Fire pumps are one of the essential components of most water-based fire protection systems, especially for high-rise taller buildings and structures. Their main job is to increase the water pressure when the water source does not have adequate pressure to supply the system. In this article, we will discuss the working and types of fire water pumps.
Working Principle of a Fire Water Pump
A fire water pump consists of a driver and a controller. Each pump works in any one of the following two working principles:
Centrifugal-type fire water pumps generate centrifugal forces by rotating their impeller and throwing the water from the center of the impeller to the outer parts of the impeller. On the other hand, positive displacement type fire water pumps take a selected amount of liquid as input and use mechanical action to displace that through the outlet. In general, they use pistons, gears, vanes, lubes, etc to increase the liquid pressure while discharging.
Centrifugal fire water pumps are used for high flow rates to provide a constant water flow mainly for buildings, utility stations, etc. Positive displacement-type fire water pumps are best suited for non-water services, specifically for foam concentrate or water mist systems.
A fire pump in a fire sprinkler system normally receives water from either an underground water supply or a water tank, lake, or reservoir. These pumps are is powered by electricity or diesel fuel. The high pressure supplied by the fire pumps helps in the proper distribution of water through the sprinkler system and hose standpipes.
Types of Firewater Pumps
Depending on the working philosophy mentioned above there are two main types of fire water pumps; Centrifugal and Positive displacement. All these fire pumps can again be sub-divided into various types as listed below:
- Centrifugal Fire Water Pump
- Horizontal and Vertical Split-Case Pump
- Vertical Turbine Pump
- In-Line Pump
- End Suction Pump
- Multistage Multiport Pump
- Positive Displacement Fire Water Pumps
Centrifugal Fire Water Pumps
Centrifugal fire pumps are the most widely used fire pumps. They can handle a large volume of water. The common sub-types of centrifugal fire pumps are discussed below:
Horizontal and Vertical Split-Case Pumps
Horizontal Split case pumps are very reliable fire pumps with long lifespans and size availability. They are available in a wide range of rated flow and pressure capacities and are thus suitable for a range of fire-water applications. In a horizontal split-case pump, the flow is divided and enters the impeller from opposite sides of the pump housing. The pump has a split casing (and hence the name) that is easy to open during pump maintenance. The pump is connected to the driver by a horizontal shaft.
A Vertical split casing pump is almost similar to that of a Horizontal split casing pump. But the orientation of the pump and motor are vertical. The vertical motor placement consumes less floor space and the
motor is protected against potential flooding conditions. Both horizontal and vertical split case pumps require a water source providing a positive suction pressure.
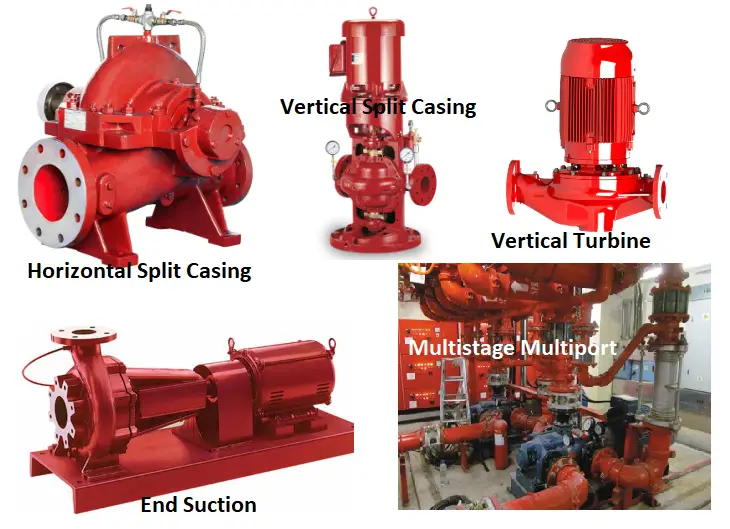
Vertical Turbine Pumps
The fire protection pump standard NFPA 20 allows vertical turbine pumps for fire water systems. They have the ability to start with negative pressure and can take water input from a below-grade source. They are available in a range of pressures and capacities and have diesel or electric drivers.
This type of fire pump is available as oil-lubricated enclosed-line-shaft and water-lubricated open-line-shaft pumps. Both vertical turbine pump types are designed for installation in drilled wells, lakes, streams, open swamps, and other subsurface sources.
In-Line Pumps
When there is limited space, in-line pumps are widely used. They can have both vertical and horizontal shafts, but the vertical shaft is the most common. Vertical in-line fire pumps provide a smooth flow of water throughout the system. This type of fire pump has a very low initial cost but they are expensive to repair. Their capacity is limited and only used with an electric driver.
End Suction Top Discharge Pump
An end suction fire pump has its discharge perpendicular to the suction inlet. They are compact and need less space as compared to horizontal split case fire pumps but have a limited capacity. End suction fire pumps are available with either an electric driver or a diesel driver.
Multistage Multiport Pump
Multistage Multiport fire pumps have multiple impellers in series in a single casing driven by a horizontal shaft. The casing has multiple discharge outlets that deliver fluids at different pressures. There is an increase in pressure in each consecutive series impeller. They can be run by an electric motor or a diesel engine.
There are certain benefits of using a multiport fire pump as listed below:
- The number of pumps required will reduce.
- Comparatively less pipe work and fewer valves.
- Reduced structural loads and associated costs as only one pump may be required
- Due to less electricity or fuel to drive only one pump energy is saved.
- Pollution is also reduced.
Positive Displacement Fire Pumps
As compared to centrifugal fire pumps, positive displacement fire pumps generate very high pressures but they have limited flow volume. They come in two main types, reciprocating and rotary. The use of positive displacement fire pumps is not common and is limited only to specialized applications with water mist and foam-water systems.
Fire Pump Drivers
As outlined in NFPA 20, there are three types of drivers to drive the impeller and shafts of a fire pump. They are:
- Electrical motor,
- Diesel engine, and
- Steam turbine systems.
The most common type of driver is the electrical motor. Electrical motor drives are cost-effective and easy to operate. The motor takes electrical power to spin which spins the shaft connected to the impeller.
While a power source is not continuously available, the diesel engine is a good choice. The diesel motor is mounted on the same skid as the pump. Diesel engines use the power generated due to the combustion of fuel to turn the impeller. However, diesel engines need a lot of infrastructure and maintenance and a governor system to control the power.
Steam turbines as fire pump drivers are very rarely used. Steam turbines need a separate unit to generate steam and costly equipment like a boiler, steam generator, etc.
Sizing a Fire Pump
A fire pump must be designed properly to handle the most demanding fire sprinkler system. Incorrectly sized fire pumps can result in several problems like:
- Improper system function.
- Undeveloped spray patterns from sprinklers.
- Insufficient pressure to hose valves.
- Too much pressure, causing components to burst and break open while operating.
Hence, the first step of fire pump sizing is to identify the most demanding system. The standpipe is the most demanding system in most commercial buildings. The standpipe system design and the fire pump flow rate requirements are given in NFPA 14.
Next, the required pressure must be calculated. Pressure requirement can be calculated as (Demand at the top + static losses+ pipe friction losses – source water pressure). Other requirements are the size of the room where the fire pump will be installed.
If the sprinkler load is the most demanding then the fire pump must be designed based on the hydraulic demand of the sprinkler system.
Once the above parameters are known, a fire pump can be selected. NFPA Fire Protection Handbook provides enough guidelines for selecting the required fire pump.
Characteristics of a Fire Pump
The main characteristic feature that a fire pump should have are listed below:
- Pump internals must be made from non-corrosive materials.
- The pump selection must be based on the required NPSH value, flow, and head demand to avoid cavitation.
- All fire pumps must have adequate power reserves.
Hello Anup, thanks for sharing the above information.
I have a technical/ compliance related question. We have an offshore processing platform with Living Quarters, and there are 3 firewater pumps (2 electric driven and 1 diesel driven) with operating capacities of 3×50%, i.e. two running (lead/lag) and 1 standby.
Pump A discharge check valve is passing at about 30m3/hr, so we have closed the manual valve on the discharge line to Ring Main. But we are expecting to do some maintenance on Pump B for a period of 10 days. So during that 10 days, we are proposing to have a dedicated personnel standby the manual valve of Pump A (14-inch valve) to be ready to open it in case of any emergencies. It will take about 30mins to fully open the manual butterfly valve. Is this approach supported by NFPA or is not in compliance?
Could you share some operating experience in industry where due to maintenance requirements, some work around method is required to keep the platform running and safe?
Thanks.
Thanks a lot for giving us knowledge about fire pump.