In today’s rapidly evolving world, scientific advancements have led to breakthroughs in various fields, including energy, medicine, and aerospace. Among these innovations, cryogenic storage tanks stand out as remarkable feats of engineering. These tanks play a crucial role in the safe and efficient storage of liquefied gases at extremely low temperatures. Cryogenic tanks are also known as cryo tanks. In this blog article, we will explore the fascinating world of cryogenic storage tanks, their design, applications, and their contribution to technological progress.
What are Cryogenic Tanks?
Cryogenic storage tanks are specially designed containers used to store and transport liquefied gases, such as nitrogen, oxygen, argon, helium, and hydrogen, at extremely low temperatures. These tanks utilize the principle of cryogenics, which involves the study and application of materials and processes at extremely low temperatures, typically below -150 degrees Celsius (-238 degrees Fahrenheit). Cryogenic tanks are manufactured in various sizes and shapes depending on requirements.
As already stated the following substances are stored in cryogenic tanks:
- LIN (liquid nitrogen)
- Liquid nitrous oxide (LN2O)
- LOX (Liquid Oxygen)
- LAR (Liquid Argon)
- Liquid CO2 (Carbon Dioxide)
- LNG (Liquefied Natural Gas)
- LPG ( Liquefied Petroleum Gas)
- LHe (Liquid Helium)
- LH2 (Liquid Hydrogen)
- Liquid Ethylene
Design and Construction of Cryogenic Tank
The design and construction of cryogenic storage tanks are critical to ensuring the safe containment of liquefied gases. These tanks are typically constructed from high-grade materials that can withstand low temperatures and maintain structural integrity. Common materials used include stainless steel, aluminum, and specialized alloys like Inconel, Monel, etc.
The tanks are double-walled with an inner vessel that holds the liquefied gas made of stainless steel and an outer vessel that acts as an insulating layer made of carbon steel. The space between the inner and outer vessel is filled with a vacuum or a highly efficient insulating material, such as perlite or foam, to minimize heat transfer and prevent the escape of stored gases.
To maintain the extremely low temperatures required, cryogenic storage tanks are often equipped with a system that allows for the circulation of cryogenic fluids, such as liquid nitrogen or liquid helium, to cool the inner vessel and maintain the desired temperature. Fig. 1 (Image Credit: https://www.linde-engineering.com/) below shows some typical images of cryogenic storage tanks.
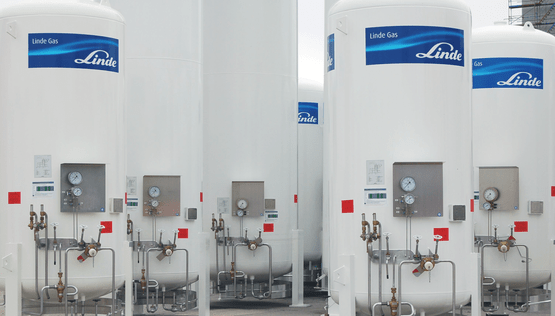
Applications of Cryogenic Tanks
Cryogenic storage tanks find widespread applications in various industries due to their ability to store large quantities of liquefied gases efficiently. Some notable applications include:
Industrial Gases:
Cryogenic storage tanks are used to store and supply industrial gases like oxygen, nitrogen, and argon, which are essential in manufacturing processes, metal fabrication, and pharmaceutical production.
Energy and Power:
Liquefied natural gas (LNG) is stored in cryogenic tanks to facilitate its transportation and use as a cleaner energy source. These tanks enable the safe storage and transportation of LNG, ensuring its availability in regions where pipelines are not economically viable.
Aerospace and Defense:
Cryogenic storage tanks play a crucial role in the aerospace industry, where they are utilized to store propellants for rockets and spacecraft. The extremely low temperatures allow for higher storage densities, enabling longer missions and more significant payloads.
Medical Applications:
Cryogenic storage tanks are used in medical facilities to store and transport cryopreserved biological materials, including stem cells, tissues, and organs, for research and transplantation purposes. These tanks provide a reliable environment for maintaining the integrity and viability of these critical materials.
Benefits of Cryogenic Storage Tanks
Cryogenic tanks offer several advantages that make them essential in various industries and applications. Here are some key advantages of cryogenic tanks:
Efficient Storage:
Cryogenic tanks enable the efficient storage of large quantities of liquefied gases. At cryogenic temperatures, gases condense into a liquid state, significantly reducing their volume. This allows for higher storage densities, enabling the transportation and storage of substantial amounts of gases economically.
Temperature Preservation:
Cryogenic tanks are designed to maintain extremely low temperatures, typically below -150 degrees Celsius (-238 degrees Fahrenheit). The double-walled construction, insulation systems, and cooling mechanisms ensure minimal heat transfer, preserving the low-temperature environment necessary for storing liquefied gases. This extends the shelf life and maintains the integrity of the stored substances.
Versatile Applications:
Cryogenic tanks find applications in various industries. They are used to store and supply industrial gases like oxygen, nitrogen, and argon, which are vital for manufacturing processes and diverse industrial applications. Cryogenic tanks are also utilized in the energy sector to store and transport liquefied natural gas (LNG), providing an efficient and cleaner energy source. Additionally, cryogenic tanks play a critical role in aerospace, medical, and scientific research, supporting space missions, cryopreservation of biological materials, and cryogenic experiments.
Safety and Reliability:
Cryogenic tanks are designed with safety as a paramount consideration. The robust construction materials and design features ensure the containment of liquefied gases under high pressures and low temperatures. Proper insulation systems minimize the risk of leaks, and safety valves are incorporated to relieve pressure if necessary. These tanks undergo rigorous testing and inspection to ensure their reliability and compliance with stringent safety standards.
Long-Term Storage:
Cryogenic tanks are suitable for the long-term storage of gases and cryopreserved materials. The low temperatures prevent degradation and maintain the stability and viability of the stored substances over extended periods. This makes cryogenic tanks invaluable for storing and preserving biological samples, tissues, organs, and other critical materials for medical research and transplantation.
Technological Advancements:
Cryogenic tanks continue to benefit from ongoing technological advancements. Research and development efforts are focused on improving insulation materials, enhancing structural integrity, and developing advanced monitoring and control systems. These advancements contribute to increased efficiency, safety, and reliability of cryogenic storage, enabling more precise temperature control and optimized operations.
Challenges and Future Developments
Designing and operating cryogenic storage tanks present certain challenges. One significant challenge is preventing the loss of stored gases due to the permeation of gases through the tank walls. Engineers are continuously working on developing advanced materials and techniques to improve insulation properties and reduce heat transfer rates.
In terms of future developments, there is ongoing research to enhance the efficiency and safety of cryogenic storage tanks. This includes the exploration of new materials, such as graphene, which could offer improved insulation and structural properties. Additionally, the use of advanced sensors and monitoring systems will enable real-time tracking of temperature, pressure, and gas levels, enhancing safety and operational efficiency.
Safety Requirements for Cryogenic Tanks
Safety is of paramount importance when it comes to the design, operation, and maintenance of cryogenic tanks. Given the extremely low temperatures and the nature of the stored substances, specific safety requirements must be met to ensure the protection of personnel, the environment, and the integrity of the tanks. Here are some key safety requirements for cryogenic tanks:
Ventilation and Gas Detection:
Adequate ventilation is essential to prevent the buildup of potentially hazardous gases in enclosed areas. Proper ventilation systems should be in place to ensure the removal of any leaked gases or vapors. Additionally, gas detection systems should be installed to monitor the concentration levels of gases and provide early warnings in case of leaks.
Pressure Relief Systems:
Cryogenic tanks should be equipped with pressure relief valves or devices to prevent over-pressurization. These valves are designed to open and release excess pressure in the event of a malfunction or an abnormal increase in pressure, ensuring the integrity of the tank and preventing catastrophic failures.
Fire Prevention and Protection:
Cryogenic gases can present fire hazards under certain conditions. Fire prevention measures, such as avoiding open flames, sparks, or smoking in the vicinity of cryogenic tanks, should be strictly enforced. Adequate fire protection systems, including fire extinguishers and fire suppression systems, should be available and maintained in case of emergencies.
Insulation Integrity:
The insulation systems of cryogenic tanks play a vital role in maintaining low temperatures and preventing heat transfer. Regular inspections and maintenance of the insulation materials and seals are crucial to ensure their integrity. Damaged or deteriorated insulation should be promptly repaired or replaced to maintain the effectiveness of the tank’s insulation system.
Personal Protective Equipment (PPE):
Proper PPE should be provided to all personnel working with or in the vicinity of cryogenic tanks. This may include thermal gloves, face shields, safety glasses, and insulated footwear. Training on the proper use of PPE and safety procedures should be provided to all individuals involved.
Emergency Response Planning:
Adequate emergency response plans should be developed and communicated to all personnel. These plans should outline procedures for handling leaks, spills, fire incidents, and other emergencies. Training and drills should be conducted regularly to ensure that personnel are prepared to respond effectively in case of an emergency.
Training and Competency:
Personnel involved in the operation, maintenance, and handling of cryogenic tanks should receive appropriate training to understand the hazards associated with cryogenic substances and safe operating procedures. This includes proper handling techniques, use of safety equipment, and understanding the risks associated with cryogenic temperatures.
Compliance with Regulations:
Cryogenic tanks are subject to various national and international regulations and standards. It is essential to comply with these regulations, which may include design standards, inspection requirements, and record-keeping obligations. Adhering to these regulations helps ensure the safe operation and maintenance of cryogenic tanks.
Cryogenic Tank Manufacturers
There are several reputable manufacturers of cryogenic tanks that provide high-quality and reliable products. Here are some well-known cryogenic tank manufacturers:
- Chart Industries: Chart Industries is a global leader in cryogenic equipment and technology. They offer a wide range of cryogenic storage and transportation solutions, including bulk storage tanks, transportable tanks, and cryogenic containers. Chart Industries has a strong reputation for innovation and has been serving various industries for over five decades.
- Air Products and Chemicals, Inc.: Air Products is a multinational corporation specializing in industrial gases and related equipment. They manufacture cryogenic storage and transportation tanks for various applications, including medical, food processing, and semiconductor industries. Air Products is known for its expertise in cryogenics and its commitment to safety and reliability.
- Linde plc: Linde is a global leader in industrial gases and engineering. They provide a wide range of cryogenic equipment and services, including cryogenic storage tanks, vaporizers, and gas distribution systems. Linde has extensive experience in cryogenic technology and offers tailored solutions to meet the specific needs of different industries.
- Taylor-Wharton: Taylor-Wharton is a renowned manufacturer of cryogenic equipment and storage systems. They offer a comprehensive range of cryogenic tanks, including bulk storage tanks, transportable containers, and micro bulk systems. Taylor-Wharton is known for its commitment to quality, innovation, and customer satisfaction.
- Cryofab, Inc.: Cryofab specializes in the design and manufacture of cryogenic equipment, including cryogenic tanks, dewars, and cryogenic piping systems. They cater to various industries, including medical, research, and industrial applications. Cryofab is recognized for its customized solutions and high-quality craftsmanship.
- Praxair, Inc. (Now part of Linde plc): Praxair, now part of Linde plc, is a leading global supplier of industrial gases and related technologies. They offer a range of cryogenic storage and transportation solutions, including bulk tanks, micro bulk systems, and cryogenic cylinders. Praxair has a strong presence in the cryogenic industry and delivers reliable solutions to meet customer needs.
Cryogenic Tank Cost
The cost of cryogenic tanks can vary significantly depending on several factors such as the size, capacity, material, design specifications, and additional features required for specific applications. Additionally, market conditions and regional factors can also influence pricing.
It’s challenging to provide precise cost figures without specific details, but here are some approximate price ranges for different types of cryogenic tanks:
- Small Cryogenic Dewars: Small dewars or portable cryogenic containers with capacities ranging from a few liters to a few hundred liters can cost anywhere from a few hundred dollars to a few thousand dollars.
- Cryogenic Cylinders: Cryogenic cylinders with larger capacities, typically used for industrial or medical applications, can range in price from a few thousand dollars to tens of thousands of dollars, depending on the size and material.
- Bulk Storage Tanks: Bulk cryogenic storage tanks, used for large-scale storage and distribution of liquefied gases, can range in cost from tens of thousands of dollars to several hundred thousand dollars or even higher. The price is influenced by factors such as storage capacity, construction material, insulation type, and additional features like pressure control systems.
Conclusion
Cryogenic storage tanks represent a remarkable fusion of engineering, materials science, and scientific principles. These tanks have revolutionized industries by enabling the safe and efficient storage of liquefied gases at ultra-low temperatures. From industrial applications to aerospace endeavors and medical breakthroughs, cryogenic storage tanks continue to contribute to our technological progress. As ongoing research and advancements pave the way for improved designs and materials, the future of cryogenic storage tanks holds immense potential for further innovation and transformative applications in diverse fields.
excellent knowledge shared.
Thank dear
Praful Dewra
Gulfcryo kuwait.