Air Cooled Heat Exchangers (ACHE) are one of the heat exchanger types frequently used in Process, Power, Steel, and several other Industries where a process system generates heat that must be removed, for which there is no local use. The main function of the Air-Cooled Heat exchanger is the direct cooling of various process mediums by atmospheric air. These heat exchangers are also known as Air Fin Fan Coolers, Air Fin Coolers, Air Coolers, or Fin-tube heat exchangers. Air-cooled heat exchangers (ACHEs) have emerged as a crucial technology in this domain. They offer a method of cooling process fluids using ambient air, avoiding the complexities and costs associated with water-cooled systems. This blog discusses the design, operation, and applications of air-cooled heat exchangers, providing a thorough understanding of their significance and functionality.
What is an Air-Cooled Heat Exchanger or Air Cooler?
An air-cooled heat exchanger is a heat rejection equipment that transfers excess heat from a process fluid to the ambient air. It works on the principle of convection and conduction to dissipate heat from process fluid to air. Unlike water-cooled heat exchangers, which use water as a cooling medium, ACHEs use air to dissipate heat. This process typically involves a heat exchange coil or a series of finned tubes where the hot fluid passes through, and the ambient air stream is passed over the tubes to carry away the heat. By effective selection of the tube material, ‘ACHE’ can effectively cool or condense process water, chemicals, petrochemicals, or any other heat transfer fluid.
Applications of Air-Cooled Heat Exchangers
Major applications of air-cooled heat exchanger are found in
1. Oil and Gas Industry
In the oil and gas industry, ACHEs are used for cooling fluids and gases in various applications, including compressors, pumps, and separators. Their ability to operate in remote locations where water is scarce makes them particularly valuable in this sector.
2. Chemical Processing
Chemical plants often use ACHEs to cool process fluids and reactors. The robust design of ACHEs makes them suitable for handling corrosive and hazardous substances.
3. Power Generation
In power plants, ACHEs are used to cool various components, including generators and turbines. They help maintain optimal operating temperatures and improve overall efficiency.
4. HVAC Systems
In large commercial and industrial buildings, ACHEs are used in HVAC systems to reject heat from refrigerants. They are a crucial component in maintaining comfortable indoor climates.
They are also sometimes found in the cement, pharmaceutical, sponge iron, and steel industries.
Advantages of Air Cooled Heat Exchanger
The main advantage of Air-Cooled Heat Exchangers (ACHE) is their very low maintenance and operating costs.
As compared to cooling towers and shell and tube heat exchangers, air coolers are a “green” solution. They do not require an auxiliary water supply because of the lost water due to drift and evaporation. Where there is no utility, such as water, available as a cooling medium. The main advantages of an air-cooled heat exchanger can be summarised as follows:
1. Reduced Water Usage
One of the most significant benefits of ACHEs is the elimination of water consumption. This is particularly advantageous in areas where water is scarce or where water discharge regulations are stringent.
2. Lower Maintenance Costs
Air-cooled systems generally have fewer components subject to corrosion and scaling compared to water-cooled systems. This results in lower maintenance and operational costs over time.
3. Environmental Benefits
By reducing the reliance on water, ACHEs help mitigate the environmental impact associated with water withdrawal and discharge. This makes them a more sustainable option in certain scenarios.
4. Simpler Operation
ACHEs are less complex to operate compared to water-cooled systems, which often require additional equipment such as cooling towers and water treatment systems.
How Air-Cooled Heat Exchangers Work
The operation of an air-cooled heat exchanger is relatively straightforward. Here’s a step-by-step explanation:
- Hot Fluid Inlet: The hot process fluid enters the heat exchange coil from the inlet.
- Heat Transfer: As the hot fluid flows through the coils, heat is transferred to the metal surface of the tubes and fins. The large surface area provided by the fins enhances this heat transfer.
- Air Flow: Fans force ambient air over the coils. The air absorbs the heat from the fins, cooling the fluid inside the tubes.
- Cool Fluid Outlet: The cooled fluid exits the coil and is directed to the next stage of the process or system.
- Warm Air Discharge: The air that has absorbed heat is expelled from the system.
ACHEs are usually used when the outlet temperature is more than about 20 °F above the maximum expected ambient air temperature. They can be used with closer approach temperatures, but often become expensive compared to a combination of a cooling tower and a water-cooled exchanger. Fig. 1 shows the operating principle of a typical air-cooled heat exchanger.
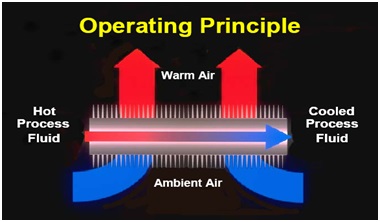
Air Cooled Heat Exchanger Construction
The construction of an Air-Cooled Heat Exchanger is fairly simple. Fig. 2 and Fig. 3 provide the component parts of an air fin fan cooler. Refer to the animated video at the end of the article for proper understanding.
- Typically air-cooled exchangers consist of a finned tube bundle with rectangular box Headers on both ends of the tubes.
- Cooling air is provided by one or more fans.
- Usually, air blows upwards through a horizontal tube bundle.
- The fans can be either forced or induced draft depending on whether the air is pushed or pulled through the tube bundle.
- The space between the fans and the tube bundle is enclosed by a plenum chamber that directs the air. The whole assembly is usually mounted on legs or a pipe rack.
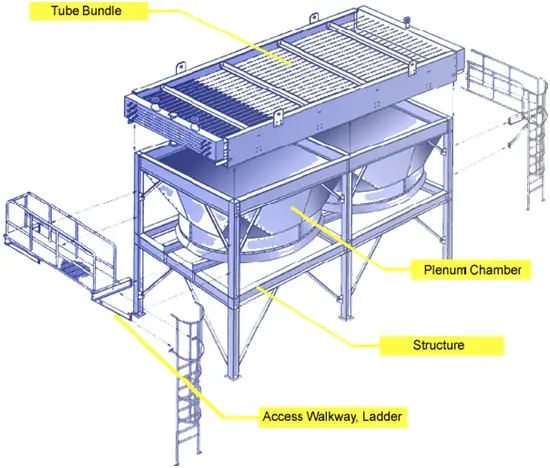
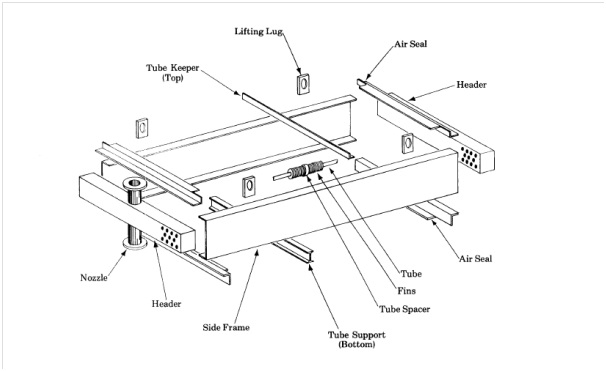
Components of an Air-Cooled Heat Exchanger
An Air Cooled Heat Exchanger consists of the following primary components (Refer to Fig. 11):
- One or more bundles of the heat transfer surface.
- A fan or blower that moves the air.
- A mechanical driver and power transmission for running the fan or blower.
- A plenum
- A supporting structure
- Header and Fan maintenance platforms.
- Optional louvers and recirculation ducts
- Optional variable-pitch fan hub or variable-frequency drive for temperature control and power savings.
Bay Arrangement in Air Cooler
One or more tube bundles, serviced by two or more fans, including the structure, plenum, and other attendant equipment is called a bay in an air-cooled heat exchanger. Refer to Fig. 4 for typical bay arrangements.
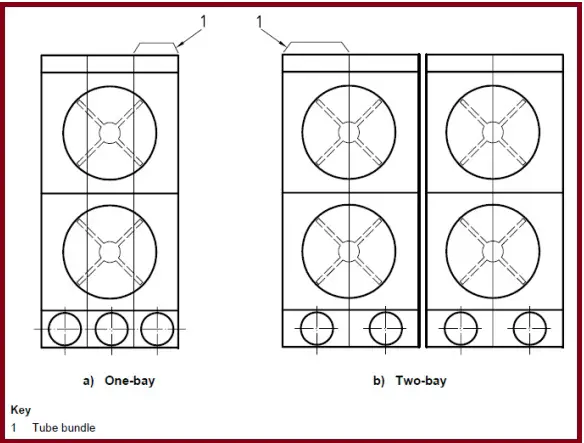
Air Cooled Heat Exchanger Tubes
Wall thickness for tubes with an OD of 1 inch (25.4 mm) to 11/2 (38.1 mm) shall not be less than specified in the table below: (Fig. 5)
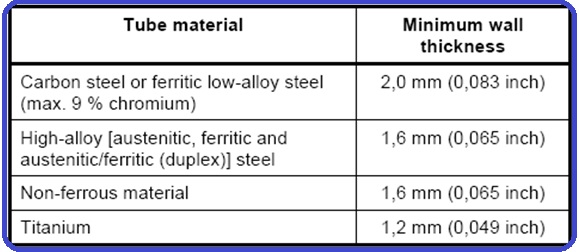
What kind of finned tubes are used for Air Coolers?
- Fin types
- Embedded
- Extruded
- Footed
- Externally bonded
- Elliptical
- Fin density (FPI) – 7 to 16
- Fin height – 3/8 inch to 5/8 inch
- Fin thickness – 0.012 to 0.02 inch
Fin Types (Fig. 6):
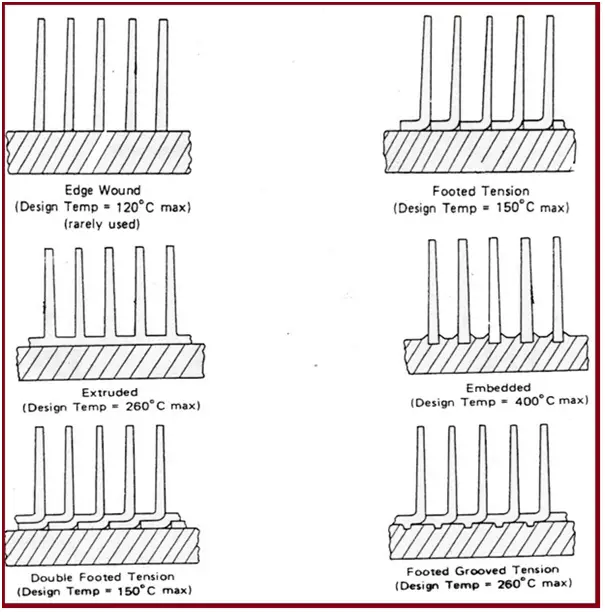
Fin Selection (Fig. 7):
Refer to Fig. 7 for limiting temperatures of various types of fins.
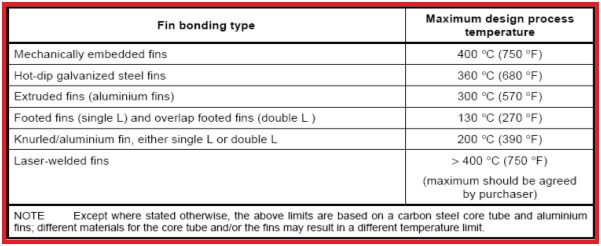
Fin Material
Typical materials used for air-cooled heat exchanger Fin construction are
- Aluminum
- Carbon steel
- Carbon steel finned tubes can be hot-dip galvanized to prevent corrosion & to provide a metallic bond between the fin and the bare tube.
- Copper
Air-cooled heat exchanger tube bundle orientation:
Three types of ACHE tube bundle orientation are possible; horizontal, vertical, and sloped orientation.
Horizontal orientation is the most preferred and common type and is widely used in process industries.
Orienting the tube bundles in a vertical direction (Fig. 8) can save a considerable area but the air cooler performance is greatly dependent on prevailing wind speed and direction. So if the prevailing wind is in the opposite direction, it will greatly reduce the performance of the air-cooled heat exchanger.
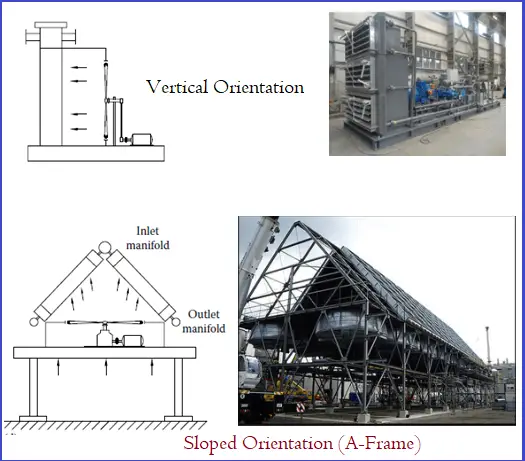
A-frame or V-frame air-cooled heat exchanger units are a compromise between the ground area requirement and exchanger performance. In this type of design, two bundles are sloped at 45°-60° and joined by their headers at the top or bottom. Thus it takes the shape of A or V. In steam condensing applications, the A-frame type (Fig. 8) with forced draft fans is used.
What are Air Cooler Headers?
Headers of air coolers are the boxes at the ends of the tubes that distribute the fluid from the piping to the tubes. The cover plate header design shall permit the removal of the cover without disturbing header piping connections. Fig. 9 shows a typical construction of tube bundles with removable cover plate headers.
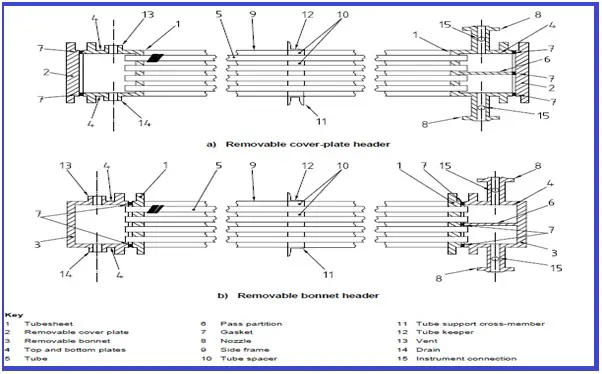
The bonnet header design shall permit the removal of the bonnet with the minimum dismantling of header piping connections. Threaded plug holes shall be provided opposite the ends of each tube for access. Holes shall be threaded to the full depth of the plug sheet or 50 mm (2 inches), whichever is less.
Common header types (Fig. 10) used in air-cooled heat exchanger construction are
- Plug Box Header: Widely used
- Bolted Cover Header
- Bonnet Header
- Manifold Header
- Pipe Header: Cylindrical header for very high-pressure services (>200 bar)
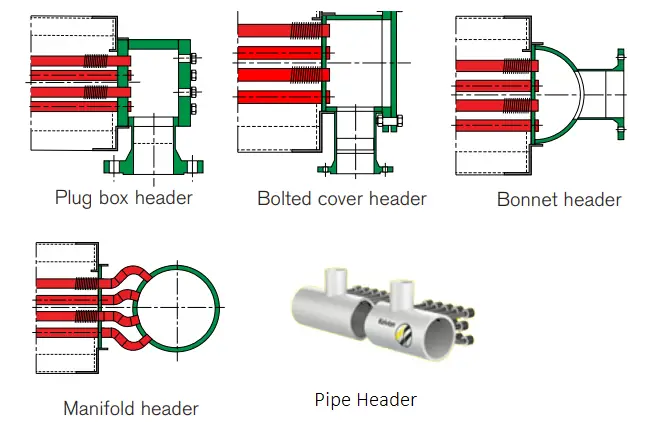
Why are some coolers forced drafts & some induced drafts (Fig. 11), and which one is better?
- Mostly air-cooled heat exchangers are of forced draft construction. Forced draft units are easier to manufacture and maintain. The tube bundle is mounted on top of the plenum, so it can be easily removed & replaced. The fan shaft is short since it does not have to extend from the drive unit through the tube bundle and plenum to the fan as in an induced draft design. Forced draft units require slightly less horsepower.
- Since the fan is moving a lower volume of air at the inlet than it would at the outlet. If the process fluid is very hot, the cooling air is hot at the outlet, this could cause problems with some fans or fan actuators. If the fan is exposed to very hot exhaust air since forced draft coolers do not have the fans exposed to hot exhaust air.
In addition to the above, The major differences between an Induced Draft and a Forced Draft Air Cooled Heat exchanger are listed below with respect to some design parameters:
Sr. No | Parameter | Induced Draft Air Cooler | Forced Draft Air Cooler |
1 | Air Distribution | Better distribution of air across the bundle. | Less uniform distribution of air over the bundle. |
2 | Air Re-circulation | Less possibility of hot effluent air recirculating into the intake | Increased possibility of hot air recirculation |
3 | Process Control and Stability | Better process control and stability. The plenum covers 60% of the bundle face area which reduces the effects of sun, rain, and hail. | Less Process Control |
4 | Fan Failure | Increased capacity in the fan failure | The low natural draft capability of fan failure |
5 | Horsepower Requirement | Possibly higher horsepower requirements if the effluent air is very hot. | Possibly lower horsepower requirements if the effluent air is very hot |
6 | Temperature Limitation | Effluent air temperature should be limited to 220°F to prevent damage to fan blades, bearings, or other mechanical equipment in the hot air stream | Accommodates higher process inlet temperatures |
7 | Fan Maintenance Access | Fans are less accessible for maintenance | Better accessibility of fans and upper bearings for maintenance. |
8 | Bundle Maintenance Access | Plenums must be removed to replace bundles | Better accessibility of bundles for replacement |
9 | Structural Cost | Increased structural cost and lower mechanical life. | Reduced Structural costs and improved mechanical life. |
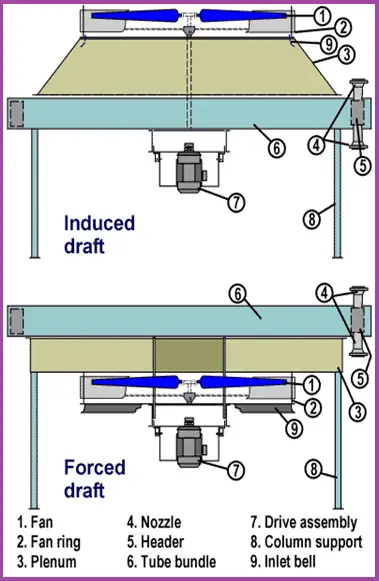
What kinds of Air Cooler controls are used?
As one might expect the best kind of control scheme depends on the application. Does the process require very tight control of the process outlet temperature or is it better to allow the process temperature to go down with the ambient air temperature? Following is a list of some of the commonly used control devices for air coolers, but in no particular order.
- Manually operated louvers
- Pneumatically activated automatic variable pitch fans.
- Variable frequency fan drive (VFD).
VFD if used shall suit the motor nameplate rating and similarly for the Belt Pulley transmission, it shall suit the motor nameplate rating.
What types of Air Cooled Heat Exchangers are used for Cold Climates?
For extremely cold regions like Canada, Siberia, etc an air-cooled heat exchanger with an internal recirculation system is used. Such systems can control the cooling air temperature regardless of ambient temperature.
Positive or Negative Step Auto variable fans are used for such systems. By using one fixed-pitch fan blowing upward and one Auto-variable pitch fan, which is capable of negative pitch and thus of blowing air downward, it is possible to temper the air to the coldest portion of the tubes and thus prevent freezing. Normally, forced draft units have a negative pitch fan at the outlet end, while induced draft units have a positive pitch fan at the outlet end.
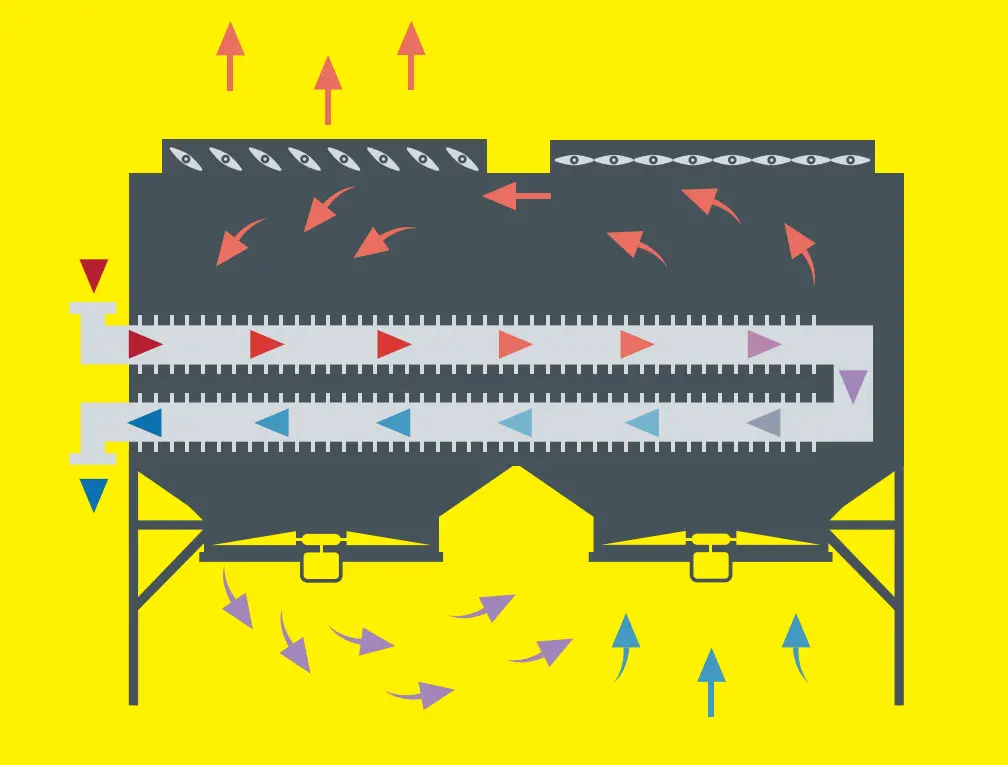
Codes and Standards for air-cooled exchanger Design
The following codes and standards govern the design of air-fin fan coolers.
- API 661 / ISO 13076 ( Air-cooled heat exchangers for general refinery service )
- ASME SECT.VIII Div.1 or Div.2
- Shell DEP 31.21.70.31
SHELL DEP special requirement for air-cooled exchangers:
- The removable Bonnet type Header Shall not be used.
- Plug-type headers shall be used for all air coolers in hydrocarbon gas or liquid service.
- Removable cover plate-type headers shall be utilized in auxiliary utility services such as lube oil, hot oil, and cooling circuits.
- Bolted joints (stud construction or flanged construction) shall be designed with confined gaskets
- Tubes shall be provided with aluminum fins. The fins for all the air cooler tubes shall be of the extruded type with 394 fins per meter
Maintenance and Inspection of Air-Cooled Heat exchangers
The performance and reliability of ACHE depend on proper inspection and maintenance of components. Regular maintenance and inspection of Air Cooler systems include
- Lubrication of motor and fan bearings (once a month if coolers work continuously)
- Checking belts for wear and ensuring their tension.
- Inspect fans, blades, bolting, etc at regular intervals.
- Maintaining proper oil levels at gearboxes.
- Checking the condition of tube bundles.
Disadvantages of Air-Cooled Heat Exchangers
Some of the disadvantages of air-cooled heat exchangers are
1. Space Requirements
ACHEs typically require more space compared to their water-cooled counterparts. The need for large fan arrays and ample clearance for airflow can be a limitation in space-constrained environments.
2. Limited Cooling Capacity
The cooling capacity of ACHEs is directly affected by ambient air temperature. In very hot climates, the efficiency of heat removal can be reduced compared to water-cooled systems.
3. Noise Levels
Fans used in ACHEs can produce significant noise, which might be a concern in noise-sensitive areas or residential environments. Proper design and placement can help mitigate this issue.
Some more useful resources for you..
Basic Considerations for Equipment and Piping Layout of Air Cooled Heat Exchanger Piping
Considerations for development of Plant Layout: A brief presentation
Some articles related to heat exchangers
Animated video tutorial of the Assembly Sequence of an Air Cooled Heat Exchanger
Refer to the below attached animated video for proper understanding and visualization of each part of a forced draft type air fin fan cooler. The assembling sequence of one single bay is shown in the video.
Air-cooled Heat Exchanger Manufacturers
When it comes to air-cooled heat exchangers (ACHEs), several manufacturers are recognized globally for their expertise, innovation, and high-quality products. Here’s a rundown of some of the world-renowned ACHE manufacturers:
- SPX Cooling Technologies, USA
- API Heat Transfer, USA
- GEA Group, Germany
- Thermax, Germany
- KTI-Plersch Kältetechnik GmbH, Germany
- Fives, France
- Hamon & Cie (International) SA, Belgium
- Heatex, Denmark
- Parker Hannifin, USA
- Sustainable Technologies (S&T), India
- Bharat Heavy Electricals Limited (BHEL), India
In conclusion, Air-cooled heat exchangers play a vital role in a wide range of industrial applications by providing an efficient and sustainable method of heat removal. Their design and operation involve careful consideration of various factors, including ambient conditions, fluid characteristics, and space requirements. Despite some disadvantages, their benefits—such as reduced water usage and lower maintenance costs—make them a valuable component in many systems.
Congratulations:
Very good and very well explained articles.
Thanks.
Nice Article
Thanks For nicely explained functions of involved components.
Than you so much.please explain step by step method for air cooler stress analysis
Good Articles and easy to understand.
Dear Sir,
We are pleased to inform you that Eastern Refinery Ltd (ERL) Chittagong, Bangladesh. Called International Tender for Complete Aero condenser Unit and Thermal Expansion Joints Supply Installation, Testing and Commissioning. If you have previous experience for similar or higher Capacity Aero condenser unit and Thermal Expansion Joints supply and if you are interested to work with us, then we can forward you full set of Tender Documents.
Your early reply in this regards will be highly appreciated.
Best regards
Khaiz Ahmed
Nice article….
thanks for useful information about air cooler.
Very good explanation for air cooler principles
Very nice article! (i suppose. i have never read) anyway, i would like to ask about your profile photo. Where did you take this photo? And what are you hugging there? This is a strange photo Mr. Anup Dey.
Regards,
Blank
https://whatispiping.com/wp-content/uploads/2020/01/Anup-Dey-author-whatispiping.com_.png
Awesome contents, thanks!
Do you consider that the system of piping need a spool removal?? when we have a removal header that include the header nozzles??
Very good article. Keep doing.
Dear sir
your article is useful.
can you guide me cleaning method for fines and tube type cooler.
What will be cost difference between two types
Excellent Article.. Thanks
Thank you very much for your sharing
Relly good article, thank you, Sir.