Desalting and Dehydration processes are crucial in the oil industry to prepare crude oil for refining and ensure the quality and safety of the final products. This comprehensive guide will cover everything you need to know about crude oil desalting and dehydration, including the processes involved, equipment used, key parameters, and the significance of these processes in the oil industry.
What is Crude Oil Desalting and Dehydration?
Desalting of Crude oil means the removal of the dissolved salt in the crude oil and increasing the grade of the crude oil. Crude oil dehydration is the process of removing the water present in crude oil to meet the purchaser’s limit. Since salt is dissolved in the water, the dissolved salt is also removed in the process.
Crude oil desalting is the initial step in the refining process, where impurities such as salts and water are removed from the crude oil. The desalting process is critical because failure to remove these impurities can lead to corrosion and fouling of downstream equipment in the refining process, which can be costly and result in suboptimal product quality.
Crude oil dehydration is another critical process in the oil industry, which involves the removal of water from crude oil. Water content in crude oil can lead to several issues, including corrosion, emulsion formation, and reduced refining efficiency.
Reason for Desalting and Dehydration of Crude Oil
Desalting and dehydration are important processes in crude oil refining that help to remove impurities and contaminants from crude oil. Here are some reasons why these processes are important:
- Protecting downstream equipment: Impurities and contaminants in crude oil can damage downstream equipment such as pumps, valves, and pipelines. Desalting and dehydration help to remove these impurities and contaminants, protecting downstream equipment and ensuring the safe and efficient operation of the refining process.
- Improving product quality: Impurities and contaminants in crude oil can also affect the quality of the final refined products such as gasoline, diesel, and jet fuel. Desalting and dehydration help to remove these impurities, improving the quality and purity of the final refined products.
- Reducing corrosion: Impurities and contaminants in crude oil can cause corrosion in pipelines and equipment. Desalting and dehydration help to remove these impurities, reducing the risk of corrosion and extending the lifespan of the equipment.
- Meeting product specifications: Refined products must meet specific product specifications and quality standards to ensure they are safe and effective for use. Desalting and dehydration help to remove impurities and contaminants that can cause refined products to fall outside of these specifications.
- Improving safety: Desalting and dehydration can also help to improve safety in the refining process by reducing the risk of equipment failure and leaks caused by impurities and contaminants.
- Minimizing Fouling: Removing sediments and trace metals reduces the fouling of heat exchangers and refining equipment, leading to more efficient and cost-effective operations.
- Environmental Compliance: Proper desalting reduces the risk of hazardous conditions, such as hydrate formation, and ensures compliance with environmental regulations by treating waste brine streams.
Overall, desalting and dehydration are important processes in crude oil refining that help to improve the quality, safety, and efficiency of the refining process, and ensure that the final refined products meet product specifications and quality standards.
Why Desalting and Dehydration of Crude Oil?
Crude purchasers place limits on the salt and water contents of the crude they buy, typically:
- Water 0.2 to 0.5% vol.
- Salt 70 g/m3
Since salt is dissolved in the water phase, dehydration is also effectively desalting.
During production, the oil and water are mixed and one phase disperses as droplets (dispersed phase) in the other (continuous phase). Maximum mixing occurs at the points of high energy dissipation, e.g. at flow beans, valves, and pumps.
Theories behind Desalting and Dehydration of Crude Oil
Water and oil are separated by virtue of their different densities; gravity is the driving force. For laminar flow conditions, the settling velocity (VT) of an unhindered dispersed phase droplet is given by Stokes Law:
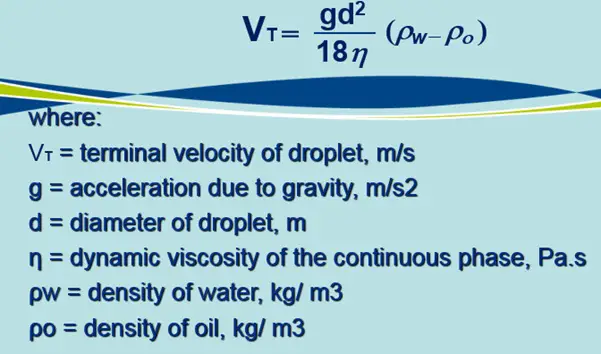
This can be increased by the use of centrifuges, cyclones, or other such devices, although this is unusual in oilfield practice.
Density Difference and Viscosity
Large density differences between oil (ρo) and water (ρw) and low oil viscosities are favorable for easy separation and therefore light crudes separate faster than heavy crudes. An increase in temperature causes a reduction in viscosity, therefore the application of heat can be used to accelerate the separation of heavy crude.
Droplet Size (d)
The settling rate depends on the square of the droplet diameter. Drop-to-drop coalescence increases droplet diameter and for this reason, coalescence is a key factor in successful dehydration. Unfortunately, however, many oilfield dispersions resist coalescence and are known as ‘stable dispersions’ or ‘stable emulsions.
Oil and water mixtures would be highly unstable were it not for naturally occurring surface-active agents (surfactants) and finely divided particles that are absorbed in oil/water interfaces to form rigid films that resist coalescence. In this way, surfactants stabilize fine droplets which then accumulate to form emulsions.
Water in oil emulsions is known as ‘normal’; most oilfield emulsions are in this category. Oil in water emulsions is termed ‘reverse’.
Crude Oil Desalting and Dehydration Procedure
Successful dehydration of crude oil is carried out in three steps
- Destabilization of the emulsion
- Coalescence of small drops into large drops
- Settling out of large drops and separation of the two phases.
Destabilization of the Emulsion
Stable inter-facial films can be broken down by:
- Chemical demulsifiers
- Heat treatment
- pH treatment
- Increased salinity.
The use of chemical demulsifiers is now the main approach for treating stable oilfield emulsions, often in combination with heat treatment. Demulsifiers are most effective when added prior to the formation of an emulsion.
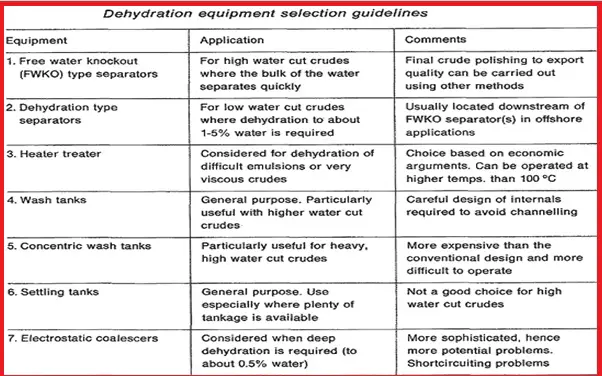
Separators in Crude oil Dehydration
Separators are prefabricated pressure vessels, which are suitable for separating oil, water, and gas.
Separators can be designed for ‘free water knock-out’ (FWKO) or ‘dehydration’ service. Both look similar in appearance, but for a given throughout the dimensions of a vessel in dehydration, service is necessarily larger.
A separator designed for free water knockout service will generally only remove free water from the feed stream. The rest of the water will remain dispersed in the crude, typically 5 to 10% vol. for light crudes (ρo < 850 kg/ m3) and 10 to 20% vol. for heavy crude (ρ o > 900 kg/ m3).
A separator designed for ‘dehydration service’ will dehydrate crudes down to low water content levels, typically 1 to 3% vol. for a liquid-liquid separator and 1 to 5% vol. for a three-phase separator.
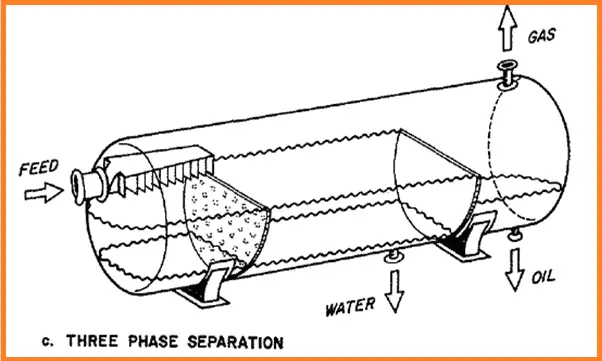
Wash Tank/ Concentric Wash Tank for Crude Oil Dehydration
Wash tanks are usually the preferred choice for general-purpose dehydration of light and medium-density crude Oils (ρo < 900 kg/ m3) on land. The water content of the crude at the outlet is typically 1 to 3% vol. Operating temperatures above 85 ºC is not usually because of unacceptable loss of light ends.
A conventional wash tank is shown below:
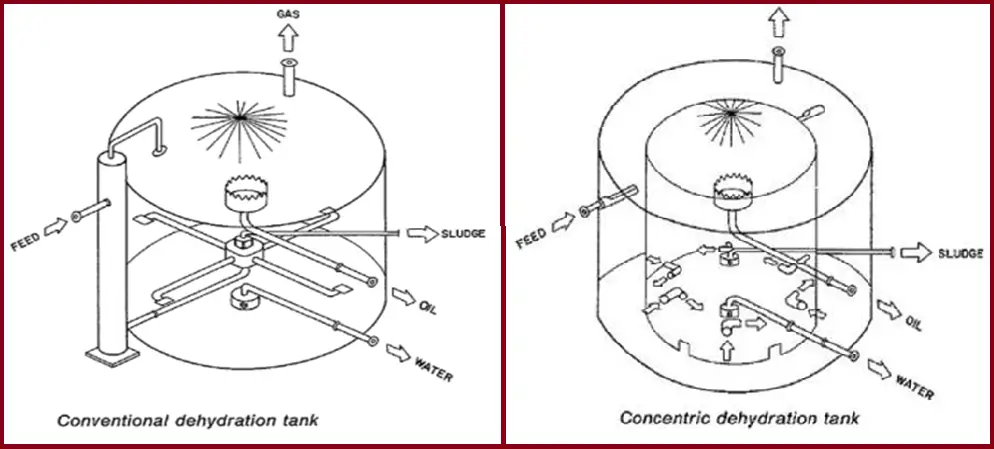
Note that ‘free gas’ is removed upstream of the tank in a gas boot. If deeper dehydration is required then either a separate degassing tank should be installed instead of the gas boot, or consideration should be given to using a concentric wash tank.
Concentric wash tanks are a relatively recent development and are particularly suitable for the dehydration of heavy/viscous crudes.
A typical concentric wash tank is above.
Electrostatic Coalescers for Crude Dehydration
Electrostatic coalescers are pressure vessels fitted with electric grid internals and are suitable for deep dehydration of crude oil. The water content of the crude oil at the outlet is typically in the range of 0.1 to 0.5% vol. The units are relatively compact and therefore suitable for use offshore.
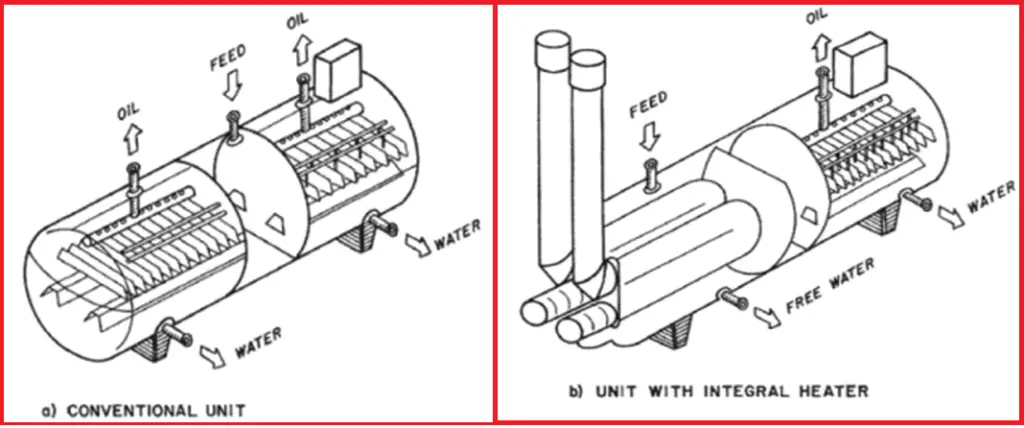
Crude oil desalting and dehydration are critical processes in the oil industry that prepare crude oil for refining and ensure the quality and safety of the final products. Desalting removes salts, water, sediments, and trace metals from crude oil, while dehydration removes water content. Proper control of key parameters, such as temperature, residence time, and the use of appropriate equipment, is essential for the success of these processes. By implementing effective desalting and dehydration techniques, the oil industry can maximize refining efficiency, reduce equipment corrosion, and produce high-quality products while adhering to environmental regulations.
Hi thank you it was useful.
Hi Anuo Kumar Dey can you help me about my cours project?
if you have information about “automation of thermal processes in the process of desalination and dehydration of oil” please you send me.
SIR
I AM WORKING FOR RUMELIA PROJECT INSTRUMENTATION DESIGN ENGINEER. PLEASE ADVISE WHAT TYPE OF IMPULSE TUBING MATERIAL FOR INSTRUMENT CONNECTION SHOULD BE USED?
THANKS AND REGARDS
K.V.RAMANA