Compression fittings are indispensable components used in various industries, from plumbing and HVAC systems to automotive and pneumatic applications. These versatile fittings provide a reliable and leak-proof connection between two pipes or tubes without the need for soldering or welding. In this blog article, we will delve into the world of compression fittings, exploring their functionality, types, materials, installation, advantages, and common applications.
What are Compression Fittings?
Compression fittings are mechanical devices designed to connect two pipes or tubes securely, ensuring a tight and leak-resistant joint. They consist of three main components: a compression nut, a compression ring (also known as a ferrule or olive), and the fitting body. The compression nut, typically made of brass or other durable materials, tightens onto the fitting body, compressing the ring against the pipe or tube to form a seal.
Types of Compression Fittings
There are several types of compression fittings available, each tailored to specific applications and pipe materials:
- Standard Compression Fittings: These are the most common type of compression fittings and work with copper, stainless steel, or plastic pipes. They are widely used in plumbing and HVAC systems.
- Flareless Compression Fittings: Flareless fittings have a conical seat and are ideal for high-pressure applications, such as hydraulic systems. They work well with steel, stainless steel, and other metal pipes.
- Threaded Compression Fittings: These fittings come with threads on one end, allowing them to be screwed onto pipes with compatible threads. They are commonly used in gas and fluid lines.
Again depending on the type of pipe fitting, compression fittings can be grouped as follows:
- Compression Elbow Fittings
- Compression Tee Fittings
- Compression Union and Coupler Fittings
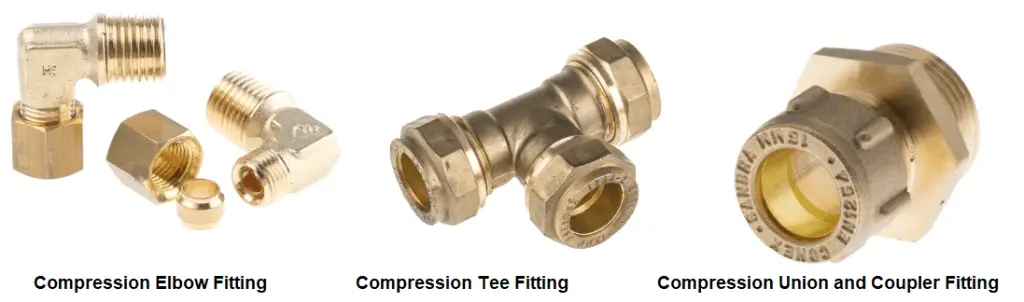
Materials Used in Compression Fittings
Compression fittings are typically crafted from robust materials that ensure durability and longevity. Common materials include:
- Brass: Brass compression fittings are widely used due to their excellent corrosion resistance, making them suitable for both indoor and outdoor applications.
- Stainless Steel: Stainless steel compression fittings are suitable for aggressive environments and high-temperature applications.
- Copper: Copper compression fittings are common in plumbing systems due to their compatibility with copper pipes.
- Plastic: Compression fittings made from plastic materials, such as nylon or PVC, are often used in low-pressure applications or where corrosion resistance is crucial.
How Does a Compression Fitting Work?
A compression fitting works on the principle of using mechanical pressure to create a tight and leak-proof connection between two pipes or tubes. It consists of three main components: a compression nut, a compression ring (also known as a ferrule or olive), and the fitting body. When these components are assembled correctly, the compression fitting forms a secure joint that effectively seals the connection.
It is essential to follow the manufacturer’s guidelines for the specific compression fitting being used, as over-tightening can damage the fitting and cause leaks, while under-tightening may result in an ineffective seal.
Installation Process
The proper installation of compression fittings is crucial to ensure an effective seal and prevent leaks. Here’s a step-by-step guide on how to install compression fittings:
- Measure and Cut: Measure the pipe or tube accurately and use a tubing cutter to cut it to the desired length, ensuring clean and burr-free edges.
- Insert the Compression Ring: Slide the compression ring onto the pipe, ensuring it sits squarely against the pipe end.
- Insert the Pipe into the Fitting: Insert the pipe into the fitting body until it bottoms out.
- Tighten the Nut: Thread the compression nut onto the fitting body and tighten it by hand. Then, use a wrench to make a quarter to a half turn to achieve a secure connection.
- Check for Leaks: After installation, carefully inspect the connection for any signs of leakage.
Advantages of Compression Fittings
Compression fittings offer several advantages, making them a preferred choice in many applications:
- No Welding or Soldering: Unlike traditional methods like soldering or welding, compression fittings do not require heat or specialized tools for installation, making them quicker and safer to use.
- Reusability: Compression fittings can be easily disassembled and reassembled, allowing for adjustments or replacements without damaging the fitting.
- Leak Resistance: When installed correctly, compression fittings provide a reliable and leak-proof connection, minimizing the risk of costly leaks and system failures.
- Versatility: With various materials and types available, compression fittings can accommodate a wide range of pipes and tubing, offering great versatility.
Common Applications
Compression fittings find applications in diverse industries and systems, including:
- Plumbing: Compression fittings are widely used in household plumbing for connecting copper or plastic pipes.
- HVAC Systems: They are employed in air conditioning and heating systems to connect refrigerant lines.
- Pneumatic Systems: Compression fittings are used in pneumatic systems to connect air tubes and control the flow of compressed air.
- Hydraulic Systems: In hydraulic systems, compression fittings provide leak-proof connections for high-pressure fluids.
- Automotive: Compression fittings are utilized in fuel lines, brake systems, and hydraulic clutches.
How much Pressure can a Compression Fitting withstand?
The pressure that a compression fitting can withstand depends on various factors, including the material of the fitting, the type of compression fitting, the pipe or tube material, and the specific design and construction of the fitting. Generally, compression fittings are designed to handle a wide range of pressures, but the maximum pressure rating may vary for different fittings and manufacturers.
Here are some general guidelines on pressure ratings for compression fittings based on common materials:
- Brass Compression Fittings: Brass is a commonly used material for compression fittings. Standard brass compression fittings can typically handle pressures up to 1,000 to 1,200 psi (pounds per square inch) for water applications and around 600 to 800 psi for oil or gas applications.
- Stainless Steel Compression Fittings: Stainless steel compression fittings are often used in higher-pressure applications. They can handle pressures ranging from 3,000 to 6,000 psi, depending on the specific design and size of the fitting.
- Copper Compression Fittings: Copper compression fittings are commonly used in plumbing applications. They can handle pressures up to 1,000 psi or more, depending on the fitting design and pipe size.
It is essential to note that these pressure ratings are general guidelines and may vary based on the specific manufacturer’s specifications and the design of the fitting. Always refer to the manufacturer’s documentation and guidelines for accurate pressure ratings for a particular compression fitting.
Additionally, the temperature of the fluid or gas being transported through the fitting can also impact its pressure-handling capabilities. High temperatures can affect the material properties and performance of the fitting, potentially reducing its pressure rating.
When selecting a compression fitting for a specific application, it is crucial to consider the working pressure of the system and ensure that the chosen fitting can handle the intended pressure without compromising safety and performance. If the application requires higher pressure ratings, it might be necessary to consider alternative fittings or connectors specifically designed for high-pressure systems, such as flareless fittings or other specialized connectors.
Disadvantages of Compression Fittings
While compression fittings have numerous advantages, they are not without their drawbacks. It is essential to consider these disadvantages before using compression fittings in specific applications:
- Potential for Leakage: Although compression fittings are designed to provide leak-resistant connections, they are not entirely foolproof. Improper installation or overtightening of the compression nut can lead to small gaps or cracks in the compression ring, resulting in leaks over time.
- Limitations in High-Pressure Applications: While compression fittings are suitable for many applications, they may not be the best choice for extremely high-pressure systems. In such cases, specialized fittings like flareless fittings or other high-pressure connectors may be more appropriate.
- Pipe Material Compatibility: While compression fittings work well with various materials such as copper, plastic, and stainless steel, they may not be compatible with all pipe materials. Some materials can be prone to deformation or damage when subjected to the compressive force of the fitting, leading to potential leaks.
- Reusability Concerns: While compression fittings are generally reusable, their effectiveness can diminish with each disassembly and reassembly. The compression ring can deform or become damaged after multiple uses, leading to potential leaks and the need for replacements.
- Skill-Dependent Installation: Proper installation of compression fittings requires a certain level of skill and attention to detail. If not installed correctly, there is a higher risk of leaks, compromising the system’s efficiency and safety.
- Susceptibility to Vibrations: In applications where pipes or tubes are subjected to frequent vibrations, such as in automotive or industrial settings, the constant movement can cause the compression fittings to loosen over time, leading to potential leaks.
Conclusion
Compression fittings play a vital role in creating reliable and leak-resistant connections in various industries. Their simple yet effective design, combined with the ability to accommodate different materials, makes them indispensable for countless applications. By understanding the types, materials, and proper installation process of compression fittings, professionals can ensure secure connections, enhancing system efficiency and safety. When used correctly, compression fittings provide a dependable solution for joining pipes and tubes, simplifying maintenance, and reducing downtime in a wide range of industrial and domestic settings.