This article will highlight a few of the points that are required to be checked while reviewing the Shell & Tube Heat exchanger. The list is not exhaustive but provides a simple guideline for beginners.
Basic Checks for Shell & Tube Heat Exchanger
- Check the Pressure Design Code to be applied and Applicable local regulations to be applied.
- Check completeness and correctness of the information, dimension, impingement plate, gasket recommendation, the applicability of IBR, TEMA type and configuration, etc. are available on the datasheet.
- Maximum design temperature and minimum design metal temperature
- Ensure the latest issue of the process data sheet is followed.
- Check if any specific notes to be highlighted like anodic protection or sloping shell, any special service requirements like NACE/Sour service, etc. are applicable which puts restrictions on material requirements.
- Ensure adequacy of shell Internal Diameter to accommodate all tubes with given pitch and orientation, the required number of tie rods, considering the provision of impingement plate, minimum U tube radius, and groove width, ligament as per TEMA recommendation is checked before starting design work.
- Design codes including wind, seismic load, and any reference books with edition number and year of publication and amendments if any have been specified and used in the calculations.
- Applicable standard specifications, Job specifications, and standards with their revision numbers.
- Nozzle schedule indicating the size, rating, and nozzle neck thickness, projections and surface finish of gasket surface of nozzle flange (projection to suit insulation thickness and facing to suit gasket material), Nozzle location, Orientation, etc.
- Test pressure including any temperature correction
- The drawing block, drawing number, and distribution are in line with the project procedure.
- Reference drawing numbers of standard drawings are indicated if details are not given on the drawing.
- The reference datasheet number with the latest revision is indicated in the drawing.
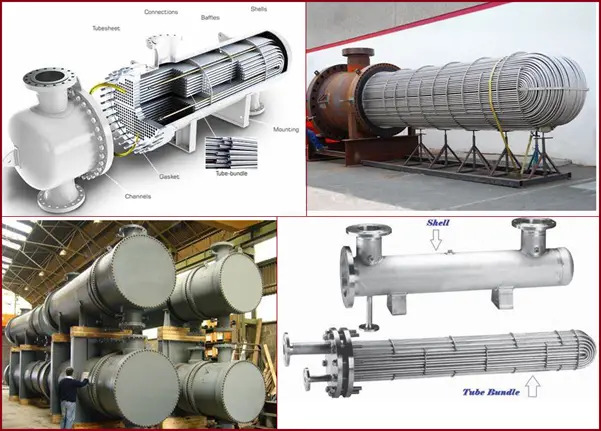
- Provision of Instrument connection as per TEMA and Provision of vent or drain connection for testing
- Support details (lugs, saddles) indicating size, numbers & PCD of foundation bolts. Foundation bolts are to be specified with their size and thread pitch in mm.
- Typical applicable weld details of plates, Nozzles, and other attachments depending upon the material of construction, and the thickness of parts. (Special attention required. for cladding/lining)
- Provision of standard attachments like Nameplate, Earthing boss,
- Tube expansion requirements for strength welded tubes.
Adequacy and applicability of general notes
- Ensure that the statement “In general the provisions of ASME / TEMA have to be followed in addition to the local company specification.”
- On-site storage is required for more than 12 months prior to installation.
- Surface preparation and painting, the surface finish of flange faces with respect to specified gaskets to be specifically checked
- In the case of the stacked heat exchanger, a note stating that the final hydro-test shall be conducted in a stacked condition must be added.
- Surface preparation and protection requirements
- For stacked heat exchangers, the requirement of shim plates as required for adjustment shall be included.
- Sliding support anchor bolts should be hand tightened and for high-temperature exchanger Teflon / graphite/Stainless steel sheet below sliding saddle to be indicated with the responsibility of its provision by the supplier.
- Grooving requirements for shell side clad tube sheets.
- In the case of the cryogenic exchanger, wooden saddles/Foam glass of adequate thickness below saddle plates are to be indicated.
TEMA minimum requirements for Shell & Tube Heat Exchanger
- Shell, channel thickness,
- Tie rods – Nos. & diameters.
- Baffles – thickness
- Partition Plates thickness
- Grooves /Steps
- Tube Holes, Bolt size,
- Impingement Plate,
- Minimum gasket width & minimum acceptable bolt diameter.
- Check if the test ring is included for ‘U’ tubes kettle type & floating heat exchangers. The testing arrangement as required for other types has also been included in the supplier’s scope.
- Chemical cleaning connections requirements, Thermowell connection requirements, Pressure gauge connection requirements
- Check if lifting lugs, jack screws, and locating pins are provided.
In the case of ‘U’ tubes
- The smallest radius of the tube bend not to be less than 1.5 times the O.D. of the tube
- Check the requirement of Heat Treatment for the inner two rows for C.S. tubes bend
- Check the requirement of solution annealing of S.S. tube bends
- For large diameter, bundles check for U-tube rear support requirements.
- Check the tube-to-tube-sheet joint critically with respect to joint requirements as per ASME Sec. VIII div-1 appendix ‘A’ provisions.
- Check details for Tie rods, spacers, runner bars, sliding strips, and sealing strips (if applicable are indicated)
- Check vent/drain notches are provided on baffles in the Horizontal Heat exchanger.
- Check if pulling/lifting arrangement is provided for removable tube bundles and clear space required for pulling bundle is shown in dotted in the schematic.
- Check vent/drain holes are provided at the highest & lowest points on pass partition plates.
- If an expansion bellow is required, proper details are included for design by a specialist vendor including the applicable design codes.
- For vertical heat exchangers which require expansion bellows, a note near the expansion bellow sketch must indicate the minimum civil cut-out size required to clear the tie-rod lugs (For this purpose assume that the bellows design by the vendor will have the tie-rod provision)
- Check section lines are appropriate for materials of construction.
Check about Hold List
- Instrument Nozzles
- Orientation of nozzles
- The orientation of attachment like a) Lifting lugs b) Nameplate, Earthing boss
- Orientation foundation bolts / support lugs / saddle & Position of fixed & sliding support
- Check completion and correctness of Nozzle Orientation
- Specific requirements of relative locations are maintained as per process datasheet
- If some special gasket or its equivalent has been specified, fix the criteria of equivalence in the job specification.
- Post weld heat treatment required for process reasons or for weld overlaid bonnet or channel
- Ensure that nozzle orientation also indicates the expansion bellows tie-rod lugs orientation
- Ensure that squad-check comments are incorporated
- Ensure that drawing is in line with P & ID and equipment modeling.
- The number of cycles to be considered for the bellows expansion joint design.
- Fatigue analysis is required for flanged and flued expansion joints, and the number of cycles is to be considered.
- Additional requirements for low chrome steels in high temp. or high-pressure hydrogen service.
- Materials of construction.
- Weight (empty, full of water and operating)
- Painting requirement.
Few more Resources for you..
Various Articles related to Heat Exchangers
Articles Related to Pumps
Piping Design and Layout
Piping Stress Analysis
Piping Materials
Great info, One thing I was looking for but did not find is the preferred way to pipe a tube & shell heat exchanger, I have a problem with 2 buildings connected with a central boiler plant. both are water source heat-pump loops, both heat exchangers are approx 6 years old.
1 heat exchanger is piped with the boiler water flowing thru the shell and it has more than enough capacity. the other has the boiler water piped thru the tubes and it struggles to reach 20-30 F temp rise. the associated piping and valves are installed correctly. My next step is to open it up to see whats going on inside and install pressure gauges. I apologize, I know this is not a trouble shooting forum and I appreciate you reading this, when I have access to an expert I have to ask. thank you in advance for your reply, or not
Piping engineer Execution and equipment or maintenance or QC
Can you give me information about fabrication heat exchanger
Is there any standard for requirement of drain and vent in shell & tube and plate type heat exchanger?
and if not than, How we decide that vent and drain to be provided or not?
Hi, I am designing test ring of heat exchanger . Kindly tell me any standard that is showing complete procedure of designing and geometric construction other than TEMA and ASME standards .
Thanks &Regards
Mechanical Engineer