An automatic recirculation valve or ARV is a multifunctional valve. ARV ensures that a pre-determined minimum flow is transferred through a centrifugal pump at all times. So an automatic recirculation valve (Fig. 1) is basically a pump protection device. To avoid permanent damage (destruction) from cavitation and overheating (thermal damage) these valves serve a very important function.
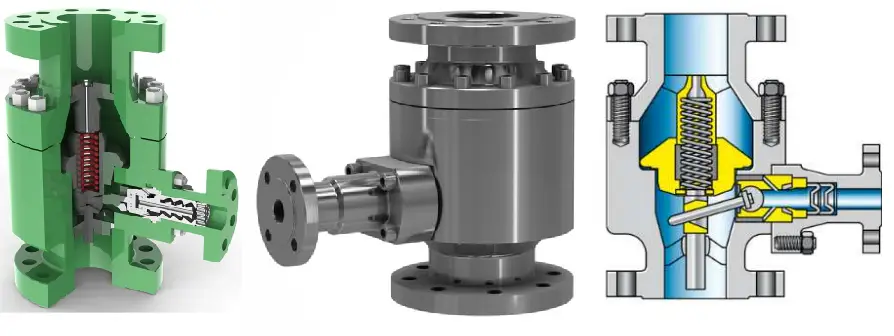
Working Principle of Automatic Recirculation Valve
The heart of the automatic recirculation valve (ARV) is a check valve disk that senses the flow rate of the fluid. The valve disk is flow-sensitive and not pressure-sensitive. It controls the fluid flow and ensures that a specified fluid volume passes through. The controlling characteristics result in a consistent and stable flow over a wide range of pressure.
At the full capacity of the valve disk, the bypass closes. Again, when the flow decreases, the action is reversed and there is an increase in the flow rate. The fluid in that situation gets into the bypass system which is controlled by the orifices and is found at the bottom of the disk.
The fluid then flows through the annulus directing it to the outlet.
The disk is lifted with an increase in the fluid flow. As a result, the bypass element which is important for the functioning of the bypass closes to limit the recirculation. This guarantees that the recirculation flow is more than the lowest volume of the flowing fluid through the pump.
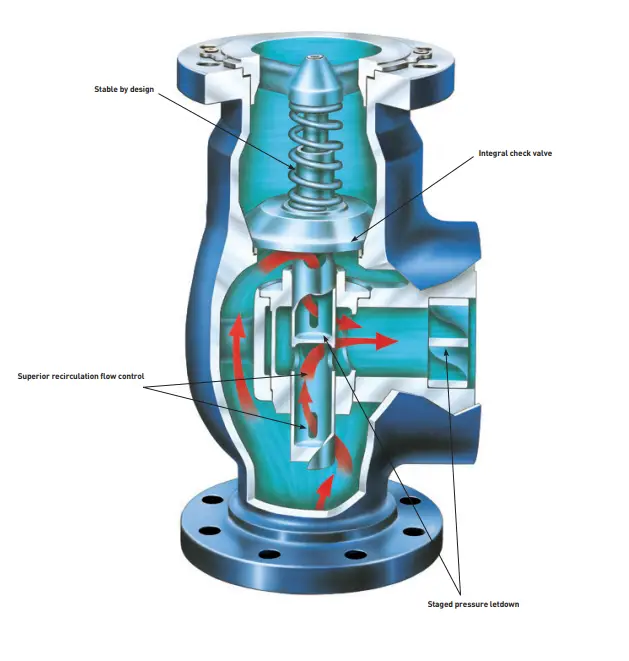
So the automatic recirculation valve sets out four functions in one body. They are:
- Flow perception: The valve disc of the ARV automatically perceives the main flow of the processing system. Then according to the flow, it determines the main valve and bypass valve disc position.
- Recirculation control: Automatic recirculation valve automatically adjust pump H – Q characteristics to realize recycling.
- Bypass multistage pressure reducing: The bypass control system of the Automatic recirculation valve reduces the backflow medium from the high-pressure pump outlet to appropriate backflow to the low-pressure storage device with low noise and small wear.
- Check: The automatic recirculation valve also provides a check valve effect that prevents the liquid backflow to the pump body.
Applications of Automatic Recirculation Valve
A common application is to protect pumps that handle hot water for boiler feeding or cooling water plants, where partial evaporation of the water content might otherwise cause the pump to run dry. Even in situations, when the flow rate of the main valve to the boiler is completely shut off, a minimum flow is maintained.
Another application of an automatic recirculation valve is to protect high-performance pumps during a start-up phase. In this scenario, several pumps are used in parallel with one on standby. The pump’s automatic recirculation valve enables the change to occur without damaging the pumps. In the Power, Paper & Pulp, Maritime, Refining, Fire protection systems, and Chemical industries, an automatic recirculation valve is widely used.
The bypass fully opens when the disk closes and there is no fluid flow. It helps to protect the pump from damage that would result if the pump continued to operate with no fluid.
Advantages of Automatic Recirculation Valve
The main advantages of an Automatic Recirculation Valve are:
- Combines both check and bypass features
- No external actuation required
- low maintenance and reliable
- Proprietary Cv calculation system
- Cavitation prevention
- Unique and stable design
- Minimum flow protection
- Easy installation
- 3 Phase Slurry and High-pressure variants available
- Eliminate external power source
- Eliminates installation and maintenance of complex conventional flow control loops
Centrifugal Pump Protection Scenarios using Automatic Recirculation Valve (ARV)
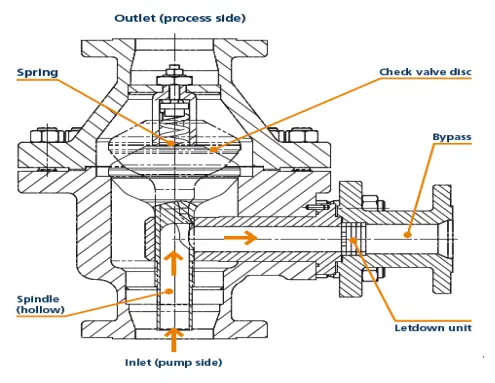
In a Centrifugal pump, the mechanical energy is transformed into pressure energy by means of centrifugal force. The impeller rotation acting on the fluid within the pump generates the centrifugal force. To avoid overheating, The pump always needs a minimum liquid flow. If the predefined minimum flow is not maintained, permanent pump damage can occur. Four different pump protection scenarios are reviewed below.
1) Non-return scenario
The pump does not have backflow prevention and therefore, the product will flow back through it once stopped. Therefore, A non-return valve (NRV) is always placed after the pump outlet. A reservoir is used to take the pump output when there is no process demand.
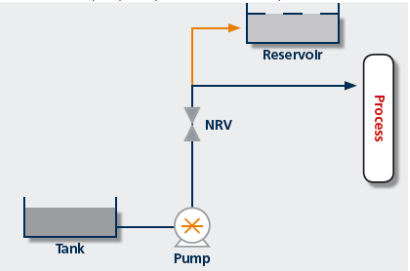
2) Continuous flow scenario
To allow the required minimum flow back to the pump inlet, A manual bypass or leakage path can be added. This is a simple and effective system, which is in constant operation and therefore is inefficient and costly (energy costs).
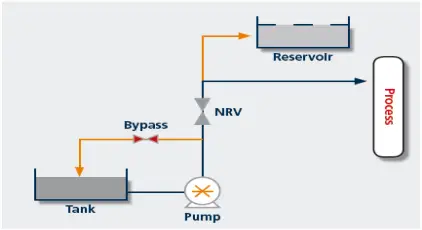
3) Control valve scenario
This comprehensive control valve solution is highly effective. In this scenario, a flow control valve is connected to a flow meter and allows the mainline flow to be metered. The control valve opens when the mainline flow decreases which allows the correct minimum flow required. However, this is a highly capital-intensive solution. It requires flow metering equipment, control, and non-return valves. No reservoir is required.
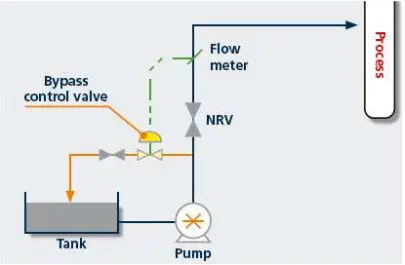
4) Automatic Recirculation Valve solution
The previous approach is costly and stands and falls within the integrity of the control system. An alternative and safer system are to combine the non-return valve, the bypass valve, and the control valve into an interconnected unit, known as “the automatic recirculation valve”. This valve closes during the no-flow condition automatically opening the bypass line, which is sized for minimum flow. When the mainline takes flow but less than the minimum, the bypass line, and the mainline are both partially open.
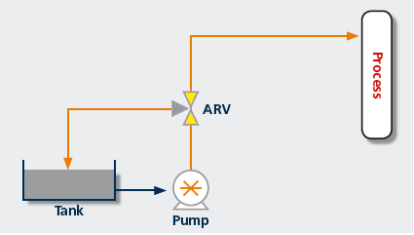
About the Author: Part of this article is prepared by Ms. Namita Modak, a Chemical Engineer with 14+ years of experience. Click here to know more about her.
Dear Mr. Dey . Ever thanks for your valuable post. Also request you to please confirm the details of manufacturers of this types of valves.
I would like to ask the following:
Regarding some pumps with very high specific sucction spedd (Nss) over 11,000. Here it is necessary to operate the pump very close to its BEP, otherwise the pump may suffer from cavitation and hydrodynamic problems that will make its operation unstable. Here the objective is not to maintain a minimum flow but rather to have the pump work very close to its BEP. If the process demands less flow than the BEP, the difference should be recirculated. For this case an ARV valve may be appropriate.??
Will this valve provide protection against pump staring against no head and run down the curve?
Hi
Dear Sir
Do you have any test procedure for ARV.
How I can modeling the ARC and BPV in Pipe-Flo software
Hello Mr.Anup Kumar,
Thanks for such good posts. It helps the Engineers a lot.
Please clarify me the below.
For commissioning, i need to do a pump performance test. during that time, all the destinations will not be requiring water. so, the pump load or water flow will be lesser but more than minimum pump flow capacity. Now, if i want to do the pump performance test at Pump rated flow, will the ARC valve open to pass the partial flow in recirculation line? or How i can do the pump performance test in this regard?
Thanks,
Tamilselvan D