What is meant by Friction Welding?
Friction welding is a solid-state welding technique for joining workpieces by producing heat through mechanical friction. They do not use an external heat source to melt or convert the metal into a plastic state. Instead, the welding is formed by the application of external pressure. In friction welding, one part of the pieces to be joined rotates relative to the other. Because of this movement, friction is generated that heats up the materials at the contact surfaces. Till the completion of the welding cycle, a high-pressure force is applied.
What metal joints are used in friction welding?
The major benefit of friction welding is that it can be used to join dissimilar metals. Friction welding is widely used with metals like steel, aluminum, copper, titanium, nickel alloy, and thermoplastics in a wide variety of aviation and automotive applications. An eco-friendly process, friction welding is also used to manufacture subassemblies for industrial printers, material handling equipment, marine, and oil applications. The components that are usually manufactured using the friction welding process are gears, axle tubes, hydraulic piston rods, drivelines, valves, truck roller bushes, connection rods, pump shafts, drill bits, etc.
Working Principle of Friction Welding
Friction welding uses the principle of heat generation by friction between two members. During the friction welding process, two surfaces to be welded are made to rub against each other at a very high speed. The developed friction between the rotating and non-rotating surface produces enough heat at the weld interface. Once the required welding temperature is generated, a uniformly increasing external pressure is applied till both the workpieces form a permanent joint. This is the basic principle of all types of friction welding processes, even though the exact process may vary slightly depending on the type.
What are the steps in Friction Welding?
All the friction welding processes mostly follow the following steps:
- Step 1: One part to be welded is placed in a rotor-driven chuck and the other part is held stationary. Now the rotor is switched on to rotate at a very high speed along with the workpiece.
- Step 2: The rubbing of welding surfaces creates sufficient heat (of the order of 900-13000 C for steel). Now a high pressure is applied through the stationary part.
- Step 3: Once the temperature of the welding surfaces reaches the required temperature, the rotor is stopped.
- Step 4: Now, the pressure is increased continuously till both parts weld to each other.
Refer to Fig. 1 below that explains the Friction welding process steps clearly.
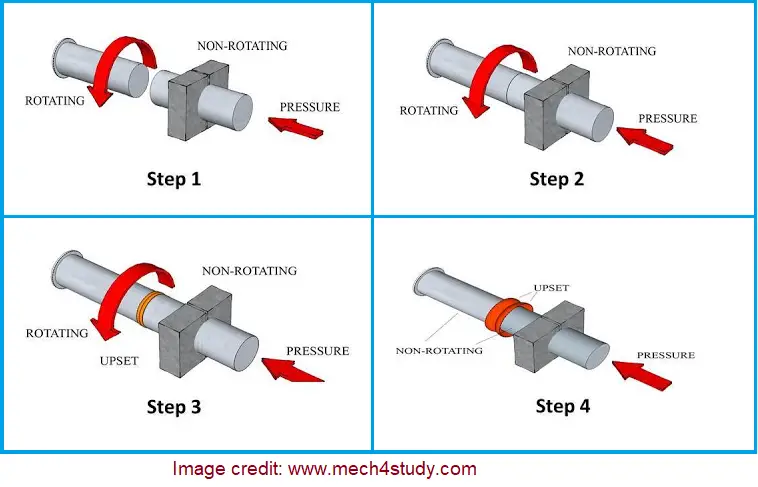
What are the Types of Friction Welding?
There are 6 types of friction welding processes that are widely used. They are:
- Inertia Friction Welding
- Direct Drive Friction Welding
- Linear Friction Welding
- Orbital Friction Welding
- Friction Stir Welding (FSW), and
- Friction Stir Spot welding
Inertia Friction Welding:
In the inertia friction welding process, different-sized flywheels are attached to the chuck and spindle shaft. The part is rotated by a motor that is connected to the spindle shaft. During the start of friction welding, the motor connected to the spindle shaft rotates the part to the required rotational speed. When the necessary speed is achieved, the motor is disengaged from the spindle shaft. Depending on the weight of the part, chuck, spindle shaft, and flywheels, rotational inertia is created by the free-spinning components. At this point, the frictional welded process started with the application of pressure. As the heat is generated by utilizing the rotational inertia when the parts are brought together, this method is known as Inertia Friction Welding.
Direct Drive Friction Welding:
In the direct drive friction welding process, the spindle shaft is permanently connected to the motor. Frictional heat between the wending surfaces is produced when the two pieces are brought together and the motor drives the rotating part. The process is usually controlled by the CNC program. It continuously slows down the spindle while the friction welding process takes place and then stopped at a pre-decided point. This type of friction welding is advantageous when a specific orientation of the workpieces is required.
Linear Friction Welding:
In the linear friction welding process, the moving chuck doesn’t spin. On the contrary, it oscillates in a lateral motion (linear). Throughout the entire friction welding process, the workpieces are held under pressure. The main benefit of this method is that by using linear friction welding, parts of any shape having high shear strength can be joined.
Orbital Friction Welding:
In orbital friction welding, both of the parts to be welded are rotated in the same direction and at the same speed, keeping an offset by up to 1/8” between their axes. When the weld cycle is completed, the rotation is slowed and the parts are returned to the same axis. However, the forging pressure is maintained while the materials re-solidify.
Friction Stir Welding (FSW):
Friction Stir Welding or FSW is a type of friction welding process that uses a special non-consumable tool with a cylindrical shoulder and a profiled pin for joining the two surfaces of the workpieces. Heat is generated between the rotating tool and the workpiece which softened the interface region. When the tool is traversed along the joint line, it mechanically intermixes the softened material of the two pieces of metal and forges the weld interface through mechanical pressure applied by the tool. Friction Stir Welding is used in trains, modern shipbuilding, and aerospace applications. Friction Stir Welding was invented in 1991 by Wayne Thomas.
Friction Stir Spot Welding:
Friction Stir Spot welding is a variant of the FSW mentioned above. It works by rotating, plunging, and retracting a non-consumable tool into two workpieces in a lap-joint configuration to make a “spot” weld. During the friction stir spot welding process, there is no traversing of the tool through the workpieces.
Other Types of Friction Welding Processes
- Friction Stud Welding: It involves a rotating stud that is forced on the plate surface under controlled conditions. Friction stud welding has a very short weld time and high-quality welding.
- Friction Taper Plug Welding: Widely used for repairing cracks in steel pipe or plates, friction taper plug welding is accomplished by drilling a tapered hole. Then friction welded into the hole is performed using a tapered plug with a similar included angle. The complete conical surface of the tapered plug is welded to the matching surface of the hole.
Benefits of Friction Welding
Friction welding provides various advantages with respect to conventional welding processes. Some of the advantages of using friction welding are:
- Joining Dissimilar Materials: Friction welding allows to join of aluminum with steel or copper to aluminum. Similarly, various bi-metallic friction welded joints can be produced.
- No external heat source or flux application
- Fast and efficient process
- Need very less surface preparation
- As the welding process is CNC controlled, the friction welding process produces consistent quality products.
- Reduced Material wastage
- Environment-friendly process
- As solid-state welding, friction welding avoids defects associated with fusion welding.
Online Courses on Friction Welding
To learn more about the basics and mechanisms of friction welding, the following two online courses will help you:
It’s nice to know that stud welding can also be done using orbital welding equipment. I’m interested in using one in the future because I’ve been getting the hang of making metal sculptures. Melding scraps together requires precision in order to not warm the metals too much.
Dear Anup:
As you might recall we join metal w/ no HAZ, no fusion line. NOT friction.
Building 2 x demos in Toronto w/ Sorsys Technologies.
#1 4″ & 6″ tubular solid state. Expecting preliminary sample welds late June, 2024. Target – spent fuel container lids. Also hydrogen pipeline – no root weld, no stress riser. Resist embrittlement.
#2 Nuclear fuel rod to end cap. Tubing Circ4 12 mm OD, 0.5 mm wall. X rays done.
This is a new class of solid state.
Sincerely
Paul Cheng
FuseRing.com