advantages that FBE coating provides are
- Suitable for higher temperatures compared to PE/ROTO lining
- Excellent adhesion to steel provides superior long-term corrosion resistance
- It can be applied to various pipe diameters from 2” to over 48”.
- It can be applied to a wide range of thicknesses.
- Good chemical resistance under most soil conditions.
- Good abrasion and high-impact resistance
Limitations of FBE Coating
However, there are some limitations of FBE coating as listed below:
- The maximum life of the FBE-coated pipe is 12 years, and if the plant design life is 25 years, one piping replacement is required.
- Can be applied only in the shop
- Applicators are not readily available
- Complex design
Internal Glass Flake Coating (Chemflake, Belzona etc)
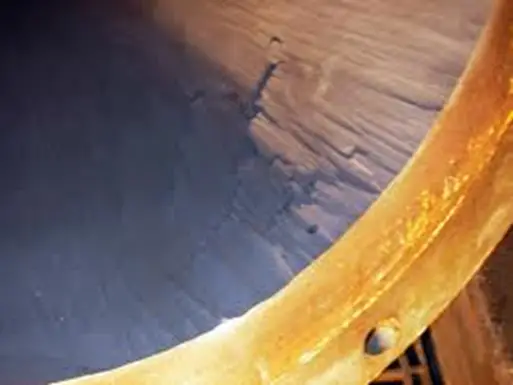
Chemflake/Belzona coatings are glass flake epoxy coatings as per PCS – 8 of SP-1246, normally suitable for up to 93°C operating temperature (Belzona can be used up to 120°C by using specific Belzona grades).
Suitable for higher pipe sizes & where Roto lining can not be carried out because of the weight limitation of the pipe spool.
Generally carried out inside a flanged pipe spool, for joining non-flanged pipe spools Thru-kote sleeves are used.
All flanges of Chemflake & Belzona coated piping shall be provided with a weld overlay of suitable material prior to dispatch for internal coating.
Internal Glass Flake Coating Application stages
- Cleaning – blast cleaning. The roughness value required is 75 – 130 microns.
- Spray – Normal airless spray or two-comp. airless spray equipment.
- Brush – Recommended for stripe coating and small areas. Care must be taken to achieve the specified dry film thickness.
- Curing – 1 coat requires around 24 hr to get a total dry film.
DFT: 2 x 750 microns (for Chemflake) 1 coat of 1000 microns (for Belzona)
Advantages of Glassflake Coating
The main advantages of glass flake coatings are
- Good chemical resistance,
- Good solvent resistance,
- Good adhesion,
- Low permeability,
- Good weather properties,
- Excellent gloss retention.
Limitations of Glassflake Coatings
Glassflake coating has the following limitations
- Temperatures & pressure-dependent – suitable only for up to 10 bar pressure & for non-flowing or less velocity fluids.
- Not suitable for abrasive fluids/slurries
- May cause skin irritation,
- Requires recoating intervals
- Chalking (for epoxy)-Time-Consuming
- Very costly
- Used only for less number of spools, not for the entire project scope
- Design life is only 3 – 4 years
PE & ROTO Lining
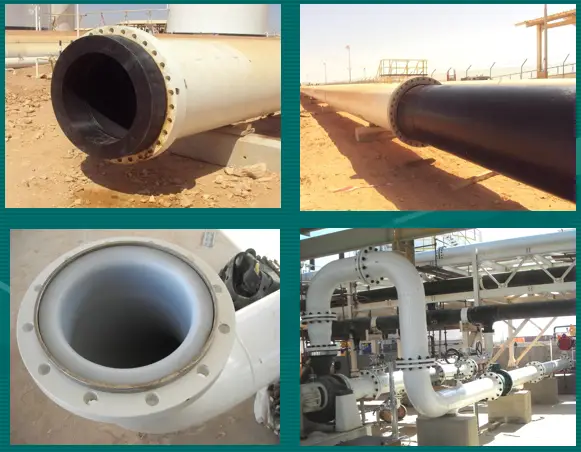
For further design details about PE/Roto lined piping please click here
How does Pipe Internal Coating Work?
Pipe internal coatings work by creating a barrier between the metal surface of the pipe and the fluid or gas being transported through the pipeline. The coating material is applied to the inner surface of the pipe, forming a protective layer that prevents the metal from coming into contact with the fluid or gas.
The coating material can be applied using various methods, including spraying, brushing, or rolling. The coating material is usually a liquid or powder that is cured to form a durable, solid layer on the pipe’s inner surface.
Once the coating has been applied, it forms a protective barrier that helps to prevent corrosion, erosion, and other forms of degradation. The coating can also improve the flow efficiency of the pipeline by providing a smooth, frictionless surface.
The effectiveness of pipe internal coatings depends on several factors, including the type of coating used, the quality of application, and the operating conditions of the pipeline. Proper surface preparation and application techniques are critical to ensuring the coating adheres to the surface of the pipe and provides effective protection against corrosion and degradation.
Internal Pipe Coating Companies
There are several companies that specialize in internal pipe coating, including:
- Shawcor: Shawcor is a global company that provides a wide range of internal pipe coating solutions for various industries, including oil and gas, water, and mining.
- Axalta: Axalta is a leading supplier of industrial coatings, including internal pipe coatings. They offer a range of coatings that are designed to provide corrosion protection and improve pipeline performance.
- PPG Industries: PPG Industries is a global supplier of paints, coatings, and specialty materials. They offer a range of internal pipe coatings that provide corrosion protection and improve the flow efficiency of pipelines.
- Sherwin-Williams: Sherwin-Williams is a leading supplier of protective coatings, including internal pipe coatings. They offer a range of coatings that are designed to provide corrosion protection and improve the durability of pipelines.
- AkzoNobel: AkzoNobel is a global supplier of coatings and specialty chemicals. They offer a range of internal pipe coatings that provide excellent corrosion protection and improve the performance of pipelines.
These are just a few examples of companies that provide internal pipe coating solutions. There are many other companies that specialize in this field, and the selection of a specific company or solution will depend on several factors, including the type of pipeline and the specific needs of the project.
Repairing Internal Pipe Coating
The repair of internal pipe coating typically involves the following steps:
- Inspection: The first step is to inspect the coating to determine the extent and location of any damage. This may involve using non-destructive testing techniques to evaluate the condition of the coating.
- Surface preparation: Once the damaged areas have been identified, the surface of the pipe must be prepared for repair. This may involve cleaning, sanding, or grinding the damaged area to remove any loose or damaged coating.
- Patching: The damaged area is then patched with suitable repair material. This may involve using a filler material, such as an epoxy-based repair compound, to fill in the damaged area.
- Coating application: Once the patching material has cured, a new coating is applied to the repaired area to restore the protective barrier.
The specific repair method will depend on the type and extent of damage to the coating. In some cases, minor damage can be repaired using a patching material and touch-up coating. In more severe cases, the damaged section of the pipeline may need to be cut out and replaced with a new section, followed by the application of a new coating.
It is important to follow proper repair procedures to ensure that the coating provides effective protection against corrosion and degradation. In some cases, it may be necessary to consult with a specialist or the coating manufacturer to ensure that the repair is performed correctly.
My husband is getting more into construction so I wondered what type of things he could be doing. I didn’t know that in FBE coating, the internal surfaces of pipes are coated using a spray gun while the pipe is being rotated in its longitudinal axis. I wonder what other equipment and parts he’ll come into contact with like pipe hangers and liners.
What is the process for interor surfaces preparation of pipes sizes from 6″ NB to 12″ NB and also interior surface coating or painting to protect from corrosion due to saline environment.
Plz suggest the equipment name for doing coating internal weld joint of pipe areas. Dia of the pipe can be from 4inches to 24 inches.
Also if you know any vendor who supply the machineries for checking the thickness of the coating through out the pipe length of 24 mtr. Dia can vary from 6 Inches to 24 inches.
HOW WE APPLIED IN CAESAR II SIR
Greetings,
What is the recommendation / way to go w.r.t. application of internal coating on the inside of weld joints?
My favorite part of this article is that pipeline coating would provide protection and durability for the proper flow and function. Yesterday, my cousin informed me that he and his business associate were hoping to find an internal pipe coating solution that could provide the development durability of the warehouse pipeline project development. He asked if I had thoughts on the best choice to consider. I love this valuable coating guide article for the best planning approach. I’ll tell him that consulting a trusted internal pipe coating service can help provide information about the process.
What will be the absolute roughness for a pipe that is internally coated with Glass Flake for seawater transportation?