In the intricate world of fluid systems, where power and precision are paramount, the importance of pump couplings often goes unnoticed. Yet, these mechanical components play a pivotal role in the smooth operation of pumps, ensuring the efficient transfer of power from a motor to a pump’s impeller. In this article, we’ll take a deep dive into the world of pump couplings, shedding light on what they are, their types, and their critical role in various industries.
What is a Pump Coupling?
A pump coupling is a mechanical device used to connect two shafts, typically one from the pump’s impeller and the other from the motor or engine. Its primary function is to transmit power while accommodating misalignment, reducing shock loads, and isolating vibrations. In essence, pump couplings are the unsung heroes of fluid systems, bridging the gap between the power source and the pump.
Functions of Pump Coupling
The major functions of a pump coupling are
Power Transmission:
The key function of a pump coupling is to efficiently transfer mechanical power from the power source (motor or engine) to the hydraulic pump. This power transmission allows the pump to pressurize and move hydraulic fluid, which is essential for various hydraulic systems.
Alignment and Misalignment Compensation:
Pump couplings are designed to accommodate any misalignment or minor axial and radial deviations between the pump and the power source. This feature helps reduce wear and tear on both the pump and the power source, enhancing their longevity.
Vibration Damping:
Many pump couplings incorporate elements that help dampen vibrations generated during operation. This is crucial in maintaining the stability and performance of the hydraulic system and reducing the risk of damage due to excessive vibrations.
Shock Load Absorption:
Hydraulic systems can experience sudden changes in load or pressure, causing shock loads. Couplings in hydraulic pump systems are designed to absorb and distribute these shock loads to prevent damage to the components.
Types of Pump Couplings
There is a diverse range of pump couplings designed to cater to different applications and requirements. Here are some common types:
Flexible Couplings:
Elastomeric Couplings:
An elastomeric coupling is a type of flexible coupling that uses an elastomeric (rubber or polymer) element to connect two shafts. This elastomer acts as a flexible intermediary, transmitting torque from one shaft to the other while accommodating misalignment and dampening vibrations. Elastomeric couplings are commonly used in machinery where shock absorption and misalignment tolerance are essential, such as in pumps and compressors.
These couplings are highly effective at accommodating angular, parallel, and axial misalignments between shafts, which helps reduce stress on the connected machinery. Elastomeric couplings are excellent at dampening vibrations, making them suitable for applications where vibration isolation is crucial, such as in pumps and compressors. They are relatively easy to install and maintain, as they don’t require lubrication and have fewer moving parts compared to some other coupling types.
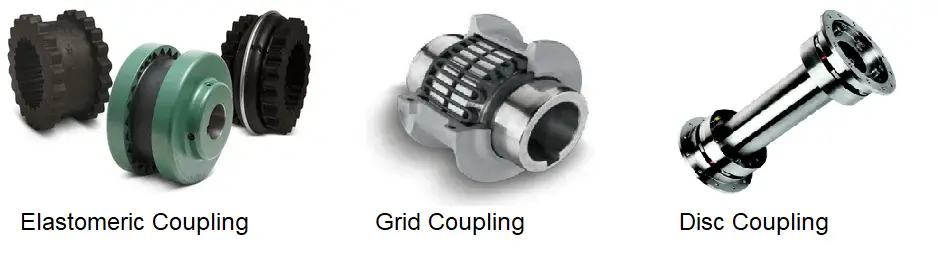
Grid Coupling:
A grid coupling is a type of flexible coupling that employs a grid or spring-like element made of metal or composite materials to connect two shafts. This grid element bridges the gap between the driving and driven shafts, providing a high torque-carrying capacity while accommodating misalignment and shock loads. Grid couplings are favored in heavy-duty applications like conveyors and mining equipment.
Disc Coupling:
A disc-coupling is a type of flexible coupling that utilizes flexible, thin metal discs to connect two shafts. These metal discs are typically arranged in a pack or series, forming the coupling assembly. Disc couplings offer high torsional stiffness, zero backlashes, and precise motion transmission, making them suitable for applications demanding precise shaft alignments and minimal backlashes, such as robotics and precision machinery.
Rigid Couplings:
Gear Couplings:
A gear coupling is a type of rigid coupling that employs external gear teeth on two hubs to connect two shafts. The gear teeth mesh together, transmitting torque from one shaft to the other. Gear couplings are known for their high torque capacity and robustness, making them suitable for heavy-duty applications like steel mills and rolling mills. They can accommodate angular misalignment but are less forgiving of parallel misalignment.
Flange Couplings:
A flange coupling is a type of rigid coupling used to connect two shafts that are perfectly aligned with each other. It consists of two flanged hubs, one on each shaft, with each hub having flanges that are bolted together. The bolts firmly secure the two flanges, creating a rigid and non-flexible connection between the shafts. Flange couplings are ideal for applications where precise alignment is possible and where no flexibility is required. They are commonly used in machinery such as pumps, compressors, and industrial gearboxes.
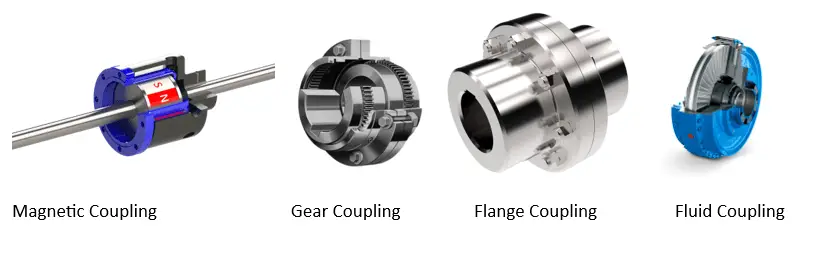
Sleeve Couplings:
A sleeve coupling, also known as a muff coupling, is a type of rigid coupling used to connect two shafts that are axially aligned but may have slight radial misalignment or parallel misalignment. It consists of a cylindrical sleeve that slides over the ends of the two shafts and is typically attached to the shafts using keyways or set screws. Sleeve couplings provide a solid and direct connection between the shafts, making them suitable for applications where minimal misalignment tolerance is required. They are relatively simple and cost-effective couplings commonly used in various machinery and equipment.
Hydrodynamic Couplings:
Fluid Coupling:
A fluid coupling is a mechanical device used to transmit rotational power from one shaft to another by means of a viscous fluid medium. It consists of two primary components: the impeller (also known as the pump) and the turbine, which is housed in a sealed casing filled with a special hydraulic fluid.
When one shaft (typically the input shaft) starts to rotate, it drives the impeller, which propels the hydraulic fluid outward in a radial direction. This action creates a flow of fluid within the coupling. The fluid then flows onto the blades of the turbine, which is connected to the output shaft. As the fluid interacts with the turbine blades, it transfers rotational energy to the output shaft, causing it to rotate.
Characteristic Features of Fluid Couplings:
- Smooth Start-Up: Fluid couplings provide a gradual, torque-limiting start-up, preventing abrupt mechanical shocks to the system and reducing wear and tear on connected machinery.
- Torque Converter: They act as torque converters, allowing for speed differences between the input and output shafts, which can be useful in applications with varying loads.
- Overload Protection: Fluid couplings can protect the drivetrain from overload by slipping when the torque exceeds a certain limit, safeguarding the machinery.
- Damping Effect: They also have a damping effect, reducing torsional vibrations and shocks in the system.
Fluid couplings are commonly used in applications like conveyor systems, crushers, and large industrial machinery where smooth start-ups and torque control are essential.
Magnetic Coupling:
A magnetic coupling is a type of coupling that uses magnetic fields to transmit torque between two rotating shafts, typically while maintaining a hermetically sealed barrier between them. It consists of an outer rotor, an inner rotor, and a magnetic assembly.
The outer rotor is typically connected to one shaft, and the inner rotor to the other. They are separated by a containment shell or housing, which prevents any physical contact between the two rotors. The magnetic assembly, which usually consists of permanent magnets, generates a magnetic field that passes through the containment shell and couples the motion of the outer rotor to the inner rotor.
Characteristic Features of Magnetic Couplings:
- Hermetic Sealing: One of the primary advantages of magnetic couplings is their ability to maintain a hermetic seal between the two shafts, preventing fluid leakage or contamination. This feature makes them valuable in applications where environmental integrity is critical, such as in chemical processing or medical equipment.
- Maintenance-Free: Magnetic couplings do not have physical contact between their components, which means they are maintenance-free and do not experience wear over time.
- Precise Torque Transmission: Magnetic couplings can provide precise and efficient torque transmission without mechanical losses, as there is no direct physical connection between the shafts.
Magnetic couplings find applications in industries where the prevention of fluid leakage and the maintenance of a sterile or controlled environment are paramount, including chemical processing, pharmaceuticals, and food production.
The Role of Pump Couplings in Industries
Pump couplings are indispensable in various industries. Here are a few examples:
- Manufacturing: In manufacturing processes, pump couplings ensure the efficient operation of pumps, which are used for coolant circulation, material handling, and more.
- Oil and Gas: In the oil and gas industry, pump couplings handle the demanding task of transferring fluids, including crude oil and natural gas, from one location to another.
- Chemical and Pharmaceutical: In these industries, where precision and containment are vital, magnetic couplings are often employed to prevent fluid leakage and contamination.
- Agriculture: In agriculture, pumps are used for irrigation and water management. Couplings help transmit power efficiently, ensuring proper water distribution.
- Water and Wastewater Treatment: In water treatment plants, pumps play a crucial role in moving and treating water. Couplings ensure their reliability.
Maintenance and Troubleshooting
Proper maintenance of pump couplings is essential to prevent downtime and costly repairs. Regular inspection for wear, misalignment, and lubrication is necessary. Vibrations or unusual noises can indicate coupling issues that need prompt attention.
What is a Pump Coupling Guard?
A pump coupling guard, also known as a coupling guard or coupling cover, is a safety device used to protect personnel and equipment from potential hazards associated with rotating couplings in machinery, such as pumps, compressors, and other industrial equipment. These guards serve several important purposes in industrial settings:
- Personnel Safety: One of the primary functions of a coupling guard is to prevent accidental contact with the rotating coupling components. Couplings can have exposed rotating parts that pose a significant risk of injury if a person’s clothing, body parts, or tools come into contact with them. The guard acts as a physical barrier, reducing the risk of accidents and injuries.
- Equipment Protection: Coupling guards also protect the coupling components themselves. They help prevent foreign objects, debris, or contaminants from entering the coupling area, which could otherwise lead to damage or misalignment of the coupling parts. In this way, coupling guards contribute to the longevity and reliability of the equipment.
- Compliance with Safety Regulations: Many industrial safety standards and regulations require the use of coupling guards to ensure a safe working environment. Compliance with these regulations is essential to avoid legal liabilities and maintain a safe workplace.
- Noise Reduction: In some cases, coupling guards may incorporate noise-reducing features, such as acoustic insulation, to mitigate the noise generated by rotating couplings. This can help improve the working conditions for personnel in noisy industrial environments.
Coupling guards come in various designs, materials, and sizes, depending on the specific application and requirements. They are typically made of metal or plastic and are designed to be easily removable for maintenance and inspection purposes. Proper installation and maintenance of coupling guards are crucial to ensuring their effectiveness in protecting both personnel and equipment.
Causes for Pump Coupling Failures and Ways to Avoid Them
Pump coupling failures can result in costly downtime and maintenance, making it essential to understand their causes and how to prevent them. Here are common causes for pump coupling failures and ways to avoid them:
Causes for Pump Coupling Failures:
- Misalignment: One of the most common causes of coupling failures is misalignment between the pump and the motor. Misalignment can result from poor installation, foundation settlement, or thermal expansion and contraction.
- Overload: Excessive torque or overload can damage couplings. This can occur due to abrupt changes in pump loads, such as sudden pressure spikes or cavitation, and it may cause coupling components to wear or fail.
- Lubrication Issues: Inadequate or improper lubrication of coupling components can lead to premature wear and failure. Lack of lubrication can cause friction, leading to heat buildup and component damage.
- Vibration: Excessive vibration in the pump system can contribute to coupling failures. Vibration may result from unbalanced impellers, worn bearings, or structural issues in the system.
- Corrosion: In corrosive environments, coupling components can deteriorate over time. Corrosion can weaken the coupling, reducing its load-bearing capacity and potentially leading to failure.
- Fatigue and Wear: Over time, couplings can experience fatigue and wear due to cyclic loading, particularly in applications with frequent starts and stops.
Ways to Avoid Pump Coupling Failures:
- Proper Alignment: Ensure that the pump and motor shafts are properly aligned during installation. Precision alignment minimizes stress on the coupling and extends its lifespan.
- Regular Maintenance: Implement a routine maintenance schedule that includes inspection, lubrication, and vibration analysis. This helps identify and address issues before they lead to failures.
- Choose the Right Coupling: Select a coupling that is suitable for your application’s specific requirements. Different couplings are designed to handle varying levels of misalignment, torque, and vibration.
- Monitor Pump Conditions: Use condition monitoring tools to track pump performance, including temperature, pressure, and vibration. Early detection of anomalies allows for timely maintenance.
- Lubrication Management: Ensure that coupling components are adequately lubricated with the right type and quantity of lubricant. Follow the manufacturer’s recommendations for lubrication intervals.
- Protect from Corrosion: If the pump is exposed to corrosive environments, use protective coatings or materials designed to resist corrosion. Regular inspections can help detect and address corrosion early.
- Reduce Overload: Implement measures to reduce the risk of overloading the pump, such as using pressure relief valves, and surge tanks, or properly sizing the pump for the application.
- Education and Training: Train personnel responsible for pump maintenance and operation to follow best practices and safety guidelines.
- Regular Inspections: Conduct regular visual inspections of coupling components for signs of wear, damage, or misalignment. Address any issues promptly.
- Balancing: Ensure that rotating components in the pump system, such as impellers, are properly balanced to minimize vibration.
By addressing these causes and implementing preventive measures, you can significantly reduce the risk of pump coupling failures, improve equipment reliability, and extend the lifespan of your pump system. Regular maintenance and monitoring are key to early detection and mitigation of potential issues.
Conclusion
Pump couplings might not be the stars of fluid systems, but they are undoubtedly the backbone. They quietly ensure the smooth and efficient transfer of power from the motor to the pump, allowing industries to function seamlessly. Understanding the types of couplings and their roles in different applications is vital for maintaining the reliability and longevity of fluid systems across various industries. So, next time you witness a pump in action, remember the unsung hero behind the scenes – the pump coupling.