Aluminum extrusion is a versatile and highly efficient manufacturing process that has revolutionized various industries. From aerospace to automotive, construction to electronics, aluminum extrusion offers a wide range of benefits that make it an attractive choice for designers, engineers, and manufacturers alike. In this comprehensive guide, we will delve into the world of aluminum extrusion, exploring its process, advantages, applications, and future potential.
What is Aluminum Extrusion Process?
The aluminum extrusion process is a manufacturing method that involves shaping aluminum alloys by forcing them through a die with a specific cross-sectional profile. It is a highly versatile and efficient process used to create continuous profiles of various shapes and sizes. The process begins with heating aluminum billets to a specific temperature, making them malleable. The heated billet is then pushed through a specially designed die using a hydraulic press, resulting in the extrusion of the aluminum material in the desired shape. The extruded aluminum profile is then cooled and cut into the desired lengths. The process allows for the production of complex shapes with precise tolerances, offering design flexibility and cost-effectiveness.
Types of Aluminum Extrusion Process
There are several types of aluminum extrusion processes that are commonly used in industry. These processes are differentiated based on the method of extrusion and the equipment used. The main types of aluminum extrusion processes include:
Direct Extrusion:
Direct extrusion, also known as forward extrusion, is the most common type of aluminum extrusion process. In this method, a cylindrical billet is placed in a container and forced through a die using a ram or hydraulic press. The aluminum flows in the forward direction through the die, resulting in the desired profile shape. This process is relatively simple and cost-effective.
Indirect Extrusion:
In indirect extrusion, the die is stationary, and the billet is held stationary or rotated while the container and ram move. The ram pushes the extrusion through the die in the opposite direction of the ram movement. Indirect extrusion offers more control over the extrusion process and can produce complex profiles with tighter tolerances. Indirect extrusion is also known as backward extrusion. Fig. 1 (Image Credit: https://www.rapiddirect.com/blog/aluminum-extrusion/ ) below shows the schematic of the direct and indirect extrusion process.
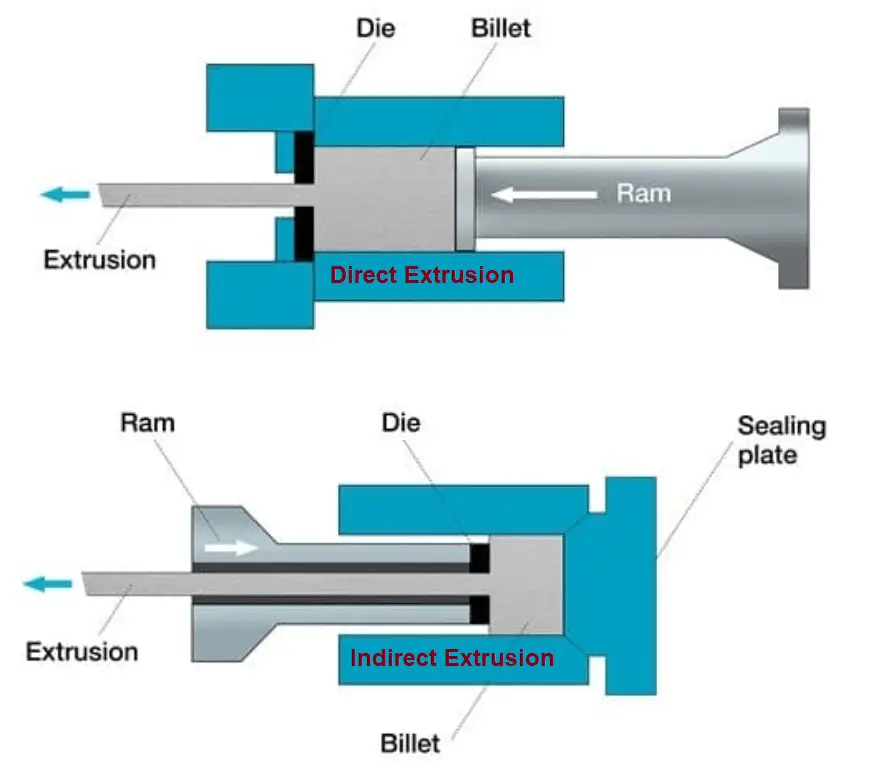
Impact Extrusion:
Impact extrusion is a specialized form of extrusion used for the production of hollow shapes. In this process, a punch is used to force the aluminum billet into a die cavity at high speed and pressure. The material deforms and flows around the punch, filling the die cavity and taking its shape. Impact extrusion is commonly used for the production of aluminum cans, tubes, and containers.
Hydrostatic Extrusion:
Hydrostatic extrusion is a unique extrusion process that involves using a high-pressure fluid as the medium to push the billet through the die. The fluid, usually oil or water, exerts pressure evenly in all directions, allowing for better control over the extrusion process and achieving precise shapes. Hydrostatic extrusion is suitable for producing high-strength aluminum components.
Tube Extrusion:
Tube extrusion is a specialized process for producing seamless aluminum tubes. It involves extruding a solid billet through a shaped die to create the tube’s desired dimensions and cross-sectional profile. Tube extrusion is commonly used in industries such as automotive, HVAC, and construction for applications where lightweight, corrosion-resistant tubes are required.
6 Steps for Aluminum Extrusion Process
The aluminum extrusion process involves several key steps to transform aluminum billets into the desired extruded profiles. Here are the general steps involved in the aluminum extrusion process:
1. Billet Preparation:
The process begins with the preparation of aluminum billets. Billets are cylindrical logs of aluminum alloy that are typically cut to the desired length and heated to a specific temperature. Heating the billets makes them soft and malleable, allowing for easier extrusion.
2. Die Design and Preparation:
A die is a specially designed tool that determines the shape and dimensions of the extruded profile. The die is made of hardened steel and consists of a hollow cavity with the desired cross-sectional profile. The die is designed based on the final product requirements and considerations such as shape, tolerances, and structural integrity.
3. Extrusion:
The heated billet is placed into a container, often called a “container sleeve” or “can,” located at the front end of the extrusion press. The container is preheated to maintain the temperature of the billet during the extrusion process. A ram or hydraulic press applies force to push the billet through the die. The aluminum material flows through the die opening, taking on the shape of the die cavity. The extrusion process is continuous, with the extruded aluminum emerging from the die as a continuous profile.
4. Cooling and Quenching:
Once the extruded profile emerges from the die, it goes through a cooling and quenching process. The extrusion is cooled using air, water, or a combination of both to solidify the aluminum and retain its shape. Quenching may involve immersion in water or other cooling mediums to rapidly cool the extrusion and enhance its mechanical properties.
5. Stretching, Straightening, and Cutting:
After the cooling process, the extruded profiles may undergo additional steps for stretching, straightening, and cutting. Stretching can be performed to improve the mechanical properties and straightness of the extrusion. Straightening processes, such as roll straightening or hydraulic straightening, are used to correct any bending or bowing in the extrusion. Finally, the extrusion is cut into the desired lengths using saws or other cutting methods.
6. Heat Treatment and Finishing:
Depending on the specific requirements, some extrusions may undergo heat treatment processes to further enhance their mechanical properties or achieve specific temper conditions. Heat treatment can include processes such as aging, annealing, or solution heat treatment. After heat treatment, the extrusions may undergo various finishing operations such as surface cleaning, deburring, anodizing, powder coating, or painting to enhance their appearance, corrosion resistance, or other desired properties.
6 Aluminum Extrusion Profiles
Aluminum extrusion allows for the creation of a wide range of shapes and profiles, offering tremendous design flexibility for various industries. Some of the common shapes made by aluminum extrusion include:
1. Solid Profiles:
Solid profiles are the simplest and most commonly extruded shapes. They have a constant cross-sectional area and are typically used for basic applications such as bars, rods, and simple geometric shapes like squares, rectangles, and circles.
2. Hollow Profiles:
Hollow profiles have a void or empty space within their cross-section. They are widely used in applications where lightweight structures with high strength are required. Hollow profiles can have different shapes, such as square tubes, rectangular tubes, round tubes, and oval tubes. They are commonly used in industries like construction, automotive, and aerospace.
3. T-slot Profiles:
T-slot aluminum extrusion profiles have a T-shaped groove along their length, allowing for easy insertion and securing of fasteners, connectors, and accessories. T-slot profiles are commonly used in applications where modularity and versatility are essential, such as framing systems, machine guards, and workstations.
4. Complex Profiles:
The aluminum extrusion also enables the production of complex profiles with intricate shapes and features. These profiles can have various combinations of curves, angles, and cutouts. Complex profiles find applications in industries like architecture, automotive, electronics, and consumer goods, where unique design requirements are crucial.
5. Heat Sink Profiles:
Heat sink profiles are specifically designed to dissipate heat efficiently. They have intricate fin patterns or heat-dissipating surfaces that maximize the surface area and enhance heat transfer. Heat sink profiles are widely used in electronic devices, lighting systems, and other applications requiring thermal management.
6. Custom Profiles:
One of the significant advantages of aluminum extrusion is the ability to create custom profiles tailored to specific project requirements. Custom profiles are designed based on the desired shape, dimensions, and functionalities needed for a particular application. Custom extrusions find applications in industries ranging from automotive and aerospace to marine, industrial equipment, and consumer goods.
Factors Affecting the Aluminum Extrusion Process
Several factors can influence the aluminum extrusion process and the quality of the extruded profiles. Understanding these factors is crucial for achieving successful extrusions. Here are the key factors that can affect the aluminum extrusion process:
Alloy Selection:
The choice of aluminum alloy is essential as it impacts the extrudability and mechanical properties of the final product. Different alloys have varying extrusion characteristics, such as extrusion temperature range, flowability, and strength. Factors to consider include alloy composition, temper, and the desired properties of the extruded profile.
Billet Temperature:
The temperature of the aluminum billet has a significant impact on the extrusion process. Heating the billet to the appropriate temperature range ensures that it is soft and malleable enough to be extruded easily through the die. The billet temperature is dependent on the alloy used and must be carefully controlled to achieve optimal extrusion results.
Die Design:
The design of the die plays a crucial role in determining the shape and dimensions of the extruded profile. Factors such as die temperature, land length, die angle, and cavity shape impact the extrusion process. Proper die design is critical to ensure uniform flow of the aluminum material, prevent defects, and achieve the desired profile characteristics.
Extrusion Speed:
The extrusion speed, or the rate at which the billet is pushed through the die, affects the extrusion process. The speed should be carefully controlled to maintain a consistent extrusion temperature, prevent overheating or deformation, and achieve the desired dimensional accuracy. Optimal extrusion speed depends on factors such as the alloy being extruded, die design, and desired profile specifications.
Pressure:
The pressure applied during extrusion determines the flow of aluminum material through the die. Sufficient pressure is required to overcome the resistance and ensure proper filling of the die cavity. Controlling the extrusion pressure is crucial to avoid defects such as insufficient fill, die lines or surface imperfections.
Cooling and Quenching:
The cooling and quenching process after extrusion affects the final properties and dimensional stability of the extruded profiles. Proper cooling rates and quenching methods help achieve the desired mechanical properties, reduce internal stresses, and minimize distortion. Cooling and quenching parameters, including cooling medium, temperature, and duration, must be carefully controlled for consistent and high-quality extrusions.
Post-Extrusion Processes:
Additional post-extrusion processes, such as stretching, straightening, heat treatment, and finishing, can impact the final properties and dimensions of the extruded profiles. Each post-extrusion process must be optimized based on the specific requirements of the extruded profiles and the intended application.
Advantages of Aluminum Extrusion
- Design Flexibility: Aluminum extrusion allows for the creation of complex cross-sectional profiles with precise tolerances. It offers designers the freedom to develop customized shapes and sizes, catering to specific project requirements.
- Lightweight and Strong: Aluminum extrusions possess excellent strength-to-weight ratios, making them ideal for applications where weight reduction is crucial without compromising structural integrity. This characteristic is particularly significant in the aerospace and automotive industries.
- Cost-Effective: Aluminum extrusion is a cost-effective manufacturing process. It minimizes material waste due to its ability to create near-net shapes, reducing the need for additional machining. Moreover, aluminum is highly recyclable, further reducing costs and environmental impact.
- Corrosion Resistance: Aluminum extrusions exhibit natural resistance to corrosion, thanks to their oxide layer. This characteristic ensures durability and longevity, making them suitable for outdoor applications or those exposed to harsh environments.
- Thermal Conductivity: Aluminum has excellent thermal conductivity, making it an ideal choice for heat sinks and other cooling applications. Its ability to dissipate heat efficiently helps to extend the lifespan of electronic components.
Applications of Aluminum Extrusion
- Construction Industry: Aluminum extrusions find extensive use in the construction sector, including window frames, curtain walls, doors, and structural components. The lightweight nature of aluminum allows for easy transportation, installation, and maintenance.
- Automotive Industry: Aluminum extrusions are widely employed in the automotive industry to manufacture components such as chassis, engine parts, heat exchangers, and body panels. The lightweight characteristics of aluminum help improve fuel efficiency and reduce emissions.
- Electronics and Electrical Industry: Aluminum extrusions are utilized in the production of heat sinks, enclosures, and frames for electronic devices. The thermal conductivity and corrosion resistance of aluminum makes it an excellent choice for efficient heat dissipation.
- Aerospace Industry: Aluminum extrusions play a vital role in the aerospace industry due to their lightweight properties, high strength, and resistance to corrosion. They are used in the construction of aircraft structures, including fuselages, wings, and interior components.
Future Potential and Sustainability
The future of aluminum extrusion looks promising. Ongoing research and development efforts are focused on enhancing the process and exploring new alloys with improved properties. The use of computer-aided design and simulation techniques is further optimizing the extrusion process, leading to greater precision and efficiency.
In terms of sustainability, aluminum extrusion aligns with the growing emphasis on eco-friendly practices. Aluminum is fully recyclable, and the extrusion process consumes significantly less energy compared to primary aluminum production. The ability to reuse and recycle aluminum extrusions contributes to reducing carbon footprints and conserving natural resources.
Frequently Asked Questions Related to Aluminum Extrusion
1. What is 80-20 Aluminum Extrusion?
80/20 aluminum extrusion, also known as T-slot aluminum extrusion, is a specific type of extruded aluminum profile system that utilizes a T-shaped groove along its length. The name “80/20” refers to the proportions of the groove, where 80% of the profile’s cross-section is a solid material, and 20% is the T-slot groove.
The 80/20 aluminum extrusion system was developed by the 80/20 Inc. company, which pioneered the concept of modular aluminum framing. The T-slot design allows for easy assembly and customization using a wide range of accessories, fasteners, and connectors. This system provides flexibility and versatility in constructing various structures and frameworks, making it popular in industries such as manufacturing, automation, robotics, and industrial applications.
The T-slot groove in 80/20 aluminum extrusion profiles allows for the insertion and positioning of bolts, nuts, and other components at any point along the profile’s length. This enables quick and simple assembly, disassembly, and adjustment of structures without the need for drilling or welding. The T-slot design also provides excellent strength and rigidity while allowing for modular configurations and future modifications.
The 80/20 aluminum extrusion system offers a wide range of profile sizes, shapes, and accessories to accommodate diverse project requirements. Profiles are typically made from 6000-series aluminum alloys, known for their strength, lightweight properties, and corrosion resistance. The extrusion process allows for precise dimensions and consistent quality, ensuring compatibility and easy integration of components.
With 80/20 aluminum extrusion, designers and engineers can create customized frameworks, machine guards, workstations, shelving, display systems, and many other structures. The system’s versatility, reusability, and ease of modification make it a popular choice for applications requiring flexible and scalable solutions.
It’s worth noting that while “80/20” is a well-known brand associated with aluminum extrusion, there are other manufacturers and suppliers that offer similar T-slot aluminum extrusion systems with different brand names.
2. What is Extrusion Ratio for Aluminum?
The extrusion ratio, also known as the reduction ratio, is an important parameter in the aluminum extrusion process. It represents the ratio between the cross-sectional area of the initial billet and the cross-sectional area of the final extruded profile. The extrusion ratio is calculated using the following formula:
Extrusion Ratio = (Initial Billet Area) / (Final Profile Area)
For example, if the initial billet has a cross-sectional area of 100 square millimeters and the final extruded profile has a cross-sectional area of 20 square millimeters, the extrusion ratio would be 5:1.
The extrusion ratio provides an indication of the amount of material flow and deformation that occurs during the extrusion process. Higher extrusion ratios generally result in more severe plastic deformation and elongation of the material, leading to thinner wall thicknesses and increased length of the extruded profile.
The specific extrusion ratio used in aluminum extrusion depends on various factors, including the desired profile shape, size, complexity, and the characteristics of the aluminum alloy being extruded. Different alloys have varying extrudability and require different extrusion ratios to achieve the desired profile dimensions and mechanical properties.
The extrusion ratio is an essential consideration for achieving successful extrusions. It influences factors such as the required extrusion force, die design, die temperature, and material flow characteristics. Balancing the extrusion ratio with other process parameters helps ensure optimal extrusion results, including dimensional accuracy, surface finish, and mechanical properties of the extruded aluminum profiles.
For hard metals, the extrusion ratio ranges from 10:1 to 35:1 whereas for soft metals like Aluminum, the extrusion ratio ranges from 10:1 to 100:1.
Conclusions
Aluminum extrusion is a game-changing manufacturing process that offers numerous advantages across various industries. Its versatility, lightweight nature, strength, and cost-effectiveness make it a popular choice for designers and manufacturers. As we move towards a more sustainable future, aluminum extrusion’s recyclability and energy efficiency will continue to make it a valuable solution. With ongoing advancements, the possibilities for aluminum extrusion are vast, and it is set to remain a key player in shaping the world of modern manufacturing.