If you are a pipeline engineer, you must be familiar with the term girth welding. Yes, you are right. Line pipes (API 5L) used in the pipeline industry are generally joined together using girth welding. In this article, we will explore more about the girth welding process. So, let’s start with the definition of girth welding.
What is Girth Welding?
Girth welding is the process of connecting two pipes by welding around their circumference. As the welding is done around the pipe circumferences, girth welding is also popular as circumferential welding. Several welding passes are required to create a proper weld joint. The most widespread application of girth weld is found to join pipe and pipeline networks for aboveground and underground applications. The ease of welding and environmental factors must be considered while selecting the girth weld process as the preferred welding method.
Girth Welding Passes
In general, there are a minimum of three welding passes, that welding operators employ while performing girth welding. They are:
- Root Pass or Stringer Bead- The root pass of girth welding is the most difficult welding pass as the welding process needs a specific speed for improved reliability.
- Hot Pass- This process increases the welding thickness of the root pass.
- Fill and Cap Pass- This is the final welding pass that completes the girth weld joint.
Girth Welding Methods
The most common methods employed for the girth welding process are:
- Manual arc welding: SMAW and GTAW are the usual MAC methods.
- Semi-automatic arc welding: SAW (Submerged arc welding), FCAW (Flux-cored Arc Welding), and GMAW (Gas Metal Arc Welding) are the common ones.
- Automatic arc welding: Flash-butt welding, friction welding, and Laser-beam welding are mostly used.
Selection of Girth Welding
The proper selection of welding methods and standards for circumferential girth welding depends on various parameters as listed below:
- The pipe manufacturing process employed
- The strength of the base pipe material
- Pipe diameter and wall thickness
- External conditions
- Environmental factors
- Length and cost of the pipeline
- Terrain
- Skills of Welder
- Welding location
- Weldment properties
- Welding Economics
- The direction of weld travel (uphill or downhill)
- Ease of implementation
- Weldability of the pipe
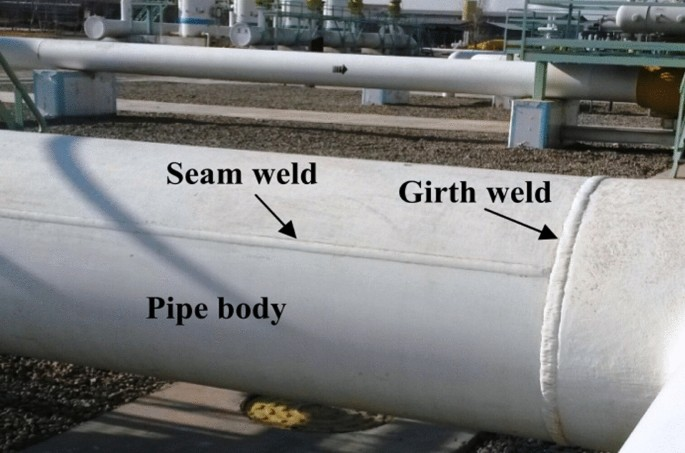
Girth Welding for Pipeline Tie-ins
An important use of the girth welding method is in the form of pipeline/piping Tie-in connections. This is a key aspect of girth welding. Tie-in pipeline connection usually means the connection of a pipeline with the facility of other existing piping networks. Sometimes, It also refers to the connections between different sections within the same pipeline.
As most of the pipeline tie-in welding connections are carried out within trenches at the work site, the use of new equipment is not practical. Hence, to create a weld joint between two completed piping sections, the alignment, preparation, and accuracy level must be well planned to get reliable and strong girth weld joints.
Repair welding and mainline welding also call for various girth welding methods like Shielded metal arc welding, Flux-cored arc welding, Gas tungsten arc welding, Submerged arc welding, Gas metal arc welding, etc. The detailed pipeline welding methods can be accessed from here.
In recent times, various automatic girth welding machines are developed which makes the girth welding process efficient with less effort. Even automatic welding robots are also developed. Girth welding can also be used for welding tanks. Automatic girth welding machines produce reliable welds with precise control of the process.
The girth seam welds are usually classified into the following two categories: Vertical circumferential seam and Horizontal girth seam.
Video Courses in Welding
To learn more about welding the following video courses you can refer to:
Nice to here about your passion.
Dear Mr.Anup, thanks for your blog as I am learning new things related to my Marketing efforts for Programable remote controlled machines from South Korea to both Indian and overseas customers mainly UAE.
We are also looking for affordable systems for SME segments who rely mostly on skilled welders. Currently we are focusing on Boiler & Pressure vessel manufacturers in Pune and their vendors.