As an engineer, you must have heard the term fillet welding. This is one of the most common terms related to welding for joining two metal pieces together to get a permanent joint. In the construction, manufacturing, maintenance, piping, and fabrication world, many of the metallic elements are joined using fillet weld. In this article, we will learn about the basics of a fillet weld, its types, characteristics, applications, symbols, and advantages.
What is Fillet Welding?
Fillet welding is a type of welding in which two metal pieces are joined together by welding at an approximately right angle to one another. The weld deposit is made along the edge of the metal, creating a fillet-shaped weld. Lap joints, corner joints, T-joints, etc are examples of typical fillet welding. This is a very simple and cost-effective joining method.
The shape of the fillet weld is triangular with a concave, convex, or flat surface depending on the welder’s technique. In the piping industry, the piping flanges are connected to pipes using a fillet welding process. Refer to Fig. 1 below that shows a typical example of a fillet weld.
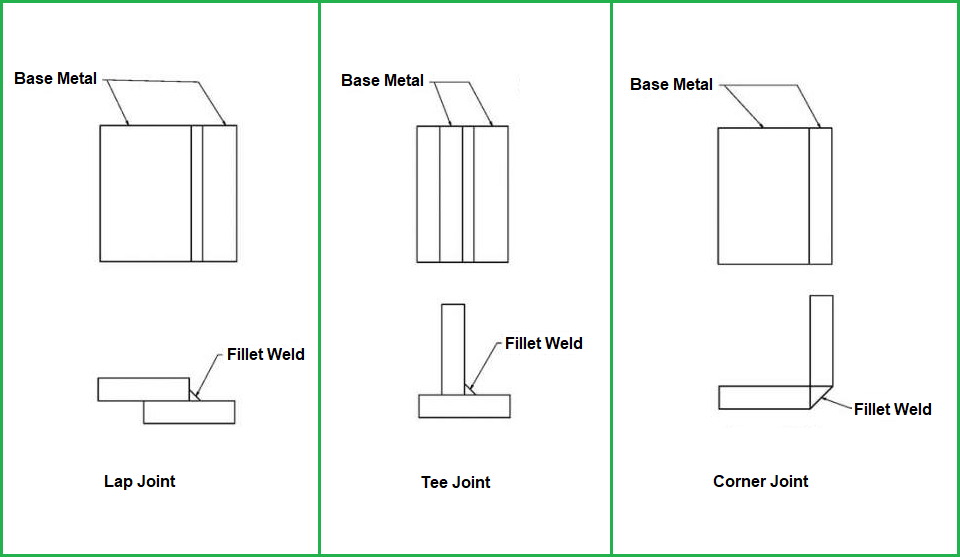
Parts of a Fillet Weld
A fillet weld usually has the following five parts (Refer to Fig. 2):
The legs: The two sides of the fillet weld are called legs. They are approximately perpendicular to the joint and connect the base metal. The legs have a triangular shape and their size is determined by the thickness of the metal being welded.
The throat: The throat is the distance between the legs of the weld and is the narrowest part of the weld. The throat size or throat thickness must be at least equal to the thickness of the thinner parts being joined. The throat thickness is a very important parameter in weld sizing as the strength of any fillet weld is calculated using the throat thickness.
The toe: The point where the legs of the weld connect the base metal is known as the toe of the fillet weld. The toe is the first part of the weld that solidifies and it must be properly fused to the base metal.
The root: The root is the bottom part of the fillet weld at the base of the throat. The root meets the legs of the weld. This is the last part of the weld to solidify and for a high-quality fillet weld, it must be properly fused to the base metal.
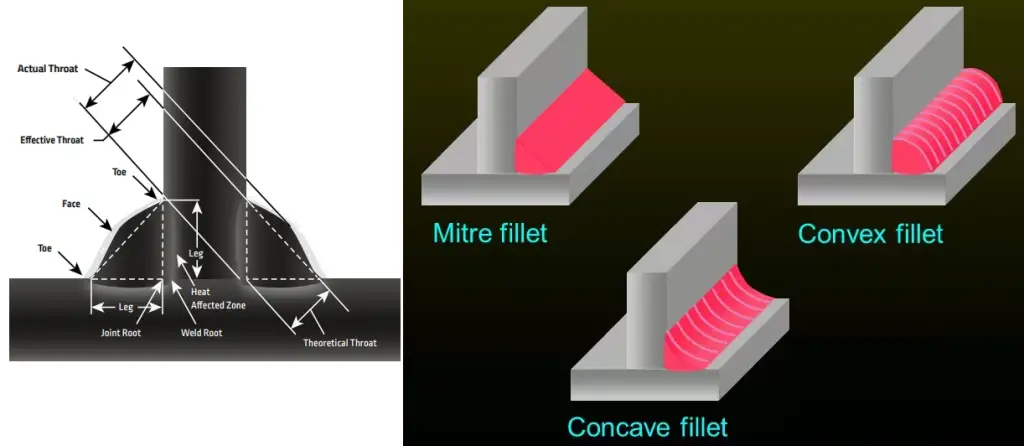
There are some other terms that are associated with fillet welding. Those are:
Convexity and Concavity: The shape of the fillet weld can be convex or concave. In a convex fillet weld, the throat of the weld is larger than the legs. On the other hand, in a concave fillet weld the throat of the weld is smaller than the legs.
The reinforcement: The extra weld metal that is added to the throat during the fillet welding process that increases its strength and size is known as the reinforcement.
Boxing: The term boxing specifies the continuation of a fillet weld around the corner of a member.
Welding Symbols: Fillet welding must be performed following the proper welding symbol as given in the construction drawing.
Note that, The fillet weld joint strength and quality are affected by the size and shape of the legs, the throat, reinforcement, and the root.
Characteristics of Fillet Welding
Some of the characteristics a typical fillet welding exhibits are:
- It is a type of welding that creates a fillet-shaped weld, typically used to join two pieces of metal at a 90-degree angle (right angle).
- A variety of welding techniques such as Gas Tungsten Arc Welding (GTAW), Gas Metal Arc Welding (GMAW), Shielded Metal Arc Welding (SMAW), etc can be used for fillet welding.
- It is a versatile method of welding and can be used on a wide range of materials, including steel, aluminum, and stainless steel.
- Fillet welding is a strong joint, but its strength is usually lower than that of a butt joint.
- The size of the fillet weld leg length is usually smaller than the thickness of the thinner parts being joined.
- The strength of the fillet weld depends on the size of the legs and the throat size.
- In order to achieve good penetration and fusion of the metal, proper surface preparation is required.
Applications of Fillet Welding
Fillet welding can be found in a wide range of applications in various industries, some of which include:
- Construction: Fillet welding is commonly used in the construction industry to join structural steel members together, such as beams, columns, and trusses.
- Manufacturing: Fillet welding is used in the manufacturing of various products such as machinery, equipment, and vehicles.
- Repair and maintenance: Fillet welding is often used to repair or reinforce existing structures and equipment.
- Piping and ductwork: Fillet welding is used to join pipes and ductwork in the plumbing and HVAC industries.
- Sheet metal fabrication: Fillet welding is used to join sheets of metal together in the fabrication of various products such as panels, enclosures, and cabinets.
In general, fillet welding is commonly used in many welding projects because it is simple, versatile, and can be performed using a variety of welding techniques and equipment.
Types of Fillet Welding
Fillet welds can be categorized depending on various parameters.
Based on the appearance, there are three types of fillet welds:
Convex Fillet Weld: Convex fillet weld as shown in Fig. 2 is used to provide additional reinforcement and strength to the weld joint. As stated earlier, the throat of the convex fillet weld is larger than the legs.
Concave Fillet Weld: When there is a need to provide additional clearance in a weld joint, the concave fillet weld (Fig. 2) is used. This type of fillet weld has a curved shape with the weld throat smaller than the legs.
Mitre Fillet Weld: Mitre fillet welds are flat fillet welds. The throat thickness of a flat fillet weld is calculated as 0.707 X Leg of the mitre fillet weld (Fig. 2).
Based on Weld Joint Configuration, there are three types of fillet welds. They are:
- Lap joint
- Tee Joint, and
- Corner Joint
In the fabrication industry Lap, Tee, and Corner joints are quite common. Refer to Fig. 1, which shows typical examples of Lap, Corner, and Tee Fillet Welds.
Based on the length of the fillet weld leg, there are two types of fillet welds as mentioned below:
- Full fillet weld: In this type of fillet weld, both legs of the weld are equal in length. The size of the full fillet weld is typically 1/4 to 5/16 inches.
- Partial fillet weld: In this type of fillet weld, one leg of the weld is shorter than the other. This type of weld is usually used while joining two metal pieces at an angle other than 90 degrees.
Based on whether the fillet welding is made on one side or both sides of the joint, they are classified as
- Single-sided fillet weld: In this type of fillet weld, the weld is made on one side of the joint only. This type of weld is used when only one side of the joint is accessible.
- Double-sided fillet weld: In this type of fillet weld, the weld is made on both sides of the joint. This type of weld provides additional strength to the weld joint.
The selection of a specific fillet welding type depends on the specific application, accessibility, and requirements of the joint.
Size of Fillet Weld
Fillet weld size refers to the dimensions of a fillet weld, specifically the size of the legs and the throat. The size of a fillet weld is usually measured in inches or millimeters and is determined by the thickness of the metal being welded and the strength required for the joint.
The size of the legs of a fillet weld is determined by the thickness of the thinner parts being joined. The thickness of the legs should be at least 1/8 inch and no more than 1/4 inch for most applications. The throat size, which is the distance between the legs of the weld, should be at least as thick as the thickness of the thinner parts being joined.
The size of the fillet weld leg length is usually smaller than the thickness of the thinner parts being joined. The size of the fillet weld leg length can be calculated using the formula: (Thickness of the thinner part x 1/√2) = Leg size.
It is important to note that the strength of a fillet weld depends on the size of the legs and the throat size. A fillet weld with larger legs and throat will be stronger than a fillet weld with smaller legs and throat. However, it’s also important to note that a fillet weld that is too large can be more brittle and less flexible, making it more susceptible to cracking.
Symbols for Fillet Welding
The symbol for fillet welding is a diagonal line, with the point of the line representing the point where the two pieces of metal are joined together. The symbol is usually accompanied by a dimension line, which indicates the size of the fillet weld. The dimension line is usually placed at a 45-degree angle to the diagonal line and is used to indicate the size of the legs of the fillet weld.
The symbol for a fillet weld is typically made up of the following elements:
- A diagonal line that represents the line of the weld.
- Two dimension lines with arrowheads at their end, one on each side of the diagonal line, representing the size of the legs of the fillet weld.
- A reference line (optional) that is parallel to the diagonal line and is used to indicate the location of the fillet weld.
This symbol is usually used in welding blueprints and engineering drawings to indicate the type and size of the welds that are required for a particular project.
Advantages and Disadvantages of Fillet Welding
Advantages of fillet welding include:
- Simplicity: Fillet welding is a relatively simple type of welding and can be done with a variety of welding techniques such as Gas Tungsten Arc Welding (GTAW), Gas Metal Arc Welding (GMAW), and Shielded Metal Arc Welding (SMAW).
- Versatility: Fillet welding can be used on a wide range of materials, including steel, aluminum, and stainless steel.
- Cost-effective: Fillet welding is generally less expensive than butt welding because it requires less welding material, and is often quicker and easier to perform.
- Strong joint: Fillet welding is a strong joint, although its strength is usually lower than that of a butt joint.
Disadvantages of fillet welding include:
- Limited strength: Fillet welding is not as strong as butt welding because the weld metal is in contact with the base metal over a smaller area.
- Limited precision: Fillet welding is not as precise as butt welding and is more prone to distortion and misalignment.
- Reduced clearance: Fillet welding may reduce the clearance of the joint, making it difficult to access or inspect the weld.
- More prone to cracking: Fillet welding is more prone to cracking than butt welding because of the smaller throat size.
It’s important to keep in mind that these are general advantages and disadvantages, the specific application and the requirements of the joint will determine if fillet welding is the best option for a particular project.
Difference between Butt Welding and Fillet Welding | Fillet Weld vs Butt Weld
The major differences between a butt weld and a fillet weld are:
- Shape: A butt weld is a type of welding in which the edges of two pieces of metal are brought together and welded, creating a straight, continuous seam. A fillet weld, on the other hand, is a type of welding in which two pieces of metal are joined together by welding along the edge of the metal, creating a fillet-shaped weld.
- Angle: A butt weld is typically used to join two pieces of metal that are in a straight line, while a fillet weld is used to join two pieces of metal at a 90-degree angle.
- Strength: A butt weld is generally stronger than a fillet weld because the weld metal is in contact with the base metal over a greater area.
- Size: A fillet weld usually has a smaller size than a butt weld. The size of the fillet weld leg length is usually smaller than the thickness of the thinner parts being joined.
- Cost: Fillet welding is generally less expensive than butt welding because it requires less welding material, and is often quicker and easier to perform.
- Applications: Both types of welding have different applications, Butt welding is typically used in heavy industry and high load-bearing structures while Fillet welding is commonly used in the construction industry, manufacturing, repair and maintenance, piping and ductwork, and sheet metal fabrication.
Video Courses in Welding
To learn more about welding the following video courses you can refer to:
I’m interested oilfield welder air pricher arc SMW and fabrication