When designing a system that controls the fluid flow, you’ll probably need to choose between a ball valve and a butterfly valve. Both these valves find applications in various industries, and each has its set of benefits. To choose the right product for your system, you must understand the butterfly vs ball valve features, working principles, advantages, and disadvantages.
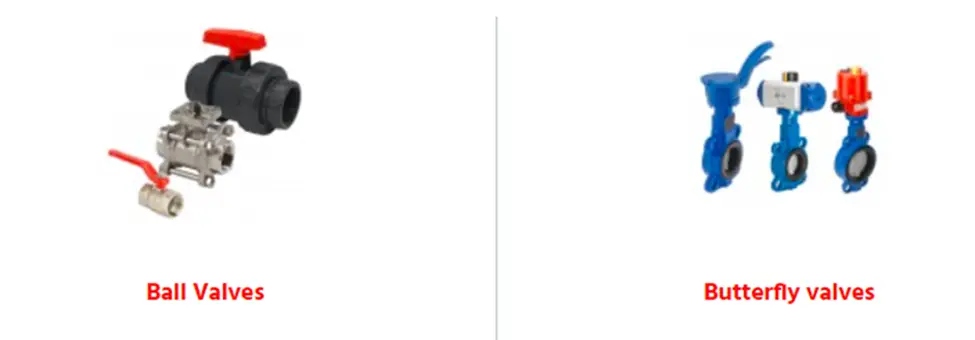
Understanding Ball Valves and Butterfly Valves
Ball valves and butterfly valves are considered some of the simplest control valves in the market. They are compatible with different fluid mediums and are used across a broad range of temperatures and pressure. Both valves are quarter-turn, meaning a 90-degree rotation will take the valve from fully open to fully close and vice versa. They can also be controlled manually or using electric, pneumatic and hydraulic actuators. Affordability, easy maintenance, reliability, and durability make these valves more widely accepted than the other types. Let’s look at each of these valves.
Butterfly Valve
Butterfly valves have a disc driven by a hand wheel or lever. The disc sits perpendicular to the fluid flow direction when it’s closed, while a seal sits on the valve body to ensure tight and secure closure. The stem position while opening or closing the valve is often directly proportional to the flow rate.
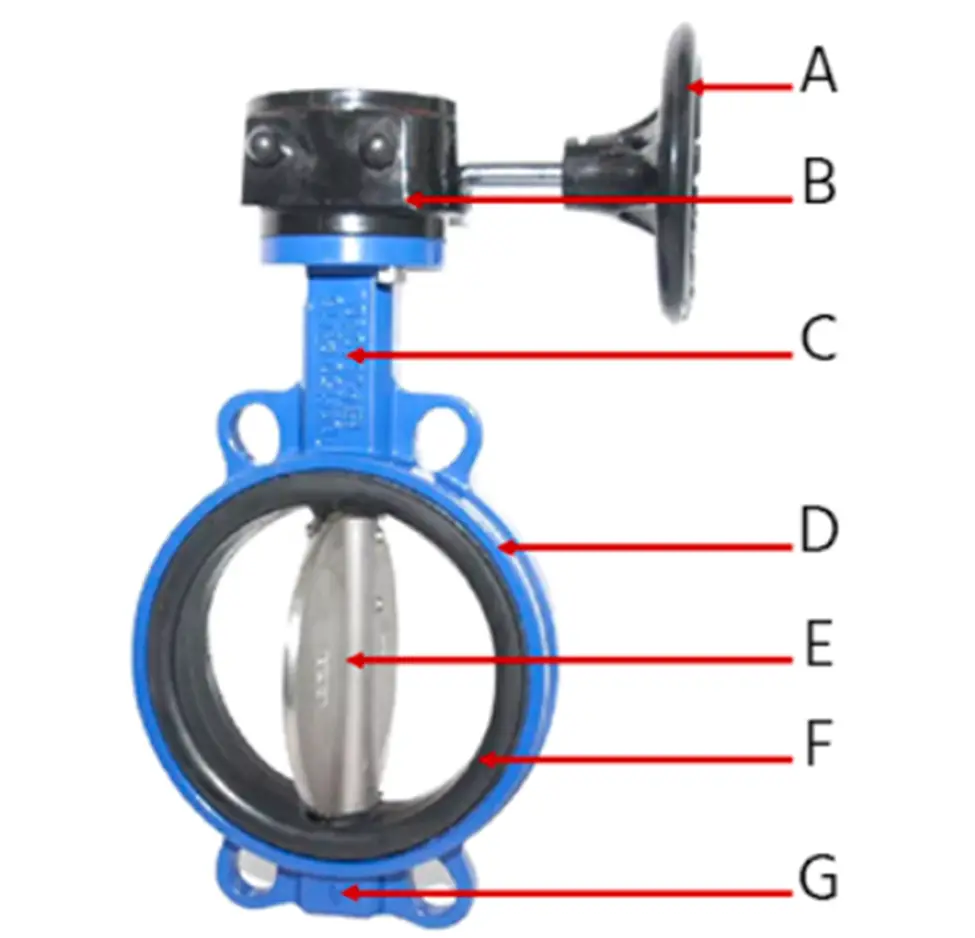
Butterfly valves are lightweight, have the least parts, and require little support. Similarly, they are cheaper than ball valves, especially beyond a certain diameter size. However, they aren’t suitable for high-pressure applications since high-pressure differences between the valve’s seal and the sides make it difficult to open the valve. A solution is to use a bypass valve to balance this pressure difference and enhance a smooth operation.
Since the disc interrupts fluid flow even when it’s fully open, there’s some pressure drop across the valve, limiting its ability for use in certain applications, e.g., pigging. They are also limited to ON/OFF operation and cannot be used for high-precision fluid control.
Ball Valve
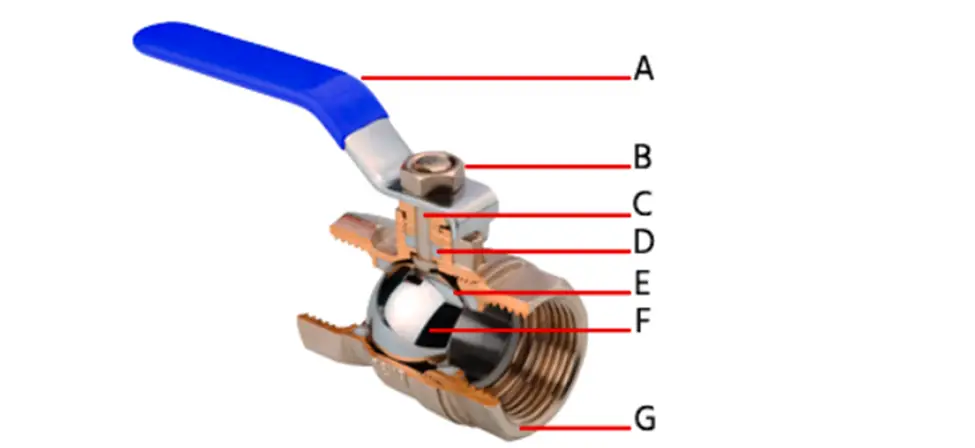
Ball valves have a hollow spherical ball held in position at one or both ends. A shaft is attached to the top end of the ball, allowing for a rotation that either opens or closes the valve. When the valve is fully open, the hole lies parallel to the fluid flow direction. The ball sits on a seat inside the valve body and can have a two-way, three-way, or four-way flow directions.
The hole in a ball valve will vary depending on the application. This hole will also feature different designs, such as a V-port and a full-port design. A V-port design guarantees stable flow control while a full port valve allows zero or near-zero pressure drop. If the bore size is less than the pipe diameter, the flow will experience some pressure drop.
Compared to butterfly valves, ball valves don’t experience leakages when fully closed. They also open easily when there’s a high differential pressure on the valve’s sides; hence do not require a bypass valve.
Advantages and Disadvantages of Butterfly Valve vs Ball Valve
While butterfly valves and ball valves have several similarities, some differences make one valve stand out in certain applications. We have rounded up the main pros and cons of both valves below.
Weight and size:
Ball valves are heavy and require significant support, while butterfly valves are lighter even at larger pipe diameters. Butterfly valves are highly recommended for applications that require larger pipe diameters (i.e., those above DN 150). The ball valve works well for size diameters below DN 50.
Leakage:
Ball valves offer a tight seal for high-pressure applications, while butterfly valves are prone to leakages at relatively high pressures.
Installation Space:
Butterfly valves have a smaller installation footprint than ball valves.
Cost:
Butterfly valves are cheaper than ball valves, especially for larger-diameter sizes.
Connection Style:
Ball valves have a wide range of connection types with flanges or threads, while butterfly valves are limited to flange style with a wafer or lug design.
Flow Control:
Ball valves are ideal for ON/OFF control and modulation purposes. It also comes with a full port valve design option that eliminates pressure drop in the valve. On the other hand, butterfly valves are only suitable for ON/OFF control, plus the valve disc restricts fluid flow, creating some pressure drop.
Butterfly Valve vs Ball Valve
The above discussions on the major differences between butterfly valves and ball valves can be provided in a tabular format as below:
Parameter | Butterfly Valve | Ball Valve |
Weight | Butterfly Valves are Light Weight Valves. Hence, transfers less load to pipe supports. | Heavy Weight is the characteristic of Ball Valves |
Structure | The butterfly valve consists of a thin disk in a thin body. Simpler design. | Ball valves have a sphere-like disc inside a bulky body. Complex design. |
Space Requirement | The installation Space requirement of the butterfly valve is less. | Ball valves need more installation space than butterfly valves. |
Leakage | At high differential pressure, butterfly valves are prone to leakage. | Ball valves provide a tight seal. |
Flow Restriction | The butterfly valve disc restricts the flow by creating a large pressure drop. | Ball valves have less pressure drop as compared to butterfly valves. |
Application | Suitable for ON/OFF control and proportional control | Suitable for modulating and ON/OFF Control. However, they are more used for isolation purposes. |
Cost | Butterfly valves are cheaper | Ball valves are expensive |
Connection | Butterfly valves have a flange style with a lug or wafer design | A range of connections is available for ball valves. |
Uses | Used for Liquid service applications | Ball valves are capable of handling both liquid and gas. |
Operating Condition | Mainly used for low-temperature and pressure services | Suitable for high temperature and pressure services |
No of Ports | Butterfly valves can have only two ports | Ball valves can have more than two ports. |
Summary
When selecting between a ball valve and a butterfly valve, you should consider all the product features, ideal use cases, and pros and cons. Understanding your system requirements and valve design expectations will also help you in decision-making.
The number of ports required, flow regulation, flow capacity, and operating conditions is the key factors to consider. You also want to choose a product from a reputed manufacturer that has a positive track record in the market. Seeking professional guidance during the selection process is highly recommended, especially if you are new to fluid control.
Thanki you Sir…for enriching my knowledge as it has assisted me a lot
I recognise your picture, I must have read your guides before. As a process engineer with ~8 years experience this information is very valuable to bring me up to speed on the basics that I’ve not worked with much so far, but that are key to developing as an engineer. Thanks!
thank you for your knowledge free share!