Alarm management can be defined as the effective design, implementation, operation, and maintenance of alarms installed in any factory or workplace. A proper alert management system must be in place to alert the operator in case of any abnormal situation when the design limits are exceeded. Every plant must ensure alert management for
- Safety of the Environment and personnel.
- Equipment integrity, and
- Product Quality control.
The control room operator must get clear and concise information from the alarm system. It enables them to recognize and respond to abnormal conditions that have arisen due to some reason. Alarm management is necessary for all operating environments. An operator can use a control system, such as a DCS, or a Programmable Logic Controller (PLC) to control abnormal situations.
Whenever any process deviates from the normal operating conditions, Alarms are triggered. The alarm management system should work on the occurrence of any type of abnormal operating situation. An abnormal situation can occur when a process in any operating plant is disturbed because of a deviation from its normal operating state, calling for human intervention.
If the abnormal situations are not diagnosed and controlled in time, they may create billions of dollars in impact on the economy. Hence, the alarm management system must aim at preventing, or at least minimizing physical and economic loss through operator intervention in response to the upset condition.
The processes and practices for determining, documenting, designing, monitoring, and maintaining alarm messages from process automation and safety systems are parts of an alarm management system.
Reason for Alarm Management
Safety and profitability are cornerstones of any sustainable operation. For safe and sustainable operations, the contribution of the Alarm and Alarm Management system is crucial.
Peter Drucker said “A well-managed plant is silent and boring,” but it actually takes a lot of work and effort to ensure this is the case.
In reality, alarm management does not always achieve this because they are improperly designed, poorly documented, changed without adequate review, or fail to provide enough information to the operator.
An effective alarm system is a key part of a safe and reliable process. Incorrectly designed and poorly functioning alarm systems can have serious consequences and lead to ineffective alarms; which in turn leads to alarm flooding, a high number of standing alarms, inadequate prioritization of alarms, and improper or no alarm action.
The advanced alarm management system is a combination of applications that help to make effective alarm systems, conforming to industry recommendations and standards such as the Engineering Equipment & Materials Users Association (EEMUA).
Advantages of Alarm Management System
Advanced alarm management system offers the following benefits:
- Minimizes the number and impact of abnormal situations.
- Identifies alarm system problems and performance, as well as operator workload.
- Improves operator effectiveness, protecting plant uptime and safety, and reducing losses
- Reduces time and effort to develop, deploy, and maintain alarm systems.
- Production optimization/debottlenecking / increased throughput
Furthermore, ineffective alarm management leads to conditions such as
- Untimely response to an alarm due to poor prioritization.
- No alarm at all in spite of occurrences of the event.
- No show of the alarm due to inhibited or disabled alarms.
- Flood of alarms leading to a missing sequence.
- A flood of alarms and missing events due to poor configuration
Ambiguous or missing instructions to the alarms are some of the harmful effects seen in the operations and many times, the alarm management systems are designed to address these issues.
Alarm Management Life Cycle and Rationalisation
A well-designed alarm management system needs to handle
- Alarm overload,
- More alarm than manageable,
- Alarm floods,
- Nuisance alarms,
- Chattering alarms
- Standing/stale alarms,
- Redundant alarms,
- Alarms that have no response, and
- Alarms with the wrong priority
Key Steps for Effective Alarm Management System
There are seven key steps for Effective Alarm Management. They are
Step 1: Creation of an alarm philosophy and its implementation
A comprehensive design and guideline document must be prepared. It should define the plant standard and employ all lessons learned and best-practice alarm management methodologies.
Step 2: Alarm performance benchmarking
Determine the strengths and deficiencies of the alarm system by Analyzing it. Map out a practical effective solution to improve the alarm management system.
Step 3: Resolution of “Bad actor” alarms
The performance of the alarm system must be improved by eliminating bad actor alarms. Experience shows that more than half of the entire alarm load usually comes from relatively few alarms. Improvement must be done by making them work with minimum effort.
Step 4: Alarm documentation and rationalisation (D&R)
Each alarm in the system must comply with the adopted alarm philosophy and the principles of good alarm management.
Step 5: Alarm system audit and enforcement
The alarm system must be audited from time to time to ensure its proper working and security. It is very easy to alter the DCS alarm systems. So, methods must be devised to ensure that the alarm system does not drift from its rational state.
Step 6: Real-time alarm management
Advanced alarm management techniques are required to ensure that the function of the alarm system is properly achieved. The alarm should alert the operator in all operating scenarios. Some examples of such advanced technologies are
- Alarm Shelving,
- State-Based Alarming, and
- Alarm Flood Suppression technologies.
Step 7: Control and maintain alarm system performance
To ensure that the gains that have been achieved from performing the steps above do not dwindle away over time, proper management of change and longer-term analysis and KPI monitoring is needed. The principle of “entropy” definitely applies to an alarm system.
Actually, the alarm management concept mainly comes from standard ISA 18.2 – now also as international standard IEC 62682. One of the milestone activities of the standards is the alarm life cycle.
The following figure (Fig. 1) provides a detailed block diagram of Alarm Life cycle management.
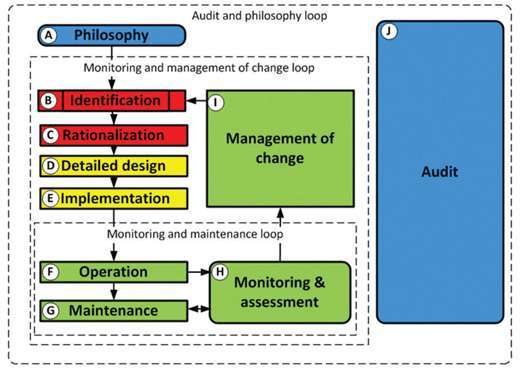
We all are aware that the oil and gas industry is a key employment generator and a huge contributor to GDP. So for such critical industries, the operation must continue 24/7 without outages. To prevent outages, and shutdowns, and improve efficiency, the industry employs alarm systems for both onshore and offshore operations. These provide alerts to help locate the problem and resolve it immediately.
In general, oil and gas plants use alarm systems that aren’t the most efficient or effective. They usually generate distracting alarms that confuse operators without any clue to figure out the actual cause of an error. As operation means a loss of production, It directly affects revenue. Hence, the challenges of current alarm systems need mitigation. It will allow the oil and gas industry to resolve their maintenance outages, which in turn, will help the operators quickly assess the situation to get plant operations back to normal.