The steel industry is considered to be one of the dirtiest industries and accounts for more than 7% of worldwide carbon emissions. To reduce the environmental impact of greenhouse gas emissions, industry experts are now turning towards a sustainable steel-making process that has the potential to bring the global CO₂ emissions close to zero. Green steel is one such endeavor to produce steel to have the lowest possible carbon footprint during production. It is believed the green steel production process reduces the CO₂ emissions by 95% as compared to the traditional steel-making process. in this article, we will explore more about Green Steel and its production. Let’s start with the definition of green steel.
Green steel refers to steel produced using methods that significantly reduce or eliminate carbon dioxide emissions compared to traditional steelmaking processes. Traditional steel production, particularly through the blast furnace method, is highly carbon-intensive due to its reliance on coke (a form of carbon) to reduce iron ore into molten iron. Green steel, in contrast, seeks to either eliminate the use of carbon or offset its emissions through innovative technologies and renewable energy sources.
What is Green Steel?
Green steel is environmentally friendly steel produced by reducing its carbon footprint as compared to the conventional steel-making process. The reduction in this footprint is obtained through the implementation of non-coal-based alternative technologies. In most cases, green steel production utilizes green hydrogen instead of coal and electricity generated from fossil-free sources.
The Environmental Impact of Traditional Steelmaking
To understand green steel, it’s essential to grasp the environmental toll of conventional steel production. The traditional process involves:
- Blast Furnaces: These furnaces use coke as a reducing agent, which releases significant amounts of carbon dioxide (CO2) during the reduction of iron ore (iron oxide) to molten iron. This process emits about 1.8 tonnes of CO2 per tonne of steel produced.
- Electric Arc Furnaces (EAFs): While less carbon-intensive than blast furnaces, EAFs still rely on electricity, which is often generated from fossil fuels. Therefore, while EAFs produce steel from scrap, they still contribute to CO2 emissions depending on the energy mix.
Green Steel Production
Green steel making involves hydrogen-based direct reduction of iron ore. The first step of the chemical green steel-making process is reducing the solid iron ore using hydrogen. It generates an intermediate product known as ‘sponge iron.’ Then, this sponge iron is fed into an electric arc furnace where the sponge iron is melted to produce the steel. In a greenfield steel plant, most of the processes involved in green steel production are fully integrated, digitized, and automated.
The green steel production process (Refer to Fig. 1) consists of the following steps:
- Decomposing water into hydrogen and oxygen by electrolysis.
- Exposing iron ore to the hydrogen inside a reactor to generate direct reduced iron which is then transported to the electric arc furnace while the DRI is in a hot state.
- The electric arc furnace heats the DRI and steel scrap to generate a homogeneous liquid steel melt. The melt is then transferred to a laddle furnace and degasser where alloying additions are done to get desired properties.
- In the next step liquid steel is converted into solid green steel products using continuous casting and rolling process.
- In the final step, depending on the customer requirement, downstream finishing is done using various treatment processes like cold working, galvanization, heat treatment, etc.
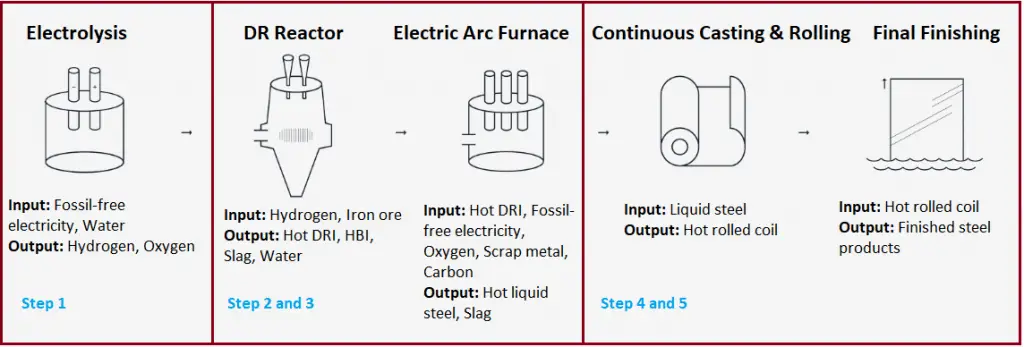
Green Steel Technologies
Green steel encompasses several innovative technologies and approaches aimed at reducing or eliminating CO2 emissions. Here are some of the most promising methods:
1. Hydrogen-Based Steelmaking
Direct Reduced Iron (DRI) with Hydrogen: Traditional DRI processes use natural gas to reduce iron ore. In contrast, hydrogen-based DRI replaces natural gas with hydrogen, which produces water vapor instead of CO2. The use of green hydrogen (produced via electrolysis using renewable energy) can potentially eliminate CO2 emissions entirely from this process.
Hydrogen Direct Reduction (H-DR): This is a cutting-edge technology where hydrogen is used as a reducing agent in a direct reduction process. Companies like SSAB, LKAB, and Vattenfall have made significant strides in developing this technology. The H-DR process is still in its experimental stages but shows promise for large-scale implementation in the future.
2. Electrolytic Reduction
Molten Oxide Electrolysis (MOE): This method involves electrolyzing molten iron ore to produce iron and oxygen. It operates at high temperatures, and the only byproduct is oxygen. While still in the developmental phase, MOE has the potential to drastically cut emissions once scaled up.
Electrolysis of Iron Ore: Another approach involves directly electrolyzing iron ore into iron and oxygen. This process is still experimental but offers a path to producing steel with zero emissions if powered by renewable electricity.
3. Carbon Capture, Utilization, and Storage (CCUS)
Carbon Capture and Storage: This technology captures CO2 emissions from steel production and stores them underground or repurposes them for industrial use. While not a green steel method per se, CCUS can significantly reduce the carbon footprint of traditional steelmaking processes.
Carbon Utilization: Innovative approaches are being explored to use captured CO2 in other industrial processes, such as producing chemicals or fuels, thereby turning a greenhouse gas into a valuable resource.
4. Biomass and Renewable Energy
Biomass Reduction: Replacing coke with biomass (e.g., wood chips, agricultural residues) in blast furnaces can reduce CO2 emissions, as biomass absorbs CO2 during its growth. However, scaling this method to meet global steel demand is a challenge.
Renewable Energy Integration: Using renewable energy sources like wind, solar, or hydroelectric power to run electric arc furnaces can reduce the carbon footprint associated with steel production.
Benefits of Green Steel
The shift to green steel offers numerous environmental and economic benefits:
Environmental Benefits
- Reduction in CO2 Emissions: Green steel technologies can significantly lower or even eliminate CO2 emissions from steel production. For example, hydrogen-based steelmaking can reduce emissions by up to 95% compared to traditional methods.
- Lower Air Pollution: Traditional steelmaking produces various pollutants, including sulfur dioxide (SO2) and nitrogen oxides (NOx). Green steel methods typically generate fewer of these harmful substances.
- Resource Efficiency: Some green steel technologies, such as those utilizing biomass or recycled materials, can enhance resource efficiency and reduce reliance on virgin iron ore.
Economic Benefits
- Innovation and Market Leadership: Companies investing in green steel technologies position themselves as leaders in sustainability, potentially gaining a competitive edge in the market.
- Job Creation: The development and scaling of green steel technologies can create new job opportunities in research, manufacturing, and infrastructure.
- Regulatory Compliance: Green steel can help steel producers comply with increasingly stringent environmental regulations and avoid potential carbon pricing or taxes.
Differences between Green steel and Conventional steel
Here’s a detailed comparison of green steel and conventional steel (regular steel):
Aspect | Green Steel | Conventional Steel |
---|---|---|
Production Methods | Hydrogen-based direct reduction, electrolytic reduction, biomass-based, or renewable energy-powered electric arc furnaces | Blast furnace (using coke) and electric arc furnaces (often powered by non-renewable energy) |
CO2 Emissions | Significantly reduced or eliminated; close to zero with technologies like hydrogen-based reduction or electrolytic reduction | Approximately 1.8 tonnes of CO2 per tonne of steel produced from blast furnaces; variable from electric arc furnaces depending on energy source |
Energy Sources | Uses renewable energy (wind, solar, hydro) or green hydrogen; some methods utilize biomass | Predominantly relies on fossil fuels (coal, natural gas) for blast furnaces; electricity for electric arc furnaces can be from fossil or renewable sources |
Byproducts | Primarily water vapor (in hydrogen-based methods) or oxygen (in electrolytic reduction); minimal air pollutants | CO2, sulfur dioxide (SO2), nitrogen oxides (NOx), and particulates; significant air pollution |
Resource Efficiency | Can enhance resource efficiency by utilizing recycled materials or biomass; reduces dependency on virgin ore | Traditionally uses large quantities of virgin iron ore and coke; recycling is limited to electric arc furnaces |
Cost | Higher initial costs due to new technologies and infrastructure; potentially lower long-term costs with economies of scale | Generally lower cost with established technology and infrastructure; costs can be high with fluctuating energy prices |
Infrastructure Needs | Requires new or retrofitted infrastructure for new technologies; significant investment needed | Uses established infrastructure; retrofitting for green technologies can be complex and costly |
Regulatory Compliance | Often supported by environmental regulations and incentives; benefits from policies aimed at reducing carbon emissions | Subject to increasing regulatory pressures to reduce emissions; may face carbon pricing or taxes |
Market Adoption | Limited market penetration currently; growing interest due to sustainability trends and consumer demand | Widely adopted with established market presence; competitive with traditional pricing |
Technological Readiness | Many technologies are still in experimental or early commercial stages; ongoing research and development | Mature technology with well-established processes and practices |
This table captures key differences between green steel and conventional steel, highlighting the advances and challenges associated with the transition to more sustainable steel production methods.
Green Steel Policy
Green Steel Policy is a comprehensive approach to fostering sustainable steel production through regulatory measures, financial incentives, technological support, and market strategies. By addressing the environmental impact of traditional steelmaking and promoting innovation, these policies aim to support a transition to a more sustainable and low-carbon steel industry.
In the face of escalating climate challenges, the Green Steel Policy emerges as a transformative blueprint for a more sustainable future. Designed to accelerate the steel industry’s transition to eco-friendly practices, this policy framework integrates ambitious emission reduction targets, financial incentives, and cutting-edge technologies. By prioritizing hydrogen-based steelmaking, renewable energy integration, and innovative carbon capture methods, the Green Steel Policy not only slashes carbon footprints but also sets the stage for groundbreaking advancements in industrial sustainability. Through targeted subsidies, tax credits, and robust research funding, it empowers steel producers to embrace greener methods, fostering a cleaner, more efficient production process that aligns with global climate goals.
Beyond its environmental impact, the Green Steel Policy heralds significant economic and market benefits. By driving innovation and establishing standards for sustainable steel, it creates new business opportunities and positions nations as leaders in green technology. This policy is a strategic investment in the future, enabling industries to reduce their carbon exposure while enhancing global competitiveness. As consumer demand for sustainable products surges, the Green Steel Policy ensures that steel manufacturers are well-equipped to meet these expectations, transforming the steel sector into a beacon of environmental stewardship and economic resilience.
Challenges with Green Steel
Decarbonizing the whole steel industry is a big hurdle while dealing with climate change. Conventional steelmaking produces around 7% of global greenhouse gas emissions, which is approximately equivalent to the annual emissions of all the cars on the world’s roads. Again, steel is required to make cars, so the impact is overlapping. This is the reason when it comes to climate change, steel is such a big deal.
Estimates show that 1 ton of steel production using the traditional methods roughly releases 2 tons of CO2 into the atmosphere and the world uses more than 2 billion tons of steel each year. Over half of the total emissions is from the blast furnace, where the iron ore is converted to pig iron.
Reducing this carbon emission in an economical way is still very challenging and various process improvements are still required. In the coming years, there will be an increased push from environmentalists to go for green steel production. Various research and development works are still ongoing and in near future, green steel production on a massive scale will become a reality.
Many countries are trying to commercialize large-scale green steel production and Sweden is currently leading the world.
This is an interesting article on an emerging technology. Is there any information that can be added to what the costs involved are relative to the more common methods making steel?
Must scrap metal be added? Is the quality of the finished product dependant on the quality of the scrap metal?