A desander is a vital component of the mining and drilling process. Desander is a solid control device with a series of hydro cyclones that separates sand and silt from the rig’s drilling fluid. The desander is fixed at the top of the sludge tank, just after the shale shaker and the degasser, and before the desilter. As they are usually installed at the wellhead in the oil and gas field, they are also known as wellhead desander. Wellhead desanders are produced in both ASME and API design ratings as per requirement.
Desanders are basically solid control devices. Cyclonic desander and desilters use a centrifugal force to separate solids from liquids. There are no rotating components. Centrifugal force is created by turning the head of a centrifugal pump into a high-speed rotating flow inside a cone.
Solids are concentrated near the cone wall in proportion to their mass and exit as underflow at the bottom of the cone. Clean liquids and fine solids return from the overflow at the top of the cone.
Demineralization and sand removal hydro-cyclones are simple mechanical devices with no moving parts, but they facilitate the solids sedimentation process. Drilling mud laden with solids is drawn into the body of the hydro-cyclone and the iatrogenic force of the flow separates the heavy solids from the lighter solids. The heavier solids are discharged at the lowest point (underflow) of the hydro-cyclone and the lighter solids at the highest point (overflow). Solids removal is dependent on feed particle size, liquid concentration, liquid feed pressure (as a function of liquid density), and hydro-cyclone size.
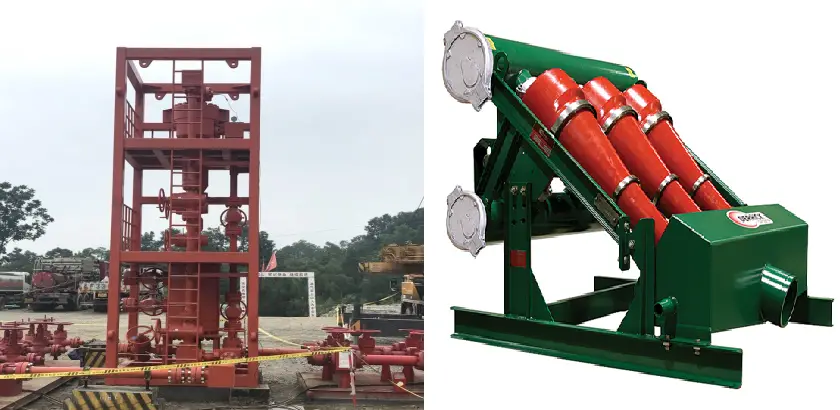
Desanders remove abrasive solids from drilling fluids that vibrators can’t remove. In general, the diameter of the solids separated by the desander is 45 µm to 74 µm and the diameter of the decanter is 15 µm to 44 µm.
Working of Desander
When the drilling fluid reaches the dead grinder, it enters through a pressurized pipe and hits the dead grinder cone first. The way this cone turns the liquid is similar to the flow of water in a sink, except the walls of the desander cone are porous to filter out sand particles.
Desanders have no moving parts and particle removal is accomplished solely by gravity and pressure. Desanders are generally not large tools, about the size of a bathtub for small jobs, and rarely larger than the average car. When the liquid reaches the small end of the cone, it is pushed out of the tube and proceeds to the next step in the purification process.
This type of work is commonly used in the oil industry. Desander is also used in other industries, primarily related to the drilling and extraction of materials such as natural gas. Companies that manage lakes and dams can use desalters and desilters to keep water flowing and remove contaminants.
Types of Desanders
- Desander of simple cycloning: These are good for sandy or slightly sandy soils. After the sludge has passed through a screening stage to remove oversize, it is fed to a cyclone separator.
- Desander of double cycloning: Similar to a single cyclone, with the difference that the sludge pass twice through the cyclone so as to separate the finest sand and silt even.
Feature of Desanders
- Cyclonic desanders and decanters have no moving parts and are extremely reliable solids removal devices when properly operated and maintained.
- Customized cone configurations.
- The material of the hydrocyclone is polyurethane, which makes it lightweight and durable.
- Victaulic clamp connects indoor and outdoor cables for easy removal.
- Skids mounted with ring bolts welded to the frame.
Selection of Desanders
The parameters that must be looked upon while selecting a desander for the specific application are:
- The Crude oil quality.
- External pipe outer diameter and the working pressure of the pipeline.
- Efficiency and accuracy of Separation.
- Operating parameters.
- Desander size requirements
- Wear resistance and anti-aging properties.
- Service life.
Advantages of Desanders
Hydrocyclones for desanders and demineralizers in drilling are used to remove sand and silt particles from drilling fluids that have passed through oil and gas vibrating screens. The main advantages of installing a desander are:
- Preventing solid build-up in equipment and pipelines.
- Elimination of fine chips
- Large capacity with a relatively simple structure
- No rotating parts
- Easy to use
- Low downtime and maintenance
- Protecting downstream equipment from wear and damage
Cavins Desander
Cavins Desander is a specially designed desander by Cavins Corporation which is providing desander solutions for the last 65 years. These easy to install Cavins desanders are widely used to separate abrasive solids from production fluids. They are installed before downhole pumps thus extends the pump life. Desanders by Cavins Corporation works by centrifugal action to separate solid particles. They are available in a range of sizes and flowrates. Cavins desanders are known for long service life, all steel construction, and quality.
Frequently Asked Questions: FAQ
1. What is a Desander?
A Desander is a specialized equipment used in the oil and gas industry for the removal of solid particles, primarily sand, and other abrasive materials, from the production fluids or drilling mud.
2. What is a Desander used for?
Desanders are primarily used to protect downstream equipment, such as pipelines, pumps, and valves, from abrasive damage caused by sand and solids present in oil, gas, or drilling fluid. They ensure the integrity and efficiency of the production process.
3. What are the components of a Desander?
A typical Desander consists of three main components:
- Inlet Section: This is where the unprocessed fluid enters the Desander.
- Cyclonic Separation Unit: This component uses centrifugal force to separate solids from the fluid.
- Outlet Section: Here, the cleaned fluid exits the Desander, while the separated solids are discharged.
4. How does a Desander work?
Desanders work by utilizing centrifugal force to separate heavier solids (like sand) from the incoming fluid. As the fluid enters the cyclonic separation unit, it is spun rapidly, causing the heavier solids to move outward and settle in a collection chamber, while the cleaned fluid continues its path through the outlet.
5. What types of solids can a Desander remove?
Desanders are primarily designed to remove sand, but they can also effectively remove other solid particles such as silt, clay, and small debris from production fluids.
6. Where are Desanders commonly used in the oil and gas industry?
Desanders are used at various stages of the production process, including wellhead facilities, drilling operations, and downstream processing plants. They are also employed in water treatment systems to remove solids from produced water.
7. What are the benefits of using a Desander?
The key benefits of using a Desander include:
- Protection of downstream equipment from erosion and damage.
- Improved operational efficiency and reduced maintenance costs.
- Enhanced production fluid quality and purity.
8. What is the maintenance required for a Desander?
Maintenance for Desanders typically involves regular inspections, cleaning or replacement of worn components, and monitoring of fluid flow rates. The specific maintenance requirements may vary depending on the application and usage.
9. Can Desanders be customized for specific applications?
Yes, Desanders can be customized to meet the specific requirements of different applications. They can be designed with various flow capacities, materials of construction, and control systems to suit the needs of a particular project.
10. Are there alternatives to Desanders for solids removal in the oil and gas industry?
Yes, alternatives such as Desilter (for smaller particles), hydrocyclones, and various filtration systems can be used for solids removal. The choice of equipment depends on factors like particle size, flow rates, and the nature of the solids in the process fluid. Desanders are favored when dealing with larger, abrasive particles like sand.
Great article